Sintered Filters: Precision Solutions for Filtration Needs
Sintered filters are essential components in various industries due to their efficiency and reliability in filtering out impurities and contaminants. These filters are created using the sintering process, where metal or other materials are heated to form a porous structure that allows fluids or gases to pass through while trapping particles. This guide provides an overview of sintered filters, including their manufacturing process, benefits, applications, and advantages.
Section 1: What Are Sintered Filters?
Sintered filters are filtration devices made from metal, ceramic, or polymer materials that are processed through sintering. Sintering involves heating powdered materials below their melting point to bond the particles together, creating a porous structure with uniform pore sizes. This structure allows for efficient filtration while maintaining strength and durability.
1. Sintered Filter Working Principle
The working principle of a sintered filter revolves around its porous structure. As fluids or gases pass through the filter, the pores trap unwanted particles while allowing the filtered substance to pass through. This process is highly efficient and can be customized based on the specific filtration needs by adjusting the pore size and material composition.
2. Manufacturing Process
The production of sintered filters typically involves the following steps:
- Material Selection:Choosing the appropriate powder material, such as stainless steel, bronze, or ceramic, based on the desired properties and application.
- Powder Preparation:Preparing the powder by mixing it with additives to improve flow and compaction.
- Compaction:Compressing the powder into molds to form the filter shape. This step creates a “green” filter that is not yet fully bonded.
- Sintering:Heating the green filter in a sintering furnace to a temperature below the melting point of the material. This step bonds the particles together, creating a porous and solid filter.
- Post-Treatment: Applying additional processes such as cleaning, surface finishing, or coating to enhance performance and durability.

Section 2: Types of Sintered Filters
Sintered filters come in various types, each suited to different applications:
1. Metal Sintered Filters
Made from metals such as stainless steel or bronze, these filters are known for their strength, corrosion resistance, and high-temperature tolerance. They are commonly used in applications involving gases and liquids.
2. Ceramic Sintered Filters
Crafted from ceramic materials, these filters offer high thermal stability, chemical resistance, and precise pore sizes. They are ideal for harsh environments and high-temperature applications.
3. Polymer Sintered Filters
Produced from polymer powders, these filters are lightweight and offer good chemical resistance. They are often used in applications requiring flexibility and cost-effectiveness.
4. Sintered Metal Filters
Sintered metal filters are made from materials like stainless steel, bronze, or titanium. These filters are known for their high strength, thermal resistance, and corrosion resistance. They are particularly suitable for applications that require filtering in high-pressure environments or with aggressive chemicals.
5. Sintered Glass Filter
A sintered glass filter is created by sintering glass powder. These filters are widely used in laboratories for chemical filtration due to their chemical inertness and high-temperature resistance. They provide precise filtration, making them ideal for sensitive applications where purity is paramount.
6. Sintered Filter Disc
Sintered filter discs are flat, circular filters used in a variety of applications, from industrial processes to laboratory experiments. These discs can be made from different sintered materials, offering versatility in terms of pore size and filtration efficiency.
7. Stainless Steel Sintered Filter
Stainless steel sintered filters are prized for their durability and ability to withstand harsh environments. They are commonly used in industries such as oil and gas, pharmaceuticals, and food processing, where both strength and hygiene are critical.
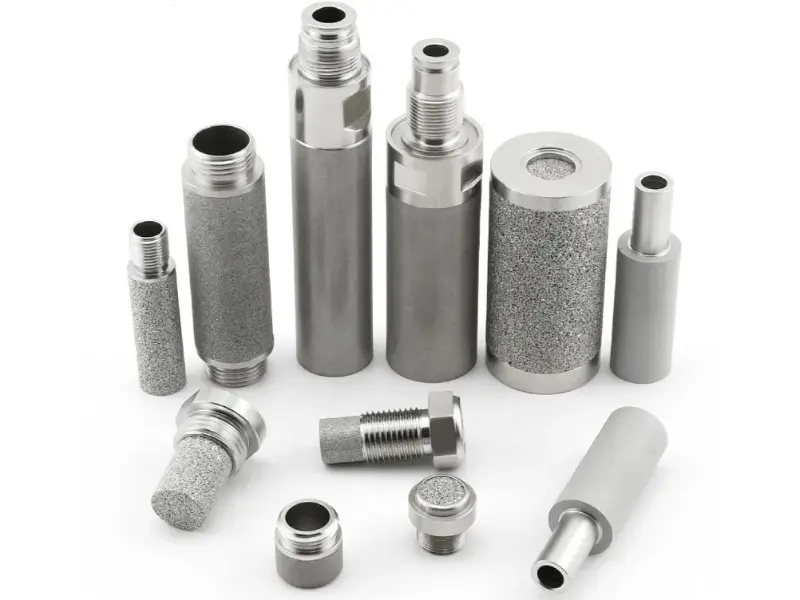
Section 3: Advantages of Sintered Filters
Sintered filters offer several benefits that make them a preferred choice for many filtration applications:
- High Filtration Efficiency: The porous structure of sintered filters provides excellent filtration performance by effectively trapping particles while allowing fluids or gases to pass through.
- Durability and Strength:Sintered filters are strong and durable, capable of withstanding high pressures, temperatures, and aggressive environments.
- Uniform Pore Size: The sintering process ensures consistent pore sizes throughout the filter, resulting in reliable and uniform filtration performance.
- Chemical and Corrosion Resistance:Metal and ceramic sintered filters are resistant to chemical attacks and corrosion, making them suitable for challenging environments.
- Customizable:Sintered filters can be engineered to meet specific filtration requirements, including pore size, material choice, and filter shape.
- Easy Maintenance:Many sintered filters can be cleaned and reused, reducing operational costs and waste.

Section 4: Applications of Sintered Filters
Sintered filters are used in a wide range of industries and applications, including:
- Automotive: In fuel and oil filtration systems to ensure engine performance and longevity.
- Aerospace:For filtration in hydraulic systems and fuel systems, where reliability and performance are critical.
- Industrial:In various processes, such as water treatment, chemical processing, and air filtration, to remove contaminants and ensure product quality.
- Medical:In medical devices and equipment to filter out impurities and ensure the safety and efficacy of medical treatments.
- Electronics:For filtering in electronic components and systems to protect sensitive devices from contaminants.
- Water Treatment:Removing contaminants from water in industrial and municipal water treatment plants.
- Oil and Gas:Filtering impurities from oil, gas, and other hydrocarbons in exploration and refining processes.
- Chemical Processing:Ensuring the purity of chemicals by removing unwanted particles during production.
- Food and Beverage:Maintaining product quality by filtering out solids and other impurities during production.
- Pharmaceuticals: Sterilization and purification processes where contamination must be minimized.
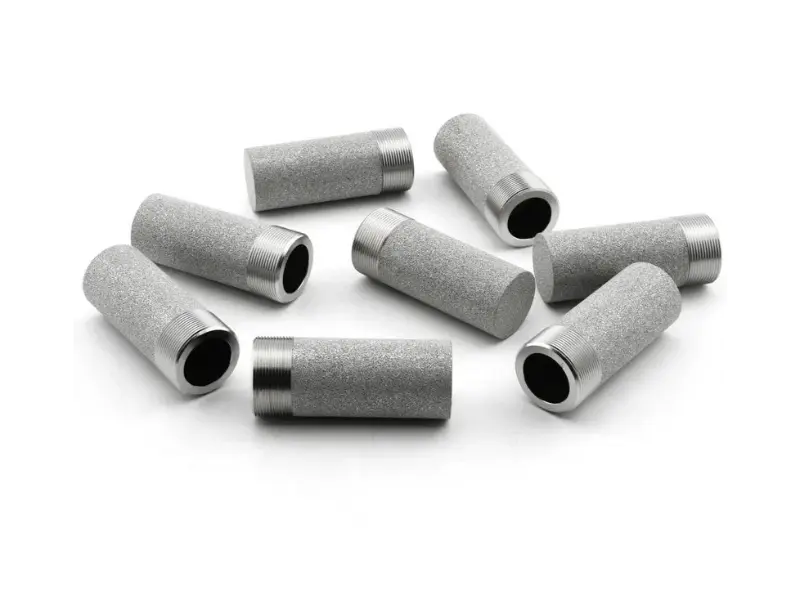
Section 5: Comparing Sintered Filters to Other Filter Types
When comparing sintered filters to other filter types, it’s essential to evaluate their performance, durability, and application suitability. Here’s a breakdown of how sintered filters stack up against other common filter types:
1. Sintered Filters
Material & Construction:
Made from metal powders (e.g., stainless steel, bronze) that are sintered (fused) at high temperatures.
Porous structure with controlled pore size.
Advantages:
- Durability: Extremely robust, resistant to high temperatures and pressures.
- Reusability: Can be cleaned and reused multiple times, reducing long-term costs.
- Precision: Offers precise filtration with uniform pore sizes, ensuring consistent performance.
- Chemical Resistance: Resistant to corrosion and chemical attack, suitable for harsh environments.
- Applications: Used in industries like pharmaceuticals, food & beverage, chemical processing, and gas filtration.
Disadvantages:
- Cost:Higher upfront cost compared to some other filter types.
- Weight: Generally heavier due to metal construction.
- Flow Rate:May have a lower flow rate due to smaller, precise pore sizes.
2. Polymeric Filters
Material & Construction:
Made from synthetic polymers such as polypropylene or nylon.
Available in various configurations like woven, non-woven, or membrane.
Advantages:
- Versatility:Available in various pore sizes and configurations.
- Cost: Relatively low cost and lightweight.
- Chemical Resistance: Good resistance to a broad range of chemicals.
- Applications: Used in water treatment, food processing, and medical applications.
Disadvantages:
- Durability:Not as robust as sintered metal filters; can degrade under extreme conditions.
- Reusability:Often single-use, though some can be cleaned and reused.
- Temperature Tolerance:Limited resistance to high temperatures.
3. Ceramic Filters
Material & Construction:
Made from ceramic materials with a porous structure.
Often used in water filtration systems.
Advantages:
- Durability: Very durable and resistant to chemical attack.
- Filtration Precision: Can filter out very fine particles, including bacteria and viruses.
- Reusability: Can be cleaned and reused multiple times.
- Applications:Common in water filtration, both household and industrial.
Disadvantages:
- Brittleness: Ceramic materials can be brittle and prone to cracking under mechanical stress.
- Flow Rate: Can have a slower flow rate compared to other filters.
- Cost: More expensive than some polymeric or paper filters.
4. Fiberglass Filters
Material & Construction:
Made from glass fibers woven into a mat or mesh.
Common in HVAC systems and industrial air filtration.
Advantages:
- Efficiency:Effective at trapping fine particles in air filtration.
- Durability: Can withstand higher temperatures compared to polymeric filters.
- Cost: Moderately priced with good performance.
- Applications: Used in air filtration, especially in HVAC systems and industrial environments.
Disadvantages:
- Health Concerns: Handling can release fine glass fibers, which can be harmful if inhaled.
- Reusability:Typically single-use and not designed for repeated cleaning.
- Chemical Resistance: Limited resistance to certain chemicals.
5. Activated Carbon Filters
Material & Construction:
Made from carbonaceous materials like coal, coconut shells, or wood, processed to create a porous structure.
Used in both air and water filtration.
Advantages:
- Adsorption Capacity:Excellent at removing odors, chemicals, and volatile organic compounds (VOCs).
- Versatility: Can be combined with other filter types for enhanced filtration.
- Applications:Common in water purification, air purifiers, and gas masks.
Disadvantages:
- Durability:Limited lifespan; needs replacement once saturated with contaminants.
- Flow Rate: Can reduce water or air flow if the filter becomes clogged.
- Cost: Moderate cost with the need for regular replacement.
Conclusion
Sintered filters are a versatile and effective solution for a wide range of filtration needs, offering high efficiency, durability, and customization options. Their ability to withstand harsh conditions and provide reliable performance makes them a valuable choice for industries such as automotive, aerospace, industrial, medical, and electronics.
For high-quality sintered filters and precision-engineered components, Welleshaft is a trusted global supplier and contract manufacturer. With extensive experience in powder metallurgy and advanced sintering technology, Welleshaft delivers reliable solutions tailored to meet diverse filtration requirements. Whether you need sintered metal filters for high-performance applications or customized solutions for specific needs, Welleshaft provides the expertise and quality to support your filtration goals.