Wear Ring Seal: Enhance Pump Performance & Durability
When it comes to maintaining optimal pump performance and extending the lifespan of your equipment, the role of wear ring seals cannot be overstated. These crucial components contribute significantly to the efficiency and durability of various pumping systems, from high-speed pneumatic applications to marine engines. In this article, we will explore the various aspects of wear ring seals, including their materials, manufacturing processes, and applications. We will also highlight Welleshaft as a trusted global supplier and contract manufacturer of wear ring seals.
Section 1: What is a Wear Ring Seal?
A wear ring seal is a crucial component designed to protect the pump shaft and housing from excessive wear and tear. Typically made from high-quality materials, wear ring seals act as a barrier to prevent abrasive particles and contaminants from entering the pump system. They help maintain a tight seal, reduce leakage, and enhance the overall performance of the pump.
What is a Sealing Ring?
A sealing ring, often used interchangeably with wear ring seals, is a component designed to create a leak-proof seal between two mating surfaces. It prevents the escape of fluids or gases, ensuring that the pump or machinery operates efficiently without any loss of performance.
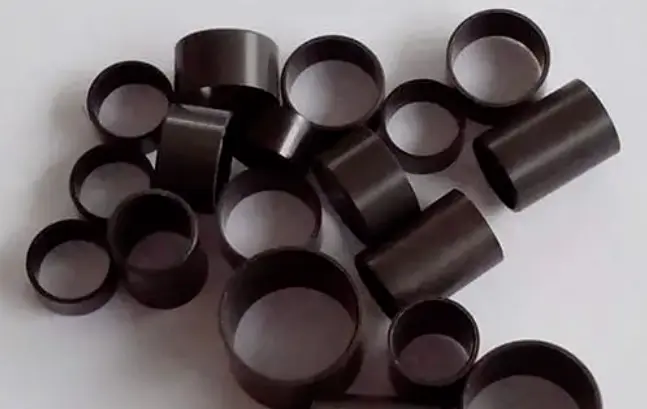
Section 2: Wear Ring Seal Materials
The choice of material for wear ring seals is critical in determining their effectiveness and longevity. Some common materials include:
1. Polyurethane (PU)
Properties: Polyurethane is known for its high abrasion resistance, flexibility, and durability. It can withstand dynamic movements and maintain its properties over a range of temperatures.
Applications: Suitable for high-speed pneumatic seals, hydraulic systems, and general industrial applications where abrasion resistance is crucial.
2. Carbon
Properties: Carbon materials, often combined with other substances like graphite, offer excellent wear resistance and can operate under high-pressure conditions. They have good thermal conductivity and low friction properties.
Applications: Used in high-pressure and high-temperature applications, such as pumps and compressors, where long-term durability and performance are essential.
3. Ceramic
Properties: Ceramic materials provide high hardness, excellent wear resistance, and can withstand extreme temperatures. They are typically used in applications requiring high durability and low friction.
Applications: Ideal for harsh operating conditions, such as in abrasive environments or where high temperatures are present. Commonly used in high-performance pumps and industrial machinery.
4. Nitrile Rubber (NBR)
Properties: Nitrile rubber is known for its good chemical resistance, flexibility, and resilience. It performs well in a range of temperatures and provides effective sealing against various fluids.
Applications: Used in a variety of sealing applications, including hydraulic systems, automotive components, and general industrial uses. It is suitable for environments where chemical resistance is important.
5. Fluorocarbon (Viton)
Properties: Fluorocarbon materials, such as Viton, offer excellent resistance to high temperatures, chemicals, and oils. They are known for their durability and long service life.
Applications: Often used in applications involving aggressive chemicals or high temperatures, such as in chemical processing or aerospace industries.
6. Metallic Alloys
Properties: Some wear ring seals are made from metallic alloys that combine high strength with wear resistance. These alloys may include stainless steel or other specialized materials.
Applications: Used in applications where high mechanical strength and wear resistance are required, such as in heavy-duty machinery or high-stress environments.
7. Composite Materials
Properties: Composite materials can be engineered to combine the properties of different materials, offering customized solutions for specific applications. They can include combinations of polymers, metals, and ceramics.
Applications: Suitable for specialized applications where a combination of properties is required, such as in advanced industrial systems or custom-engineered machinery.
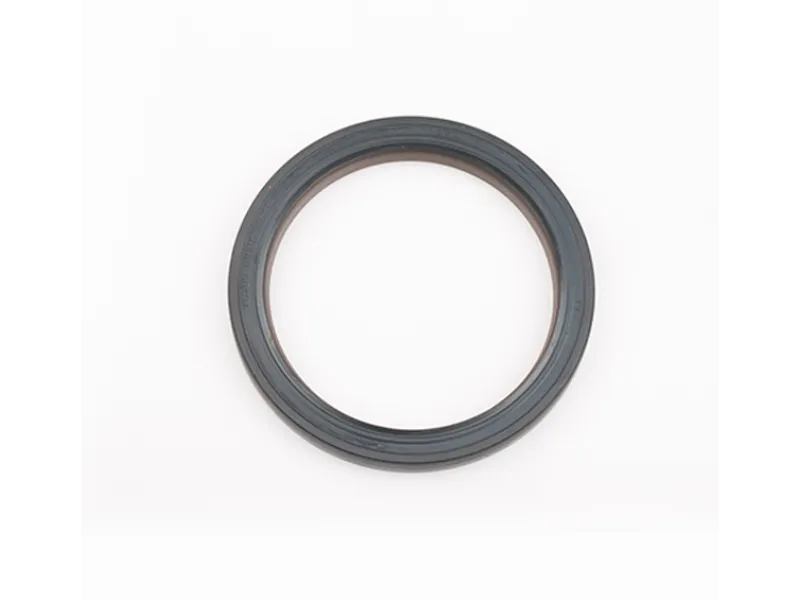
Section 3: Wear Ring Seal Manufacturing Process
The manufacturing process of wear ring seals involves several key steps:
1. Material Selection
The first step is selecting the appropriate material for the wear ring seal based on the application requirements. Common materials include:
- Polyurethane: For high abrasion resistance and flexibility.
- Carbon: For high wear resistance and durability.
- Ceramic: For high hardness and extreme conditions.
- Nitrile Rubber (NBR): For general chemical resistance and flexibility.
2. Design and Prototyping
- Design: Engineers design the wear ring seal using CAD (Computer-Aided Design) software. The design includes dimensions, tolerances, and specific features required for the application.
- Prototyping: A prototype is created to validate the design. This can involve 3D printing or machining a sample to test fit and performance.
3. Molding or Machining
Depending on the material and design, the wear ring seal is produced through either molding or machining processes:
- Molding: For materials like polyurethane or rubber, the design is created using an injection molding process. The material is heated until it melts, injected into a mold, and allowed to cool and solidify.
- Machining: For materials like carbon or ceramics, the wear ring is cut and shaped from raw material using precision machining techniques. This may involve turning, grinding, or other machining methods to achieve the final dimensions and surface finish.
4. Quality Control
- Inspection: Finished wear rings are inspected for defects such as cracks, dimensional inaccuracies, or surface imperfections. Quality control checks ensure that the wear rings meet the specified tolerances and standards.
- Testing: The wear rings are subjected to performance tests to verify their durability, wear resistance, and compatibility with the intended application. This may include pressure tests, wear simulations, and environmental testing.
5. Finishing and Assembly
- Finishing: Any additional finishing processes, such as polishing or coating, are applied to enhance the performance and appearance of the wear ring.
- Assembly: In some cases, wear rings may be assembled into larger components or systems. Proper assembly ensures that the seals function correctly within the complete system.
6. Packaging and Distribution
- Packaging: Wear ring seals are carefully packaged to prevent damage during transportation. Packaging is designed to protect the seals from physical damage and contamination.
- Distribution: The packaged seals are distributed to customers or suppliers, ready for use in various applications.
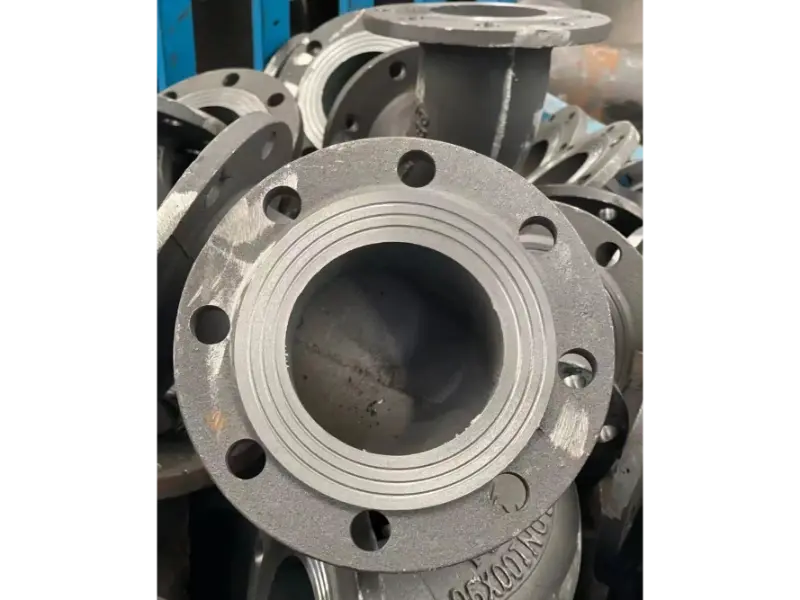
Section 4: Where Do You Wear a Seal Ring?
Seal rings are used in various applications to ensure a leak-proof seal between two surfaces, preventing fluid or gas from escaping. Here are some common locations where seal rings are employed:
1. Pumps
Seal rings are crucial in pumps to prevent leakage of fluids and protect internal components from damage. They are used between the pump shaft and the pump casing, as well as in the connections between different pump parts.
2. Hydraulic and Pneumatic Cylinders
In hydraulic and pneumatic cylinders, seal rings prevent the escape of hydraulic fluid or compressed air, maintaining system pressure and ensuring smooth operation. They are placed in grooves within the cylinder head and piston.
3. Engines
Seal rings are used in engines to prevent oil and gas leaks. Common locations include around the pistons, between the cylinder head and the engine block, and in various engine seals such as the crankshaft seal and camshaft seal.
4. Valves
In valves, seal rings are used to ensure a tight seal between the valve body and the valve stem or between different valve components. They help prevent leakage of fluids or gases through the valve.
5. Flanges and Connections
Seal rings are used between flanged joints and other types of connections to prevent leaks. They are essential in maintaining a secure seal in pipelines and other assembly points.
6. Rotary and Sliding Mechanisms
In rotary and sliding mechanisms, seal rings are used to prevent leakage and contamination. They are often found in rotating shafts and sliding parts to maintain lubrication and reduce friction.
7. Automotive Applications
Seal rings are used in various automotive applications, including transmissions, differential housings, and other critical components, to ensure leak-proof operation and protection against contaminants.
8. Industrial Equipment
In industrial equipment, seal rings are employed to maintain seals in pumps, compressors, and other machinery where leakage could result in efficiency loss or damage to the equipment.
For more information on high-quality Wear ring seals and to find the perfect solution for your application, please contact us.
Jinan Welle Metal Products Co., Ltd (Welleshaft)
Website: www.welleshaft.com
Email: [email protected]
Phone: +86-156-5017-9596
Explore our range of durable and reliable wear ring seals today!
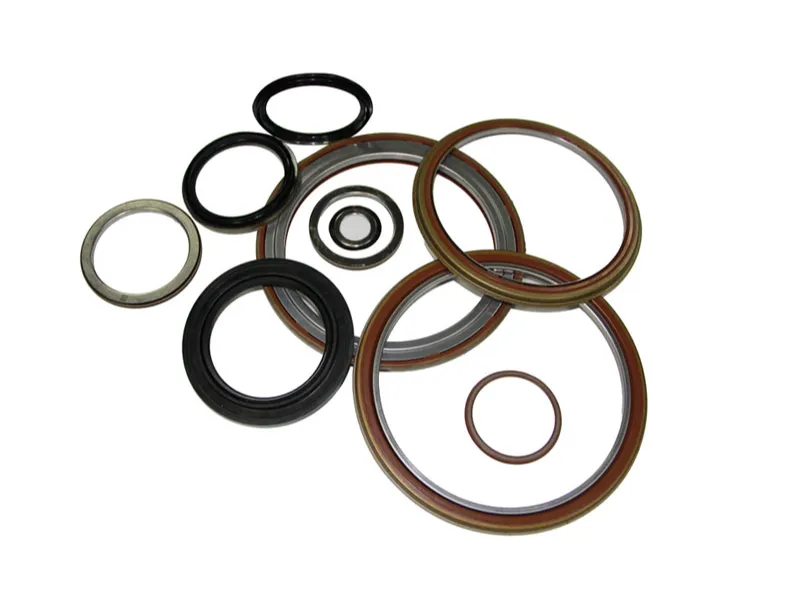
Section 5: Wear Ring Seal for Sale
When looking for wear ring seals, it’s essential to choose a reliable supplier who can provide high-quality products that meet your specific requirements. Welleshaft is a trusted global supplier and contract manufacturer specializing in wear ring seals and other sealing solutions.
Welleshaft: Your Trusted Supplier for Wear Ring Seals
Welleshaft offers a wide range of wear ring seals designed to enhance pump performance and durability. As a leading global supplier and contract manufacturer, Welleshaft provides:
- High-Quality Materials: Using premium materials such as polyurethane, carbon, and ceramic to ensure optimal performance.
- Custom Manufacturing: Tailoring wear ring seals to meet your specific application needs.
- Expert Support: Providing technical expertise and support to help you select the right seal for your application.
Conclusion
Wear ring seals are essential components for enhancing pump performance and durability. Understanding their materials, manufacturing processes, and applications can help you make informed decisions when selecting these components for your equipment. Welleshaft stands out as a trusted global supplier and contract manufacturer, offering high-quality wear ring seals and expert support to meet your needs. For reliable and durable wear ring seals, consider partnering with Welleshaft to ensure the optimal performance of your pumps and machinery.