SOURCING, STREAMLINED
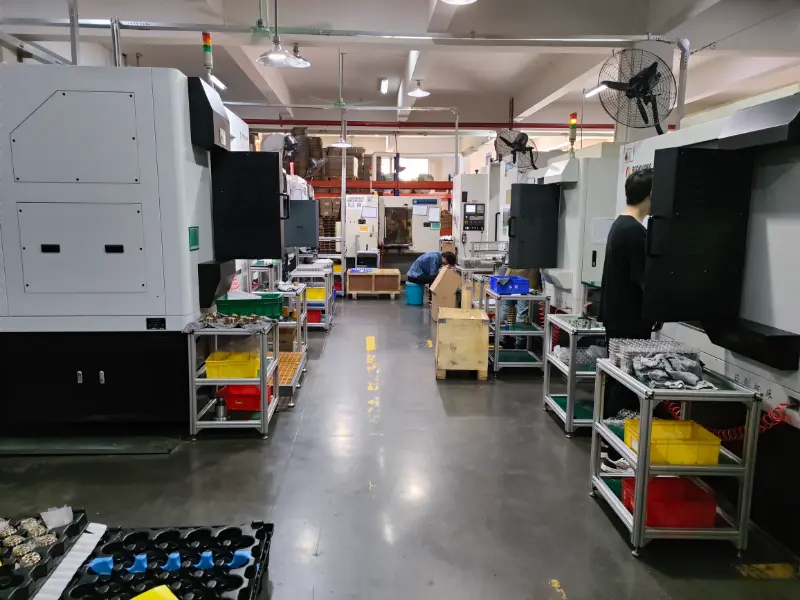
Outsourcing Factory 1
Gear Machining Mastery: Navigating Precision
The gear factory, equipped with over 100 sets of various kinds of gear machines, CNC machines, 3 heat treatment lines, and professional inspection machines. Focusing on supplying auto parts to vehicle manufacturers, it exports the products mainly to the USA and Europe. The factory has a product portfolio covering 10 series and over 200 different specs. It is certified with ISO9001 and TS16949, with annual production capability reaching 800K Helix Bevel Gear and 1.2M Cylindrical Gear.
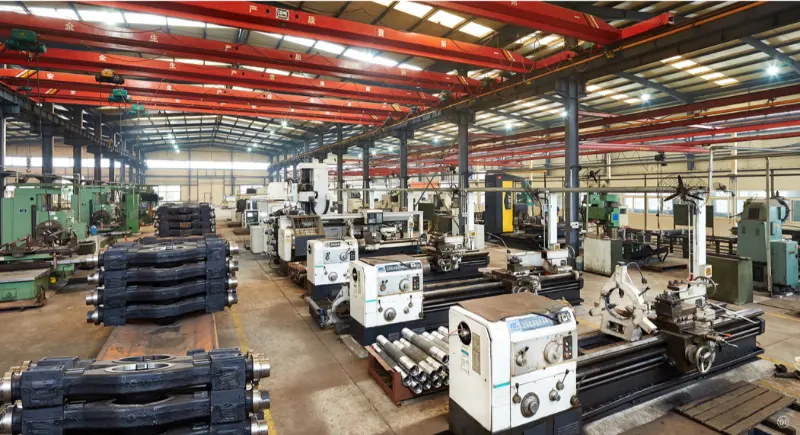
Outsourcing Factory 2
CNC Machining、Stamping and Welding Wonders in Modern Factories
The machining factory has more than 300 employees and 100,000 square meters industry zone. Notably, more than 60 professionals specialize in engineering, technical, and quality roles, highlighting the company’s commitment to expertise.
The company excels in a broad spectrum of primary processing capabilities, including machining, stamping (10T-800T), cutting (flame cutting, plasma cutting, laser cutting), welding, heat treatment, surface treatment, assembly, and polyurethane foam molding. Its state-of-the-art manufacturing arsenal comprises over 100 sets of high-end equipment, ranging from machining centers and CNC devices to over 200 sets of general machinery, such as lathes, milling machines, and grinders.
Furthermore, the company is well-equipped with 30 sets of punching presses and hydraulic presses, 5 sets of heat treatment equipment, 2 spray production lines, and one each of pickling and electrophoresis production lines. Key testing capabilities encompass ultrasonic testing (UT), magnetic particle testing (MT), penetrant testing (PT), Hexagon CMM, universal testing machines, hardness testers, salt spray test machines, and durability testing machines, showcasing a robust quality assurance framework.
The company proudly holds prestigious certifications, including IATF16949 and ISO14001 for environmental management systems, in addition to 3C certification. It plays a crucial role as a supplier for esteemed clients such as SinoTruck, ArvinMeritor, Hande Axle, Randon, Agco, SDLG, Caterpillar, among others, solidifying its position in the industry.
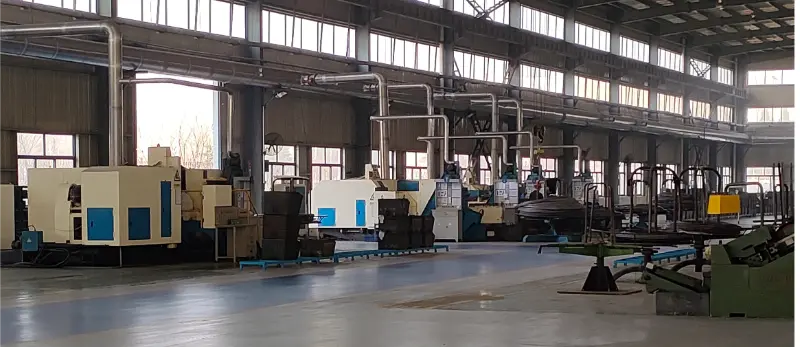
Outsourcing Factory 3
Cold Heading Excellence: Crafting the Extraordinary
The Cold Heading Factory covering 200,000 square meters with building area of 10,000 square meters, the factory has 300 employees, of whom 30 are engaged in engineering and technical support. Equipped with 30 lines of the advanced automatic Bolt and Nut Cold heading Machinery with 100 sets of Threading and Grinding machinery,6 Pre-dephosphorization Heat Treatment Production Line. The products are widely used in Automotive Standard Fasteners, Non-standard fasteners and High-strength High Grade Standard Fasteners etc. Its production capacity of models reaches 30000 tons per year. It is certified with IATF16949, ISO14001 and ISO/IEC17025:2017.
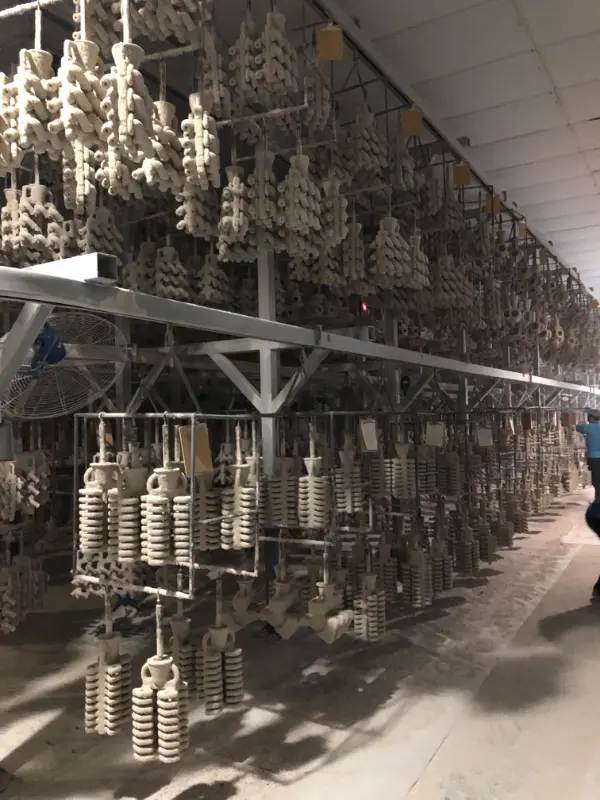
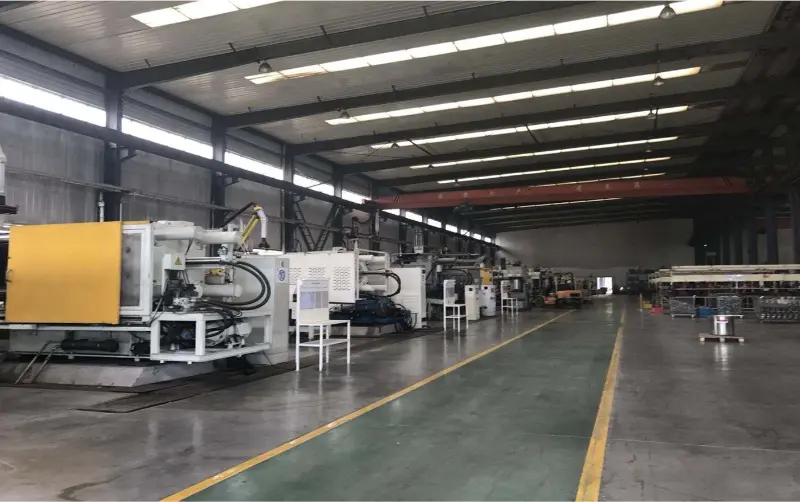
Outsourcing Factory 5
Die Casting Marvels: Molding the Future
The die casting factory with 380 employees, our company excels in Aluminum Extrusion,high and low-pressure die-casting with a capacity from 180T to 2500T. Our facility boasts 100+ CNC machining centers, 40+ presses (10T-200T), and automated painting and oxidation lines, ensuring a daily output of 500,000 accessory sets. Equipped with advanced testing facilities,such as dedicated thermal resistance testing laboratory, CMM, ultrasonic flaw detectors, roughness measuring, metallographic analyzers, cleanliness detectors, salt spray test chambers, fluorescence analyzers, universal testing machines, we hold ISO9001:2015, ISO14001, and IATF16949 certifications. Our product range includes radiators, aluminum die-castings, and LED accessories, serving applications in VFDs, energy storage, automotive components, and more. We proudly supply major clients like BYD, GEELY, WEICHAI POWERTRAIN, HP, Haier, Panasonic, Great Wall Motors, Midea, among others.
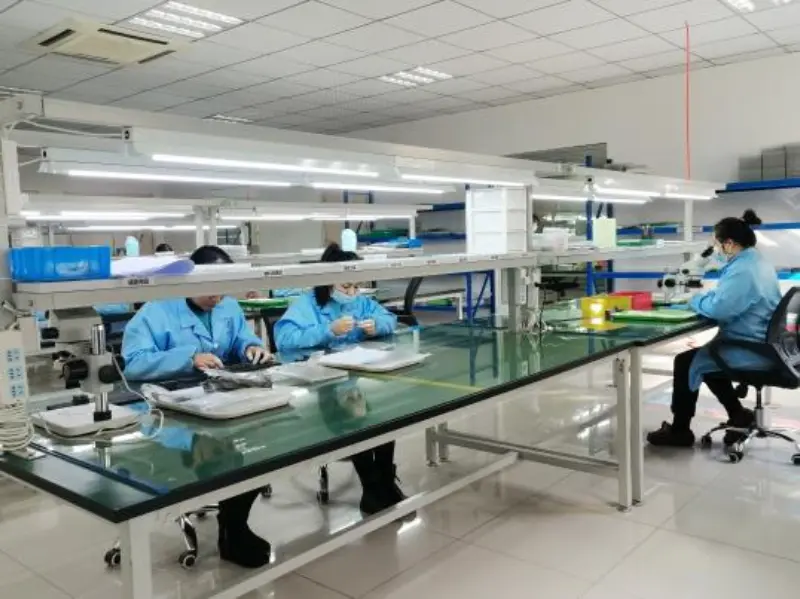
Outsourcing Factory 6
Photonics Packagings Factories: Illuminating Innovation
Covering an area of 1500 square meters with a staff of 50, our facility is equipped with five sintering and brazing furnaces, including four double-tube atmosphere furnaces and one chain mesh belt furnace. Capable of performing silver-copper, gold-tin, and pure silver brazing processes, we also have a dedicated nickel and gold electroplating line. Additionally, we can execute sealing processes like matched sealing and pressure sealing. Our testing equipment includes a physical and chemical laboratory, helium mass spectrometer leak detector, pressure testing machine, X-Ray coating thickness gauge, insulation resistance meter, multi-focus automatic microscope, and optical imaging instrument.
We specialize in processing precision metal components using materials such as tungsten-copper, molybdenum-copper, oxygen-free copper, stainless steel, Kovar alloy, nickel-based alloy, and silicon-aluminum alloy. Our products find extensive applications in the fields of optical communication device housings, SMD ceramic packaging housings, TO-type packaging housings, and other electronic packaging products. These are widely used in infrared, laser, microwave, hybrid integrated circuits, electronic power, medical, automotive, new energy, aerospace, and other industries. We deliver one million sets of packaged products annually.
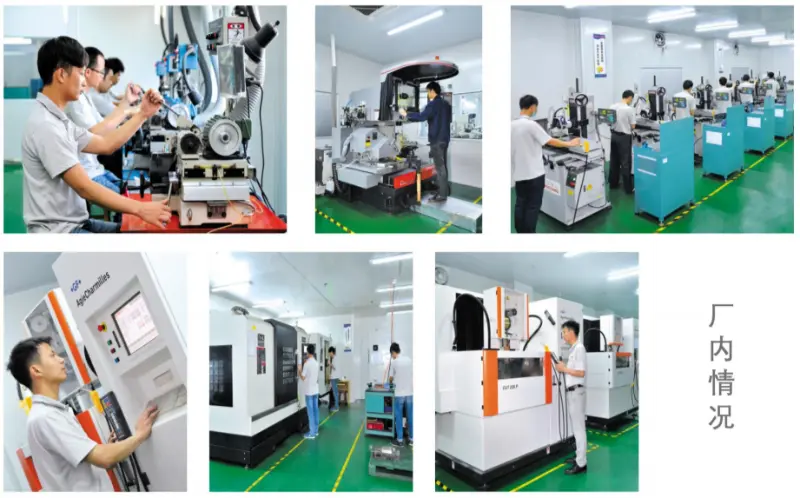
Outsourcing Factory 7
Cemented Carbide Precision Components
We specialize in high-speed stamping die components and precision parts manufacturing, ensuring micrometer-level accuracy. Our core offerings include precision stamping die components, plastic mold core parts, and custom-made precision cutting tools for various industries. We prioritize Japanese imported materials for connector components, semiconductor parts, and special circular parts. With over 50 machining and testing devices, including optical projection grinders and wire cut machines, we maintain ISO9001 standards. Our commitment to excellence extends to providing short lead time delivery services through international air courier. Additionally, we offer a range of precision components like cemented carbide and tungsten carbide parts, ensuring top-notch quality across industries.

Outsourcing Factory 8
Innovations in Metal Injection Molding Factories
The company excels in advanced technology and quality management, certified in ISO9001, ISO14000, and ISO/TS16949 systems. With over 100 specialized staff, including 22 seasoned engineers and 66 professionals, we operate 16 to 500-ton presses and injection molding equipment, 22 sintering furnaces, and over 200 machining equipment. Fully equipped with testing facilities, we produce 3500 tons annually, exporting globally. Equipment includes presses, furnaces, machining tools, and testing devices such as CNC lathes, universal testing machines, and coordinate measuring machines(CMM).
Conclusion
In the past years, WELLE has surveyed thousands of suppliers and established a wide, reliable network of “member manufacturers” and partners, totaling around 200 manufactures, with 10% stamping members, 11 % forging members, 15% machining members, 9% Plastic/Rubber molding members, 16% casting members,13% MIM/PM members, 9% welding members, 3% mold (for metal and plastic) members, and 14% others.
I have learn several good stuff here. Definitely price bookmarking for revisiting. I surprise how much effort you set to make this kind of fantastic informative website.