Tubular Shafts for Drive Systems, Robotics & More
Tubular shafts, also known as hollow shafts or cannulated shafts, are a versatile and increasingly popular engineering component used in a wide range of applications. From high-performance drive systems and precision robotics to specialized machinery and innovative medical devices, the unique properties of tubular shafts offer significant advantages over their solid counterparts. This article explores the benefits of tubular shafts, their diverse applications, material considerations, and why they are becoming an essential element in modern engineering design.
What are Tubular Shafts?
In its simplest form, a tubular shaft is a cylindrical component with a hollow core. This fundamental design difference from a solid shaft translates into a suite of performance benefits. While seemingly basic, this simple modification provides engineers with powerful opportunities to optimize their designs, particularly regarding weight reduction, torsional stiffness, and the potential for integrated functionality. They are used in various industries and can be referred to by many names, including: Hollow Core Shaft, Cannulated Shaft, Empty Shaft, Bored Shaft, Through-Bore Shaft, Internal Bore Shaft, Passage Shaft, Hollow Drive Shaft, Hollow Transmission Shaft, Hollow Splined Shaft, Hollow Camshaft, Hollow Propeller Shaft, Tubular Rotating Shaft, Internally Bored Shaft, Passage Core Shaft, Through-Bore Torsion Shaft, Hollow Transmission Spindle, Open Core Shaft, and Ducted Shaft.
Key Advantages of Tubular Shafts
The adoption of tubular shafts is driven by their inherent advantages:
Weight Reduction: This is often the primary driver for using tubular shafts. By removing material from the core, the overall weight of the shaft is significantly reduced. This weight savings is particularly crucial in applications where minimizing inertia is paramount, such as robotics, aerospace, and high-speed machinery. A lighter shaft requires less energy to accelerate and decelerate, leading to improved efficiency and responsiveness.
Increased Torsional Stiffness-to-Weight Ratio: Surprisingly, a hollow shaft can offer higher torsional stiffness for the same weight compared to a solid shaft of the same outer diameter. The material is concentrated further away from the center axis, increasing the moment of inertia and therefore the resistance to twisting forces. This is vital for power transmission systems, where minimizing torsional deflection is essential for maintaining accurate motion and preventing premature failure.
Accommodating Internal Components: The hollow core provides a channel for routing other components, such as wires, cables, fluids, or even other shafts. This is especially beneficial in robotics, where wiring for end-effectors can be neatly contained within the shaft, preventing entanglement and damage. In medical devices, the hollow core can facilitate the passage of fluids or instruments.
Thermal Management: In some applications, the hollow core can be used for thermal management. For instance, circulating coolant through the shaft can help dissipate heat generated by friction or other processes, preventing overheating and maintaining optimal performance.
Cost Effectiveness: In some cases, tubular shafts can be cost-effective, especially if material costs are high. Removing material from the core can reduce the overall material usage without significantly compromising strength or performance.
Applications of Tubular Shafts
The benefits of tubular shafts translate into a wide range of applications across various industries:
Drive Systems (Automotive, Aerospace, Industrial): Propeller shafts, drive shafts, and transmission shafts in vehicles and machinery are often tubular to reduce weight and improve fuel efficiency or performance. The increased torsional stiffness helps transmit power efficiently and reliably.
Robotics: Tubular shafts are crucial in robotic arms and joints. They provide pathways for wiring, reduce inertia for faster and more precise movements, and can be used to transmit fluids or gases.
Machine Tools: Spindles in machine tools, such as lathes and milling machines, benefit from the increased stiffness and reduced weight of tubular shafts. This leads to improved accuracy, higher cutting speeds, and reduced vibration.
Medical Devices: Cannulated shafts are used in surgical instruments, endoscopes, and other medical devices. The hollow core allows for the passage of wires, fluids, or instruments to the target area.
Printing Industry: Rollers in printing presses use tubular shafts to reduce weight and improve dynamic performance at high speeds.
Packaging Machinery: Similar to printing presses, packaging machinery benefits from the reduced inertia of tubular shafts, allowing for faster and more precise operation.
Textile Machinery: Tubular shafts are used in various components of textile machinery to reduce weight and improve speed.
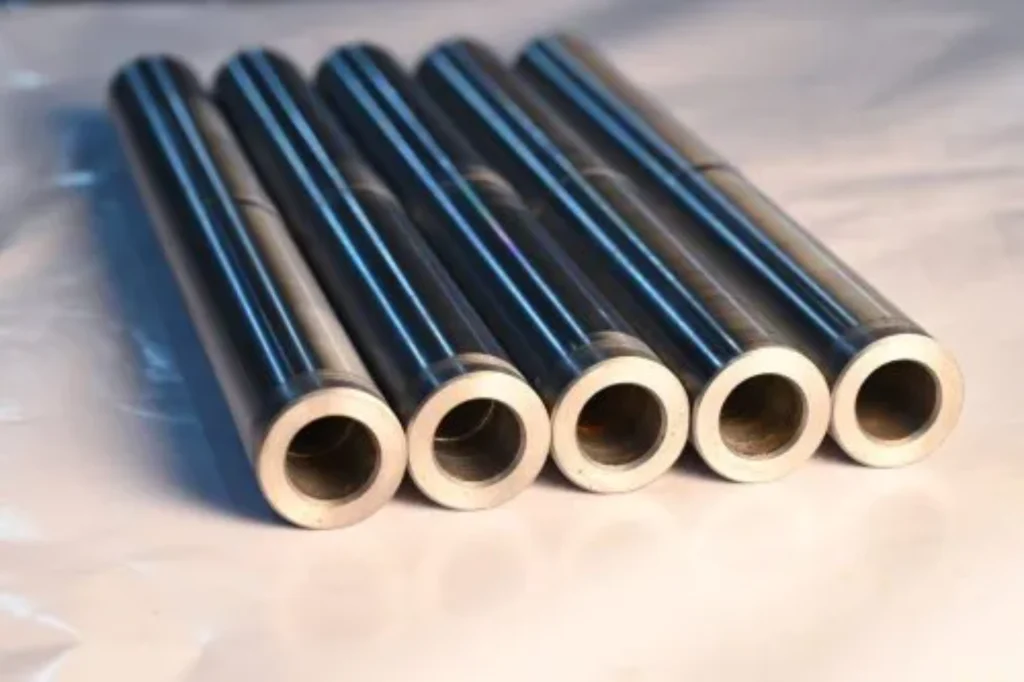
Material Considerations for Tubular Shafts
The choice of material for a tubular shaft depends on the specific application and performance requirements. Common materials include:
Steel: High-strength alloy steels are frequently used for demanding applications requiring high torsional strength and fatigue resistance. Examples include 4140, 4340, and various stainless steel grades.
Aluminum: Aluminum alloys offer excellent strength-to-weight ratios and are suitable for applications where weight reduction is a top priority.
Composites: Carbon fiber reinforced polymers (CFRP) and other composite materials provide exceptional stiffness-to-weight ratios and are increasingly used in high-performance applications, such as aerospace and racing.
Titanium: Titanium alloys offer a good balance of strength, weight, and corrosion resistance, making them suitable for demanding environments.
The selection process involves considering factors like:
Strength and Stiffness: The material must withstand the applied loads without excessive deformation or failure.
Weight: The material’s density impacts the overall weight of the shaft.
Corrosion Resistance: The material must be resistant to corrosion in the operating environment.
Machinability: The material must be machinable to the required tolerances and surface finish.
Cost: The material’s cost must be balanced against its performance benefits.
Related Information
Category |
Description |
Alternative Names |
Hollow Core Shaft, Cannulated Shaft, Bored Shaft, Through-Bore Shaft, Hollow Drive Shaft, etc. |
Key Benefits |
Weight Reduction, Torsional Stiffness, Internal Routing, Thermal Management |
Common Applications |
Drive Systems, Robotics, Machine Tools, Medical Devices |
Common Materials |
Steel, Aluminum, Composites, Titanium |
Important Properties |
Strength, Stiffness, Weight, Corrosion Resistance, Machinability |
Design Considerations
Designing with tubular shafts requires careful consideration of several factors:
Wall Thickness: The wall thickness must be sufficient to withstand the applied loads without buckling or yielding.
End Connections: The design of the end connections is crucial for transmitting torque and preventing stress concentrations. Common end connections include splines, keyways, and flanges.
Manufacturing Processes: The manufacturing process can impact the performance and cost of the tubular shaft. Common manufacturing processes include extrusion, drawing, and machining.
Critical Speed: The critical speed of the shaft must be considered to avoid resonance and vibration problems.
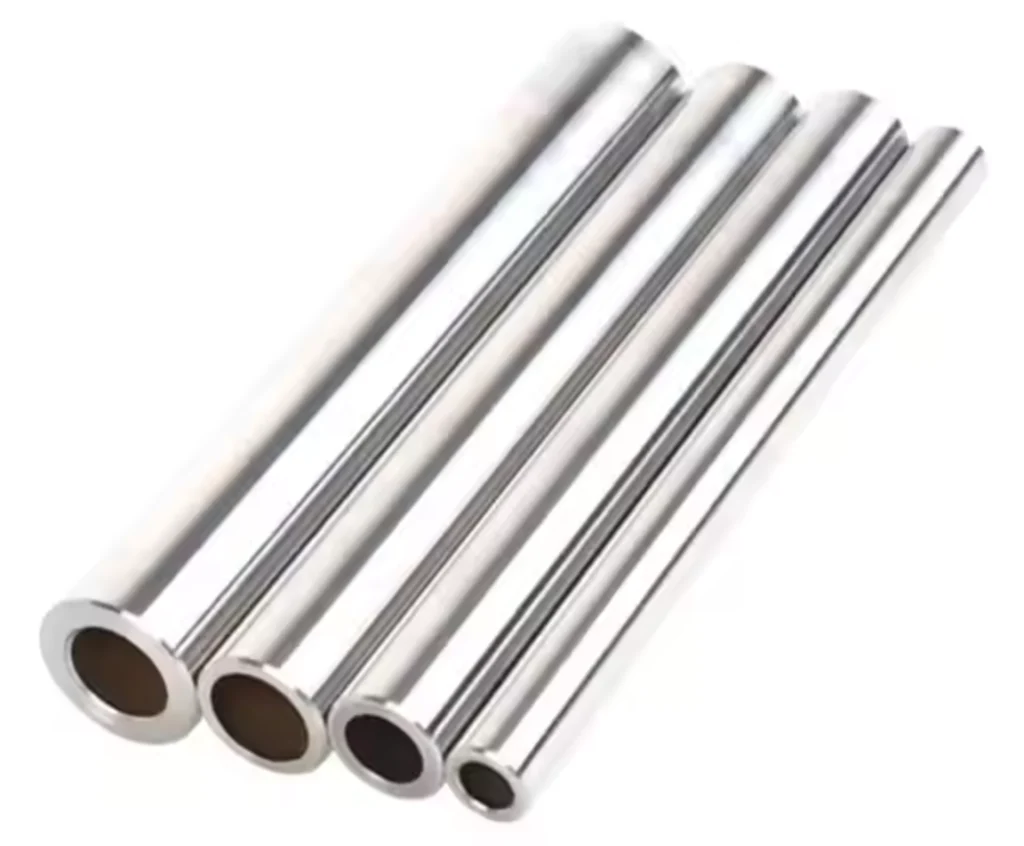
Choosing a Tubular Shaft Manufacturer
Selecting a reputable and experienced manufacturer is critical for ensuring the quality and reliability of tubular shafts. Look for manufacturers with:
Extensive experience in manufacturing tubular shafts for various applications.
Advanced manufacturing capabilities including precision machining, heat treating, and surface finishing.
Stringent quality control processes to ensure dimensional accuracy and material integrity.
Engineering support to assist with design and material selection.
A proven track record of delivering high-quality products on time and within budget.
The Future of Tubular Shafts
As engineering demands increase for lighter, more efficient, and more functional components, the use of tubular shafts is expected to continue to grow. Advancements in materials, manufacturing processes, and design techniques will further enhance the performance and versatility of tubular shafts, enabling their adoption in even more demanding applications.
Why You Should Consider Welleshaft
When it comes to sourcing high-quality and reliable tubular shafts, Welleshaft stands out as a trusted global supplier and contract manufacturer. With decades of experience in precision machining and manufacturing, Welleshaft has established itself as a leader in providing custom tubular shaft solutions for a diverse range of industries.
Here’s why Welleshaft should be your first choice:
Expertise and Experience: Welleshaft possesses a deep understanding of tubular shaft design, materials, and manufacturing processes. Their team of experienced engineers and technicians can provide valuable support throughout the entire process, from initial design to final production.
Comprehensive Manufacturing Capabilities: Welleshaft offers a wide range of manufacturing capabilities, including precision CNC machining, turning, milling, drilling, honing, grinding, and surface finishing. They can handle complex geometries and tight tolerances with ease.
Material Versatility: Welleshaft works with a wide variety of materials, including steel, aluminum, composites, titanium, and specialty alloys. This allows them to tailor the material selection to meet the specific performance requirements of each application.
Quality Assurance: Welleshaft is committed to providing the highest quality tubular shafts. They maintain stringent quality control processes throughout the entire manufacturing process, ensuring that every shaft meets or exceeds customer expectations.
Custom Solutions: Welleshaft specializes in providing custom tubular shaft solutions. They work closely with customers to understand their specific needs and develop tailored solutions that meet their exact requirements.
Global Reach: Welleshaft serves customers worldwide. Their global manufacturing and distribution network ensures timely delivery and responsive customer service.
Competitive Pricing: Welleshaft offers competitive pricing without compromising on quality or performance. They are committed to providing cost-effective solutions that meet their customers’ budgetary needs.
Contract Manufacturing Expertise: Welleshaft is a trusted contract manufacturer, capable of handling large-scale production runs while maintaining consistent quality and on-time delivery.
Whether you need tubular shafts for drive systems, robotics, medical devices, or any other application, Welleshaft has the expertise and capabilities to deliver the perfect solution.
Conclusion
Tubular shafts offer a compelling combination of weight reduction, torsional stiffness, and functional integration, making them an indispensable component in modern engineering design. By carefully considering material selection, design parameters, and manufacturing processes, engineers can leverage the benefits of tubular shafts to optimize performance, improve efficiency, and unlock new possibilities across a wide spectrum of applications. When sourcing your next tubular shaft project, be sure to consider Welleshaft for their expertise, quality, and commitment to customer satisfaction.