Understanding the Basics of Cold Forming
Cold forming, also known as cold heading, is a highly efficient, high-speed manufacturing process used to shape metal at room temperature. By applying compressive force through dies and punches, manufacturers can create intricate components—often without removing any material—resulting in superior strength, dimensional accuracy, and minimal waste.
What is Cold Forming?
Cold forming is a chipless metal forming process that reshapes metal wire or rod into a specific configuration without the need for heating. The process relies on plastic deformation—forcing the metal beyond its yield strength but below its melting point—to permanently alter its shape while maintaining its internal grain structure.
Unlike machining or hot forging, cold forming maintains material volume and integrity, often improving the mechanical properties of the final product.
Cold Forming Process Overview
The cold forming process starts with wire or coil feedstock, typically made of cold-heading quality steel or other ductile metals. Here’s a general breakdown of the process:
- Wire Cutting (Slug Formation): The wire is cut into precise lengths (slugs) using a cut-off knife integrated into the machine.
- Initial Forming (Cold Heading): A punch applies high pressure to the slug inside a die to begin shaping. This may include upsetting, extruding, or reducing.
- Multi-Station Forming: In modern cold formers, the part progresses through multiple die stations. Each station performs specific operations such as:
- Piercing
- Blank Rolling
- Pointing
- Thread Rolling
- Trimming
- Sizing
- Transfer Mechanism: Precision transfer fingers move the part between stations to ensure alignment and timing.
- Final Ejection: Knock-out pins eject the completed part once forming is complete.
This sequence can produce up to 400 parts per minute with near-net-shape results, requiring little to no secondary machining.
Materials Used in Cold Forming
Material selection is critical in cold forming, as not all metals respond equally well to the stress of deformation at room temperature. Suitable materials must be ductile, clean, and uniform in composition.
Common Cold Forming Materials:
- Cold Heading Quality (CHQ) Steels – carbon and alloy grades specifically designed for heading
- Stainless Steels – corrosion-resistant and formable grades like AISI 302, 304, and 430
- Tempered Alloy Steels – for high-strength applications
- Ferritic-Martensitic Duplex Steels – for enhanced toughness and fatigue resistance
- Aluminum, Brass, and Copper Alloys – for lighter-duty or electrical applications
Modern alloy producers also develop special formulations optimized for cold formability, including specific AISI grades with controlled inclusions for better die life and forming ease.
Tooling in Cold Forming: Dies, Punches, and Transfer Systems
Cold forming tooling must withstand extreme pressures and cycle counts. The two most critical components are dies and punches, supported by a precise transfer system for multi-stage operations.
Cold Forming Dies
Dies are the stationary components mounted in the header that shape and hold the material under pressure. Typically constructed in multi-piece assemblies, dies absorb significant radial pressure during forming.
- Casing Support: Dies are press-fit into hardened steel casings to distribute load and extend lifespan.
- Knock-Out Pins: Located behind the die, these pins eject the part once forming is complete.
Cold Forming Punches
Punches are smaller moving components attached to the ram or reciprocating head of the machine. Though they experience less pressure than dies, punches must maintain precision under load.
- Shaping Roles: Punches form part features like screw heads or recessed cavities.
- Back Extrusion: Some punches are designed to support backward extrusion of complex shapes.
Transfer System
The transfer system ensures the part moves accurately between stations. In multi-die cold headers, the transfer system often includes fingers or grippers that:
- Hold parts firmly during transport
- Prevent part slippage or misalignment
- Are critical in forming larger or asymmetric parts
Proper synchronization of transfer timing is vital to prevent forming defects like head misalignment or shoulder droop.
Cold Heading Machinery
Modern cold heading machines are high-speed, automated units that can handle a wide range of part sizes and shapes. They utilize cams, bevel gears, and slider mechanisms to drive the punches and synchronize die interactions.
Key Features of Cold Formers:
- Multi-Station Capabilities: From 1-die/2-blow to 6-die/6-blow configurations
- CNC-Adjustable Settings: For rapid tool changeovers and fine-tuned controls
- Quiet Operation Designs: Improved mechanisms reduce noise and impact force
- Servo-Based Transfers: Enhance speed and part placement accuracy
Advancements have made it possible to work with high-temperature alloys and exotic materials in cold forming, expanding its use across aerospace, automotive, and medical device industries.
Innovations in Cold Forming
Recent innovations in cold heading include:
- Advanced Tool Steels: Extend die and punch life
- Multi-Diameter Forming Capabilities: Reduce secondary processes
- Integration with Thread Rolling and Trimming: For complete part finishing
- Predictive Maintenance Sensors: Increase uptime and productivity
- Environmentally Friendly Lubricants: Support cleaner, more sustainable production
Types of Cold Heading Equipment
Cold heading machines are central to the cold forming industry and are typically categorized into two main types:
- Cold Headers
- Part Formers
Both use horizontal rams and fixed bolsters to reshape metal wire into precision components. These machines range from simple single-die systems to complex multi-die, multi-blow machines—some with up to seven dies—enabling high-volume production of bolts, screws, rivets, and custom hardware.
Equipment Capabilities and Automation
The output capacity of a cold heading facility is directly tied to the number and sophistication of machines in operation. Multi-station headers allow for the manufacture of complex geometries with fewer secondary processes. Automated systems can include wire feeders, material preparation units, and inline inspection modules—ensuring high throughput, process stability, and compliance with stringent industry standards.
Key Cold Heading Tooling Components
Effective cold heading relies on two essential tools:
- Punches: Apply compressive force to shape the workpiece.
- Dies: Form and define the final dimensions of the part.
This tooling setup allows manufacturers to produce intricate features while maintaining tight tolerances, even on high-strength alloy steel, stainless steel, or copper materials.
Core Cold Heading Processes
1. Cold Heading by Upsetting
Upsetting is the foundational cold heading method that increases a workpiece’s diameter by compressing metal into a confined area—typically to form heads on bolts or screws. The process begins with a wire blank cut to a specific length from a coil, then fed into the machine for shaping.
First and Finish Upset Blows
Since only a limited volume of material can be upset in a single blow (around two diameters), manufacturers often use multiple blows or stages to form larger or more complex heads.
- Single-die headers typically handle up to 1.25 diameters of upset.
- Two-blow headers can form up to 4.5 diameters or more, depending on the material and machine capability.
Careful planning of the upset ratio (blank length ÷ wire diameter) is critical to avoid part defects such as cracking or cold shuts. Advanced simulation tools help optimize these parameters for consistent, defect-free production.
2. Cold Heading Extrusion Processes
Extrusion in cold heading refers to shaping material by forcing it through a die, either forward or reverse, to alter its cross-section. This method is ideal for manufacturing solid and hollow parts with high material utilization and minimal waste.
Forward Extrusion
In this process, metal flows in the same direction as the punch, creating elongated parts with reduced diameter. It’s widely used to produce:
- Threaded rods
- Stepped shafts
- Long fastener blanks
Reverse Extrusion
Here, material is forced backward around the punch, ideal for forming:
- Hollow features
- Recessed cavities
- Nuts, sleeves, or bushings
Reverse extrusion is also used to create internal drive recesses (e.g., Phillips, Torx) in screw heads.
3. Variants of Extrusion Techniques
Open Extrusion
- Metal is partially contained by the tooling.
- Allows for longer extrusions but requires higher force.
- Suitable for wire-formed products or simple rods.
Proper alignment and support are essential to prevent buckling or distortion.
Trapped (Contained) Extrusion
- The workpiece is fully enclosed during extrusion.
- Enables greater dimensional reduction (up to 75%) under high compressive force.
- Ideal for:
- Stepped components
- Complex head-shank relationships
- Precision parts with tight tolerances
Radial extrusion dies are often used to reduce die stress and ensure smooth material flow.
Auxiliary Operations in Cold Heading
To maximize efficiency and eliminate secondary machining, modern cold heading systems often integrate:
- Trimming: Removes excess material to form precise head shapes (e.g., hex heads).
- Piercing: Creates holes or internal bores in nuts or bushings.
These additions help produce net-shape or near-net-shape components, optimizing cycle times and lowering unit costs.
Cold Heading vs. Cold Forming: What’s the Difference?
While often used interchangeably, there are subtle distinctions:
- Cold Heading specifically refers to forming a head on a fastener or part, often via upsetting.
- Cold Forming encompasses a broader range of techniques, including heading, extrusion, and other deformation methods without heat.
Understanding this difference helps in selecting the right process for part geometry, material behavior, and strength requirements.
Cold Forming vs. Hot Forging
Criteria | Cold Forming | Hot Forging |
Temperature | Room Temperature | High Temperature (~1200°C for steel) |
Material Strength | Increases due to grain flow alignment | May reduce due to grain growth |
Surface Finish | Excellent | Often requires machining |
Energy Consumption | Lower | Higher |
Speed | Faster production (100-400 parts/min) | Slower production rates |
Applications and Advantages of Cold Heading Forming
Cold heading, also known as cold forming, is a widely used manufacturing process for producing high-quality, high-volume fasteners and precision components without applying heat. This technique reshapes metal at room temperature using compressive force, resulting in minimal material waste and enhanced mechanical properties.
Applications of Cold Heading
Cold heading is primarily used to manufacture fasteners such as bolts, screws, rivets, pins, and studs. These components are essential in industries that demand strength, consistency, and cost-efficiency.
Industrial Sectors Utilizing Cold Heading:
- Automotive: Wheel bolts, engine studs, brake pins
- Aerospace: Aircraft rivets, specialty fasteners
- Construction: Anchors, threaded rods, rebar components
- Electronics: Micro screws, contact pins, terminals
- Consumer Goods: Fasteners for appliances, furniture, and tools
To achieve optimal performance, cold heading requires high-quality raw materials. A common choice is cold heading quality (CHQ) steel, which offers superior ductility and consistent chemical composition. Additionally, tempered alloy steels, structural steels, and ferritic-martensitic duplex steels are used depending on the application requirements.
Advantages of Cold Heading Forming
Cold heading provides a number of advantages over conventional machining or hot forming methods, particularly for high-volume manufacturing.
1. High-Speed Production
Cold forming is exceptionally efficient. Advanced machines can produce up to 100 parts per minute, making it ideal for mass production. This rapid cycle time also ensures dimensional uniformity and process repeatability, reducing inspection and rework.
2. Superior Strength and Grain Structure
Since the material is formed at ambient temperature without cutting or melting, the metal’s grain flow is preserved and reoriented along the contours of the part. This natural grain alignment enhances tensile strength, fatigue resistance, and impact durability—making cold headed components stronger than machined or cast equivalents.
3. Material Efficiency
Cold heading produces near-net-shape parts, minimizing scrap and eliminating the need for extensive secondary machining. This not only reduces raw material costs but also contributes to more sustainable manufacturing practices.
4. Lower Energy Consumption
Unlike hot forging or casting, cold forming does not require the use of furnaces or heat treatment during forming. As a result, it significantly reduces energy consumption, operating costs, and environmental footprint.
Limitations of Cold Heading
While cold heading offers numerous benefits, it is not suitable for all manufacturing scenarios. Below are some common challenges:
1. Size Restrictions
As the diameter of the part increases, so does the required forming pressure. Although large cold headers exist, they are often cost-prohibitive and less efficient for oversized components. For very large fasteners or custom geometries, CNC machining or hot forging may be more practical alternatives.
2. Material Constraints
Not all metals respond well to cold forming. Brittle, high-carbon steels or materials with poor ductility may crack or fail during the process. Therefore, material selection is critical to ensuring product quality. Manufacturers must choose alloys that balance formability, strength, and end-use performance.
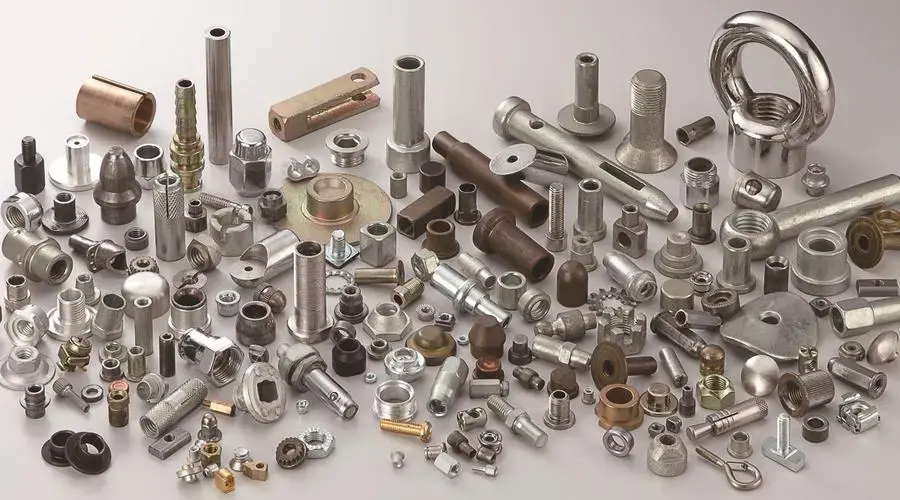
Cold Heading Industry Insights
Popular Questions (People Also Ask)
1.What is cold heading?
Cold heading is a cold forming process that uses dies and punches to form the heads of fasteners without heating the metal.
2.How does cold forming work in manufacturing?
It reshapes metal at room temperature using compressive force, improving strength and reducing waste.
3.What is bolt heading process?
Bolt heading is the operation of forming the head on a bolt using cold heading machines.
4.What’s the difference between cold heading and cold forming?
Cold heading is a type of cold forming specifically focused on forming the head of fasteners, while cold forming includes other processes like extrusion and rolling.
5.What are examples of cold headed conversions?
Examples include converting standard bolts into multi-diameter, stepped, or internally threaded components.
Conclusion
Cold heading and cold forming processes are revolutionizing high-volume metal part manufacturing. With advanced cold forming machinery, precision tooling, and demand across sectors, the process continues to evolve with innovation and scale.
China’s best cold forming machine factories and cold forming tooling suppliers are leading the way with smart automation and CNC-integrated cold former machines, shaping the future of cold heading fasteners, cold headed steel, and cold forging tools for precision parts.