Top-Quality Hydraulic Wear Rings for Reliable Sealing Solutions
Hydraulic systems rely on various components to ensure efficient and reliable operation. Among these components, hydraulic wear rings play a critical role in maintaining performance and longevity. This article delves into the significance of hydraulic wear rings, their types, materials, and applications, and highlights why Welleshaft is your trusted global supplier and contract manufacturer for top-quality hydraulic wear rings.
Section 1: Introduction
1. What Are Hydraulic Wear Rings?
Hydraulic wear rings are crucial components in hydraulic cylinders and other hydraulic systems. They are designed to reduce friction between the moving parts of the hydraulic cylinder, minimize wear, and ensure smooth operation. Wear rings help maintain the integrity of the hydraulic system by preventing metal-to-metal contact and protecting the cylinder from abrasive particles.
2. Function of Wear Rings in Hydraulic Cylinders
The primary function of wear rings in hydraulic cylinders is to support and guide the piston or rod while reducing friction and wear. They:
- Reduce Friction: Wear rings provide a low-friction surface, reducing the wear and tear on hydraulic cylinders and extending their lifespan.
- Guide Movement: They help in maintaining alignment and guiding the piston or rod, ensuring smooth and accurate movement within the cylinder.
- Prevent Metal-to-Metal Contact: By providing a cushioning layer, wear rings prevent direct metal contact between the piston and cylinder, reducing the risk of damage.
3. Hydraulic Cylinder Wear Ring Materials
The choice of material for hydraulic cylinder wear rings significantly affects their performance and durability. Common materials include:
- Nylon: Known for its excellent wear resistance and low friction, making it suitable for high-speed applications.
- PTFE (Polytetrafluoroethylene): Offers superior chemical resistance and low friction, ideal for harsh operating conditions.
- UHMWPE (Ultra-High Molecular Weight Polyethylene): Provides high wear resistance and impact strength, often used in heavy-duty applications.
- Bronze: Used in high-pressure environments due to its durability and strength.
For more information on high-quality hydraulic cylinder wear rings and to find the perfect solution for your application, please contact us.
Jinan Welle Metal Products Co., Ltd (Welleshaft)
Website: www.welleshaft.com
Email: [email protected]
Phone: +86-156-5017-9596
Explore our range of durable and reliable hydraulic cylinder wear rings today!
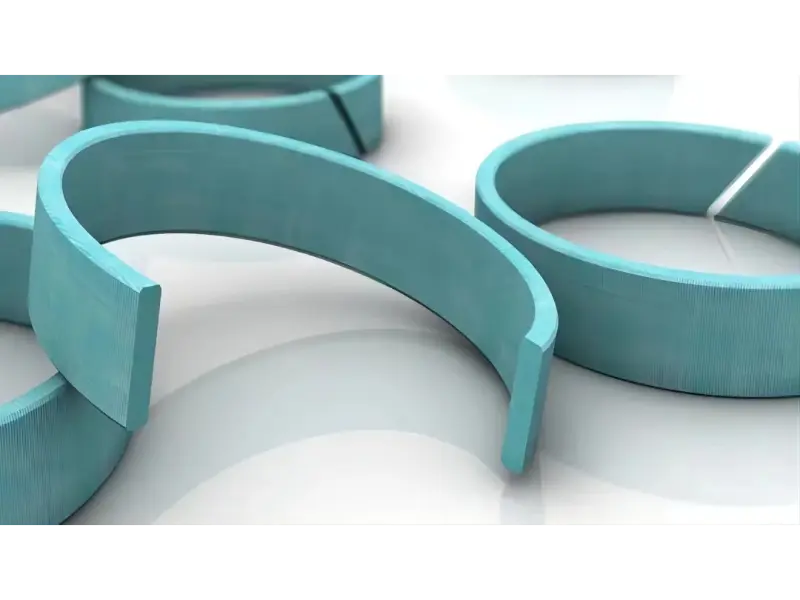
Section 2: Types of Hydraulic Wear Rings
Hydraulic wear rings come in various types, each designed for specific applications and performance requirements. Some common types include:
1. Solid Wear Rings
Description:
Solid wear rings are made from a single, continuous piece of material. They are often used for their simplicity and durability.
Materials:
- Nylon: Provides good wear resistance and is suitable for moderate pressures and temperatures.
- PTFE (Polytetrafluoroethylene): Known for its low friction and high chemical resistance.
- UHMWPE (Ultra-High Molecular Weight Polyethylene): Offers high impact strength and wear resistance.
Applications:
Hydraulic cylinders
Pumps
General industrial machinery
Advantages:
Durable and long-lasting
Simple design with fewer parts
2. Segmented Wear Rings
Description:
Segmented wear rings are composed of multiple segments or pieces that fit together to form the complete ring. These segments can often be replaced individually.
Materials:
- Composite materials: Combining various polymers or metals for enhanced properties.
- Bronze: Used for high-pressure applications.
Applications:
Large hydraulic cylinders
Equipment with frequent maintenance needs
Advantages:
Easier to replace individual segments
Flexible design for different applications
3. Composite Wear Rings
Description:
Composite wear rings are engineered from a blend of materials to achieve specific performance characteristics. These materials are often chosen to provide a balance of wear resistance, flexibility, and chemical resistance.
Materials:
- Composite polymers: Such as reinforced plastics or blends of various resins.
- Hybrid materials: Combining polymers with metal or ceramic components.
Applications:
High-pressure hydraulic systems
Environments with abrasive fluids
Advantages:
Customized properties for specific applications
Enhanced performance in demanding conditions
4. Metallic Wear Rings
Description:
Metallic wear rings are made from various metals or alloys designed to withstand extreme conditions, including high pressures and temperatures.
Materials:
- Stainless Steel: Offers corrosion resistance and high strength.
- Bronze: Known for its wear resistance and durability.
Applications:
Heavy-duty hydraulic machinery
High-temperature or high-pressure applications
Advantages:
Exceptional strength and durability
Suitable for extreme conditions
5. High-Speed Wear Rings
Description:
High-speed wear rings are specifically designed to handle the challenges associated with high-speed hydraulic systems. They are made from materials that can endure increased friction and wear.
Materials:
- Specialized polymers: Engineered to withstand high speeds.
- Advanced composites: Providing low friction and high wear resistance.
Applications:
High-speed hydraulic cylinders
High-performance industrial equipment
Advantages:
Enhanced performance in high-speed operations
Reduced friction and wear
6. Guide Rings
Description:
Guide rings, often used in conjunction with wear rings, help maintain the alignment and guidance of pistons or rods within hydraulic cylinders. They provide additional support and ensure smooth movement.
Materials:
Nylon
PTFE
UHMWPE
Applications:
Hydraulic cylinders
Pneumatic actuators
Advantages:
Improved alignment and guidance
Enhanced stability in dynamic systems
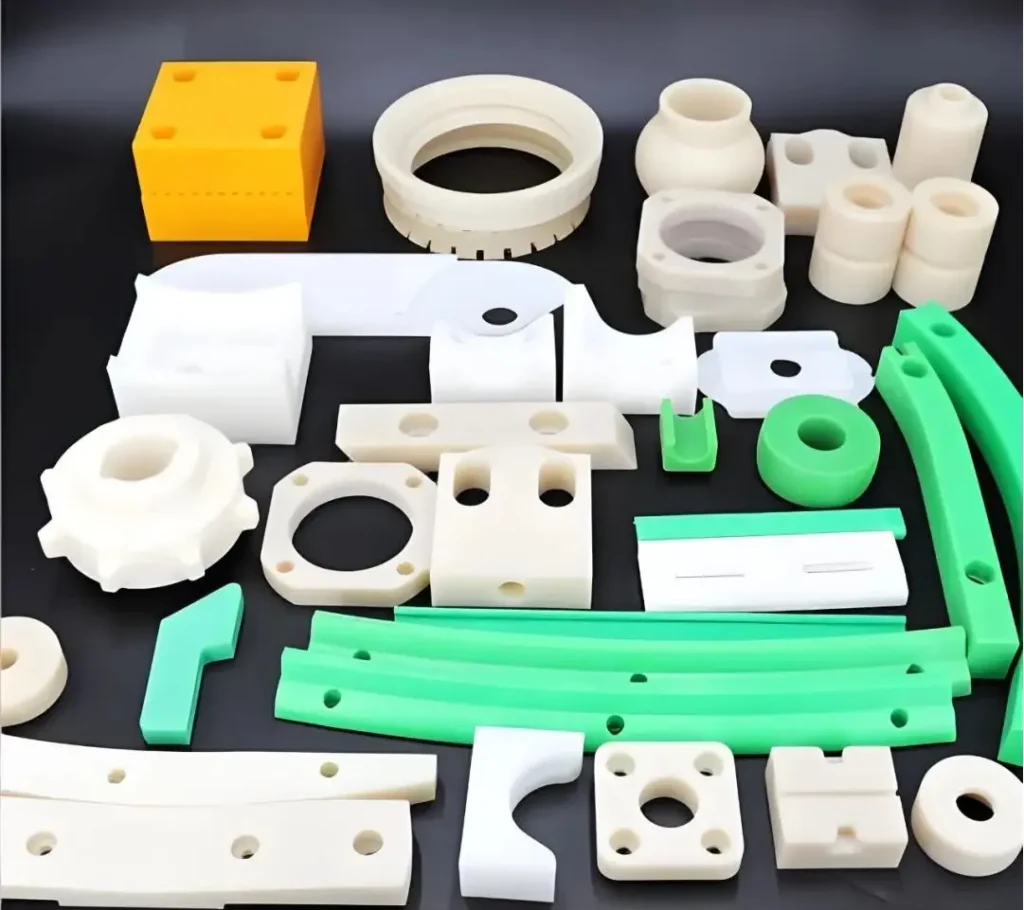
Section 3: Hydraulic Wear Rings in Various Applications
Hydraulic wear rings are used in a wide range of applications beyond hydraulic cylinders. Some notable uses include:
- Wear Ring Seal in Centrifugal Pumps: Wear rings in centrifugal pumps protect the pump casing and impeller from wear caused by abrasive particles in the pumped fluid. They help maintain the efficiency and longevity of the pump.
- Hydraulic Piston Rings: Used in hydraulic cylinders to maintain a tight seal between the piston and cylinder wall, hydraulic piston rings prevent leakage and ensure efficient operation.
Section 4: Choosing the Best Hydraulic Wear Rings
When selecting hydraulic wear rings, consider the following factors to ensure you choose the best option for your application:
- Material Compatibility: Choose wear rings made from materials that are compatible with the fluids and conditions in your hydraulic system.
- Size and Fit: Ensure that the wear rings are the correct size and fit for your hydraulic cylinder or application.
- Performance Requirements: Consider the operating conditions, such as temperature, pressure, and speed, to select wear rings that can handle these conditions effectively.
Section 5: Special O-Rings for Hydraulics
Yes, there are special O-rings designed specifically for hydraulic applications. These O-rings are made from materials that can withstand the pressures, temperatures, and chemical exposures typical in hydraulic systems. Common materials for hydraulic O-rings include:
- Nitrile Rubber (NBR): Offers good resistance to hydraulic fluids and high pressure.
- Viton (Fluorocarbon): Provides excellent resistance to high temperatures and chemicals, making it suitable for demanding hydraulic applications.
Section 6: Common Questions About O-rings for Hydraulics
1.Are Viton O-Rings Good for Hydraulics?
Yes, Viton O-rings are highly suitable for hydraulic applications. They offer superior resistance to high temperatures, chemicals, and oils, making them an excellent choice for demanding hydraulic systems.
2.What Is the O-Ring for Hydraulic Systems?
The O-ring used in hydraulic systems is a sealing component designed to prevent leakage of hydraulic fluids. It is made from materials such as nitrile rubber or Viton, depending on the specific requirements of the hydraulic system.
Section 7: Why Choose Welleshaft for Hydraulic Wear Rings?
Welleshaft is a leading global supplier and contract manufacturer of hydraulic wear rings, offering top-quality solutions for various applications. Here’s why Welleshaft stands out:
- Expertise and Precision: With extensive experience in manufacturing hydraulic wear rings, Welleshaft provides precision-engineered components that meet the highest standards.
- Quality Materials: Welleshaft uses only the best materials, ensuring durability and performance in every wear ring produced.
- Custom Solutions: Welleshaft offers custom manufacturing services to meet specific requirements and applications, providing tailored solutions for your needs.
- Global Reach: As a trusted global supplier, Welleshaft delivers high-quality wear rings to customers worldwide, ensuring reliable and timely service.
Conclusion
Hydraulic wear rings are essential components that contribute to the efficiency, performance, and longevity of hydraulic systems. Understanding their materials, types, and applications helps in selecting the best wear rings for your needs. Welleshaft, with its expertise and high-quality products, is your trusted partner for reliable hydraulic wear rings and sealing solutions. For top-quality hydraulic wear rings and expert support, consider Welleshaft as your go-to global supplier and contract manufacturer.