The Critical Role of Engineering and Quality Control
In the world of manufacturing, precision engineering and stringent quality control are paramount. Whether it’s ensuring the durability of an automotive component or the reliability of a medical device, engineering excellence and quality inspection play pivotal roles in delivering products that meet the highest standards.
Engineering excellence and quality inspection are the twin pillars upon which the foundation of modern manufacturing stands. In today’s globalized marketplace, where competition is fierce and consumer expectations are soaring, companies can ill-afford to compromise on the quality of their products. At the heart of every successful manufacturing operation lies a robust engineering framework coupled with meticulous quality inspection protocols. This synergy ensures that each component rolling off the production line adheres to stringent standards, delivering not just functionality but also reliability and longevity.
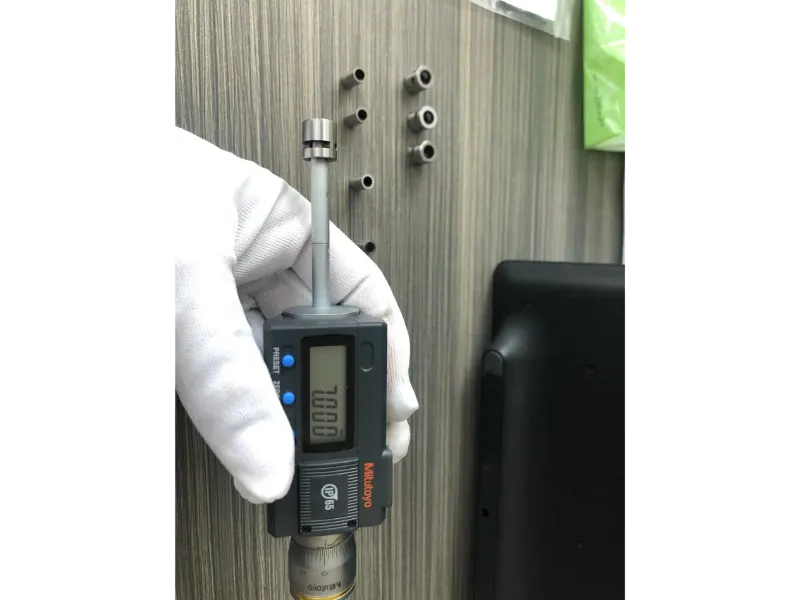
Global Quality Certifications and Expertise
At Welle, we understand the paramount importance of global quality certifications and expertise in today’s competitive landscape. Our commitment to engineering excellence and meticulous quality control is evident in our adherence to the highest industry standards and certifications. These certifications serve as badges of honor, signaling to consumers and stakeholders alike that Welle takes quality seriously and strives for excellence in every aspect of our operations.
In an interconnected world where products traverse borders effortlessly, adhering to global quality certifications is non-negotiable for Welle. These certifications provide a framework for quality management systems, environmental practices, and industry-specific requirements, guiding our journey towards excellence. Among the most recognized certifications are those provided by the International Organization for Standardization (ISO), and Welle proudly holds certifications such as ISO 9001:2015, ISO 14001, and others.
ISO 9001:2015 certification, for instance, is the gold standard for quality management systems (QMS), and Welle’s adherence to this standard ensures that our processes consistently meet regulatory requirements and deliver products of exceptional quality. Similarly, compliance with industry-specific standards such as IATF 16949 is paramount for Welle, particularly in sectors like automotive manufacturing, where precision and reliability are non-negotiable.
In addition to ISO and industry-specific certifications, Welle is committed to navigating regulatory frameworks such as RoHS and REACH. Compliance with these regulations underscores our dedication to environmental responsibility and consumer safety, further enhancing trust in the quality and integrity of our products.
Quality Control in Manufacturing Processes
At Welle, quality control is ingrained in every stage of our manufacturing processes, ensuring that each component meets the highest standards of precision and reliability. From raw material inspection to final product testing, our comprehensive quality control measures leave no stone unturned in our quest for excellence.
Material testing lies at the heart of our quality control efforts, and Welle employs advanced techniques such as hardness testing, chemical analysis, and spectroscopy to ascertain the integrity and composition of raw materials. Whether it’s metal alloys for aerospace components or polymers for consumer electronics, our rigorous testing protocols guarantee the quality and performance of our products.
Dimensional accuracy is another critical parameter in manufacturing, and Welle utilizes state-of-the-art techniques such as coordinate measuring machines (CMM), laser scanning, and optical comparators to verify the precision of components with micron-level accuracy. Our commitment to dimensional accuracy ensures proper fit and functionality, delivering products that exceed customer expectations.
Furthermore, cleanliness testing is paramount in industries where even minute contaminants can compromise product performance. At Welle, we employ techniques such as particle counting, surface cleanliness analysis, and ionic contamination testing to ensure that our products meet the stringent cleanliness requirements of sectors such as semiconductor manufacturing and medical device production.
Supervision and Compliance Enforcement
At Welle, we recognize that adherence to quality standards begins with robust processes and certifications but is sustained through vigilant supervision and compliance enforcement. Our onsite supervisors act as custodians of quality, ensuring transparency and accountability throughout the manufacturing lifecycle.
From conducting random inspections to implementing real-time monitoring systems, our onsite supervisors are dedicated to maintaining the highest standards of quality and integrity in every aspect of our operations. By closely monitoring production activities and identifying deviations from established standards, we proactively address issues and implement corrective measures to uphold the quality and reliability of our products.
Moreover, compliance enforcement is not merely about detecting deviations but also about addressing them promptly and effectively. At Welle, we have protocols in place to investigate root causes, implement corrective actions, and prevent recurrence, ensuring that our products consistently meet or exceed customer expectations.
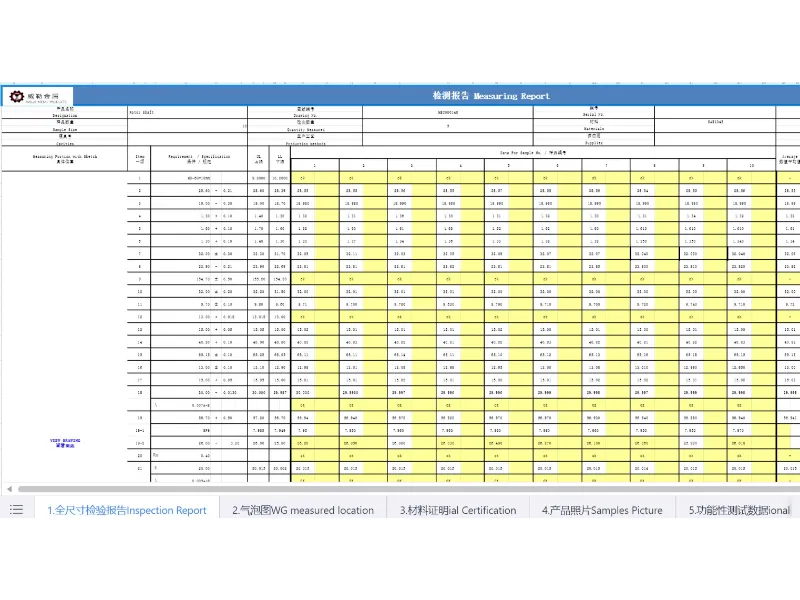
Quality Certification and Methodologies
At Welle, achieving quality excellence is not just a goal; it’s a mindset that permeates every aspect of our operations. Our commitment to continuous improvement is reflected in our adoption of quality methodologies that provide frameworks and tools to systematically identify, analyze, and mitigate risks.
Failure Mode and Effects Analysis (FMEA) is a cornerstone of our quality management approach, enabling us to proactively identify potential failure modes in our products and processes and develop mitigation strategies to prevent their occurrence. By prioritizing failure modes based on severity, occurrence, and detectability, we focus our resources on addressing high-risk areas and ensuring the reliability and performance of our products.
Advanced Product Quality Planning (APQP) is another key methodology that guides our product development and manufacturing processes. By defining clear objectives, milestones, and deliverables, APQP fosters collaboration and accountability across cross-functional teams, ensuring that our products meet or exceed customer requirements from inception to delivery.
Similarly, Statistical Process Control (SPC) and Measurement System Analysis (MSA) are integral components of our quality management system, enabling us to monitor process stability and measurement system capability in real time. By collecting and analyzing data, we identify trends, detect outliers, and make informed decisions to optimize processes and enhance product quality.
Addressing Common Concerns and FAQs
- How does Quality Inspection Impact Overall Product Performance? At Welle, quality inspection is not just a routine check; it’s a critical aspect of our commitment to delivering products of exceptional quality and reliability. By identifying and addressing defects early in the manufacturing process, quality inspection helps prevent costly rework, minimize warranty claims, and enhance customer satisfaction.
- What are the Benefits of Obtaining Global Quality Certifications? Global quality certifications such as ISO 9001:2015 and ISO 14001 demonstrate Welle’s commitment to excellence, compliance, and continuous improvement. These certifications enhance market access, foster customer trust, and mitigate risks associated with quality failures or regulatory non-compliance, positioning us as a trusted partner in the global marketplace.
- How Can Companies Ensure Consistency in Quality Across Various Suppliers? Consistency in quality across suppliers requires robust supplier qualification processes, clear specifications, and ongoing performance monitoring. At Welle, we establish communication channels, conduct regular audits, and provide feedback to suppliers to ensure alignment with our quality expectations, thereby ensuring consistency and reliability in our supply chain.
Conclusion
At Welle, we are committed to engineering excellence and meticulous quality control in every aspect of our operations. From adhering to global quality certifications and employing rigorous quality control measures to implementing advanced methodologies and fostering a culture of continuous improvement, we are dedicated to delivering products of exceptional quality, reliability, and performance to our customers worldwide.