Understanding Cold Heading: Processes, Types, and Principles
1. Processes of Cold Heading
Cold heading is a manufacturing process used primarily in the production of metal components such as fasteners, screws, bolts, and pins. It’s a cold forming technique that transforms raw material into desired shapes without the need for heat. This process is highly valued for its efficiency, precision, and ability to create complex shapes with minimal material waste.
The cold heading process begins with selecting a suitable metal material, typically steel, aluminum, or brass. The chosen material is then fed into a cold heading machine, also known as a header. This machine applies extreme pressure to the metal blank, forcing it into a die cavity to form the desired shape.
One of the key components of the cold heading process is the die set, which consists of a punch and a die. The punch applies the necessary force to shape the metal, while the die provides the desired form. These dies are precision-engineered to produce parts with tight tolerances and consistent quality.
During cold heading, the metal undergoes plastic deformation, meaning it changes shape without reaching its melting point. This results in parts with excellent mechanical properties, including high strength and durability. Additionally, since no heat is involved, cold heading minimizes material distortion and maintains the integrity of the metal’s microstructure.
Cold heading is widely used in industries such as automotive, aerospace, construction, and electronics, where high-quality fasteners and components are essential. Its versatility allows for the production of a wide range of shapes and sizes, making it a cost-effective solution for mass production.
2. Types of Cold Heading
When it comes to manufacturing precision metal components, understanding the different types of cold heading processes is essential. Cold heading, a form of metal forming, encompasses various techniques tailored to specific applications and requirements. From progressive to rotary, each type of cold heading offers distinct advantages, making it crucial for manufacturers to select the most suitable method for their production needs.
Progressive cold heading stands out as one of the most widely used techniques in the industry. It involves feeding a continuous coil of wire through a series of dies, with each die performing a specific forming operation. This method enables high-volume production of complex parts with minimal material waste, making it ideal for industries such as automotive and electronics.
Transfer cold heading, on the other hand, relies on a transfer mechanism to move the workpiece between different dies. This approach allows for greater flexibility in part design and facilitates the production of larger components with intricate features. Transfer cold heading finds applications in manufacturing bolts, screws, and other fasteners requiring precise dimensions and tight tolerances.
Single-die and multi-die cold heading techniques are differentiated by the number of dies involved in the process. Single-die cold heading, also known as upset forging, involves shaping the workpiece using a single die and a punch. It’s commonly used for producing simple parts such as rivets and pins. In contrast, multi-die cold heading utilizes multiple dies to achieve more complex geometries and tighter tolerances, making it suitable for high-precision components like gears and shafts.
Impact cold heading utilizes the force of impact to deform the metal blank into the desired shape. This rapid forming technique is often employed in the production of small, symmetrical parts such as rivets and connectors.
In summary, the diverse range of cold heading techniques offers manufacturers flexibility, efficiency, and precision in producing a wide array of metal components. By understanding the characteristics and applications of each type, manufacturers can optimize their production processes to meet the demands of modern industries.
3. Principles Behind Cold Heading
Advantages of Choosing Leading Cold Headed Part Manufacturers
1. Precision Beyond Compare
2. Quality Standards and Certification
One of the hallmarks of renowned cold headed manufacturers is their commitment to precision engineering. By leveraging advanced cold forming technology and expertise, these manufacturers produce precision cold headed components with tight tolerances and consistent dimensions. This precision is essential for applications where reliability and performance are paramount, such as automotive, aerospace, and electronics.
Moreover, leading cold headed part manufacturers offer customized solutions tailored to the specific needs of their customers. Whether it’s a complex geometry, unique material requirement, or stringent performance criteria, these manufacturers have the capabilities and flexibility to deliver custom cold headed parts that meet or exceed expectations.
Quality assurance is another crucial aspect of choosing a leading cold headed part manufacturer. These manufacturers adhere to strict quality management systems and undergo regular audits to ensure compliance with industry standards and regulations. Additionally, many leading manufacturers hold certifications such as ISO 9001, demonstrating their commitment to quality and continuous improvement.
By partnering with a certified cold heading manufacturer, customers can have confidence in the reliability and performance of their products. From fasteners and connectors to precision components, these manufacturers uphold the highest quality standards to deliver solutions that meet the most demanding specifications.
Applications Across Industries: Where Precision Matters
1. Automotive Industry
The automotive industry stands as a testament to the relentless pursuit of precision, innovation, and reliability. From engines to chassis, every component plays a vital role in ensuring the safety, performance, and longevity of vehicles. Within this intricate ecosystem, cold headed parts emerge as indispensable elements, providing critical functionalities across various automotive applications.
One of the primary applications of cold headed parts in the automotive sector is fastening. Bolts, screws, nuts, and rivets manufactured through cold heading techniques secure essential components of vehicles, including engines, transmissions, suspensions, and body structures. These fasteners must exhibit exceptional strength, durability, and resistance to vibration and fatigue to withstand the demanding conditions of automotive operation.
Furthermore, cold headed parts find extensive use in automotive safety systems. Components such as airbag initiators, seatbelt anchors, and brake system fittings require precision-engineered parts to ensure optimal performance during critical moments. Cold heading technology enables the production of intricate geometries and precise dimensions necessary for these safety-critical applications.
Beyond fastening and safety systems, cold headed parts contribute to various other automotive subsystems. From fuel injection systems to climate control mechanisms, these precision components play a pivotal role in enhancing vehicle efficiency, comfort, and performance. Additionally, cold heading allows for the integration of lightweight materials, contributing to overall fuel economy and environmental sustainability.
In the fiercely competitive automotive industry, manufacturers rely on cold headed parts to gain a competitive edge. The ability to produce high-quality, cost-effective components with tight tolerances and consistent quality is paramount in meeting the evolving demands of vehicle manufacturers and consumers alike. As automotive technology continues to advance, cold heading remains an essential manufacturing process, driving innovation and excellence across the industry.
2. Aerospace Sector
In the vast expanse of the aerospace sector, precision isn’t just a desire—it’s an absolute necessity. From towering commercial airliners to sleek spacecraft venturing beyond Earth’s atmosphere, every component must meet stringent standards of reliability, durability, and accuracy. Cold headed parts play a crucial role in fulfilling these requirements, serving as indispensable elements across a wide array of aerospace applications.
At the forefront of aerospace engineering, cold headed fasteners stand as pillars of structural integrity and safety. These meticulously crafted components secure critical assemblies within aircraft and spacecraft, withstanding extreme forces, vibrations, and temperature fluctuations encountered during flight. Whether it’s securing wings, fuselages, or propulsion systems, cold headed fasteners ensure the structural integrity of aerospace vehicles, contributing to the safety of passengers and crew.
Moreover, cold headed parts find extensive use in aerospace propulsion systems, where precision and reliability are paramount. From turbine blades to engine mounts, these components must withstand the intense heat and forces generated by jet engines and rocket propulsion systems. Cold heading technology enables the production of high-strength, heat-resistant parts capable of withstanding the harsh conditions of aerospace propulsion.
In the realm of avionics and spacecraft instrumentation, cold headed connectors play a vital role in ensuring reliable communication and control systems. These precision-engineered components facilitate the transmission of data, signals, and power between various subsystems, enabling seamless operation and navigation in the aerospace environment.
Furthermore, cold headed parts contribute to the lightweighting efforts in aerospace design, where reducing weight without compromising strength is crucial for fuel efficiency and performance. By utilizing advanced materials and innovative manufacturing techniques, cold heading enables the production of lightweight, yet durable components, contributing to the overall efficiency and sustainability of aerospace vehicles.
In summary, the aerospace sector relies on cold headed parts to achieve the highest standards of precision, reliability, and performance. From fasteners to connectors, these components play a critical role in ensuring the safety, efficiency, and success of aerospace missions, pushing the boundaries of exploration and technology in the skies and beyond.
Leading Innovations and Technologies in Cold Heading
1. Digital Precision in Manufacturing
At the forefront of digital precision in manufacturing lies the integration of advanced computer-controlled systems into cold heading machinery. High-speed cold heading machines equipped with servo-driven technology enable precise control over forming parameters, resulting in the production of intricate and complex cold headed parts with exceptional accuracy and consistency.
Furthermore, digital die design and simulation tools empower manufacturers to optimize cold heading processes before physical production begins. By simulating the behavior of materials and tooling in a virtual environment, engineers can identify potential issues, refine designs, and optimize process parameters to enhance productivity and reduce waste.
The advent of Industry 4.0 has revolutionized cold heading production by facilitating seamless connectivity and data exchange between machines, systems, and processes. Real-time monitoring of cold heading parameters, coupled with automated quality inspection systems, ensures that every part meets the highest standards of quality and precision.
Moreover, artificial intelligence and machine learning algorithms are being employed to analyze vast amounts of data generated during cold heading production, enabling predictive maintenance, process optimization, and continuous improvement.
In the quest for digital precision in manufacturing, additive manufacturing technologies are also playing a significant role in cold heading tooling. By leveraging 3D printing techniques, manufacturers can rapidly prototype and produce customized tooling with intricate geometries, enhancing the efficiency and flexibility of cold heading operations.
2. Sustainable Cold Heading Practices
At the forefront of sustainable cold heading practices lies the adoption of energy-efficient technologies and processes. Manufacturers are investing in high-speed cold heading machines equipped with servo-driven technology to minimize energy consumption while maximizing productivity. By optimizing process parameters and reducing idle times, these advanced machines contribute to significant energy savings and carbon footprint reduction.
Moreover, sustainable cold heading practices emphasize the use of advanced materials and coatings that minimize waste and enhance durability. Cold heading tool coatings and surface treatments prolong tool life, reducing the frequency of tool changes and minimizing material waste. Additionally, the incorporation of recycled and recyclable materials in cold heading processes further enhances sustainability by reducing raw material consumption and waste generation.
The integration of Industry 4.0 technologies in cold heading production also plays a pivotal role in sustainable practices. Real-time monitoring of process parameters enables manufacturers to optimize energy usage, minimize scrap, and maximize yield. Automated quality inspection systems ensure that only parts meeting the highest standards are produced, reducing rework and waste.
Furthermore, sustainable cold heading practices extend beyond the production process to encompass responsible waste management and recycling initiatives. Manufacturers are implementing comprehensive recycling programs to reclaim and repurpose metal scrap generated during cold heading operations, further minimizing environmental impact and promoting circular economy principles.
Choosing the Right Cold Headed Part Manufacturer: Factors to Consider
1. Experience and Expertise
2. Customization and Flexibility
Leading cold headed part manufacturers recognize the importance of customization, offering a diverse range of options to accommodate varied applications and requirements. Whether it’s modifying part dimensions, altering material compositions, or incorporating specialized features, manufacturers with customization capabilities empower customers to obtain precisely the components they need for their projects.
Flexibility is another critical factor in selecting a cold headed part manufacturer. The ability to respond quickly to shifting priorities, accommodate urgent orders, and adjust production schedules to meet tight deadlines can make all the difference in the success of a project. Manufacturers with flexible operations and agile processes can seamlessly adapt to changes in project scope, ensuring timely delivery without compromising on quality.
Moreover, customization and flexibility go hand in hand with collaboration and communication. Reputable manufacturers actively engage with customers throughout the project lifecycle, soliciting feedback, addressing concerns, and providing updates on progress. This open dialogue fosters a partnership mentality, where manufacturers become trusted allies in achieving project goals and overcoming challenges together.
From prototype development to full-scale production, the ability to customize parts and adapt to evolving requirements is crucial for success in the competitive marketplace. By partnering with a cold headed part manufacturer that prioritizes customization and flexibility, customers can unlock new opportunities for innovation, efficiency, and differentiation in their products and projects.
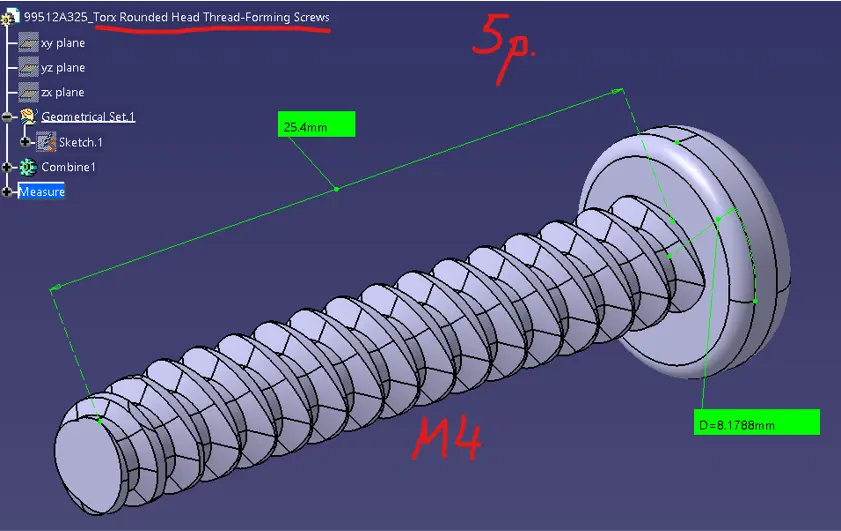
Global OEM&ODM Fasteners Brand
Wurth: The Wurth Group was founded in Germany in 1945 and has been continuously growing for nearly 70 years. Currently, the Wurth Group is in a leading position in the global assembly and fastener business market. Fasteners are the core product line of the Wurth Group, and Wurth is the largest fastener supplier in Europe. The group has tens of thousands of high-quality fastener products with a complete range and a huge inventory base. Wurth provides clients with professional ORSY and CPS ® KANBAN Kanban service provides customers with efficient C-Parts management solutions. Our products include: covering DIN German standards, ISO international standards, EN European standards, GB national standards, as well as various non-standard customized products. Wurth Group has over 400 companies in more than 80 countries worldwide, and its core business is to provide over 125000 types of products for the industry market.
Keller& Kalmbach: Keller& Kalmbach is one of the leading sellers in the fastener industry, mainly engaged in the sales of screws, fastening systems, anchors, painting parts, hand tools, electric tools, lifting equipment, safety, operating equipment, chemical technology products, etc. Since 1988, Keller& Kalmbach has gradually grown into a management expert in the field of parts sales. Here, the company proposes the Kanban model in KKL’s modular storage system and e-commerce solution. More than 900 projects have been completed and the logistics advantage of having over 1.2 million containers is self-evident. Keller& Kalmbach has over 500 employees and an annual sales revenue of over 200 million euros. The company’s business is divided into the automotive industry, industry, and trade. In addition to Germany, Keller& Kalmbach has also established foreign branches in China, Croatia, Austria, Poland, Romania, Slovakia, the Czech Republic, and Hungary.
TEXTRON: Textron is a multinational industrial group and one of the Fortune 500 companies in the United States, with annual sales of over 12 billion US dollars. The Textron fastening system mainly includes several series, including threaded fasteners, rivets and matching tools, assemblies, cold formed parts, stamped parts, and plastic parts. The Textron fastening series products are mainly non-standard types, which can meet the assembly needs of different products and customers, and provide comprehensive fastening solutions.
Alcoa: Alcoa is a leader in the world’s aluminum production and manufacturing industry, committed to producing sustainable products such as aluminum. Its main products include rolling products, wheels, forgings, fastener systems, precision castings, and solutions in the field of building systems. Its technology also involves other light metals, including titanium nickel superalloys. Ranked 439th on the 2012 Fortune Global 500 list.
Bossard: Bossard is a global provider of fastening and assembly technology solutions, providing over a million types of standard, non-standard, and branded fasteners, assembly technology consulting, and intelligent factory logistics management services. With over 190 years of experience in fastening technology, it not only helps customers enhance their core competitiveness through fastening solutions, but also achieves sustainable productivity through optimized assembly processes and intelligent factory logistics. Bossard entered the Chinese market in 1999 and is headquartered in Shanghai. It has established two wholly-owned companies, Bossard Fasteners (Shanghai) Co., Ltd. and Bossard Fasteners (Tianjin) Co., Ltd. It has four major warehousing and logistics centers in Shanghai, Tianjin, Shenzhen, and Chengdu, as well as branch offices in 14 cities to provide localized services to customers. To this day, the four major businesses of fastener product solutions, assembly technology services, intelligent factory logistics, and intelligent factory assembly have all settled in China.
Pencom: Pencom Hardware is a company headquartered in California, USA, mainly engaged in the production and procurement of customized standard fasteners, machinery, electronic machinery, and thermal control components. The mission of Pencom Hardware Products is to become a leading global solution provider, OEM design engineers and manufacturing components in the mechanical field, and provide inventory management solutions, localized inventory, improved inventory turnover, reduced inventory risk, and reduced inventory management costs.
Nelson: Nelson has been established for over 66 years and is a leading global manufacturer and distributor of welding nail fasteners and application equipment, providing products and services to a wide range of markets, including automotive, construction, and industrial markets. Welding nail products are almost suitable for the bonding needs of all industries. The product series includes external threaded fasteners, shear nails, concrete anchoring, perforated resistance bolts, inserts, ports, pipe and cable suspension hooks, welding nails and screws, as well as equipment for applying, assembling, and welding these products.
REYHER: Reyher is a family company founded in Hamburg, Germany in 1887. Headquartered in Hamburg, Germany, it is a world leading provider of fastener products and technology, with a global customer base covering industrial, mechanical equipment manufacturing, and equipment maintenance. It is also one of the largest fastener wholesalers in Europe.
EJOT: EJOT Group is a medium-sized German enterprise that produces and sells high-end fasteners. The predecessor of the group, AdolfBoehl Screw Factory, was established in 1922. Currently, Ejot Group Company has more than 20 branches worldwide and more than 1800 employees. In Europe, EJOT Group holds a leading position in the fastener industry, and EJOT is also one of the initiators of the Global Fastener Alliance. The goal of this alliance is to provide its members with high-end fastener products and technology to customers around the world.
A.AGRATI: Agrati’s passion and manufacturing glory can be traced back a long, long time ago. Thanks to the efforts of thousands of passionate individuals with diverse cultural backgrounds but shared values, Agrati has grown from a small company in Brianza, Italy to today’s leading global enterprise. In the early 1940s, Agrati was still a small mechanical engineering company. In its early days, the production of screws and bolts was limited to wooden screws, woodworking parts, and connecting rods. Agrati Group is pleased to offer its profound experience and in-depth professional knowledge related to fastening systems, as well as its next-generation laboratory equipment and testing capabilities, which have condensed the wisdom of generations.
PSM International: PSM International is a global multinational company that manufactures and sells professional fasteners. The company was founded in 1931 and is headquartered in Willenhall, central England. It now has branches in 12 countries and regions around the world. PSM’s business in the Asia Pacific region has expanded to Japan, Australia, Taiwan, Singapore, Hong Kong, and China. In addition, PSM Group has a high-quality global sales team dedicated to continuously expanding the market and providing customers with comprehensive solutions.
ITW Fasteners: ITW is a global manufacturer of professional industrial equipment, fasteners, components, and consumables for 55 countries/regions, headquartered in Glenview, Illinois. ITW Automotive, a subsidiary of ITW, uses various molding techniques to design and manufacture customized fastener solutions, while its construction subsidiary, ITW Buildex, also produces threaded fasteners, hangers, and more building products.
LISI Fasteners: LISI Group is a global metal component manufacturer targeting the aerospace, automotive, and medical industries. Their three main departments are LISI Medical, LISI Automotive, and LISI Aerospace, which produce fastening technologies and components for global healthcare, automotive, aerospace, and defense applications. They have 45 industrial bases in 13 countries/regions, all supervised by their headquarters in Paris, France.
ARAymond: ARAymond is a French global manufacturer and designer that provides fastening solutions for the automotive, industrial, energy, agricultural, and life sciences markets. In 2018 alone, they created over 1000 new fastening solutions in factories in 25 countries/regions, with a total of over 7000 employees. Their headquarters are located in Grenoble, France.
Fontana Gruppo: Fontana Gruppo is a global manufacturer group headquartered in Vedojo, Italy, specializing in standardized fasteners, special parts, patents, structural products, and other fastening solutions. They provide services to the distribution, automotive, agriculture, construction and construction, earthworks, powertrain, aerospace and defense, and general engineering industries in over 50 branches worldwide.
NORMA Group: NORMA Group is a global manufacturer and supplier of fixtures, connectors, fluid systems, and connection technologies located in Maintal, Germany. In addition to producing and selling various fasteners, NORMA also focuses on providing irrigation, architecture, landscaping, and other water management solutions to customers in 100 countries.
KAMAX Group: KAMAX Group is a leading manufacturer of high-strength fasteners and cold formed parts for automotive applications in 12 international regions. Their clients include many well-known brands such as Ford, Honda, Mike, Hyundai, Isuzu, Land Rover, Jaguar, Johnson Controls, Kia, etc. Their international headquarters are located in Humberg, Germany.
Meidoh: Meidoh is a global manufacturer of high-strength nuts and bolts, complex cold forging products, high-strength aluminum alloy parts and other fastener related solutions, headquartered in Aichi Prefecture, Japan. Meidoh collaborates with Toyota, Yamaha, and other clients to provide robust and reliable fastening solutions for numerous industries.
Aoyama Seisakusho: Aoyama Seisakusho also from Aoyama Manufacturing Co., Ltd. in Aichi Prefecture, Japan, is a global automotive fastener manufacturer. They provide services to customers from 6 countries, allowing for direct wire drawing, cold forming, rolling, heat treatment, surface treatment, and transportation from their facilities.
Precision Castparts Corp. Fasteners:Precision Castparts Corp. Fasteners is a fastener manufacturer in the aerospace industry and a division of Precision Castparts Corp., a global manufacturer of complex metal components and products, investment castings, forgings, fasteners, and other aerospace solutions. They have a large selection of special alloys to choose from and serve the petroleum, automotive, structural, and forging industries.
STANLEY Engineering Fastening: STANLEY Engineering Fastening is a global manufacturer of fastening and assembly solutions and a department of STANLEY Black&Decker. They use well-known brand fasteners such as Avdel,Integra, Optia, Nelson, Pop, Tucker, as well as more fasteners made of steel, plastic, and non-ferrous metals. They have factories in almost every continent, providing customers with delivery, warehousing, research and development, and related technical services.
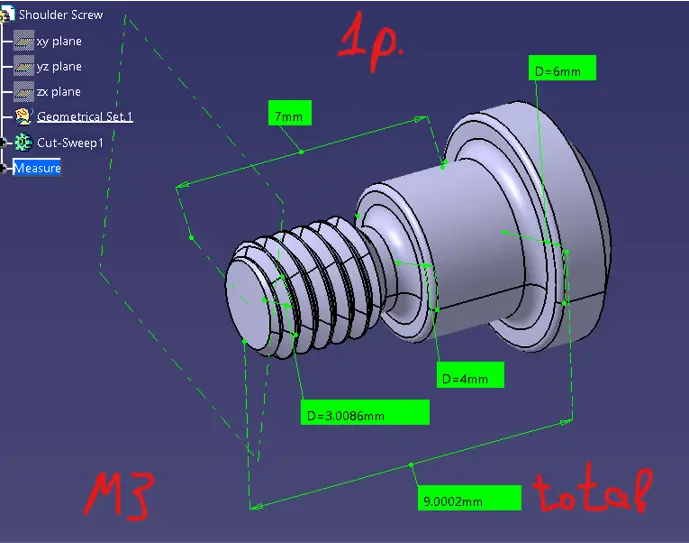
Common FAQs About Leading Cold Headed Part Manufacturers
-
Q: Why choose cold headed parts over other fastening options?
- A: Cold headed parts, especially premium security fasteners, offer unparalleled precision, strength, and tamper-proof features, making them ideal for critical applications in various industries.
-
Q: What certifications should I look for when selecting a cold headed part manufacturer?
- A: ISO certification is crucial to ensure quality and adherence to international standards. Additionally, manufacturers like Welleshaft may have certifications for their premium security fasteners.
-
Q: How can I determine the right type of cold headed part for my specific application?
- A: Consult with experienced manufacturers like Welleshaft, who can provide tailored solutions based on your requirements, including the selection of security bolts, screws, and nuts based on the desired level of tamper resistance.
Conclusion: Elevating Industries Through Precision and Expertise
In conclusion, leading cold headed part manufacturers, exemplified by the excellence of Welleshaft, play a pivotal role in shaping the future of precision manufacturing. The intricate processes, adherence to principles, and commitment to innovation showcased by these manufacturers underscore their importance in industries where precision is non-negotiable. As the demand for reliable and high-quality components, especially premium security fasteners, continues to rise, the contributions of leading cold headed part manufacturers remain indispensable, driving the evolution of modern manufacturing towards new heights of precision and excellence.