Titanium Injection Molding | Precision Parts Manufacturing & Solutions
In the world of advanced manufacturing, titanium injection molding has emerged as a cutting-edge technique that allows for the creation of highly precise and complex titanium components. This method is particularly popular in industries where the strength, durability, and lightweight properties of titanium are essential, such as aerospace, medical devices, automotive, and electronics. In this article, we will explore the intricacies of titanium injection molding, its benefits, applications, and why Welleshaft is the trusted global supplier and contract manufacturer for your titanium injection molding needs.
Section 1: What is Titanium Injection Molding?
Titanium injection molding (TIM) is a manufacturing process that involves injecting a mixture of titanium powder and a binder material into a mold to create complex shapes. This process is similar to metal injection molding (MIM) but is specifically designed for titanium, which is known for its strength, corrosion resistance, and biocompatibility. The process begins with the creation of a feedstock, a blend of titanium powder and a binder. This feedstock is then injected into a mold under high pressure, forming the desired shape. After molding, the binder is removed, and the part is sintered to achieve the final properties of titanium.
1.1.How is Titanium Injection Molded?
The titanium injection molding process involves several key steps:
1. Feedstock Preparation:
The process begins with the creation of a feedstock, a homogeneous mixture of fine titanium powder and a thermoplastic binder. This mixture is critical for ensuring the proper flow of the material during the injection process.
2. Injection Molding:
The feedstock is injected into a precision mold under high pressure. The mold is designed to create the desired shape, and the injection process ensures that the material fills the mold cavity completely, capturing every detail.
3. Debinding:
Once the part is molded, the binder material needs to be removed. This step, known as debinding, is essential for ensuring that the final part is composed solely of titanium. The debinding process typically involves thermal or solvent methods.
4. Sintering:
After debinding, the part undergoes sintering, where it is heated to a temperature just below its melting point. This process causes the titanium particles to fuse together, resulting in a dense, solid component with the desired mechanical properties.
5. Finishing:
Depending on the application, the sintered part may undergo additional finishing processes, such as machining, polishing, or surface treatments, to achieve the required specifications.
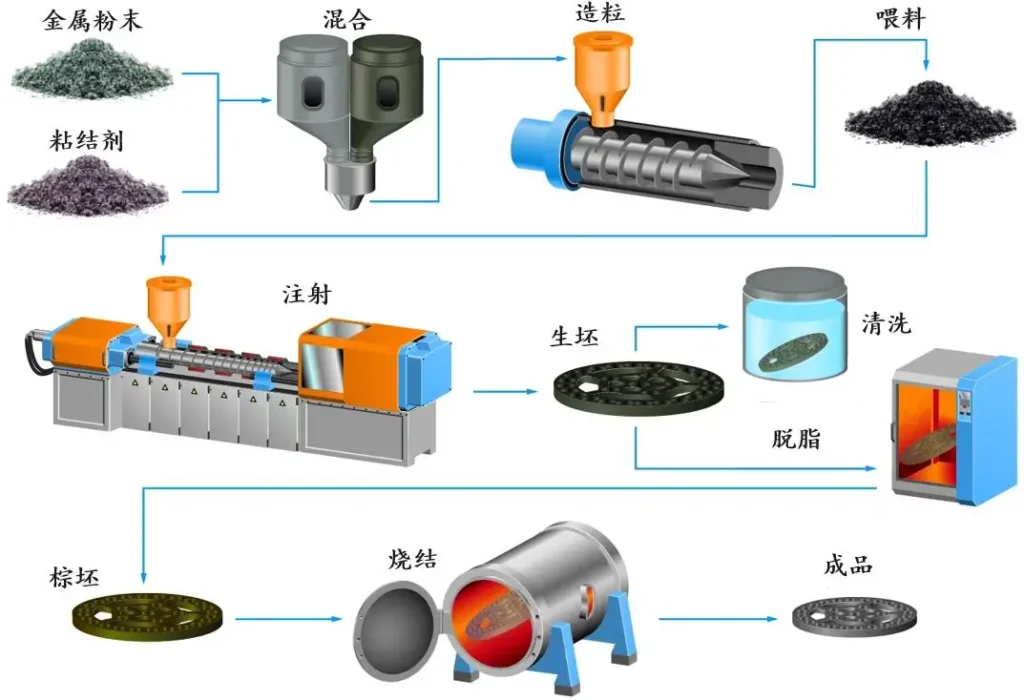
Section 2: The Advantages of Titanium Injection Molding
1. Precision and Complexity:
Titanium injection molding allows for the production of highly complex and precise components that would be difficult or impossible to achieve through traditional machining processes. This precision is crucial for industries where exact specifications are non-negotiable.
2. Material Efficiency:
The TIM process significantly reduces material waste compared to traditional manufacturing methods. The near-net-shape capabilities mean that less machining is required, and the process can create parts with minimal excess material.
3. Cost-Effectiveness:
Despite the initial cost of tooling, titanium injection molding can be more cost-effective for high-volume production runs. The ability to produce complex shapes in a single step reduces the need for multiple manufacturing processes, saving time and money.
4. Strength and Durability:
Titanium is known for its exceptional strength-to-weight ratio, corrosion resistance, and biocompatibility. Parts produced through titanium injection molding retain these properties, making them ideal for demanding applications.
Section 3: Applications of Titanium Injection Molding
Titanium injection molding is used in a wide range of industries due to its ability to produce high-quality parts with complex geometries. Some of the most common applications include:
1. Medical Devices:
Titanium’s biocompatibility makes it ideal for medical implants, surgical instruments, and dental components. The precision of TIM ensures that these parts meet the strict regulatory standards required in the medical field.
2. Aerospace and Defense:
The aerospace industry demands lightweight, high-strength components for aircraft and spacecraft. MIM titanium allows for the production of complex parts that meet these stringent requirements, such as turbine blades, fasteners, and structural components.
3. Automotive:
In the automotive industry, titanium injection molding is used to create parts that require a high strength-to-weight ratio, such as engine components, exhaust systems, and suspension parts.
4. Electronics:
Titanium’s corrosion resistance and durability make it suitable for electronic components, including connectors, housings, and heat sinks.
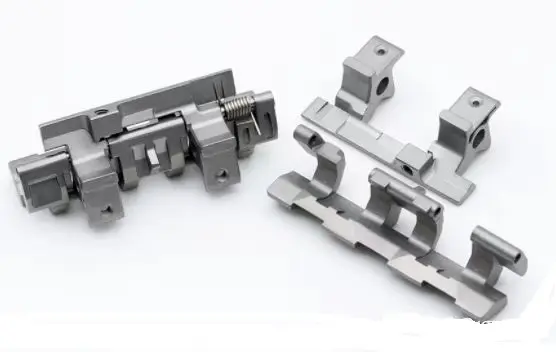
Section 4: Understanding the Cost of Titanium Injection Molding
The titanium injection molding price can vary depending on several factors, including the complexity of the part, the volume of production, and the cost of raw materials. While the initial investment in tooling can be high, the overall cost can be reduced for large production runs due to the efficiency of the process. It’s also important to consider the long-term savings associated with reduced material waste and the ability to produce parts with minimal secondary machining.
1. Material Costs
Titanium is a premium material known for its excellent properties, but it comes with a high price tag. The cost of raw titanium powder used in injection molding is significantly higher than that of other metals such as aluminum or steel. Titanium’s high melting point and the need for specialized equipment to handle it also contribute to the material costs.
However, titanium’s durability and strength often justify the initial expense, especially in applications where performance and longevity are critical. To optimize material costs, manufacturers might consider using titanium alloys, which can offer similar benefits at a lower price point.
2. Tooling and Mold Costs
The tooling and mold costs in titanium injection molding are substantial. The process requires custom molds that can withstand the high temperatures and pressures involved in molding titanium. These molds are typically made from hardened steel or other durable materials, and their design and fabrication can be time-consuming and expensive.
The complexity of the component being molded also affects tooling costs. More intricate designs require more sophisticated molds, which can drive up the overall cost. However, the ability to produce highly complex shapes with minimal post-processing can offset these costs by reducing the need for additional machining or assembly.
3. Processing Costs
Titanium injection molding is a multi-step process that includes mixing the titanium powder with a binder, injecting the mixture into a mold, and then sintering the part to remove the binder and densify the material. Each of these steps requires specialized equipment and precise control over temperature, pressure, and other variables, all of which contribute to processing costs.
The sintering process, in particular, is energy-intensive and requires precise control to achieve the desired material properties. This stage can be a significant contributor to the overall cost, but it is essential for ensuring the strength and integrity of the final product.
4. Labor Costs
Highly skilled labor is required for the titanium injection molding process. From the design and production of the molds to the operation of the injection molding machines and the sintering process, each step demands expertise and precision. The labor costs associated with TIM are higher compared to traditional molding processes due to the specialized skills and knowledge required.
Manufacturers can optimize labor costs by investing in automation and training, but the need for skilled technicians remains a crucial factor in maintaining quality.
5. Production Volume
Production volume plays a significant role in determining the cost per part in titanium injection molding. While the initial setup costs (including tooling and mold creation) are high, these costs can be amortized over a large production run. Higher production volumes can lead to a lower cost per part, making titanium injection molding more cost-effective for mass production.
For smaller production runs or prototyping, the high setup costs may result in a higher per-unit cost, making other manufacturing methods more attractive unless the unique benefits of TIM are essential for the application.
6. Post-Processing Costs
Although titanium injection molding produces parts with near-net-shape precision, some post-processing may still be required. This can include machining, surface treatment, or additional heat treatments to achieve the desired final properties. These post-processing steps add to the overall cost and must be factored into the total expense of producing titanium components.
Minimizing post-processing through careful design and optimization of the injection molding process can help reduce these additional costs.
7. Quality Control and Testing
Given the high-performance applications of titanium components, rigorous quality control and testing are necessary to ensure that each part meets the required specifications. This includes dimensional inspection, material property verification, and non-destructive testing methods such as X-ray or ultrasound.
The costs associated with quality control are essential for maintaining the reliability and safety of the final product, particularly in critical industries like aerospace and medical devices.
Section 5: Binder Jetting Titanium: An Alternative to Injection Molding
Binder jetting titanium is an additive manufacturing process that offers an alternative to traditional injection molding. In this process, a binder is selectively deposited onto a bed of titanium powder, layer by layer, to create the desired shape. The part is then sintered to fuse the titanium particles together. Binder jetting is particularly useful for producing low-volume, complex parts with minimal material waste. However, it may not offer the same level of mechanical properties as injection-molded titanium parts.
1. Understanding Binder Jetting
Binder jetting is a 3D printing technology that involves depositing a liquid binding agent onto a bed of titanium powder, layer by layer, to build a part. After printing, the part is typically cured, then sintered to remove the binder and fuse the titanium particles into a solid structure. Unlike other additive manufacturing methods that use lasers or electron beams, binder jetting operates at lower temperatures and does not require support structures during the build process.
2. Advantages of Binder Jetting Titanium
a. Design Flexibility
One of the most significant advantages of binder jetting is its ability to create complex geometries that would be challenging or impossible with traditional methods like injection molding. Intricate internal features, lattice structures, and complex surface textures can be easily achieved without the need for complex tooling or molds.
b. Material Efficiency
Binder jetting is an additive process, meaning that material is only used where needed, resulting in minimal waste. This is particularly beneficial when working with expensive materials like titanium, as it reduces overall material costs.
c. Speed and Scalability
Binder jetting can produce parts relatively quickly, especially compared to processes like injection molding, which require time-consuming mold design and fabrication. Additionally, the process is easily scalable; multiple parts can be printed simultaneously on a single build platform, making it suitable for both small-batch production and large-scale manufacturing.
d. Lower Initial Costs
Unlike titanium injection molding, which requires expensive tooling and molds, binder jetting does not need any specialized equipment beyond the printer itself. This results in lower initial setup costs, making it an attractive option for prototyping or small production runs.
3. Challenges and Limitations
a. Mechanical Properties
While binder jetting can produce parts with complex shapes, the mechanical properties of the final product may not match those of parts made through injection molding or traditional methods. The sintering process used to densify the printed parts may result in porosity or incomplete fusion, leading to lower strength and durability. However, ongoing advancements in binder jetting technology and post-processing techniques are continually improving the mechanical properties of printed titanium parts.
b. Surface Finish
Parts produced by binder jetting typically have a rougher surface finish compared to those made by injection molding. This may necessitate additional post-processing steps, such as machining or polishing, to achieve the desired surface quality, which can add to the overall cost and lead time.
c. Size Limitations
The size of parts that can be produced through binder jetting is limited by the build volume of the printer. Large components may need to be printed in sections and then assembled, which can introduce additional complexity and potential weak points.
4. Cost Comparison: Binder Jetting vs. Injection Molding
a. Initial Investment
As mentioned earlier, the initial investment for binder jetting is significantly lower than for injection molding. The absence of expensive molds and tooling makes binder jetting an attractive option for manufacturers looking to minimize upfront costs, especially for low-volume production or prototyping.
b. Per-Part Costs
For small production runs, binder jetting can be more cost-effective than injection molding due to the lower setup costs. However, as production volumes increase, the per-part cost of injection molding may become more competitive, as the high initial costs are spread across a larger number of units.
c. Time to Market
Binder jetting typically offers faster time-to-market compared to injection molding, as it eliminates the need for mold design and fabrication. This can be a critical factor for companies looking to rapidly prototype and iterate designs or respond quickly to market demands.
5. Applications of Binder Jetting Titanium
Binder jetting is particularly well-suited for applications where design complexity, material efficiency, and rapid production are key considerations. Industries such as aerospace, medical devices, and automotive can benefit from the technology’s ability to produce lightweight, high-performance components with intricate geometries.
For example, in the aerospace industry, binder jetting can be used to create complex titanium parts with internal cooling channels or lattice structures that reduce weight while maintaining strength. In the medical field, the technology is ideal for producing custom implants and prosthetics that require precise geometry and biocompatibility.
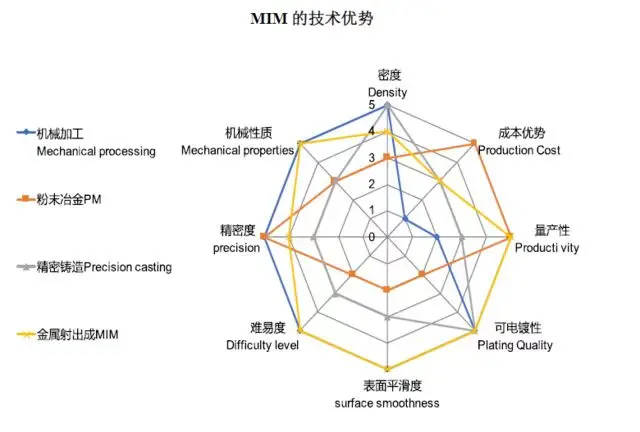
Section 6: Welleshaft: Your Trusted Global Supplier and Contract Manufacturer
When it comes to titanium injection molding, Welleshaft stands out as a trusted global supplier and contract manufacturer. With over 13 years of experience in metal casting and forging, Welleshaft has the expertise, state-of-the-art equipment, and commitment to quality that you need for your titanium components.
6.1.Why Choose Welleshaft?
1. Expertise:
Welleshaft’s team of engineers and technicians are experts in titanium injection molding and metal injection molding titanium. They understand the unique challenges of working with titanium and are dedicated to delivering high-quality parts that meet your exact specifications.
2. Customization:
Welleshaft offers complete customization of your titanium components, from design to production. Whether you need a small batch of prototypes or large-scale production, Welleshaft can accommodate your needs.
3. Quality Assurance:
Welleshaft adheres to strict quality control standards at every stage of the manufacturing process. This ensures that your parts meet the highest standards of precision, strength, and durability.
4. Competitive Pricing:
Welleshaft offers competitive pricing for titanium injection molding and related services. They work with you to optimize your production process, reducing costs while maintaining the highest quality.
5. Global Reach:
With a strong global presence, Welleshaft is well-positioned to serve clients around the world. Their reliable logistics and supply chain management ensure timely delivery of your parts, no matter where you are located.
Conclusion
Titanium injection molding is a powerful manufacturing process that enables the production of high-precision, complex titanium components for a variety of industries. Whether you’re in aerospace, medical, automotive, or electronics, TIM offers the strength, durability, and efficiency you need for your critical applications.
When it comes to sourcing titanium injection molded parts, Welleshaft is the trusted global supplier and contract manufacturer you can rely on. With their expertise, commitment to quality, and competitive pricing, Welleshaft is the partner you need to take your projects to the next level.
For all your titanium injection molding needs, contact Welleshaft today and discover how they can help you achieve your manufacturing goals with precision and excellence.