Sintered Stainless Steel: High-Performance Solutions for Precision Engineering
Sintered stainless steel is a game-changer in the world of precision engineering, offering unparalleled performance and reliability. This article explores the benefits and applications of sintered stainless steel, comparing it with traditional stainless steel and steel, and highlighting why Welleshaft is your go-to global supplier and contract manufacturer for these advanced materials.
Section 1: What is Sintered Stainless Steel?
Sintered stainless steel is created through a process known as sintering, where stainless steel powder is heated to just below its melting point to form a solid mass. This technique allows for precise control over the material’s properties and structure, resulting in products with exceptional strength, durability, and performance.
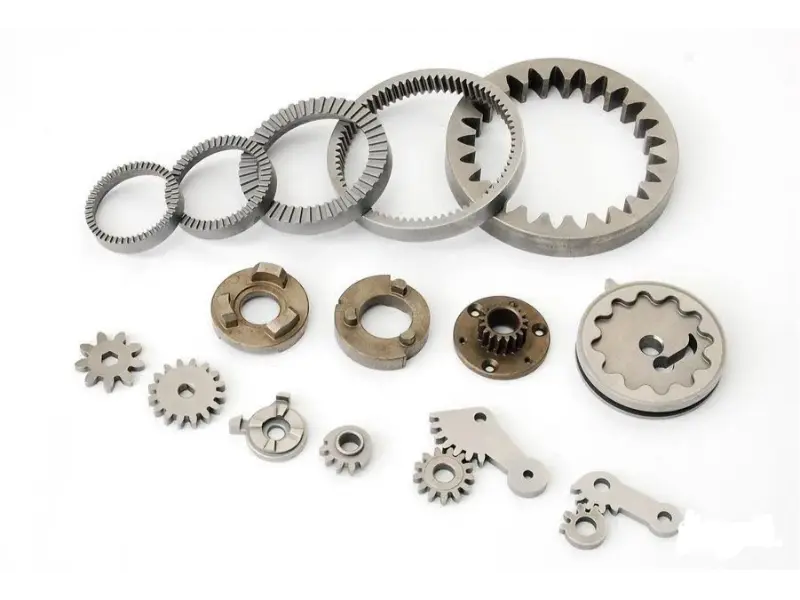
Section 2: Sintered Stainless Steel vs. Stainless Steel
While traditional stainless steel is manufactured through melting and casting, sintered stainless steel is produced from powder. The sintering process imparts several distinct advantages:
- Porosity Control: Sintering allows for controlled porosity, which can be tailored to specific applications, such as filtration.
- Material Efficiency: Less waste is generated compared to traditional manufacturing methods.
- Custom Properties: Sintered stainless steel can be engineered to meet specific performance criteria, including enhanced hardness and resistance to wear.
2.1. Key Differences Between Sintered Stainless Steel and Traditional Stainless Steel
1. Manufacturing Process
- Stainless Steel:Produced through melting and casting, followed by shaping and machining. The process involves melting raw materials and forming them into the desired shape, followed by cooling and solidifying.
- Sintered Stainless Steel:Created from powdered stainless steel that is compacted and heated. The sintering process involves heating the powder to form a solid structure without melting it completely.
2. Material Properties
- Stainless Steel:Offers high strength, corrosion resistance, and durability. The properties are generally uniform throughout the material, making it suitable for a wide range of applications.
- Sintered Stainless Steel:Allows for customization of properties, including controlled porosity and tailored mechanical properties. This makes it ideal for specific applications like filters and bearings.
3. Porosity and Customization
- Stainless Steel: Typically non-porous and requires additional processes to create porous materials. Customization is limited to shape and size.
- Sintered Stainless Steel:Can be engineered with controlled porosity, which is advantageous for filtration and other specialized applications. Custom properties can be designed to meet precise requirements.
4. Waste and Efficiency
- Stainless Steel: The traditional manufacturing process can generate significant waste, particularly in machining and shaping operations.
- Sintered Stainless Steel: The powder metallurgy process is more efficient with minimal waste. The material is formed to near-final shapes, reducing the need for additional machining.
5. Cost Considerations
- Stainless Steel:Generally less expensive due to established manufacturing processes and widespread availability. However, costs can increase with complex shapes and machining requirements.
- Sintered Stainless Steel: May have a higher initial cost due to the specialized sintering process and material preparation. However, the reduced waste and ability to produce complex shapes can offset these costs in the long run.
2.2. Applications and Uses
1. Stainless Steel:
Construction: Used for structural components, handrails, and architectural elements.
Automotive: Employed in exhaust systems, engine components, and trim.
Aerospace: Utilized in various structural and engine parts.
Consumer Goods: Found in kitchenware, appliances, and medical instruments.
2. Sintered Stainless Steel:
Filtration: Sintered stainless steel filters, discs, and frits are used in industrial filtration systems due to their controlled porosity and durability.
Bearings: Sintered stainless steel bearings offer high performance in demanding applications with precise requirements.
Complex Parts: Ideal for producing intricate parts and components that are challenging to manufacture using traditional methods.
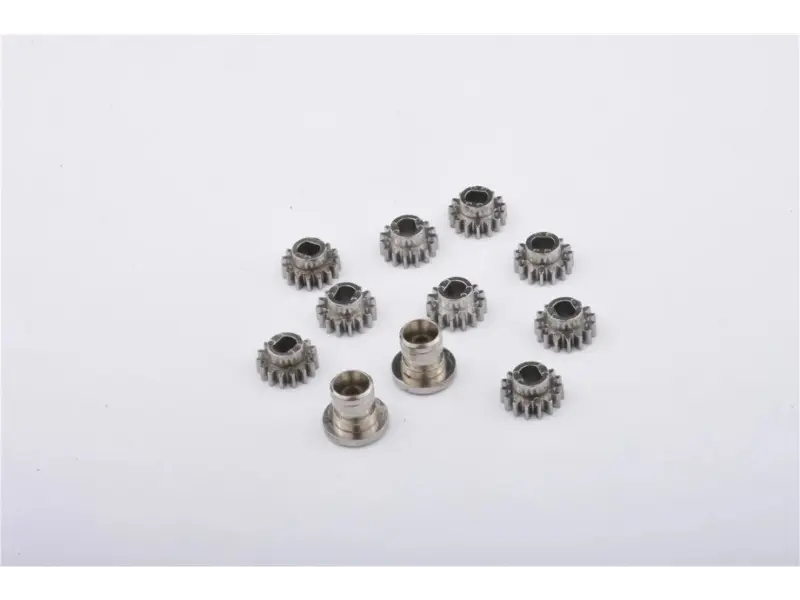
Section 3: Advantages of Sintered Stainless Steel
1. Enhanced Durability
Sintered stainless steel exhibits superior mechanical properties, including increased hardness and resistance to wear. This makes it ideal for demanding applications such as bearings, filters, and structural components.
2. Precision Engineering
The sintering process allows for high precision in the final product, with tight tolerances and consistent quality. This is particularly beneficial in precision engineering, where exact specifications are crucial.
3. Corrosion Resistance
Sintered stainless steel maintains the excellent corrosion resistance inherent to stainless steel, making it suitable for use in harsh environments.
4. Customizable Porosity
For applications like filtration, the ability to control the porosity of sintered stainless steel is a significant advantage. This allows for the production of sintered stainless steel filters, filter discs, and frits with specific filtration capabilities.
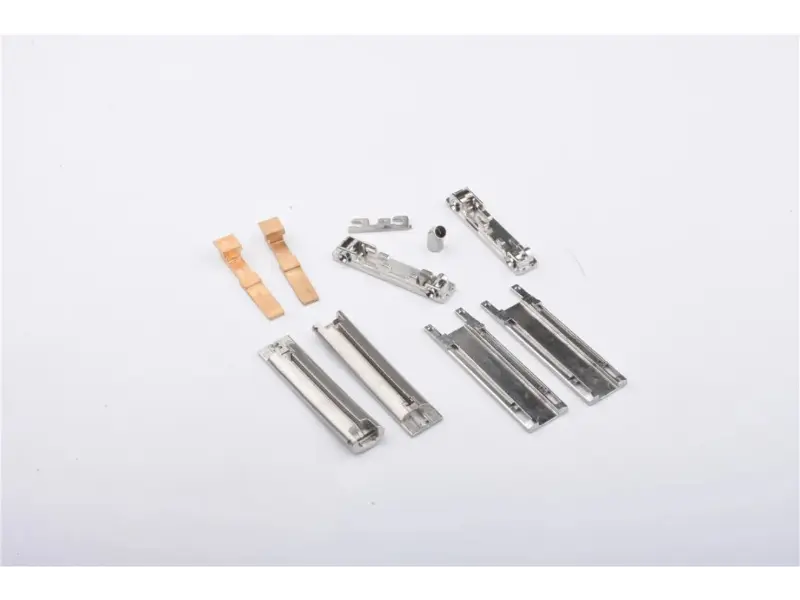
Section 4: Sintered Stainless Steel Products
1. Sintered Stainless Steel Filters
Sintered stainless steel filters are widely used for their high filtration efficiency, strength, and resistance to harsh environments. They are ideal for applications where durability and consistent performance are crucial.
Applications:
- Industrial Filtration: Used in chemical processing, petrochemical, and water treatment industries.
- Automotive: Employed in fuel and oil filtration systems.
- Aerospace: Utilized in hydraulic and fuel filtration systems.
Benefits:
- High Filtration Efficiency: Capable of filtering fine particles and contaminants.
- Durability: Resistant to high temperatures and corrosive environments.
- Customizable: Can be tailored to specific pore sizes and filtration requirements.
2. Sintered Stainless Steel Tubes
Sintered stainless steel tubes are known for their strength, high-temperature resistance, and versatility. They are used in applications requiring robust performance and precision.
Applications:
- Heat Exchangers: Used in systems that require efficient heat transfer and resistance to thermal stress.
- Chemical Processing: Employed in processes that involve aggressive chemicals and high pressures.
- Aerospace: Utilized in components that require lightweight and strong materials.
Benefits:
- Strength and Durability: Capable of withstanding high pressures and temperatures.
- Precision Engineering: Suitable for applications requiring exact dimensions and tolerances.
- Corrosion Resistance: Maintains performance in harsh environments.
3. Sintered Stainless Steel Filter Discs
Sintered stainless steel filter discs are used in filtration systems where high strength and precise filtration are necessary. They are designed to meet specific filtration needs and can be customized based on the application.
Applications:
- Filtration Systems: Used in liquid and gas filtration to separate solids from fluids.
- Industrial Processes: Employed in various manufacturing and processing operations.
- Laboratory Equipment: Utilized in analytical and research applications.
Benefits:
- High Mechanical Strength: Can handle high pressure and flow rates.
- Customizable: Available in various diameters and pore sizes to fit different needs.
- Longevity: Offers long-lasting performance and reliability.
4. Sintered Stainless Steel Sheets and Plates
Sintered stainless steel sheets and plates are used in applications that require high strength and durability. They are often used in structural and industrial applications where precise material properties are needed.
Applications:
- Structural Components: Used in construction and manufacturing where strength and durability are required.
- Industrial Equipment: Employed in machinery and equipment that undergoes significant wear and tear.
- Architectural Applications: Utilized in decorative and functional architectural elements.
Benefits:
- Enhanced Strength: Provides high tensile and impact strength.
- Durability: Resists wear and corrosion in challenging environments.
- Customizable: Can be produced to specific thicknesses and dimensions.
5. Sintered Stainless Steel Mesh
Sintered stainless steel mesh is used in filtration, separation, and screening applications. It offers high strength and stability, even in extreme conditions.
Applications:
- Filtration: Used in industrial and laboratory filtration systems.
- Separation: Employed in processes that require the separation of different materials or phases.
- Screening: Utilized in mining and aggregate industries for sorting and sizing materials.
Benefits:
- Strength and Stability: Maintains integrity under high pressure and temperature.
- Customizable Mesh Sizes: Available in various mesh sizes and configurations.
- Corrosion Resistance: Performs well in aggressive environments.
6. Sintered Stainless Steel Frit
Sintered stainless steel frit is used in applications requiring high porosity and precise filtration. It is often used in the production of filters and separators.
Applications:
- Filtration: Used in high-efficiency filtration systems for liquids and gases.
- Catalysis: Employed in catalytic processes where high surface area and precise porosity are needed.
- Separators: Utilized in separating mixtures in various industrial processes.
Benefits:
- High Porosity: Provides effective filtration and separation.
- Customizable: Can be engineered to specific porosity and size requirements.
- Durability: Resistant to mechanical and chemical stresses.
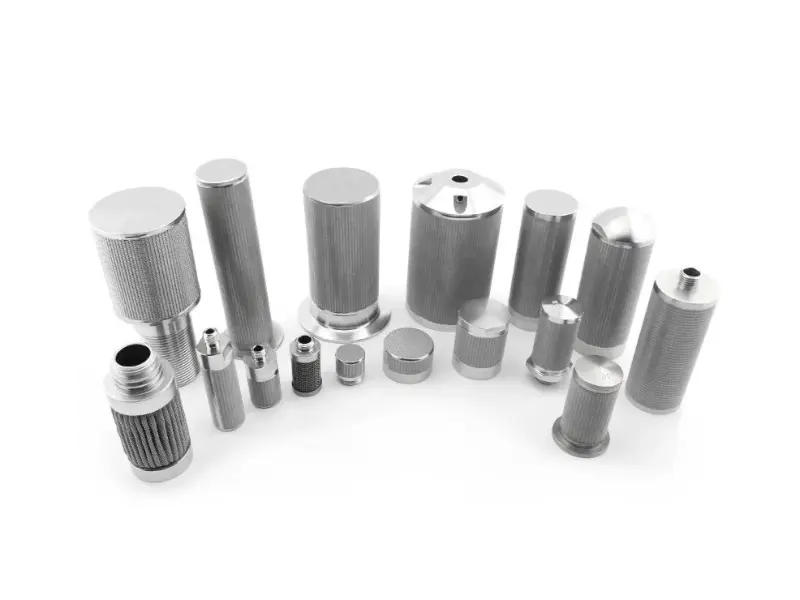
Section 5: Frequently Asked Questions
1. What is Sintered Stainless Steel Made Of?
Sintered stainless steel is made from stainless steel powder that is compacted and heated to form a solid material. The composition of the powder can vary depending on the desired properties of the final product.
2. What is a Sintered Steel?
Sintered steel is steel that has been manufactured using the sintering process, which involves heating powdered steel to form a solid material with specific properties and geometries.
3. Does Sintered Steel Rust?
Sintered steel can rust if it is not made from stainless steel powder or if it is exposed to harsh environments without adequate protection. Sintered stainless steel, however, maintains the corrosion resistance of stainless steel.
4. What are the Advantages of Sintered Metal?
The advantages of sintered metal include enhanced durability, precision engineering, customizable porosity, and efficient material use. These properties make sintered metal an ideal choice for various high-performance applications.
Welleshaft: Your Trusted Supplier for Sintered Stainless Steel
Welleshaft is a global leader in the supply and manufacture of sintered stainless steel products. With years of experience in the industry, we provide high-quality solutions tailored to your specific needs. Whether you require sintered stainless steel filters, tubes, plates, or custom components, Welleshaft offers unparalleled expertise and reliability.
Our state-of-the-art facilities and commitment to excellence ensure that you receive products that meet the highest standards of performance and quality. Partner with Welleshaft to access premium sintered stainless steel solutions that enhance your engineering projects and drive success.
For more information about our sintered stainless steel products and services, visit our website or contact us today. Discover how Welleshaft can support your precision engineering needs with top-tier sintered stainless steel solutions.
Great article! I really appreciate the clear and detailed insights you’ve provided on this topic. It’s always refreshing to read content that breaks things down so well, making it easy for readers to grasp even complex ideas. I also found the practical tips you’ve shared to be very helpful. Looking forward to more informative posts like this! Keep up the good work! YouTube Downloader Online