I.Guide to Sintered Gears: Gear Manufacturing
Powder Metal Gears, often referred to as Sintered Gears, represent a groundbreaking advancement in the field of gear manufacturing. Utilizing the principles of Powder Metallurgy (P/M), these gears are created through processes like sintering and powder forging. In this comprehensive guide, we delve into the intricacies of powdered metal gears, exploring their types, manufacturing processes, applications across diverse industries, and much more.
II. Types of Powder Metal Gears
The foundation of powder metal gears (Sintered Gears) technology lies in various gear types, each designed to cater to specific applications. Spur gears serve as the fundamental building blocks, providing a robust base. Helical gears bring precision to motion, while bevel gears seamlessly blend efficiency with innovation. Sprocket gearboxes further exemplify the evolution of gear manufacturing.
1. Spur Gears: The Foundation of Powdered Metal Gear Technology Spur gears, essential components in powdered metal gear technology, embody simplicity and durability. Their straight teeth ensure efficient power transfer, making them foundational for various applications, from automotive to industrial machinery.
III.The Manufacturing Process of Sintered Gears
Powder Metallurgy, a transformative manufacturing technique, is at the core of creating powdered metal gears. Sintering, a crucial step, imparts strength and durability. Powder forging enhances compression strength, while machine finishing ensures precision in the final product. Together, these processes contribute to the superior quality of Sintered gears.
IV.Sintered Gear Applications
Exploring the extensive applications of powdered metal gears unveils their versatility in powering a range of industries. Noteworthy applications include:
- Reduction Gears: Efficiently lowering the rotational speed of a driving device to enhance output torque, ensuring optimal performance in various machinery.
- Transmission Gear Systems: Vital components in the transmission systems of automobiles and machinery, delivering seamless power transfer and reliable functionality.
- Decoupled Gears: Revolutionizing transmission stability with specially designed gears, ensuring minimized vibrations and improved overall performance.
- Mass Balancer Gears: Counteracting undesired vibrations in engines and machinery, enhancing system balance and reducing wear on critical components.
- Camshafts and Crankshafts: Precision-crafted gears contribute to the smooth operation of engines, regulating valve and piston movements for optimal combustion.
- Oil Pump Gears: Facilitating efficient oil circulation in engines, ensuring lubrication to critical components and maintaining overall engine health.
- Scissor Gears: Employed in various mechanisms, scissor gears provide synchronized movement, crucial in applications like scissor lifts and other lifting equipment.
- Planetary Gears: Essential in planetary gear systems, distributing load and torque evenly, commonly used in automatic transmissions.
- Drive Pinions and Planet Gears: Integral components in gear assemblies, enabling controlled movement and power distribution in diverse machinery.
- Sprockets and Pulleys for Connecting Systems: Serving as connectors in power transmission systems, facilitating smooth and controlled movement.
- Fluid Transfer Gears: Applied in pumps and fluid handling equipment, ensuring precise fluid transfer in various industrial processes.
These applications showcase the adaptability of powdered metal gears across different sectors, emphasizing their indispensable role in powering machinery and systems.
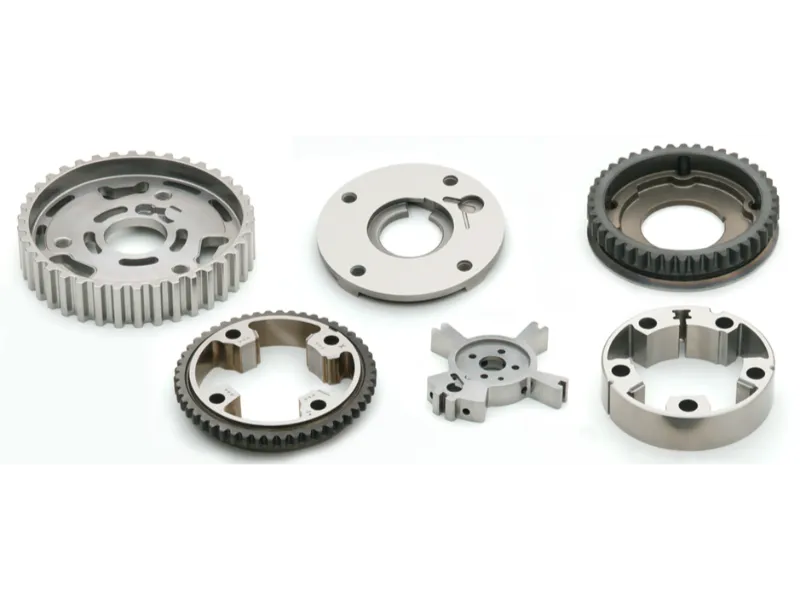
V. Advantages and Limitations of Sintered Gears
The advantages of powdered metal gears include enhanced efficiency, cost-effectiveness, and versatility in applications. However, like any manufacturing process, there are limitations that warrant consideration. Addressing these challenges is crucial for optimizing P/M gear manufacturing.
Limitations of Sintered Gears: Strength, Size, and Material Constraints
VI. Applications Across Industries
Powdered metal gears find applications across a spectrum of industries. In the automotive sector, they drive innovation on the roads, while in the medical industry, precision in healthcare equipment is paramount. From agriculture to marine applications, these gears enhance performance in various fields.Welle’s plant facilities are certified to IATF 16949 and ISO 9001.
- Automotive: Driving the wheels of innovation in the automotive sector, powdered metal gears contribute to efficient transmissions, enhancing overall vehicle performance and fuel efficiency.Automotive components include but not limited to:Engine Components: Used to produce complex engine components such as gears, sprockets, and valve guides.Transmission Components: Used to produce transmission components such as shift forks, synchronizer hubs, and planetary gears.
Steering Components: Used to produce steering components such as power steering rack guides, pinion gears, and rack and pinion housings.
Fuel System Components: Used to produce fuel system components such as injector nozzles and fuel rails.
Suspension Components: Used to produce suspension components such as ball studs, clevis pins, and shock absorber rods.
Brake System Components: Used to produce brake system components such as brake caliper pistons, anti-lock brake system (ABS) sensor rings, and brake shoe adjusters.
Electrical System Components: Used to produce electrical system components such as sensors, connectors, and terminals.
We also provide premium quality and tight-tolerance, fine-pitched Sintered gears and we manufacture and assemble small planetary gear drives.
- Power Tools: Powering precision and durability in various tools, metal powder gears ensure reliable operation, making them essential in the power tools manufacturing industry.Power& Hand tools rely on gears for torque and speed control. Welle produced gears offer unparalleled precision and durability, ensuring the smooth and efficient operation of the tools.
- Medical Industry: In healthcare equipment, precision is paramount. Sintered gears play a crucial role in ensuring the accuracy and reliability of medical devices, contributing to advancements in patient care. Such as: Gears, Gearboxes, Planetary drives, medical dispensing devices and more.Our ISO 9001:2015 certified facility fabricates precision small medical devices and components to the tightest tolerances in conformance with AGMA Class 8 Gearing.
- Domestic Appliances: Enhancing the efficiency of everyday appliances, from washing machines to blenders, powdered metal gears provide longevity and smooth operation in household devices.
- eMobility: Paving the way for sustainable transportation, powdered metal gears are integral to the electric mobility revolution, ensuring smooth transitions in electric vehicles.
- Agriculture: Powering performance in the field, sintered gears contribute to the agricultural sector by ensuring reliable operation in machinery such as tractors and harvesters.
- Power Transmission: Playing a vital role in the transmission of power, powdered metal gears contribute to efficient and reliable power transfer in various industrial applications.
- Fluid Handling: In pumps and fluid transfer systems, sintered gears ensure precision in fluid handling, contributing to the seamless operation of industrial processes.
- Marine: Navigating waters demands reliability. Powdered metal gears find applications in marine equipment, ensuring robust performance in critical components.
- Recreational: Powering recreational vehicles and equipment, these gears enhance the performance and durability of products in the leisure and sports industry.
- Material Handling: In material handling equipment, sintered gears contribute to the smooth and efficient movement of goods, optimizing logistics and manufacturing processes.
- Convey Technology: Essential in conveyor systems, powdered metal gears ensure precise and reliable movement in material handling and manufacturing applications.
- eBikes: In the electric bike industry, sintered gears provide the necessary power transmission for a smooth and efficient riding experience.
- Outdoor Power Equipment: From lawnmowers to chainsaws, metal powder gears contribute to the reliability and longevity of outdoor power equipment.
These applications underscore the broad-reaching impact of powdered metal gears, emphasizing their significance in powering essential components across various industries, ultimately driving innovation, efficiency, and sustainability.
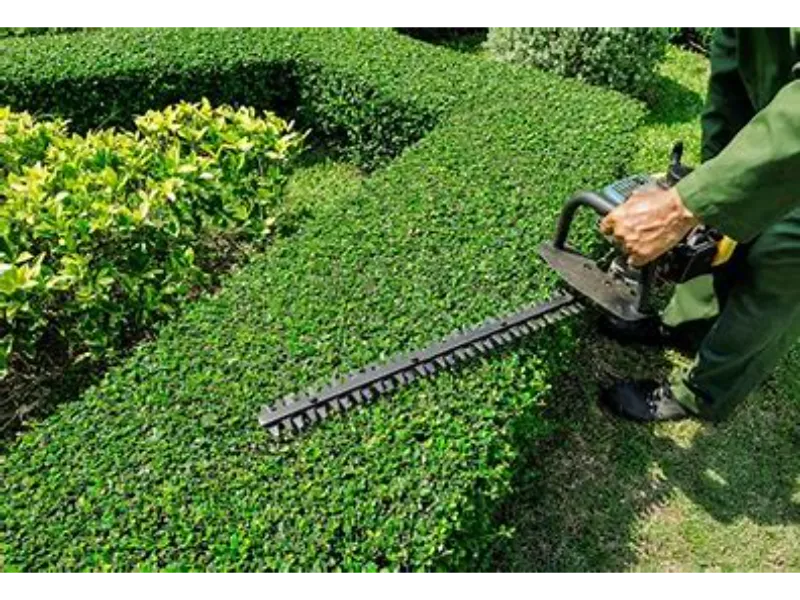
VII. Materials Used in Sintered Gears
The materials used in powdered metal gears play a pivotal role in their performance. From copper and iron alloys to bronze, brass, carbon steel, and stainless steel alloys, manufacturers have a spectrum of choices to meet specific requirements.
Harnessing powder metallurgy, gears of diverse sizes and profiles—straight, double, or helical—can be crafted from various steels. Notably, sinterhardened steels (e.g., SAE 4600 series) exhibit high hardness post-sintering, eliminating the need for additional heat treatment. Copper and iron alloys, including brass (e.g., C26000, C27000) and bronze (e.g., C51000, C62300), are commonly employed. Brass features adjustable zinc levels for ductility, and bronze offers superior strength, corrosion resistance, and wear resistance. Carbon steel (e.g., AISI 1018, AISI 1045), known for machinability and wear resistance, remains cost-effective. Stainless steel alloys (e.g., AISI 300 series), with varying compositions, provide different levels of wear and corrosion resistance, offering versatility in gear manufacturing.
VIII. American Gear Manufacturers Association (AGMA) Standards
AGMA sets the standards for gear manufacturing excellence, ensuring that powdered metal gears adhere to stringent quality benchmarks. These standards contribute to the reliability and performance of gears in diverse applications.
IX. Common Questions About Powdered Metal Gears
- What makes powdered metal gears an ideal choice in manufacturing?Re:Powdered metal gears excel due to their direct geometry shaping in the compacting operation, a feature of powder metallurgy technology.
- How does powder metallurgy technology shape gear geometry directly?Re: Powder metallurgy enables direct shaping of gear geometry, allowing for versatile sizes and profiles (straight, double, or helical).
- Which steels, including specific alloy grades, are commonly used in powdered metal gears? Re: Common materials include sinterhardened steels (e.g., SAE 4600 series), carbon steel (e.g., AISI 1018, AISI 1045), and copper/iron alloys like brass (C26000, C27000) and bronze (C51000, C62300).
- Why are sinterhardened steels significant in gear production? Re:Sinterhardened steels, exemplified by the SAE 4600 series, exhibit high hardness post-sintering, eliminating the need for additional heat treatment.
- What are the key attributes of copper and iron alloys, such as brass and bronze, in gear manufacturing? Re: Copper alloys, such as brass (C26000, C27000), offer ductility, while bronze (C51000, C62300) provides superior strength, corrosion resistance, and wear resistance.
- Can you explain the advantages and variations in stainless steel alloys used for powdered metal gears? Re:Stainless steel alloys (e.g., AISI 300 series) with diverse compositions offer different levels of wear and corrosion resistance, enhancing the versatility of powdered metal gears.