Top-Quality Forged Flanges | Durable Solutions for Industrial Applications
Forged flanges play an essential role in connecting pipes, valves, pumps, and other components to form complete piping systems. Their durability, strength, and ability to withstand high pressures make them indispensable in industries such as oil & gas, petrochemicals, power generation, and more. In this article, we will explore the various aspects of forged flanges, including their types, specifications, and manufacturing process. We will also highlight Welleshaft as a trusted global supplier of forged flanges and related components.
Section 1: Forged Steel Flange Types and Specifications
Flanges come in various types, each designed for specific applications and operating conditions. The most common types of forged steel flanges include:
Weld Neck Flange: Ideal for high-pressure applications, weld neck flanges feature a long, tapered hub that is butt-welded to the pipe. This ensures a smooth flow of fluids and enhances mechanical strength.
Slip-On Flange: Easy to install, slip-on flanges slide over the pipe and are welded both inside and outside to increase strength. They are suitable for lower-pressure applications.
Blind Flange: Used to close the ends of piping systems, blind flanges do not have a bore. These are ideal for maintenance and inspection purposes, offering flexibility in system design.
Socket Weld Flange: Designed for small-diameter, high-pressure pipes, socket weld flanges have a socket where the pipe is inserted and then welded. This type is common in chemical and power industries.
Lap Joint Flange: Used in conjunction with a stub end, lap joint flanges are typically applied where frequent disassembly is required. These flanges are not welded but are held in place by bolts.
Threaded Flange: Common in low-pressure, non-critical applications, threaded flanges are screwed onto the pipe. No welding is required, making them suitable for hazardous areas where welding poses a risk.
Each type of forged flange must adhere to specific ASME B16.5 standards, which dictate dimensions, pressure ratings, and materials for flanges used in piping systems. Forged flanges are available in various materials, including carbon steel, stainless steel, and alloy steel.
Section 2: The Purpose of Forged Flanges
Forged flanges serve several essential purposes in industrial piping systems:
- Connection: They connect pipes, valves, pumps, and other equipment, enabling easy disassembly for maintenance or inspection.
- Strength: Forging improves the mechanical properties of flanges, making them stronger and more resistant to fatigue, impact, and high-pressure conditions.
- Sealing: Forged flanges provide a tight seal, preventing leaks in high-pressure environments.
- Corrosion Resistance: Stainless steel and alloy flanges offer resistance to corrosion, making them suitable for harsh environments such as offshore platforms and chemical plants.
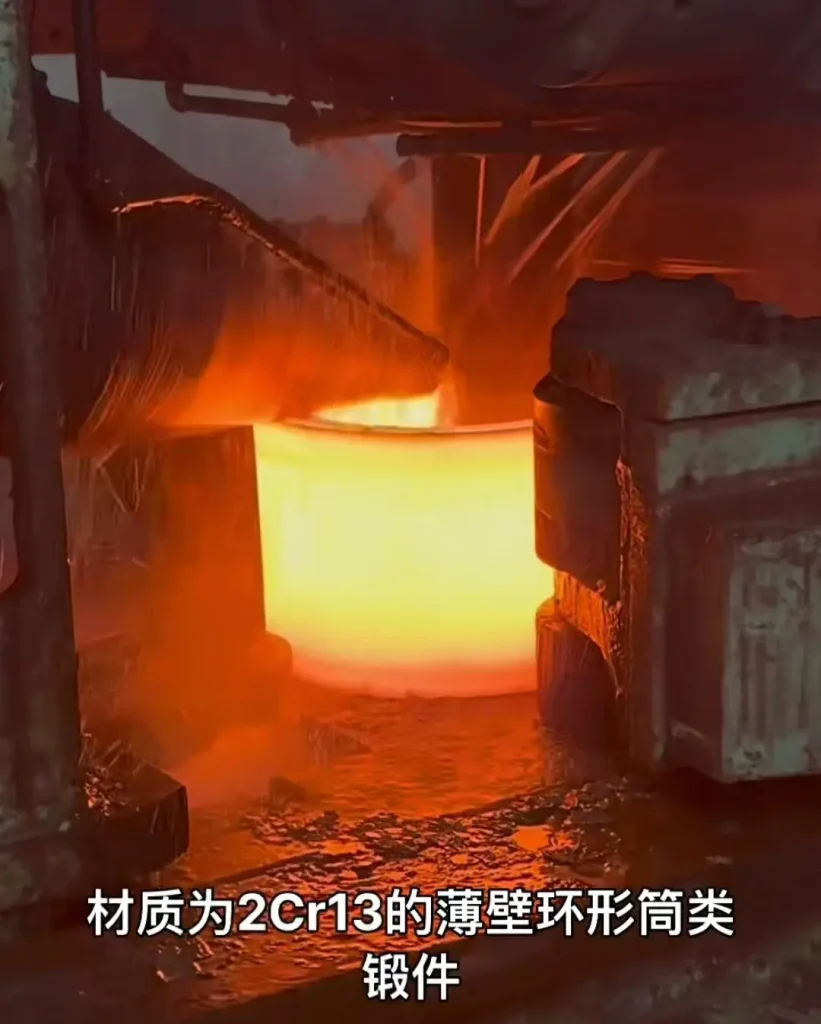
Section 3: Leaders in Forged Flanges for Piping Systems
As a leading manufacturer of forged flanges, Welleshaft provides durable and high-quality solutions for various industrial applications. Our forged flanges are designed to meet international standards such as ASME B16.5, ensuring compatibility and safety in critical operations.
Welleshaft’s expertise lies in producing:
- Stainless Steel Flanges: Offering excellent corrosion resistance, ideal for offshore, marine, and chemical industries.
- Carbon Steel Flanges: Known for their strength and durability, carbon steel flanges are widely used in oil & gas and power generation.
- Alloy Steel Flanges: These flanges provide additional mechanical strength and heat resistance, suitable for high-temperature applications.
- Nickel Alloys:Used in specialized environments where high corrosion resistance is required.
Welleshaft stands out as a reliable partner for companies around the globe, particularly in China, India, and other key industrial regions. Whether you need standard flanges or custom solutions, we have the manufacturing capabilities to meet your needs.
Section 4: ASME B16.5 Forged Flanges: Stainless and Carbon Steel
ASME B16.5 is the standard that governs pipe flanges and fittings in the sizes ranging from NPS 1/2 through NPS 24. It covers pressure-temperature ratings, materials, dimensions, tolerances, and marking.
Stainless steel forged flanges are widely used in industries where corrosion resistance is crucial, while carbon steel flanges are chosen for their strength and cost-effectiveness. Welleshaft manufactures both types, adhering to ASME B16.5 standards, ensuring they meet all industry regulations.
4.1. Forged Flanges vs Plate Flanges
One common question is: What is the difference between forged flanges and plate flanges?
Forged Flanges: These are made by forging steel, which involves heating and shaping the metal to improve its grain structure, resulting in enhanced strength, toughness, and durability.
Plate Flanges: These are cut from a steel plate and do not undergo the forging process. As a result, they are less robust and have lower mechanical properties compared to forged flanges. Plate flanges are generally used in lower-pressure applications.
4.2. The Forged Flanges Manufacturing Process
Forging is a process that improves the mechanical properties of metal by compressing it under high pressure. The process for manufacturing forged flanges includes several key steps:
- Heating the Metal: The metal is heated to a specific temperature, depending on the material, to make it malleable.
- Forging: The heated metal is placed between dies and compressed to form the shape of the flange.
- Trimming: Excess material is trimmed off to achieve the correct dimensions.
- Heat Treatment: The forged flange undergoes heat treatment to enhance its mechanical properties, such as strength and toughness.
- Machining: Finally, the flange is machined to precise tolerances to meet industry standards.
4.3. Slip-On Flange vs Weld Neck Flange
Slip-on flanges are easier to install and more cost-effective, making them a popular choice for low-pressure applications. However, weld neck flanges are preferred for high-pressure systems due to their strong, welded connection to the pipe, providing greater structural integrity.
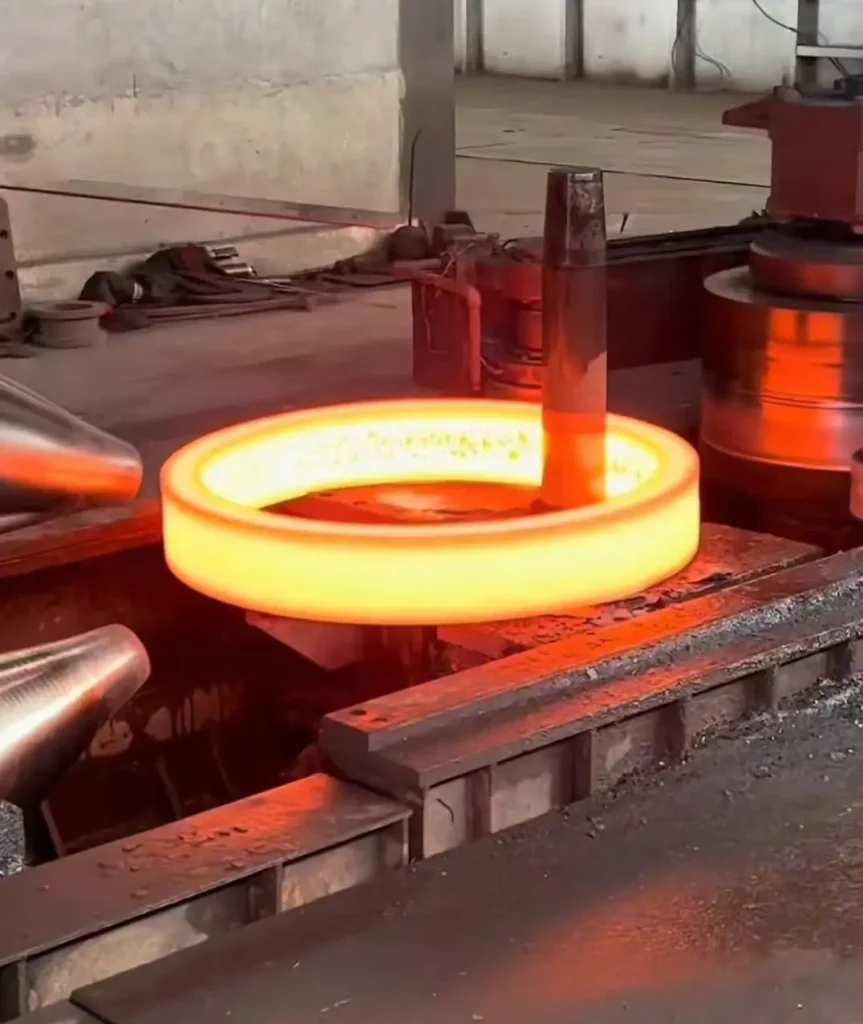
Section 5: Stainless Steel Flange Supplier in China
Welleshaft is a leading stainless steel flange supplier in China, offering a range of products for both domestic and international markets. We are recognized for our high-quality materials, precision manufacturing, and adherence to global standards such as ASME B16.5.
Section 6: Forged Flanges Price and Weight Chart
When selecting forged flanges for industrial applications, it’s essential to consider both their weight and price, as these factors vary based on the flange type, size, material, and pressure class. The cost of a forged flange depends largely on the manufacturing process, material composition (such as stainless steel or carbon steel), and the specific standards they meet, like ASME B16.5.
6.1.Price Factors of Forged Flanges:
- Material: Stainless steel flanges tend to be more expensive due to their corrosion resistance and longer lifespan compared to carbon steel flanges.
- Size: Larger flanges require more material and involve more intricate manufacturing processes, making them more expensive.
- Pressure Class: Flanges with higher pressure ratings (such as Class 150, Class 300, or higher) are built to withstand more demanding environments, which increases their cost.
- Quantity: Bulk orders typically reduce the price per unit, making large-scale projects more cost-efficient.
- Customization: Custom-designed flanges or those requiring specific machining features can have a higher price due to additional labor and tooling needs.
6.2.Weight Chart for Common Forged Flange Types:
The weight of a forged flange is an important consideration, as it impacts shipping, handling, and installation logistics. Below is a general weight chart for common flange types based on a selection of sizes.
Flange Type | Nominal Size (inches) | Pressure Class | Weight (kg) |
Weld Neck Flange | 2 | Class 150 | 5.5 |
Slip-On Flange | 4 | Class 300 | 12.7 |
Blind Flange | 6 | Class 150 | 15.3 |
Socket Weld Flange | 8 | Class 600 | 25.4 |
Lap Joint Flange | 10 | Class 300 | 30.7 |
Threaded Flange | 12 | Class 150 | 45.8 |
Note: This is a simplified weight chart for reference. Actual weights may vary based on the manufacturer, specific standards, and custom modifications.
6.3.Typical Price Ranges:
- Carbon Steel Flanges: $5 – $500 depending on size and class.
- Stainless Steel Flanges: $10 – $800 for higher corrosion resistance.
- Alloy Steel Flanges: $20 – $1000 for high-strength, heat-resistant applications.
To get an accurate price quote for your specific needs, it’s recommended to consult directly with suppliers like Welleshaft, who can offer competitive pricing based on your project’s requirements.
Welleshaft provides a comprehensive weight chart and pricing details for forged flanges, ensuring that clients select the right products for their projects. Whether you’re looking for ASME B16.5 standard flanges or custom solutions, Welleshaft has the resources to provide the highest quality flanges at competitive prices.

Section 7: Why Choose Welleshaft?
With years of experience and advanced manufacturing capabilities, Welleshaft is your go-to supplier for forged flanges and fittings. We offer:
- Custom solutions to meet specific client needs.
- A broad selection of flange types, including weld neck, blind, and slip-on flanges.
- Products that adhere to strict international standards such as ASME B16.5.
- Competitive pricing and reliable global shipping.
Welleshaft is committed to delivering top-quality forged flanges that exceed your expectations in terms of performance and durability. Partner with us for all your forged flange needs, and ensure the success of your projects with reliable and durable products.