Top Metal Injection Molding Manufacturer | High-Precision Molding Solutions
Metal Injection Molding (MIM) is revolutionizing how complex metal parts are manufactured, offering unparalleled precision, efficiency, and versatility. As industries continue to demand more sophisticated and reliable components, finding the right MIM manufacturer is crucial. This article will delve into why Welleshaft stands out as a top choice among metal injection molding companies, exploring our expertise, the industries we serve, and our global presence.
Section 1: What is Metal Injection Molding?
Metal Injection Molding (MIM) is a process that combines the versatility of plastic injection molding with the performance characteristics of metal. This technique involves mixing fine metal powders with a binder to create a feedstock, which is then injected into molds to form complex shapes. After molding, the binder is removed, and the remaining metal is sintered to achieve the desired density and mechanical properties.
1.1.Industries That Use Metal Injection Molding
Metal injection molding is employed across various industries due to its ability to produce high-precision and complex components. Key sectors include:
Aerospace: For producing lightweight, high-strength parts that meet stringent safety and performance standards.
Automotive: In manufacturing components like turbochargers, valve seats, and transmission gears.
Medical Devices: To create intricate parts for surgical instruments and implants.
Consumer Electronics: For producing durable, miniaturized components used in modern devices.
Defense: In the production of critical components for firearms, ammunition, and tactical equipment.
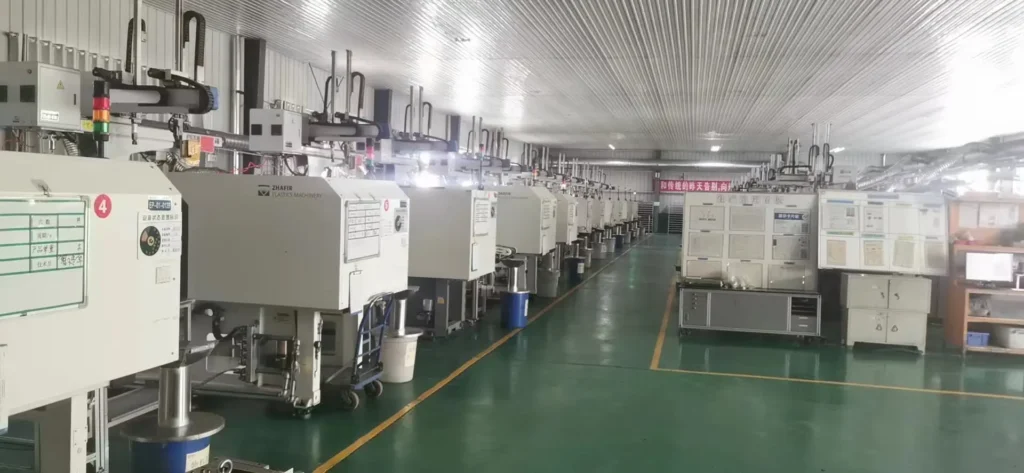
Section 2: Welleshaft: A Leading Metal Injection Molding Manufacturer
1.Expertise in Metal Injection Molding
Welleshaft is renowned for its high-quality metal injection molding services. With 15 years of experience in the industry, we excel in delivering precision-engineered components that meet the most demanding specifications. Our state-of-the-art facilities and advanced MIM machines enable us to produce complex geometries with tight tolerances, ensuring exceptional performance and reliability.
2.Global Reach and Local Expertise
As a trusted global supplier and contract manufacturer, Welleshaft has established a strong presence in key markets worldwide. Our international footprint includes:
- Metal Injection Molding Companies in Singapore: Offering advanced MIM solutions tailored to the needs of the Singaporean market.
- Metal Injection Molding Companies in the USA: Providing top-notch molding services and support for American manufacturers.
- Metal Injection Molding Companies in Europe: Serving European clients with high-precision, high-quality components.
- Metal Injection Molding Companies in China:Delivering cost-effective and efficient molding solutions for the Chinese market.
- Metal Injection Molding Companies in India (Bangalore and Pune): Meeting the growing demands of the Indian manufacturing sector.
3.Welleshaft’s Cutting-Edge MIM Machines
Welleshaft is also a leading MIM machine manufacturer, offering state-of-the-art machinery designed to optimize the molding process. Our MIM machines are built to handle a variety of metal powders and produce components with exceptional detail and consistency.
4.Why Choose Welleshaft?
Innovative Technology: Our advanced MIM machines and manufacturing techniques ensure the highest quality and precision.
Global Supply Chain: With operations in major markets worldwide, we can serve clients across different regions effectively.
Expert Team: Our skilled professionals bring extensive knowledge and experience to every project, ensuring top-notch results.
Commitment to Excellence: We prioritize quality control and customer satisfaction, making us a reliable partner for your metal injection molding needs.
Section 3: The Evolution of Metal Injection Molding
1.Who Invented Metal Injection Molding?
Metal Injection Molding was developed in the late 1970s by the researchers at the Massachusetts Institute of Technology (MIT). The process has since evolved, incorporating advanced materials and technologies to meet the growing demands of various industries.
2.What is the Largest Injection Molding Company in the World?
Several large companies dominate the global injection molding industry, but specific rankings can vary based on criteria such as revenue, production capacity, and market share. Welleshaft is proud to be recognized among the top metal injection molding companies, known for our commitment to quality and innovation.
For more information on high-quality MIM Manufacturer and to find the perfect solution for your application, please contact us.
Jinan Welle Metal Products Co., Ltd (Welleshaft)
Website: www.welleshaft.com
Email: [email protected]
Phone: +86-156-5017-9596
Explore our range of durable and reliable MIM Parts today!
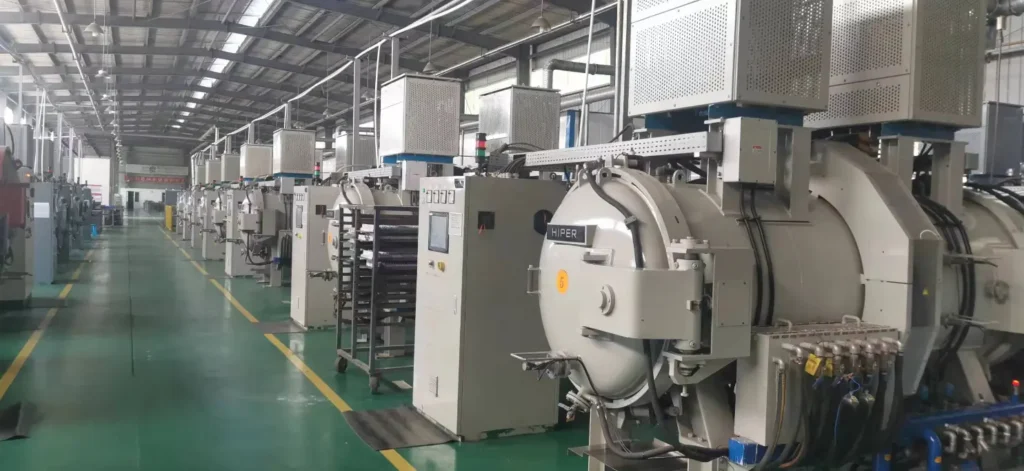
Section 4: Metal Injection Molding Services Offered by Welleshaft
At Welleshaft, we provide a comprehensive range of metal injection molding services, including:
- Custom MIM Solutions:Tailored to meet specific design and performance requirements.
- Prototype Development:Rapid prototyping services to help clients validate designs before full-scale production.
- High-Volume Production:Efficient manufacturing processes to handle large production runs without compromising quality.
Section 5: Choosing the Best Metal Injection Molding Manufacturer
5.1.What to Look For in a MIM Manufacturer
When selecting a Metal Injection Molding (MIM) manufacturer, several key factors should be considered to ensure that you choose a partner who can meet your project requirements and deliver high-quality results. Here are some important aspects to look for in a MIM manufacturer:
5.1.1. Technical Expertise
Material Knowledge: The manufacturer should have extensive experience working with a variety of metal powders and binders to suit different applications.
Design Capabilities: They should be proficient in designing and optimizing molds for complex geometries and high-precision parts.
Process Understanding: The manufacturer should have a deep understanding of the MIM process, including feedstock preparation, molding, debinding, and sintering.
5.1.2. Quality Control
Certifications: Look for certifications such as ISO 9001, ISO/TS 16949, or other relevant industry standards that demonstrate a commitment to quality management.
Inspection Procedures: The manufacturer should have rigorous quality control procedures in place, including regular inspection and testing of parts to ensure they meet specified tolerances and performance standards.
Traceability: Ensure that the manufacturer has systems in place for tracking and documenting the production process to identify and address any issues promptly.
5.1.3. Production Capabilities
Equipment: The manufacturer should have state-of-the-art MIM machines and equipment capable of handling your specific requirements, such as high-volume production or complex part geometries.
Capacity: Assess whether the manufacturer can handle your production volume, whether it’s a small batch or large-scale manufacturing.
Flexibility: Evaluate their ability to adapt to changes in design or production schedules, as well as their capacity for rapid prototyping and short lead times.
5.1.4. Experience and Track Record
Industry Experience: Choose a manufacturer with experience in your specific industry or application, whether it’s aerospace, automotive, medical devices, or consumer electronics.
Client References: Request references or case studies from past or current clients to gauge their satisfaction and the manufacturer’s performance on similar projects.
5.1.5. Technical Support and Collaboration
Engineering Support: The manufacturer should provide engineering support throughout the project, from initial design to final production, to help optimize designs and solve any technical challenges.
Communication: Effective communication is crucial for a successful partnership. Ensure the manufacturer is responsive, transparent, and willing to collaborate closely with your team.
5.1.6. Cost and Value
Competitive Pricing: While cost is an important factor, it should be balanced with the quality of the product and the services provided. Beware of manufacturers offering significantly lower prices, as this may indicate compromised quality.
Value-Added Services: Consider additional services offered, such as post-processing, finishing, or assembly, which can add value to your project and reduce the need for multiple suppliers.
5.1.7. Global Presence and Local Support
Geographic Reach: If your project requires global support or shipping, choose a manufacturer with a strong international presence or the ability to provide local support in key regions.
Local Facilities: For regions with specific regulatory or market needs, having local manufacturing facilities or representatives can be beneficial.
5..1.8. Innovation and R&D
Investment in Technology: Look for manufacturers that invest in research and development to stay at the forefront of MIM technology and improve their processes.
Innovation: Evaluate their commitment to innovation in materials, techniques, and solutions to meet evolving industry demands and standards.
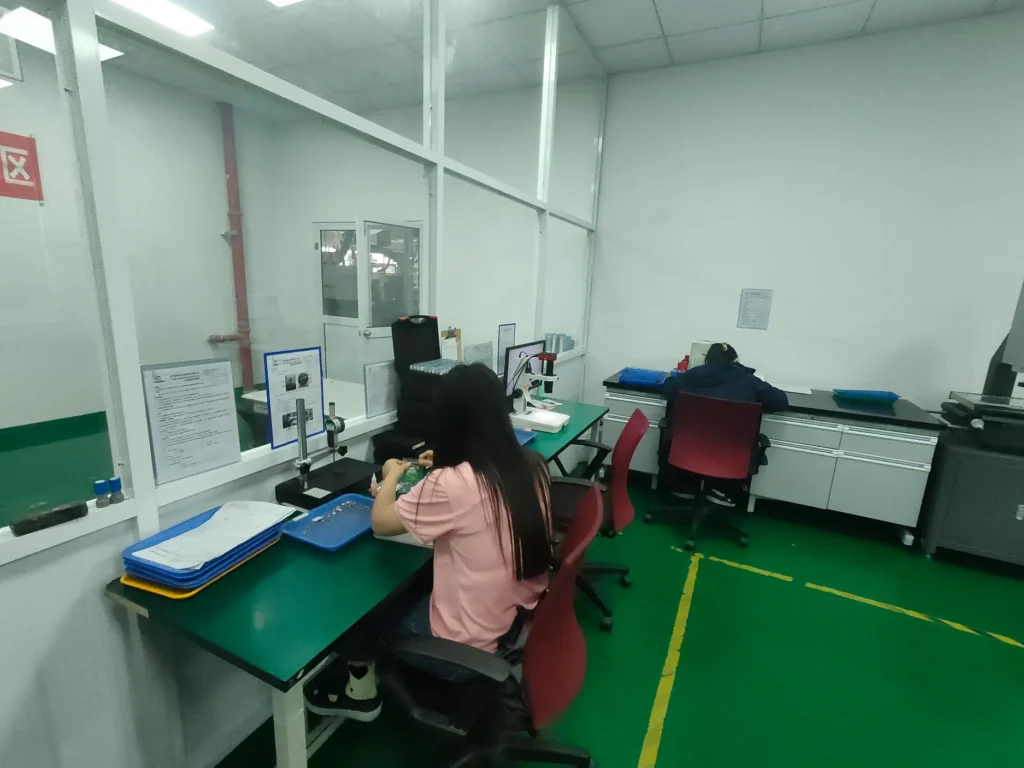
5.2.Why Welleshaft is the Best Choice
Welleshaft’s extensive experience, advanced technology, and global reach make us a standout choice for metal injection molding. Whether you are looking for a reliable supplier in Singapore, the USA, Europe, China, or India, Welleshaft offers the expertise and resources to meet your needs.
Conclusion
Metal injection molding continues to transform manufacturing across various industries, and selecting the right manufacturer is crucial for achieving high-quality results. Welleshaft, as a top metal injection molding manufacturer, provides cutting-edge solutions and unparalleled expertise to ensure your components meet the highest standards. Contact us today to learn more about our services and how we can support your next project.
For more information or to discuss your specific needs, visit Welleshaft or reach out to us directly.