When it comes to drilling operations, selecting the right drill collar is crucial for the success and efficiency of your projects. Whether you’re working in the oil and gas industry, geothermal drilling, or any other field requiring precision drilling, understanding the specifications and types of drill collars is essential. This comprehensive guide covers various aspects of drill collars—including their types, weight, sizes, lengths, materials, and applications—along with insights into top-rated drill collar suppliers.
Section 1: What is a Drill Collar?
A drill collar is a heavyweight component in the drill string, primarily used to apply downward force on the drill bit, ensuring efficient drilling operations. They are essential for maintaining the stability and direction of the drilling process, especially in challenging environments.
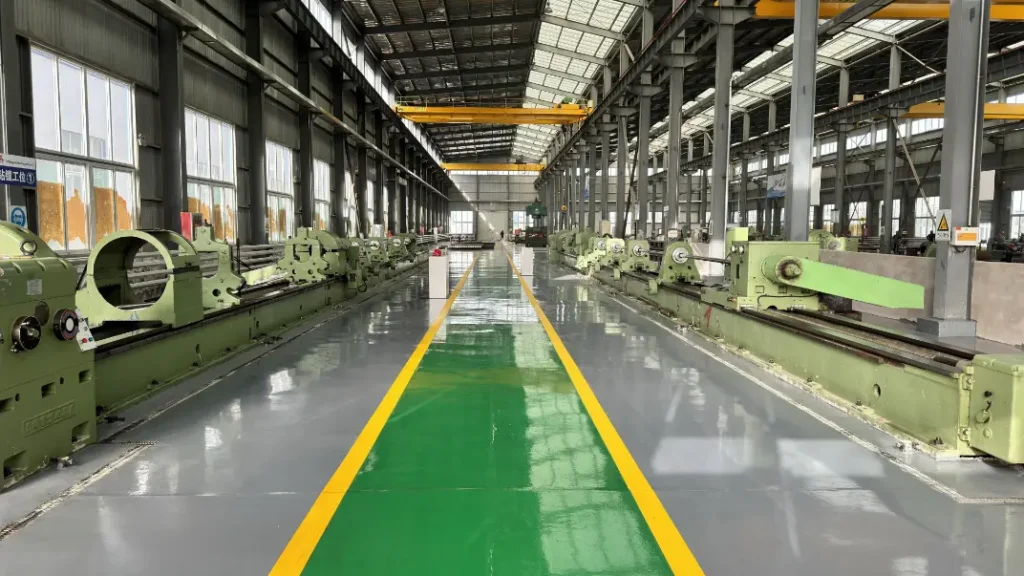
Section 2: Understanding Drill Collar Specifications
When selecting a drill collar, it’s essential to consider the specifications that match your drilling needs. These include size, weight, length, and material. Ensure that the drill collar meets industry standards and certifications for optimal performance.
Types of Drill Collars
Standard Drill Collar: These are the most common type, providing weight and stability to the drill bit.
Spiral Drill Collar: Designed to reduce the risk of differential sticking.
Non-Magnetic Drill Collar: Used in directional drilling to avoid interference with directional sensors.
Pony Drill Collar: Shorter in length, used for precise weight distribution.
Drill Collar Weight
The weight of a drill collar varies based on its size and length, typically ranging from 500 lbs to over 1500 lbs. The right weight ensures optimal pressure on the drill bit for efficient drilling.
- 500 lbs: Suitable for light drilling operations.
- 1000 lbs: Commonly used in standard drilling operations.
- 1500 lbs: Preferred for heavy-duty drilling tasks.
Drill Collar Sizes
Drill collars come in various sizes, typically measured by their outer diameter. Common sizes include:
- 4 3/4 inch(120.65 mm): Suitable for smaller boreholes.
- 6 1/2 inch(165.1 mm): Standard size for most drilling operations.
- 8 inch(203.2 mm): Used for larger boreholes.
Drill Collar Length
Standard lengths for drill collars range from 31 feet to 40 feet, providing flexibility for various drilling depths and applications.
- 31 feet: Standard length for general drilling operations.
- 34 feet: Offers additional weight and stability.
- 40 feet: Used in deeper drilling operations.
Materials Used in Drill Collars
Drill collars are made from high-strength materials to withstand the harsh conditions of drilling. Common materials include:
- AISI 4145H Modified Steel: Known for its strength and durability.
- Non-Magnetic Alloys:Prevents interference with directional drilling tools.
Connection Types
Available with different connection types like API Regular, API IF (Internal Flush), and API FH (Full Hole) to match various drilling needs.
Hardbanding
Options for hardbanding include Arnco 100XT and Duraband NC, providing enhanced wear resistance.
Certification
Drill collars typically come with API Spec 7-1 and NS-1 certifications, ensuring compliance with industry standards.
Applications of Drill Collars
Drill collars are used in various drilling applications, including:
Oil and Gas Drilling: Essential for providing weight and stability.
Geothermal Drilling: Suitable for high-temperature environments.
Directional Drilling: Non-magnetic drill collars prevent interference with sensors.
Drill Collar Accessories
Drill collar slips are used to securely grip the drill collar during drilling operations, ensuring stability and safety. The drill collar lifting sub assists in lifting and handling the heavy drill collars efficiently. When needed, the drill collar severing tool allows operators to cut through the drill collar safely and precisely. Together, these tools play essential roles in managing and maintaining drill collars throughout the drilling process.
Key Keywords: drill collar slips, drill collar lifting sub, drill collar severing tool
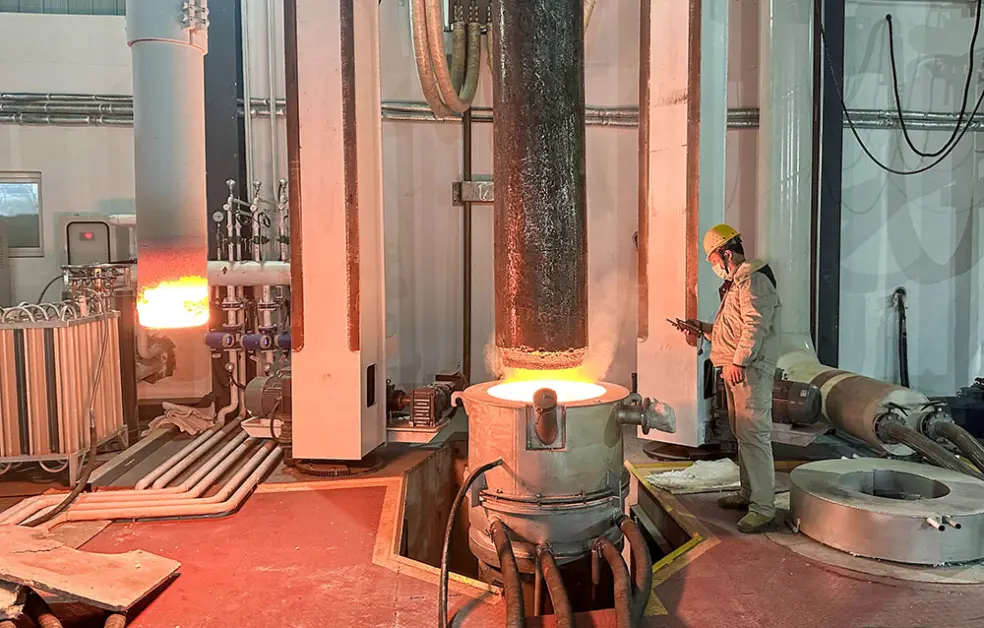
Section 3:Drill Collar vs Drill Pipe
In the world of drilling, particularly in oil and gas exploration, understanding the components of a drill string is crucial for efficient and successful operations. Two essential components of the drill string are the drill collar and the drill pipe. While they are both integral to the drilling process, they serve different purposes and have distinct characteristics.
1. What is a Drill Collar?
A drill collar is a heavyweight, thick-walled tube typically made of steel, used to add weight to the drill bit, enabling it to break and cut through rock formations. The primary functions of a drill collar are:
Providing Weight on Bit (WOB): The drill collar adds the necessary weight to the drill bit to enable it to cut through rock efficiently.
Maintaining Directional Control: Due to their rigidity, drill collars help maintain the direction of the drilling process, especially in deviated or directional wells.
Minimizing Drill String Flexure: The heavy and stiff nature of drill collars minimizes the bending of the drill string, enhancing the precision of the drilling process.
2. What is a Drill Pipe?
A drill pipe is a hollow, thin-walled tube used to transmit drilling fluid (mud) to the drill bit and to rotate the bit. Drill pipes are the primary conduit for delivering the mechanical energy needed for drilling and the hydraulic energy for removing cuttings from the borehole. The primary functions of a drill pipe are:
Transmitting Drilling Fluid: Drill pipes transport drilling fluid to the drill bit to cool and lubricate it, as well as to carry rock cuttings back to the surface.
Rotating the Drill Bit: Drill pipes are connected to the drill bit and the rotary table, enabling the bit to rotate and drill into the rock.
Connecting the Surface to the Bottomhole Assembly (BHA): Drill pipes connect the drilling rig at the surface to the BHA, which includes the drill bit and drill collars.
3. Key Differences Between Drill Collars and Drill Pipes
Function:
Drill Collar: Provides weight on bit (WOB) and maintains directional control.
Drill Pipe: Transmits drilling fluid and rotates the drill bit.
Construction:
Drill Collar: Heavyweight, thick-walled, and typically solid or with a small bore.
Drill Pipe: Lightweight, thin-walled, and hollow.
Material:
Drill Collar: Made of high-strength steel or non-magnetic alloys.
Drill Pipe: Made of high-strength steel with a protective coating.
Position in Drill String:
Drill Collar: Positioned near the drill bit in the Bottomhole Assembly (BHA).
Drill Pipe: Runs from the surface to the BHA, making up the majority of the drill string length.
Role in Drilling Process:
Drill Collar: Adds weight and stability to the drill bit.
Drill Pipe: Delivers mechanical and hydraulic energy to the drill bit.
4.Applications of Drill Collars and Drill Pipes
Oil and Gas Drilling: Both drill collars and drill pipes are used extensively in oil and gas drilling to reach hydrocarbon reservoirs.
Geothermal Drilling: Suitable for high-temperature drilling operations.
Directional Drilling: Non-magnetic drill collars are essential for avoiding interference with directional drilling tools.
Deepwater Drilling: High-strength drill pipes are necessary for the extreme conditions of deepwater drilling.
Section 4: Commonly Used Drill Collar HS Codes
HS codes are crucial for international shipping and classification of drill collars. Common HS codes for drill collars include:
HS Code 7304.29: Tubes, pipes, and hollow profiles of iron or steel.
HS Code 8431.43: Parts suitable for use solely or principally with the machinery of headings 8425 to 8430.
Section 5: Top-Rated Drill Collar Suppliers
Welleshaft: Specializes in high-quality drill collars and other drilling tools.
National Oilwell Varco: Renowned for their wide range of drilling equipment.
Schlumberger: Offers advanced drilling solutions and tools.
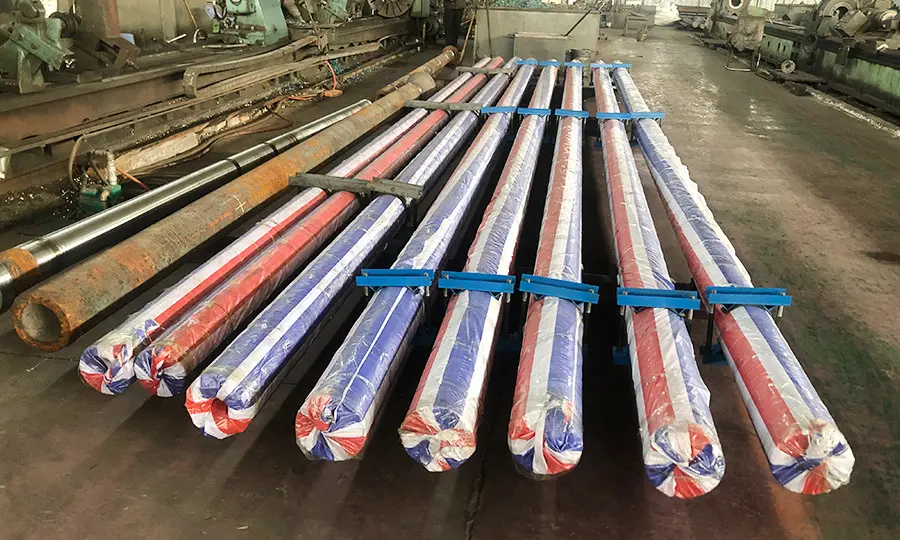
Conclusion
Selecting the right drill collar is vital for the success of any drilling operation. By understanding the various types, sizes, weights, and materials, and choosing from top-rated suppliers, you can ensure efficient and effective drilling performance. Keep in mind the specifications and applications to match your specific needs, and always opt for certified products to guarantee quality and reliability.
For more information or inquiries about high-quality drill collars, please contact us.
Email: [email protected]
Phone: +86-156-5017-9596 (whatsapp)
Address: No. 123, Industrial Zone, Jinan, Shandong, China
Welleshaft specializes in customized drilling tools and solutions, ensuring top-notch quality and performance for your drilling projects.
FAQs
What is the collar of a drill?
The collar of a drill refers to the heavy component used to apply weight on the drill bit, aiding in the drilling process.
What is the difference between a drill pipe and a drill collar?
Drill pipes are lighter and used for connecting the drill bit to surface equipment, whereas drill collars are heavier and provide the necessary weight for drilling.
What does it mean to collar a drill hole?
To collar a drill hole means to start the drilling process by positioning the drill bit at the desired location.
What is the difference between drill collar and HWDP?
HWDP (Heavy Weight Drill Pipe) is a type of drill pipe that is heavier than standard drill pipe but lighter than a drill collar, providing a transition between the two.