Materials Standards for PM Structural Parts Released
Powder metallurgy (PM) is a critical manufacturing method, revolutionizing how structural parts are made in many industries. Using PM techniques makes parts cheaper, better, and faster. Following strict material guidelines ensures high quality and reliability. The recent release of MPIF Standard 35 is a big deal. It provides detailed rules for making PM parts, helping manufacturers achieve the best results.
The MPIF (Metal Powder Industries Federation) standards cover a wide range of material types used in powder metallurgy for structural parts. Here are some common material types along with their applications and functions:
PM Copper-Based Materials
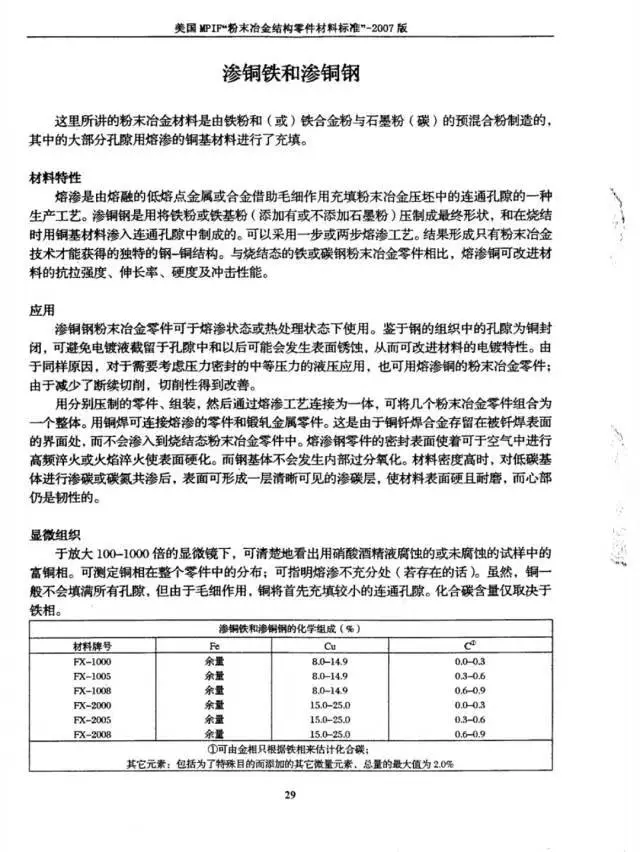
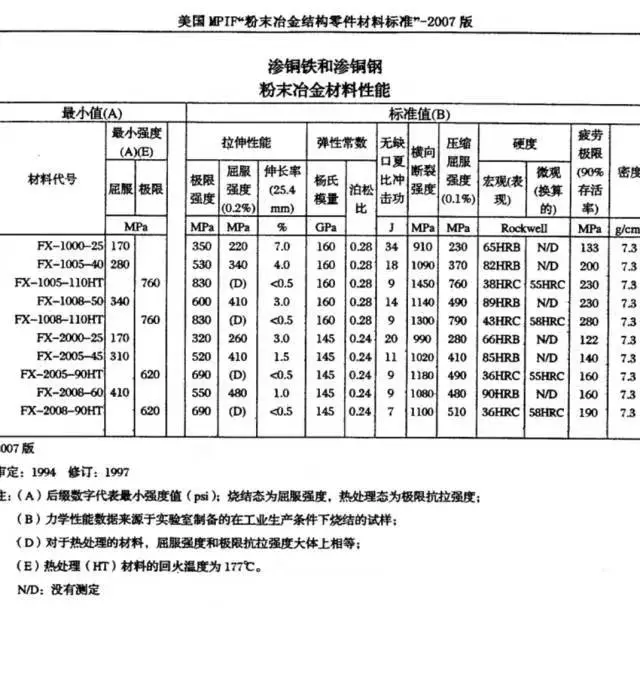
PM Iron-Based Materials
Function: These materials provide high strength, wear resistance, and dimensional stability, making them suitable for components subjected to heavy loads and harsh operating conditions.
Application: Iron-based materials are widely used in automotive, industrial machinery, and consumer goods applications due to their excellent mechanical properties and cost-effectiveness.
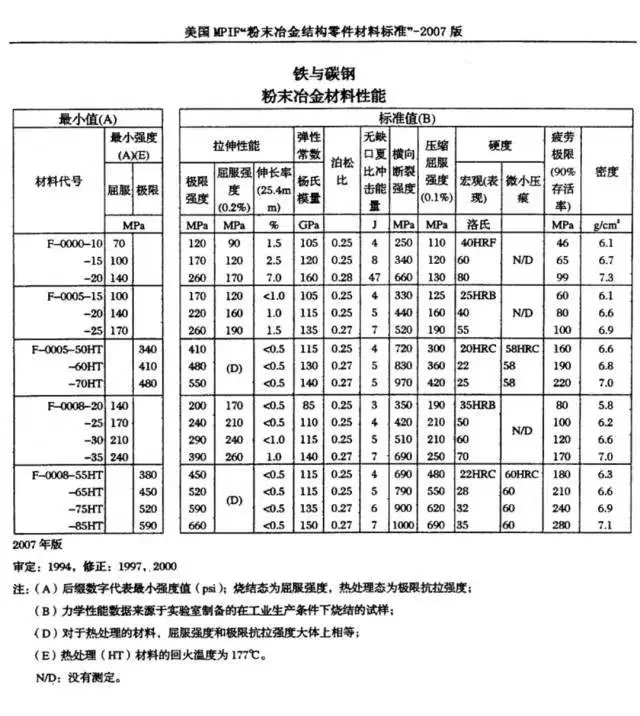
PM Nickel-Based Materials
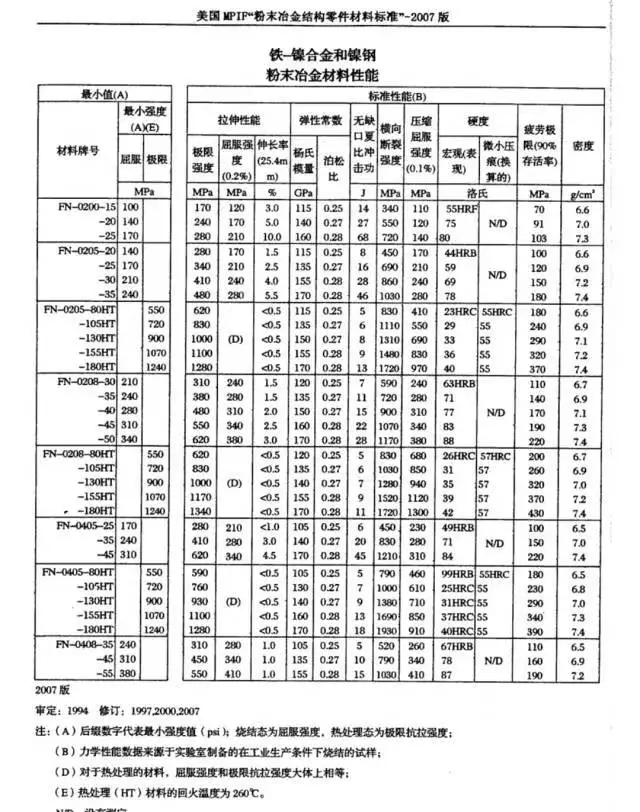
PM Steel-Based Materials
Function: Steel-based materials offer superior mechanical properties, including high tensile strength, fatigue resistance, and toughness, making them ideal for structural components requiring durability and reliability.
Application: Steel-based materials find applications in automotive, aerospace, and industrial equipment due to their versatility and strength-to-weight ratio.
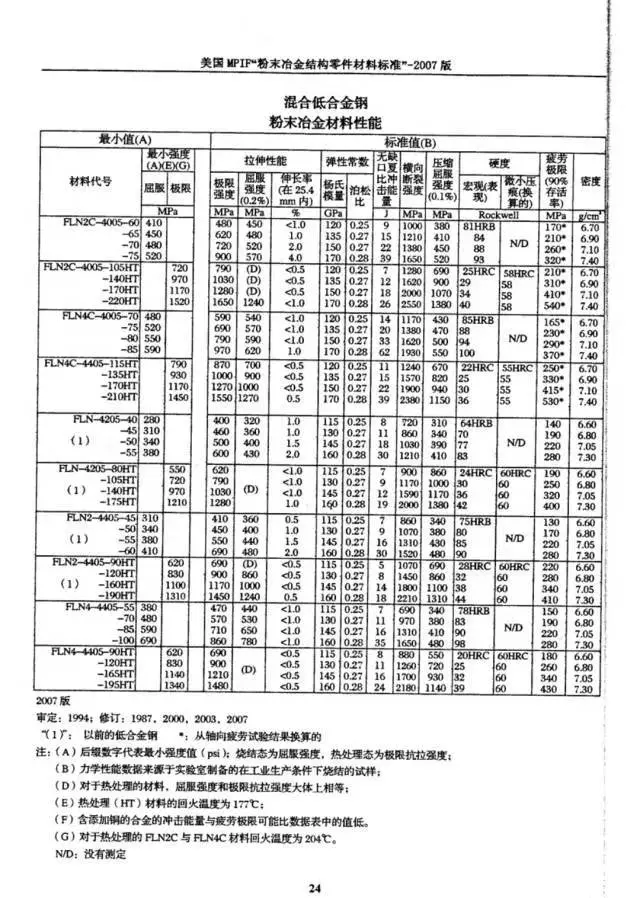
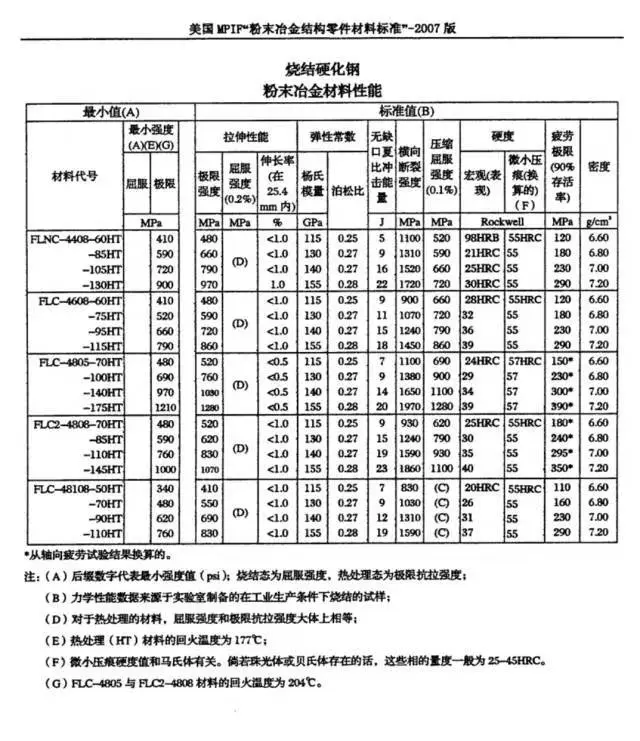
MPIF Material Sintering Types
In the realm of powder metallurgy (PM), adhering to meticulous material guidelines is paramount to ensuring the quality, performance, and reliability of structural parts. From metal sintering to selective laser sintering powder, a multitude of techniques and processes are employed to transform powdered materials into functional components across diverse industries.
Metal Sintering: Metal sintering is a fundamental process in PM, involving the compacting and heating of metal powders to form solid structures with enhanced mechanical properties.
Selective Laser Sintering Powder: Selective laser sintering powder enables the precise fabrication of complex geometries by selectively melting layers of powdered material using a laser.
Powder Forming: Powder forming techniques, such as powder compaction and powder extrusion, shape powdered materials into desired forms before sintering or injection molding.
Powder Compaction: Powder compaction involves compressing powdered materials into a desired shape or form using mechanical or hydraulic presses, ensuring uniform density and integrity.
Metal Injection Molding (MIM): Powder injection molding (PIM) combines the versatility of injection molding with the versatility of powder metallurgy, enabling the production of complex, high-precision components.
Powder Sintering: Powder sintering is the process of heating compacted powdered materials to a temperature below their melting point, causing them to bond and form a solid mass with improved mechanical properties.
Isostatic Compaction: Isostatic compaction applies uniform pressure to powdered materials from all directions, resulting in components with consistent density and structural integrity.
Cold Isostatic Compaction: Cold isostatic compaction subjects powdered materials to high pressure in a liquid medium at room temperature, facilitating the production of complex shapes with minimal defects.
Powder Metallurgy (PM): Powder metallurgy (PM) encompasses a range of techniques for fabricating metal parts from powdered materials, offering advantages in cost, complexity, and material utilization.
In powder metallurgy, every step matters, from pre-sintering to post-processing. By following established material guidelines, Welleshaft manufacturers can make the most of PM, creating innovative and high-quality components.