High-Quality Upset Forging Services | Precision Forging Solutions for Durable Components
Upset forging is a critical manufacturing process that enhances the durability and strength of metal components used across various industries. Known for its ability to create high-precision parts, upset forging is a versatile and efficient method to produce components that meet stringent industry standards. In this article, we will explore the upset forging process, its applications, and how Welleshaft, a trusted global supplier and contract manufacturer, provides high-quality upset forging services tailored to your needs.
Section 1:Introduction of Upset Forging
1.1. What is Upset Forging?
Upset forging, also known as upsetting, is a forging process where a metal workpiece is compressed between two dies, increasing its cross-sectional area while reducing its length. This technique is widely used for creating stronger, more durable parts such as bolts, screws, fasteners, and other critical components.
The process typically involves heating the workpiece to a specific temperature before applying pressure. The heated metal becomes malleable, allowing the dies to shape it into the desired form. However, cold forging is also employed in some cases where precision and surface finish are more important than strength.
1.2. What is Upsetting or Upset Forging?
Upsetting refers to increasing the diameter of a portion of the metal workpiece by compressing its length. In upset forging, the process is repeated until the desired shape and size are achieved. Upsetting enhances the mechanical properties of the material, making it more resistant to stress and fatigue, which is crucial in industries such as automotive, aerospace, and construction.
1.3. Manufacturing by Upset Forging
Upset forging is primarily used in manufacturing processes where strength and durability are vital. Components produced through upset forging are often used in:
Automotive industry: crankshafts, axle shafts, and connecting rods.
Aerospace industry: landing gear components, engine parts, and structural supports.
Construction: fasteners, bolts, and other critical structural elements.
1.4. The Upset Forging Process
The upset forging process involves several key steps:
Heating the workpiece: The metal is heated to a temperature that allows for easy deformation while maintaining its integrity.
Positioning in the upset forging machine: The heated workpiece is placed between the upper and lower dies of the upset forging machine.
Applying pressure: The machine exerts force on the workpiece, compressing it and forming the required shape.
Final shaping: The process may involve multiple stages of pressing and shaping until the final product meets the desired specifications.
The process is highly efficient and repeatable, making it ideal for mass production of complex parts.
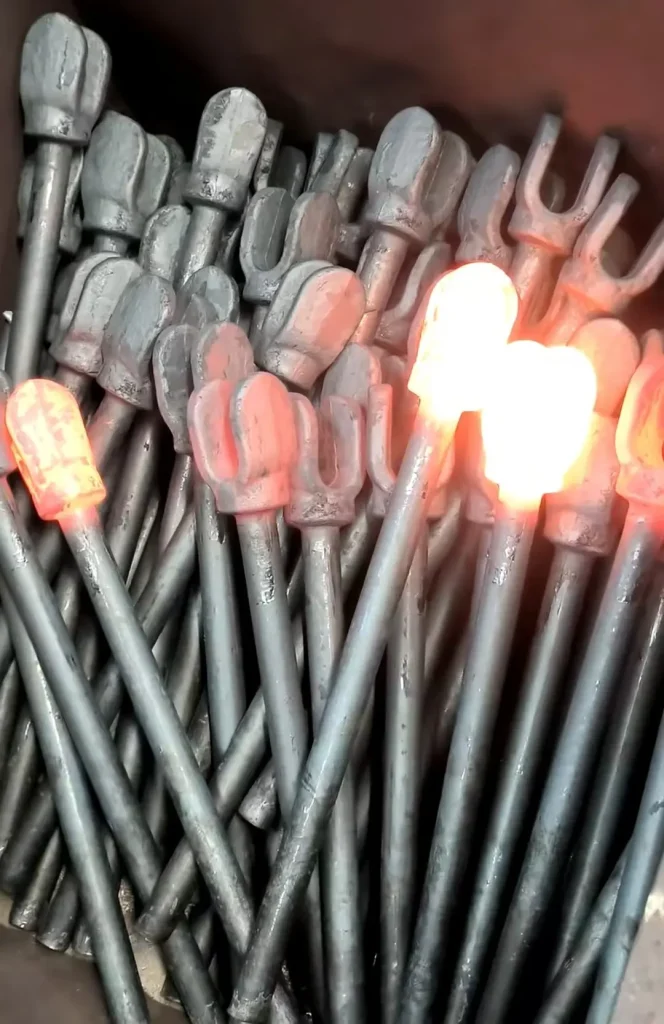
Section 2: What is Drop and Upset Forging?
Both drop forging and upset forging are widely used in metalworking, but they serve different purposes.
Drop forging: This involves dropping a hammer onto the metal workpiece, shaping it in the die. Drop forging is ideal for parts requiring high strength, such as wrenches and hammers.
Upset forging: Instead of striking the workpiece, pressure is applied to compress and shape it. Upset forging is better suited for components that require increased cross-sectional area, such as bolts and rivets.
Welleshaft offers both drop forging and upset forging, catering to a wide range of applications and industries.
2.1.What are the Different Types of Upset Forging?
There are two main types of upset forging:
Hot upset forging: The workpiece is heated before compression. This method is more common because it allows for better shaping of complex parts.
Cold upset forging: The process occurs at room temperature, providing better surface finishes and dimensional accuracy, but requiring higher forces due to the lack of material softening.
2.2. What are the Three Types of Forging?
Forging can be categorized into three types:
Open-die forging: Involves shaping the metal using flat dies, allowing for free deformation of the material. This method is suitable for large, simple parts.
Impression-die forging: The metal is shaped within a die cavity, allowing for more complex and accurate part production.
Upset forging: Focuses on increasing the cross-sectional area of the metal workpiece by compressing its length.
2.3. Upset Forging Companies and Industry Demand
Upset forging is a highly sought-after service in industries where the mechanical strength of parts is crucial. Companies that specialize in upset forging, such as Welleshaft, provide tailored solutions to meet the unique demands of their clients. Welleshaft’s state-of-the-art facilities and expertise make them a trusted global supplier for industries ranging from automotive to aerospace.
2.4. Upset Forging Machines
The upset forging process relies on specialized machines designed to apply precise pressure to the heated workpiece. These machines come in various sizes and configurations, depending on the size and complexity of the parts being manufactured. Welleshaft utilizes advanced upset forging machines that ensure consistent results and high-quality products.
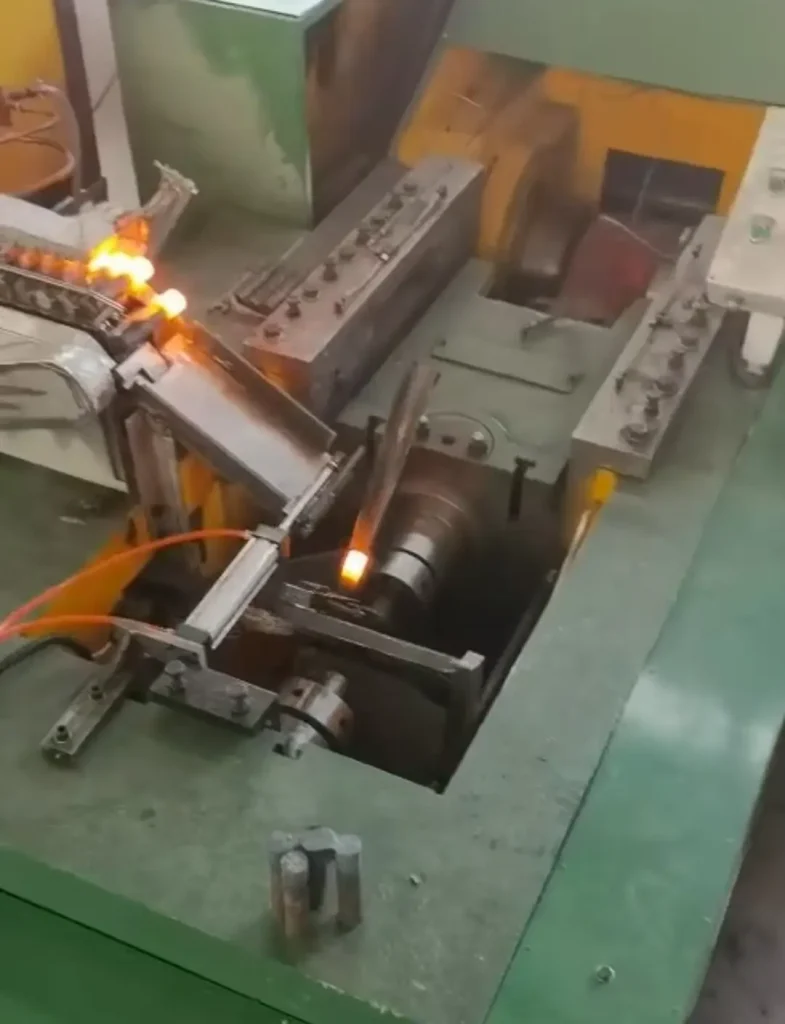
Section 3: Cold Forging vs. Upset Forging
Cold forging and upset forging are two distinct metal forming processes, each with unique characteristics, advantages, and applications. Here’s a comparison between the two:
3.1. Cold Forging
Cold forging refers to a forging process where metal is shaped at or near room temperature. Unlike hot forging, cold forging does not require the material to be heated, which makes it more energy-efficient and capable of producing components with superior surface finishes and tighter tolerances.
Process: In cold forging, the metal is deformed through compressive forces while it remains in a solid state, which increases its strength by enhancing the metal’s internal grain structure.
Advantages:
- Improved surface finish:Since there is no heat involved, cold forging produces components with smoother surfaces.
- Tighter tolerances: The process allows for greater dimensional accuracy.
- Increased strength:Cold forging strengthens the metal through work hardening, making it more durable.
- Cost-effective: The absence of heating reduces energy consumption and operational costs.
Disadvantages:
- High forces required:Forging metal at room temperature requires greater force, which can limit the process to softer metals like aluminum or mild steel.
- Limited complexity:Cold forging is not ideal for parts with highly complex geometries, as it’s more suited for simple shapes.
Applications of Cold Forging:
- Used for manufacturing bolts, screws, fasteners, and smaller components in industries like automotive, aerospace, and construction.
- Ideal for parts where surface quality and dimensional precision are critical.
3.2. Upset Forging
Upset forging, also known as upsetting, involves increasing the cross-sectional area of a portion of the workpiece by compressing its length. The process typically involves heating the metal before applying pressure, although it can also be performed cold in some cases.
Process: In upset forging, force is applied to a heated or cold metal workpiece between two dies, increasing its cross-sectional area in the desired region (e.g., the head of a bolt or the end of a rod).
Advantages:
- Strength and durability: Upset forging enhances the material’s strength by concentrating its grain structure, making it more resistant to stress and fatigue.
- Efficiency:The process is fast and well-suited for mass production.
- High volume capability:Ideal for producing large quantities of standardized parts like bolts, axles, and fasteners.
Disadvantages:
- Heat requirement:If done as hot forging, upset forging requires the workpiece to be heated, which adds energy costs and extra steps.
- Limited applications:Upset forging is generally used for parts where only a section of the workpiece needs to be modified.
Applications of Upset Forging:
- Commonly used in the production of bolts, nuts, rivets, and similar fasteners.
- Ideal for automotive parts like axles, shafts, and other components that require increased strength at specific points.
3.3. Key Differences
- Temperature:Cold forging is performed at room temperature, whereas upset forging is typically a hot process, though cold upset forging is possible.
- Material Behavior: In cold forging, the metal retains its original strength and hardness but becomes strain-hardened, whereas upset forging, especially when hot, makes the material more malleable, allowing for easier shaping.
- Precision: Cold forging offers superior dimensional accuracy and surface finish due to the lack of heat, whereas upset forging focuses on enlarging specific sections of the workpiece.
- Application: Cold forging is better for smaller, more intricate parts requiring precision, while upset forging is typically used for larger, high-strength components that need localized expansion.
Welleshaft offers both cold forging and upset forging services, allowing them to cater to a wide range of customer requirements.
3.4. Upset Forging Diagrams and Examples
The upset forging process can be better understood through diagrams that illustrate the movement of the metal and the forces applied during the compression stage. A typical upset forging diagram shows the workpiece being compressed between two dies, with the cross-sectional area increasing as the length decreases.
Some common examples of upset forging products include:
Bolts: The heads of bolts are typically made using upset forging, where the shank is compressed to form a larger diameter.
Axles: In automotive applications, axles are forged through upsetting to increase strength and durability.
Fasteners: High-strength fasteners used in construction and machinery are often produced through upset forging.
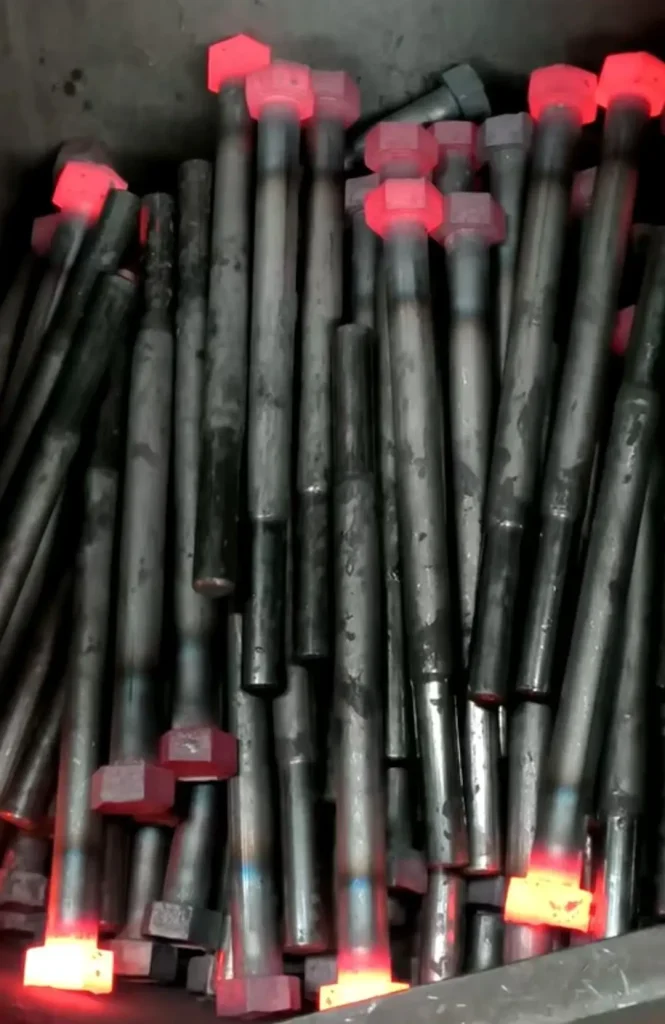
Section 4: Press Forging vs. Upset Forging
Press forging and upset forging are two different forging processes, each with its unique characteristics and applications. Understanding the distinctions between these methods is essential for choosing the right forging technique for a specific component.
4.1. Press Forging
Press forging involves applying continuous, controlled pressure to a heated metal workpiece using a forging press. This process gradually deforms the metal into the desired shape, providing a more precise and controlled operation compared to other forging techniques.
Force application: In press forging, the force is applied gradually and steadily, which allows for deeper penetration into the workpiece and improved material flow.
Precision: Press forging is ideal for producing complex, precision components, such as gears, crankshafts, and structural parts for aerospace or automotive applications.
Efficiency: While the process may take longer due to the slower application of force, it provides a higher degree of accuracy and consistency in the final product.
Material usage: Press forging reduces the need for excess material, leading to minimal waste and improved material efficiency.
Applications of Press Forging:
High-precision parts in aerospace, automotive, and heavy machinery industries.
Structural components that require consistent grain flow and superior mechanical properties.
4.2. Upset Forging
Upset forging focuses on increasing the cross-sectional area of the metal by compressing its length. It is commonly used for producing parts like bolts, screws, and fasteners where the head or other specific areas of the workpiece need to be enlarged.
Force application: Upset forging typically involves rapid, repeated application of force to specific sections of the workpiece, shaping the metal into a larger cross-section while maintaining its overall length.
Strength: The primary advantage of upset forging is the enhanced strength and durability of the final product, making it ideal for parts that undergo high levels of stress or strain.
Efficiency: The process is fast and highly repeatable, making it suitable for mass production of standardized components like fasteners, rivets, and axles.
Applications of Upset Forging:
Manufacturing bolts, nuts, and other fasteners with increased strength.
Producing axle shafts, engine components, and other parts for automotive and aerospace industries.
4.3. Key Differences
Force Application: In press forging, force is applied gradually and uniformly, while in upset forging, force is applied quickly and repetitively to specific areas.
Precision: Press forging is more precise and is suitable for intricate parts, whereas upset forging is typically used for simpler shapes with localized enlargement of specific areas.
Material Focus: Press forging allows for deeper shaping and more complex geometries, while upset forging focuses on enlarging the cross-sectional area of specific portions of the workpiece.
Production Speed: Upset forging is faster and more suited for mass production, while press forging is slower but offers higher accuracy and control.
Both press forging and upset forging are essential in manufacturing high-quality components, and the choice between the two depends on the specific requirements of the part being produced.
Why Choose Welleshaft for Your Upset Forging Needs?
Welleshaft stands out as a trusted global supplier and contract manufacturer for upset forging services. With a strong commitment to quality, Welleshaft offers:
Advanced technology: Welleshaft’s modern facilities are equipped with state-of-the-art upset forging machines, ensuring high precision and consistency in every batch.
Customized solutions: Welleshaft works closely with clients to provide tailored solutions that meet their specific requirements, from material selection to final product design.
Global presence: As a leading global supplier, Welleshaft serves customers across various industries, providing reliable upset forging services at competitive prices.
Quality assurance: Welleshaft follows strict quality control measures to ensure every product meets the highest standards, offering durable and reliable components for even the most demanding applications.
Conclusion
Upset forging is a critical process for producing durable and high-strength components across a wide range of industries. With expertise in both upset and drop forging, Welleshaft offers precision forging solutions that ensure the highest quality products. Whether you need custom bolts, fasteners, or other complex parts, Welleshaft is your trusted global supplier and contract manufacturer for upset forging services.
For more information or to request a quote, contact Welleshaft today!