Elevating Aerospace and Defense: Precision Engineering Unveiled
Introduction to Advanced Engineering Solutions in Aerospace and Defense highlights cutting-edge technologies and innovations that enhance performance, safety, and reliability in the aerospace sector.
- CNC Machining in Aerospace
- Casting Techniques in Defense
- Fasteners in Aerospace Engineering
- Forging Strength in Defense Applications
- Sintering and Metal Injection Molding
- Surface Finishing for Aerospace Components
- Materials Innovation in Aerospace Engineering
- Common Processes and Types in Aerospace Manufacturing
- Components Vital to Aerospace and Defense
- Applications Across Aerospace and Defense
- Challenges and Innovations in Aerospace Manufacturing
- Why Choose Welle for Aerospace and Defense Components Manufacturing?
Welle Fasteners and custom Casting, Sintering and Machining spare parts have become more widely used for aircraft carriers, submarines, and other naval vessels.
-
Introduction
-
- Precision engineering powers Advanced Engineering Solutions in Aerospace and Defense, ensuring unmatched accuracy, reliability, and technological excellence in every component.
-
-
CNC Machining in Aerospace
- CNC machining delivers Advanced Engineering Solutions in Aerospace and Defense, enabling precise, repeatable, and complex component manufacturing with tight tolerances.
- Advancements in CNC machining ensure unparalleled accuracy and efficiency, making it the cornerstone of crafting intricate aerospace parts. Its applications extend from manufacturing aircraft components to spacecraft parts, highlighting its versatility. The advantages lie in its ability to achieve complex geometries, maintain tight tolerances, and enhance overall production efficiency. Embraced across various industries, CNC machining in aerospace sets the standard for reliability and innovation in manufacturing processes.
- CNC machining in aerospace, governed by the principles of computer numerical control, employs aerospace-grade alloys, such as Titanium (Ti-6Al-4V) and Aluminum (7075-T6), alongside advanced composites. These material choices play a vital role in ensuring optimal strength and durability in component manufacturing. The precision of CNC machining, combined with the selection of specific materials, underscores its crucial contribution to aerospace systems, meeting stringent standards and advancing the industry’s technological frontiers.
-
Casting Techniques in Defense
-
Defense industries adopt advanced casting to manufacture precise, complex components for mission-critical systems.
-
Investment casting produces intricate, high-strength parts essential for modern military equipment.
-
Precision casting enhances dimensional accuracy and ensures structural reliability in defense components.
-
Engineers improve defense systems by applying innovative casting processes to critical hardware.
-
Manufacturers use Titanium (Ti-6Al-4V) and Stainless Steel (17-4 PH) for superior strength and durability.
-
Casting techniques enable lightweight, high-performance parts for extreme operational environments.
-
Defense sectors cast firearm components, missile parts, and radar system housings.
-
Precision casting supports complex geometries required for guidance and surveillance systems.
-
Foundries produce engine components and gear systems using cutting-edge casting methods.
-
Advanced casting strengthens defense capabilities with reliable, innovative component solutions.
-
-
Fasteners in Aerospace Engineering
- Fasteners in aerospace engineering serve as critical connections, ensuring the structural integrity and safety of aircraft components. From securing panels and joints to supporting crucial load-bearing elements, these fasteners play an indispensable role in the complex web of aerospace systems. Precision-engineered and designed for reliability, they exemplify the meticulous attention to detail necessary for the demanding requirements of aerospace engineering, where every connection is a key link in ensuring the safety and functionality of the aircraft.
- The significance of fasteners in aerospace engineering lies in their role as essential components for secure and reliable aircraft assembly. High-performance fasteners, crafted with precision, ensure the structural integrity of critical elements. From securing aircraft panels to holding together intricate components, these fasteners contribute to the seamless assembly and overall safety of aerospace systems. Their importance extends beyond mere connections, exemplifying the meticulous engineering required for high-stakes applications in the aviation industry.
- In the realm of aerospace engineering, the diversity of fasteners is paramount. Ranging from rivets and bolts to nuts and screws, each type plays a specific role in securing aircraft components. Crafted from high-strength materials such as Titanium (Ti-6Al-4V) and Stainless Steel (A286), these fasteners withstand extreme conditions. Their role extends beyond mere connections, ensuring the structural integrity and safety of critical aerospace components, reflecting the meticulous engineering required for aviation excellence.
- Here are some of the applications of fasteners, but not limited to:Including aircraft engine, aircraft Panel Fastener Kits, Rivets, Pins, Washers, Nuts, Ferrules, airframe and cockpit avionics, helicopters and rotary wings and missile applications, Naval and Marine Fasteners, and more.
-
Forging Strength in Defense Applications
- Forging strength takes center stage in defense applications, where the robustness of components is paramount. The forging process, utilizing high-strength materials such as Alloy Steel and Titanium (Ti-6Al-4V), ensures the creation of resilient components. From critical structural elements to heavy-duty gear systems, forging imparts durability and reliability. This technique stands as a cornerstone in fortifying defense applications, providing components with the strength to withstand extreme conditions and operational demands.
- Forging strength in defense applications represents a transformative process where metal is shaped under immense pressure, enhancing its structural integrity. This method ensures superior grain structure and eliminates weak points, resulting in components with heightened durability. Whether crafting armor plates or critical gear systems, forging stands as a linchpin, fortifying defense applications with unparalleled strength and resilience, making it an indispensable technique in the arsenal of defense manufacturing.
- Forging strength in defense applications involves diverse processes like closed-die and open-die forging, utilizing materials such as Alloy Steel and Titanium (Ti-6Al-4V). The advantages lie in imparting superior mechanical properties, critical for military applications. From crafting robust weapon components to heavy-duty vehicle parts, forging ensures unmatched strength and reliability in defense systems, embodying a vital aspect of military-grade manufacturing.
-
Sintering and Metal Injection Molding
- Sintering and Metal Injection Molding epitomize precision in production, essential in crafting intricate components for military applications. These advanced manufacturing techniques involve the compacting of metal powders, creating components with exceptional accuracy. In the military domain, this precision is crucial, ensuring the reliability and functionality of mission-critical parts. Sintering and Metal Injection Molding stand as pillars in achieving intricate designs and maintaining the high standards required for military-grade components.
- In aerospace and defense, Sintering and Metal Injection Molding play a pivotal role in producing intricate components with precision. By compacting metal powders under high heat, these advanced techniques create complex, high-strength parts crucial for aerospace systems and defense applications. This precision ensures the reliability and performance necessary for mission-critical components, establishing Sintering and Metal Injection Molding as indispensable processes in advancing technology within the aerospace and defense industries.
- In the realm of Sintering and Metal Injection Molding, materials of varying grades come into play. Common material specifications include Stainless Steel (e.g., 316L), Titanium alloys (e.g., Ti-6Al-4V), and other specialized alloys tailored to specific applications. These material grades underscore the versatility of these manufacturing processes in creating components with distinct properties, catering to the exacting requirements of diverse industries.
-
Surface Finishing for Aerospace Components
- Surface finishing for aerospace components is paramount, enhancing both durability and performance. These processes, such as anodizing and chemical conversion coating, provide protective layers, safeguarding against corrosion and wear. The meticulous application of surface finishes not only ensures the longevity of aerospace parts but also contributes to improved aerodynamics and overall performance, exemplifying the critical role of surface finishing in elevating the quality and functionality of aerospace components.
-
- Surface finishing for aerospace components employs various techniques such as anodizing, painting, and passivation. These applications extend across critical aerospace parts, offering advantages like enhanced corrosion resistance, improved aesthetics, and increased durability. The meticulous selection of surface finishing techniques reflects the aerospace industry’s commitment to meeting stringent standards and ensuring components not only perform at their best but also withstand the demanding environmental conditions they encounter..
-
Materials Innovation in Aerospace Engineering
- Materials innovation in aerospace engineering heralds cutting-edge solutions, propelling the industry towards new heights. From advanced composites to high-performance alloys, these innovations redefine the possibilities for aircraft design and performance. This constant pursuit of superior materials underscores the commitment to achieving lighter, stronger, and more fuel-efficient aerospace components, pushing the boundaries of what is achievable in modern aviation.
- Advancing the frontiers of aerospace engineering, materials innovation takes center stage with the integration of advanced materials. From carbon-fiber composites to high-strength alloys, these cutting-edge solutions redefine aircraft design possibilities. This commitment to incorporating advanced materials reflects the aerospace industry’s dedication to pushing boundaries, enhancing performance, and ensuring the next era of aviation stands at the forefront of technological progress.
- Materials innovation in aerospace engineering is prominently characterized by the integration of advanced composite and alloy materials. These cutting-edge solutions are revolutionizing the industry, enhancing aircraft performance and design. Composite materials, known for their lightweight and robust properties, find applications in aircraft structures, while advanced alloys contribute to improved engine efficiency and durability. This relentless pursuit of innovative materials underscores the aerospace industry’s commitment to pushing the boundaries of technology for superior performance and sustainability.
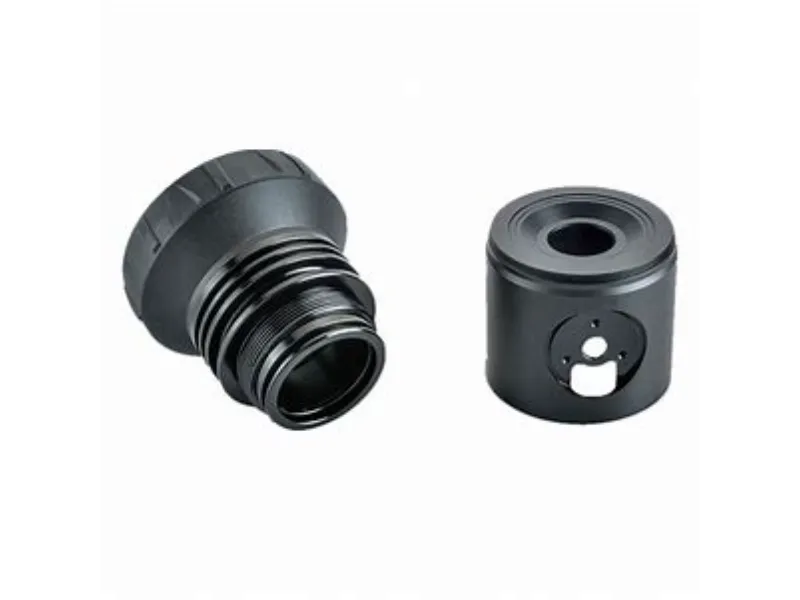
-
Common Processes and Types in Aerospace Manufacturing
- Aerospace manufacturing thrives on the diversity of common processes and types, ensuring a comprehensive approach to production. From precision CNC machining to intricate casting techniques, these processes collectively contribute to the intricate web of creating high-performance aerospace components. Embracing this diversity is crucial for meeting the industry’s rigorous standards, enabling the production of components that withstand the demanding conditions of aerospace applications while maintaining the highest standards of quality and reliability.
- The realm of aerospace manufacturing encompasses various processes and types to ensure precision and quality. From CNC machining and casting techniques to forging and sintering, these diverse methodologies cater to the complex needs of producing high-performance aerospace components. The synergy of these various manufacturing processes allows the industry to achieve unparalleled standards, meeting the stringent requirements of aerospace applications and contributing to the ongoing advancements in aviation technology.
- Common processes in aerospace manufacturing span the spectrum of rapid prototyping, precision machining, and additive manufacturing. These dynamic methodologies collectively propel the industry towards innovation and efficiency. Rapid prototyping enables swift design iterations, precision machining ensures accuracy in component production, while additive manufacturing revolutionizes complex part creation. Embracing this diversity of techniques is pivotal for aerospace manufacturers, fostering a robust foundation for producing cutting-edge components that define the future of aviation.
-
Components Vital to Aerospace and Defense
- From propulsion systems driving flight to intricate avionics governing navigation, components are undeniably vital to aerospace and defense. Each element, whether it’s a high-thrust engine or a sophisticated navigation system, plays a crucial role in ensuring the efficiency, safety, and mission success of aerospace endeavors. The seamless integration of these diverse components underscores their collective significance, shaping the capabilities and reliability of aerospace and defense technologies.
- Key components, ranging from powerful engines propelling flight to intricate electronic systems governing navigation and communication, form the backbone of aerospace and defense technologies. The synergy of these vital elements ensures the seamless operation, safety, and precision required for missions. Whether it’s the thrust of engines or the sophistication of electronic controls, each component contributes indispensably to the success and capabilities of aerospace and defense systems.
- The vitality of aerospace and defense lies in key components, their functions, criticality, materials, and manufacturing processes. From powerful engines to advanced avionics, these components are the bedrock of operational success. Precision in materials and manufacturing processes ensures durability, while understanding the critical functions of each element is paramount for mission success. The intricate synergy of these components defines the reliability and capabilities of aerospace and defense technologies, safeguarding global security and technological advancement.
-
Applications Across Aerospace and Defense
- Vacuum and investment casting create essential components for aerospace and defense systems.
-
Challenges and Innovations in Aerospace Manufacturing
- Navigating the complex landscape of aerospace manufacturing presents both challenges and opportunities for innovation. Key areas include:
- Material Advancements: Overcoming material limitations and exploring advanced alloys.
- Precision Engineering: Meeting stringent tolerances and ensuring flawless component integration.
- Supply Chain Resilience: Adapting to global disruptions and enhancing supply chain robustness.
- Environmental Sustainability: Innovating greener processes and materials to meet eco-friendly standards.
- Technological Integration: Embracing AI, IoT, and automation for enhanced manufacturing efficiency.
These challenges inspire continuous innovation, driving the aerospace industry towards cutting-edge solutions.
- Navigating the complex landscape of aerospace manufacturing presents both challenges and opportunities for innovation. Key areas include:
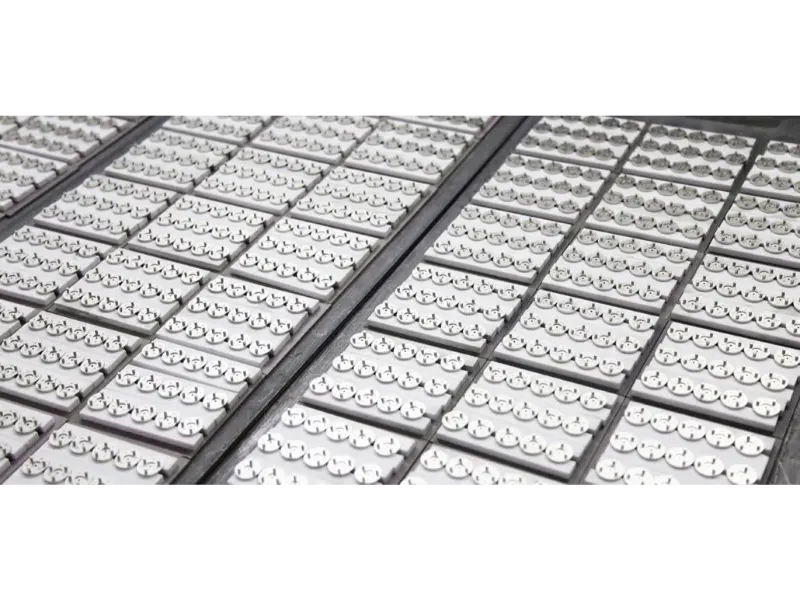
Why Choose Welle for Aerospace and Defense Components Manufacturing?
When it comes to aerospace and defense components manufacturing, welle takes center stage, setting itself apart with an unwavering commitment to excellence. We seamlessly integrate cutting-edge technology with meticulous craftsmanship to deliver unrivaled products, ensuring your peace of mind in every project.
Precision and Quality Excellence
-
Our skilled team crafts each part with precision using advanced manufacturing technology.
-
We ensure every component meets the highest quality standards with strict attention to detail.
Comprehensive Capabilities
-
Welle offers in-house plastic injection, metal injection, CNC, forging, and laser cutting services.
-
We handle custom metal, plastic, and rubber parts with full process control and fast turnaround.
Technical Expertise at Your Service
-
Our engineers bring deep expertise in metal and plastic part manufacturing.
-
We optimize processes to improve both efficiency and product quality.
Cost-Effective Solutions without Compromise
-
Welle delivers affordable solutions without sacrificing quality or performance.
-
We tailor each project to meet your cost-effectiveness goals.
Flexibility to Suit Your Needs
-
We adapt flexibly to both small-batch and large-volume production requirements.
-
Our custom manufacturing process adjusts to meet your specific needs.
Timely Delivery, Every Time
-
Welle prioritizes on-time delivery for every aerospace and defense project.
-
We meet tight deadlines to support your fast-paced industry demands.