Submersible Pump Shaft – Precision Engineered for Harsh Conditions
Submersible pumps are vital for numerous industries, providing a reliable solution for moving fluids from challenging locations. However, the effectiveness and longevity of these pumps hinge on the quality of their components, particularly the submersible pump shaft. This article explores the critical role of the submersible pump shaft, the challenges posed by harsh operating conditions, and how precision engineering ensures optimal performance. We’ll also introduce Welleshaft as a trusted global supplier and contract manufacturer of high-quality submersible pump shafts.
Understanding the Submersible Pump Shaft
The submersible pump shaft serves as the central component that transmits rotational power from the motor to the impeller, enabling the pump to move fluids. It’s a critical link in the pump’s drivetrain. Unlike shafts in surface-mounted pumps, the submersible pump shaft operates fully immersed in the fluid being pumped, which can be corrosive or abrasive. Here’s a breakdown of the shaft’s function and different types:
Function: Transmits torque from the motor to the impeller, driving fluid movement.
Materials: Typically made of stainless steel, carbon steel, or specialized alloys for corrosion resistance.
Types: Can be solid shafts, hollow shafts, or stepped shafts depending on the pump design and application.
Related Terms: You might also hear it referred to as a rotor shaft, impeller shaft, pump spindle, or motor shaft, all indicating similar core functions but possibly in relation to different parts of the shaft and pump assembly.
The Challenges of Harsh Operating Conditions
Submersible pumps often operate in extremely challenging environments that can significantly impact the lifespan and performance of the pump shaft. These conditions include:
Corrosion: Exposure to corrosive fluids, such as seawater, acids, or chemicals, can lead to rapid shaft degradation.
Abrasion: Abrasive particles in the pumped fluid, like sand, silt, or solids, can erode the shaft’s surface.
High Temperatures: Elevated temperatures can weaken the shaft’s material and accelerate corrosion.
High Pressure: Submersible pumps operate at significant depths, subjecting the shaft to high pressure that can cause fatigue.
Vibration & Fatigue: Constant vibration and cyclical loading can lead to fatigue failure, especially if the shaft is not properly balanced or manufactured.
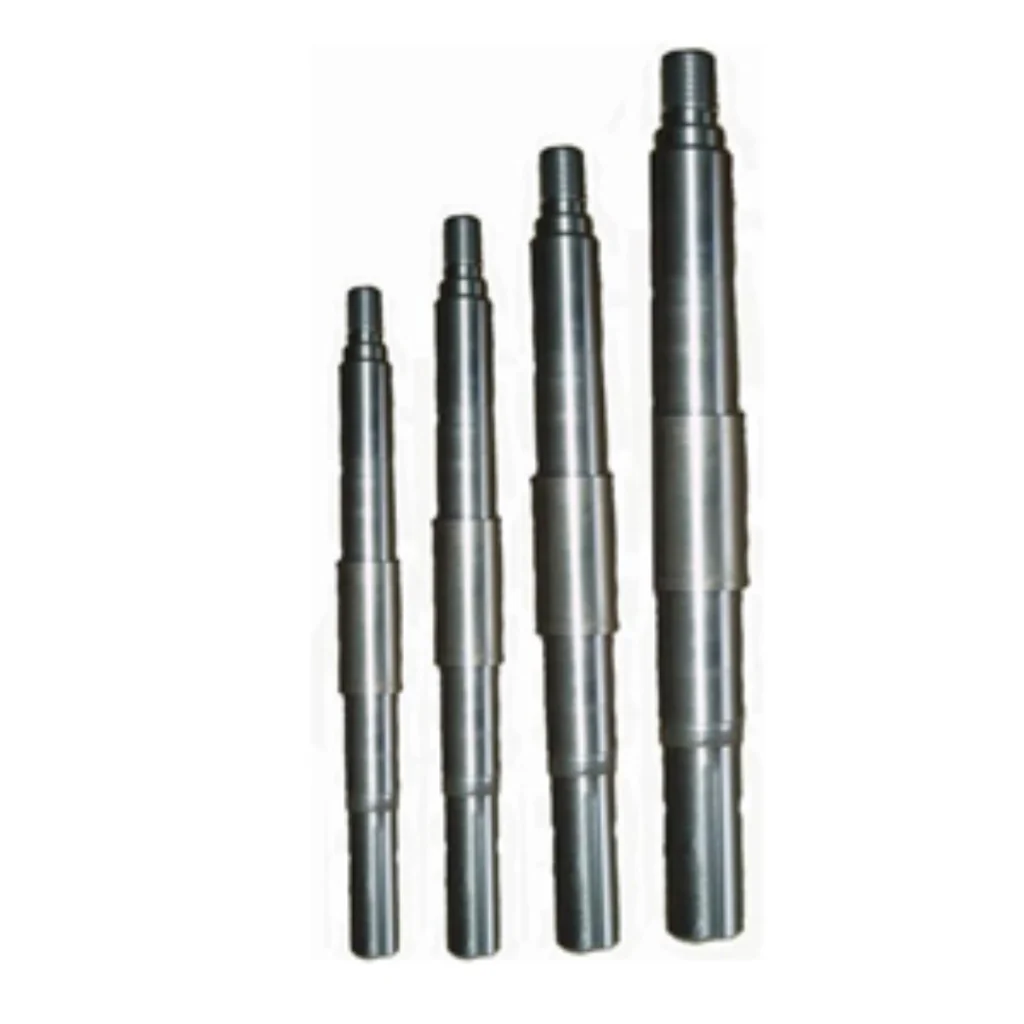
Precision Engineering for Enhanced Durability
To overcome these challenges, submersible pump shafts must be precision engineered and manufactured using high-quality materials and advanced techniques. Key aspects of precision engineering include:
Material Selection: Choosing the right material is paramount. Stainless steel alloys, such as 316 or duplex stainless steel, offer excellent corrosion resistance. Specialized alloys may be required for extremely aggressive environments.
Surface Finish: A smooth surface finish minimizes friction and reduces wear from abrasive particles.
Dimensional Accuracy: Precise dimensions and tolerances are essential for proper fit and alignment, reducing vibration and stress.
Heat Treatment: Heat treatment processes can enhance the shaft’s strength, hardness, and fatigue resistance.
Balancing: Dynamically balancing the shaft minimizes vibration and extends its lifespan.
The Role of Shaft Design
The design of the submersible pump shaft itself plays a crucial role in its ability to withstand harsh conditions. Considerations include:
Shaft Diameter: A larger diameter shaft offers greater strength and resistance to bending and twisting.
Keyways and Splines: These features transmit torque but can also be points of stress concentration. Proper design and machining are crucial.
Surface Coatings: Applying protective coatings, such as ceramic or tungsten carbide, can further enhance corrosion and wear resistance.
Coupled Shafts: Using coupled shafts can help dampen vibrations and make field installation and maintenance easier.
Importance of Quality Control
Rigorous quality control is essential throughout the manufacturing process to ensure that submersible pump shafts meet the required specifications and performance standards. This includes:
Material Testing: Verifying the chemical composition and mechanical properties of the raw materials.
Dimensional Inspection: Checking the shaft’s dimensions and tolerances using precision measuring instruments.
Non-Destructive Testing (NDT): Employing techniques like ultrasonic testing or magnetic particle inspection to detect internal flaws or surface cracks.
Performance Testing: Simulating operating conditions to evaluate the shaft’s performance under load and stress.
Table: Common Submersible Pump Shaft Materials and Applications
Material |
Common Applications |
Key Properties |
304 Stainless Steel |
General-purpose submersible pumps, clean water applications |
Good corrosion resistance, weldable, relatively low cost |
316 Stainless Steel |
Corrosive environments, seawater pumps, chemical processing |
Superior corrosion resistance to 304, higher cost |
Duplex Stainless Steel |
Highly corrosive environments, offshore platforms, aggressive chemicals |
Excellent corrosion resistance, high strength, high cost |
Carbon Steel (with coating) |
Industrial pumps, non-corrosive fluids |
High strength, low cost, requires protective coating to prevent corrosion |
Alloy Steel |
High-stress applications, deep well pumps, high-horsepower pumps |
High strength, good fatigue resistance, moderate corrosion resistance |
Ceramic Coating |
For applications with extremely abrasive elements such as slurry, mining tailings, or drilling mud. |
Increases surface harness, resists wear and corrosion, costly due to precision application, brittle and prone to cracking in some applications. |
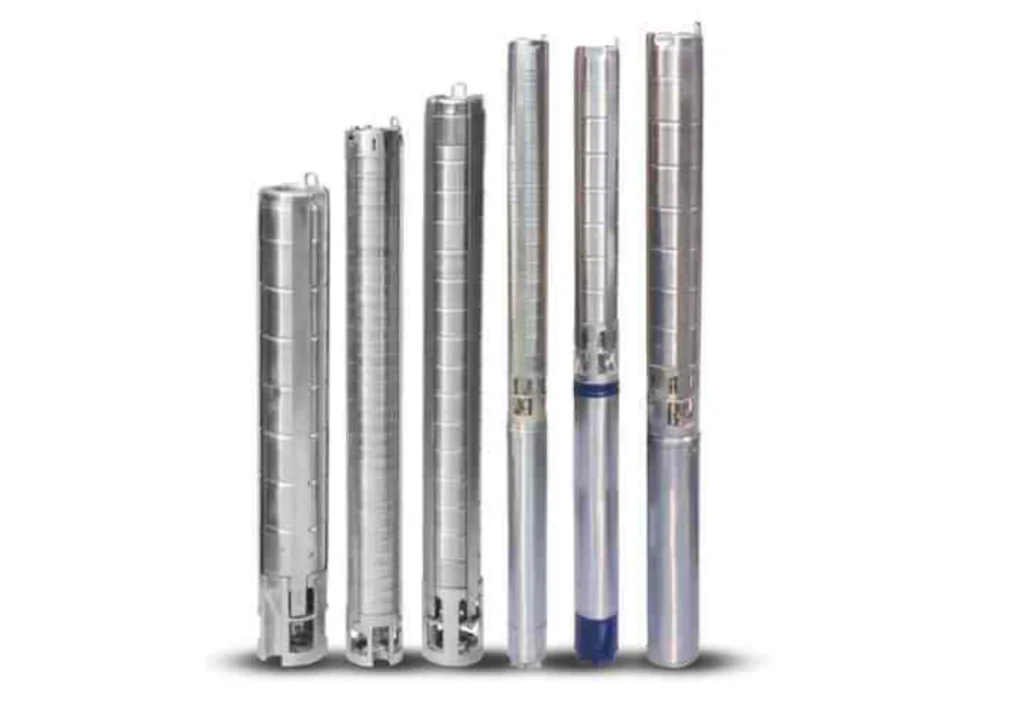
The Cost of Substandard Shafts
Using inferior submersible pump shafts can lead to a cascade of problems, including:
Premature Failure: Shafts that are not properly engineered or manufactured are prone to failure, resulting in pump downtime and costly repairs.
Reduced Pump Efficiency: Worn or damaged shafts can reduce pump efficiency, increasing energy consumption and operating costs.
Contamination: Shaft failure can lead to contamination of the pumped fluid, particularly in sensitive applications like food processing or pharmaceuticals.
Safety Hazards: Catastrophic shaft failure can pose safety hazards to personnel and equipment.
Introducing Welleshaft: Your Trusted Global Supplier
When it comes to submersible pump shafts designed for harsh conditions, reliability and performance are paramount. Welleshaft stands out as a trusted global supplier and contract manufacturer, offering a comprehensive range of precision-engineered shafts to meet the most demanding applications. With decades of experience and a commitment to quality, Welleshaft provides:
High-Quality Materials: Welleshaft uses only the finest materials, carefully selected for their corrosion resistance, strength, and durability.
Advanced Manufacturing Techniques: Welleshaft employs state-of-the-art manufacturing processes, including precision machining, heat treatment, and surface finishing, to ensure that their shafts meet the highest standards.
Custom Solutions: Welleshaft offers custom design and manufacturing services to meet specific application requirements. They work closely with customers to develop tailored solutions that optimize pump performance and longevity.
Global Reach: With a global network of manufacturing facilities and distribution partners, Welleshaft can provide timely and cost-effective solutions to customers worldwide.
Focus on Reliability: Committed to providing quality products, Welleshaft can produce shafts that meet industry standards, as well as custom build to application requirements.
Why Choose Welleshaft?
Expertise: Welleshaft’s team of experienced engineers and metallurgists possesses in-depth knowledge of submersible pump shaft design and materials.
Quality Assurance: Welleshaft maintains a rigorous quality assurance program to ensure that all shafts meet the highest standards of performance and reliability.
Competitive Pricing: Welleshaft offers competitive pricing without compromising on quality.
Customer Support: Welleshaft provides exceptional customer support, from initial consultation to after-sales service.
Complete Solutions: Offers all shaft types including, rotor shafts, submersible motor shafts, impeller shafts, and coupled shafts.
Conclusion
The submersible pump shaft is a critical component that plays a vital role in the reliable operation of submersible pumps. By understanding the challenges posed by harsh operating conditions and employing precision engineering techniques, it is possible to create shafts that withstand these challenges and provide long-lasting performance. Welleshaft is your trusted partner for submersible pump shafts, offering high-quality solutions that meet the most demanding application requirements. Contact Welleshaft today to discuss your specific needs and discover how they can help you optimize the performance and longevity of your submersible pumps.