Solving Gear Drive Challenges with Hypoid Gears
Gear drives are the unsung heroes of mechanical systems, silently translating power and motion across countless applications. However, designers often face significant challenges when selecting the optimal gear type. Space constraints, noise reduction, high torque requirements, and the need for non-intersecting shafts can all present difficult hurdles. Enter the hypoid gear: a versatile and often overlooked solution for overcoming these obstacles.
What are Hypoid Gears?
A hypoid gear is a type of spiral bevel gear with non-intersecting axes. This means that the pinion (the smaller gear) and the gear (the larger gear) are offset from each other. This offset is the defining characteristic of a hypoid gear and what gives it its unique advantages. Hypoid gears are categorized in different kinds as hypoid gear sets, hypoid pinion and gear, offset gears, hypoid final drive, hypoid bevel gears, spiral bevel gears, offset-axis gears, offset pinion gears, high-offset bevel gears, non-intersecting axis bevel gears, angled-axis gears, lower pinion gears, high-contact-ratio bevel gears, undermounted pinion gears, high-sliding-motion gears, asymmetric bevel gears.
A Quick Comparison: Hypoid vs. Other Gear Types
To understand the strengths of hypoid gears, it’s helpful to compare them to other common types:
Spur Gears: Simple and efficient for parallel shafts but noisy at high speeds.
Helical Gears: Quieter than spur gears due to gradual tooth engagement but generate axial thrust.
Bevel Gears: Transmit motion between intersecting shafts, but standard bevel gears are limited in ratio.
Spiral Bevel Gears: A more advanced bevel gear with curved teeth for smoother operation and higher load capacity. Hypoid gears are a type of spiral bevel gear, but with the added benefit of a non-intersecting axis.
Worm Gears: High gear ratios possible but have lower efficiency due to significant sliding friction.
The following table provides a more structured overview:
Feature | Spur Gear | Helical Gear | Bevel Gear | Spiral Bevel Gear | Hypoid Gear | Worm Gear |
Shaft Orientation | Parallel | Parallel | Intersecting | Intersecting | Non-Intersecting | Perpendicular |
Noise Level | High | Medium | Medium | Low | Low | Low |
Gear Ratio Range | Low | Low | Medium | Medium | High | Very High |
Efficiency | High | High | Medium | Medium | Medium to Low | Low |
Load Capacity | Medium | Medium | Medium | High | High | Medium |
Complexity | Low | Medium | Medium | High | High | Medium |
Sliding Action | Low | Medium | Low | Low | High | Very High |
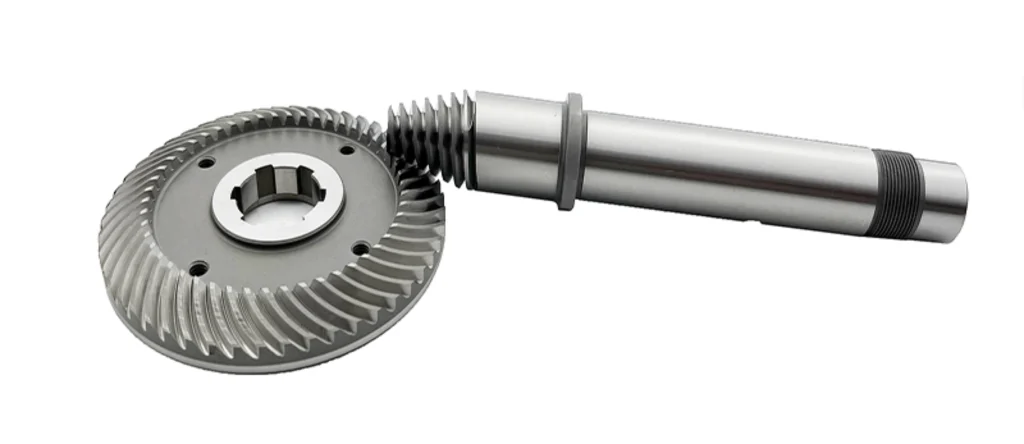
Key Advantages of Hypoid Gears
Hypoid gears offer a unique combination of benefits that make them ideal for specific applications:
High Gear Ratios: The offset axis allows for larger gear ratios than comparable bevel gear sets within the same physical space. This is particularly advantageous in applications where space is limited. They have high-ratio.
Compact Design: The offset allows the pinion to be smaller and positioned lower relative to the gear. This results in a lower center of gravity and a more compact overall design.
Smooth and Quiet Operation: The spiral teeth and gradual engagement provide smoother and quieter operation compared to straight bevel gears or spur gears.
High Torque Capacity: The larger tooth contact area of hypoid gears allows them to transmit high levels of torque.
Design Flexibility: The offset allows designers greater freedom in positioning components within a system.
Applications of Hypoid Gears
Hypoid gears are found in a wide range of applications, particularly where the advantages listed above are critical:
Automotive Differentials: This is perhaps the most well-known application. Hypoid gears are used to transmit power from the driveshaft to the axles, allowing the wheels to rotate at different speeds during turns. Hypoid final drive play important role in this part.
Industrial Machinery: Used in various types of machinery requiring high torque and compact designs, such as conveyors, mixers, and pumps.
Aerospace: Employed in aircraft actuators and other systems where weight and space are critical.
Off-Road Vehicles: Their ability to handle high torque and provide large gear reductions makes them suitable for off-road applications.
Robotics: Used in robotic joints and transmissions to provide precise motion control and high torque.
The Challenges of Hypoid Gear Design and Manufacturing
While hypoid gears offer numerous advantages, they also present unique challenges in design and manufacturing:
Complex Geometry: The non-intersecting axes and spiral teeth require sophisticated design tools and manufacturing processes.
High Sliding Friction: The sliding action between the teeth generates heat and requires specialized lubricants.
Precise Manufacturing Tolerances: Tight tolerances are essential to ensure proper meshing and minimize noise and vibration.
Specialized Lubrication: Hypoid gears require special lubricants that can withstand high pressures and temperatures. These lubricants typically contain additives that reduce friction and wear.
Hypoid Gear Lubrication
The significant sliding action in hypoid gear meshes generates substantial heat and pressure. Therefore, specialized lubricants are crucial for their proper operation and longevity. These lubricants typically contain extreme pressure (EP) additives, such as sulfur-phosphorus compounds, which form a protective film on the gear teeth to prevent wear and scuffing. The difference between hypoid and regular gear oil is in the additives. Regular gear oil may not provide sufficient protection under the high-pressure conditions found in hypoid gearboxes.
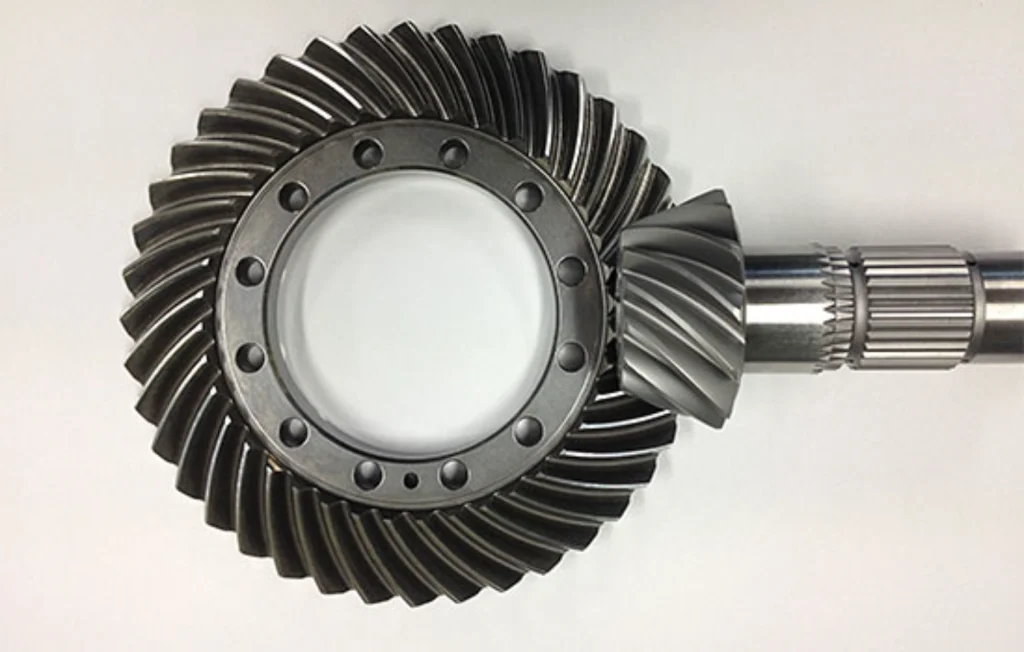
Hypoid Gearboxes
Hypoid gearboxes are self-contained units that house a hypoid gear set, bearings, and lubrication system. They are designed to provide a specific gear ratio and transmit power between shafts with a significant offset. These gearboxes are used in a wide range of industrial and automotive applications.
Selecting a Hypoid Gear Manufacturer
Choosing a reliable and experienced hypoid gear manufacturer is crucial for ensuring the quality and performance of your gear drives. Key considerations include:
Experience and Expertise: Look for a manufacturer with a proven track record in designing and manufacturing hypoid gears.
Manufacturing Capabilities: Ensure the manufacturer has the necessary equipment and technology to produce gears to the required specifications.
Quality Control: A robust quality control system is essential for ensuring the accuracy and reliability of the gears.
Materials Expertise: Understanding and working with appropriate materials is crucial for hypoid gear performance.
Customer Support: Choose a manufacturer that provides excellent customer support and technical assistance.
Why Choose Welleshaft for Your Hypoid Gear Needs?
Welleshaft stands out as a trusted global supplier and contract manufacturer of high-quality hypoid gears. With years of experience and a commitment to excellence, Welleshaft offers:
Expert Engineering Team: Welleshaft’s team of experienced engineers can assist you with every stage of the design and manufacturing process, from concept to production.
Advanced Manufacturing Technology: Welleshaft utilizes state-of-the-art CNC gear cutting machines and inspection equipment to ensure the highest levels of precision and accuracy.
Stringent Quality Control: Welleshaft’s quality control system is designed to meet the most demanding industry standards. They utilize coordinate measuring machines (CMMs) and other advanced inspection tools to verify the accuracy of every gear.
Custom Solutions: Welleshaft specializes in providing custom gear solutions tailored to your specific needs. Whether you require a small batch of prototype gears or high-volume production, Welleshaft can deliver.
Global Reach: With a global presence, Welleshaft can provide support and service wherever you are located.
Competitive Pricing: Welleshaft offers competitive pricing without compromising on quality.
By partnering with Welleshaft, you can be confident that you are receiving the highest quality hypoid gears and exceptional customer service. Contact Welleshaft today to discuss your specific gear drive requirements.
Conclusion
Hypoid gears offer a compelling solution to a wide range of gear drive challenges. Their ability to provide high gear ratios, compact designs, smooth operation, and high torque capacity makes them ideal for numerous applications. While the design and manufacturing of hypoid gears can be complex, working with an experienced and reputable manufacturer like Welleshaft can ensure the success of your project. By understanding the advantages and challenges of hypoid gears, engineers and designers can leverage their unique capabilities to create more efficient, reliable, and innovative mechanical systems.