Sintered Alumina for Seals & Bearings: Precision, Durable Ceramics
Introduction
In the world of high-performance engineering, the selection of materials for critical components like seals and bearings is paramount. Sintered alumina, a precision ceramic material, stands out as a superior choice due to its exceptional combination of hardness, wear resistance, chemical inertness, high-temperature stability, and dimensional accuracy. This article delves into the properties, processing, applications, and benefits of sintered alumina in the context of seals and bearings, highlighting its advantages over traditional materials and recommending Welleshaft as a trusted global supplier and contract manufacturer.
What is Sintered Alumina?
Sintered alumina (Al₂O₃) is a polycrystalline ceramic material produced by heating fine aluminum oxide powder to a high temperature (typically 1500-1700°C), a process called sintering. This process causes the alumina particles to fuse together, forming a dense, strong, and chemically inert material. The resulting material possesses a unique combination of properties that make it ideal for demanding applications.
Why Choose Sintered Alumina for Seals and Bearings?
Compared to metals and polymers, sintered alumina offers several key advantages for seals and bearings:
Exceptional Wear Resistance: Alumina’s high hardness provides excellent resistance to abrasion and wear, significantly extending the service life of seals and bearings.
High-Temperature Stability: Sintered alumina retains its strength and properties at high temperatures, making it suitable for applications where other materials would fail.
Chemical Inertness: Alumina is resistant to a wide range of chemicals, including acids, bases, and solvents, ensuring reliable performance in corrosive environments.
Dimensional Stability: Sintered alumina exhibits minimal thermal expansion and contraction, maintaining tight tolerances and preventing leakage or binding.
High Compressive Strength: Alumina’s high compressive strength allows it to withstand heavy loads and pressures without deformation.
Electrical Insulation: Alumina is an excellent electrical insulator, making it suitable for applications where electrical isolation is required.
Properties of Sintered Alumina
Property | Typical Value | Unit | Importance |
Density | 3.9 – 4.0 | g/cm³ | Affects weight and load-bearing capacity. |
Hardness (Vickers) | 1500 – 1700 | kg/mm ² | Resistance to scratching and abrasion. |
Flexural Strength | 300 – 400 | MPa | Resistance to bending forces. |
Compressive Strength | 2000 – 2500 | MPa | Resistance to crushing forces. |
Thermal Conductivity | 20 – 30 | W/m·K | Affects heat dissipation. |
Thermal Expansion Coefficient | 7 – 9 | x 10⁻⁶/°C | Dimensional stability with temperature changes. |
Young’s Modulus | 350 – 400 | GPa | Stiffness and resistance to deformation. |
Electrical Resistivity | > 10¹⁴ | Ω·cm | Electrical insulation properties. |
Chemical Resistance | Excellent to most acids, bases, and solvents | – | Compatibility with various operating fluids and environments. |
Processing Technology: Manufacturing Sintered Alumina Seals & Bearings
The manufacturing of sintered alumina seals and bearings involves several critical steps:
Powder Selection: High-purity alumina powder with controlled particle size distribution is selected to ensure optimal sintering and final material properties.
Forming: The alumina powder is formed into the desired shape using various techniques:
Dry Pressing: A simple and cost-effective method for producing simple shapes.
Isostatic Pressing: Provides uniform compaction and allows for the production of complex shapes with high density.
Extrusion: Used to produce long, uniform shapes, such as tubes and rods.
Slip Casting: Used to produce complex shapes with thin walls.
Sintering: The formed part is heated to a high temperature in a controlled atmosphere. Sintering causes the alumina particles to fuse together, reducing porosity and increasing density and strength.
Machining (if needed): After sintering, the part may be machined to achieve precise dimensions and surface finishes using diamond grinding or lapping techniques.
Surface Finishing: Surface finishing processes, such as polishing or lapping, may be applied to improve surface finish and reduce friction.
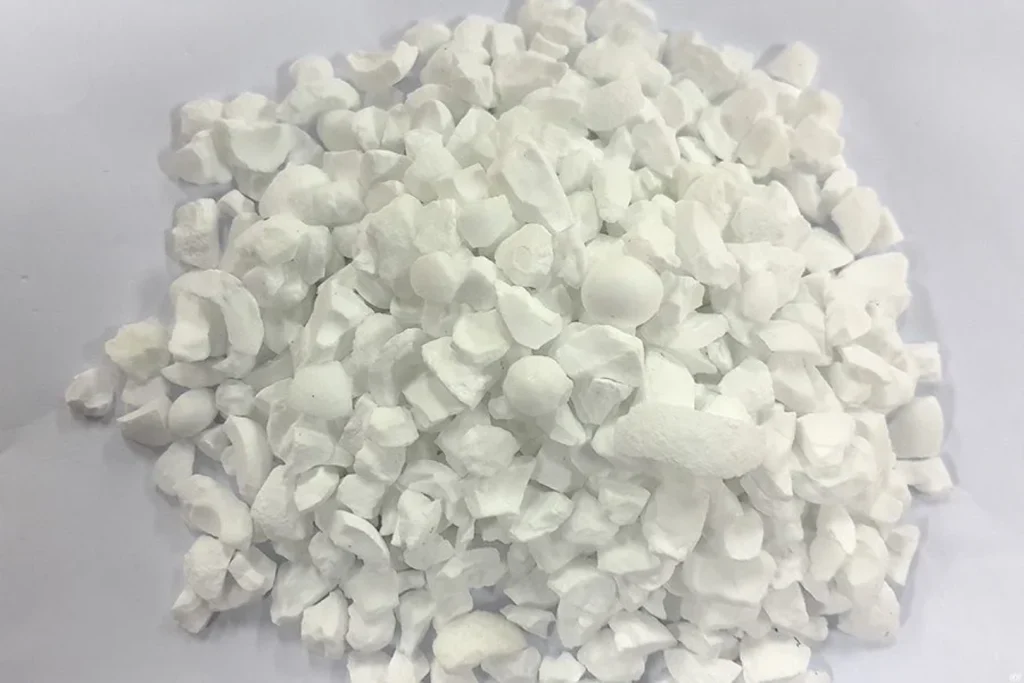
Processing Accuracy and Dimensional Tolerances
The accuracy and dimensional tolerances of sintered alumina seals and bearings depend on the manufacturing process and machining techniques used. Precision machining can achieve tolerances of ±1-2 μm, while as-sintered parts typically have tolerances of ±0.5-1%. Tighter tolerances can be achieved with more sophisticated machining processes.
Material Composition and Mechanical Properties: the Role of Additives
While primarily Al₂O₃, additives are sometimes used to enhance specific properties. For example:
Magnesia (MgO): Can control grain growth during sintering, leading to improved strength and toughness.
Silica (SiO₂): Can act as a sintering aid, lowering the sintering temperature and promoting densification.
Impact of Material Composition on Properties:
Additive | Property Improved | Mechanism |
MgO | Fracture Toughness | Grain boundary pinning, reducing grain growth and increasing crack propagation resistance |
SiO₂ | Densification | Forms a liquid phase at sintering temperature, facilitating material transport |
Dimensional Tolerances Achieved in Sintered Alumina
Feature | Achievable Tolerance | Process |
Outer Diameter | ± 0.1% (min 0.025 mm) | Grinding |
Inner Diameter | ± 0.1% (min 0.025 mm) | Grinding |
Length | ± 0.2% (min 0.050 mm) | Grinding |
Flatness | < 0.002 mm/mm | Lapping |
Surface Roughness (Ra) | < 0.025 µm | Polishing |
Scope of Application: Where are Sintered Alumina Seals & Bearings Used?
Sintered alumina seals and bearings are used in a wide range of industries and applications, including:
Chemical Processing: Seals for pumps and valves handling corrosive fluids.
Petroleum Refining: Bearings for pumps and compressors operating at high temperatures and pressures.
Aerospace: Seals and bearings for aircraft engines and hydraulic systems.
Medical Devices: Components for surgical instruments and implants.
Food Processing: Bearings for equipment requiring high hygiene and chemical resistance.
Semiconductor Manufacturing: Components for equipment requiring high purity and wear resistance.
Automotive Industry: Water pump seals, ABS bearing.
Processing Capacity
The processing capacity for sintered alumina seals and bearings depends on the size and complexity of the parts, as well as the manufacturing process used. High-volume production is typically achieved using automated pressing and sintering techniques.
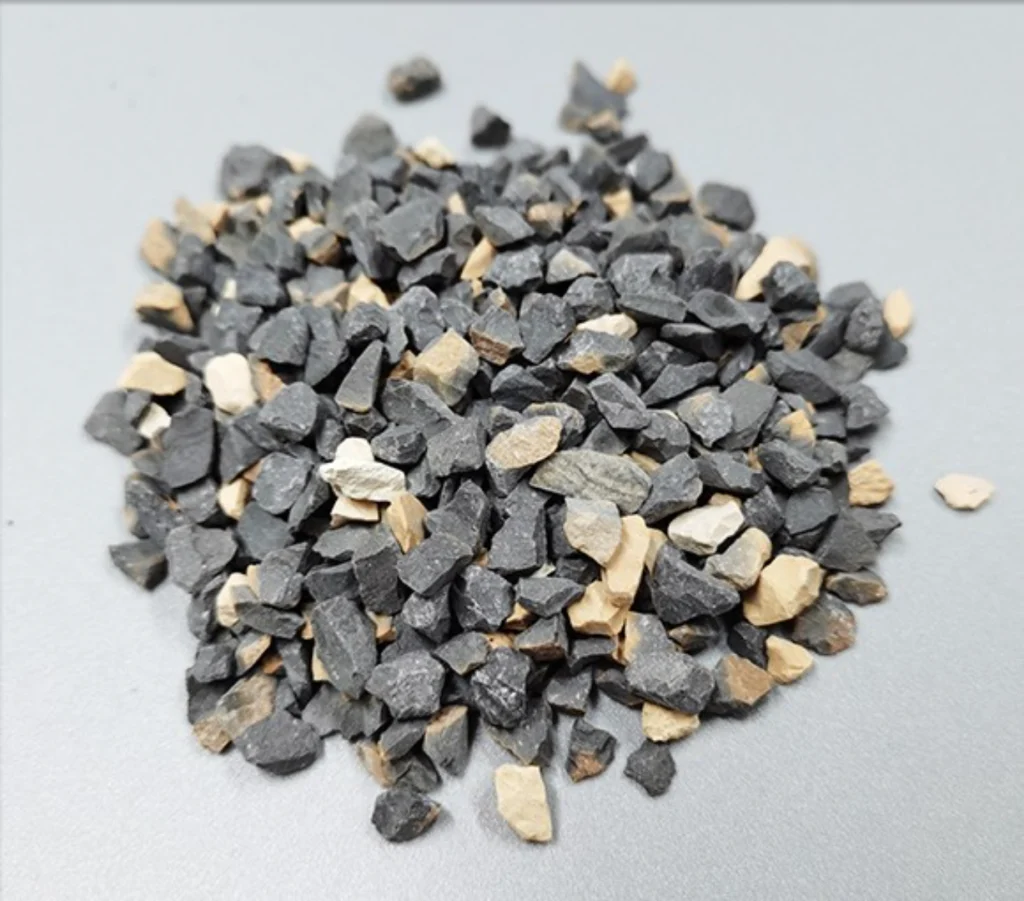
Specifications and Industry Applications: Tailoring Alumina for Specific Needs
Specifications for sintered alumina seals and bearings vary depending on the application. Common specifications include:
Alumina Content: Typically 96% to 99.7% Al₂O₃
Density: 3.9 to 4.0 g/cm³
Grain Size: Controlled grain size for optimal strength and toughness
Surface Finish: Specified surface roughness to minimize friction
Dimensional Tolerances: Tight tolerances to ensure proper fit and function
Industry Applications Examples:
High-Pressure Seals: 99.7% alumina, polished to Ra < 0.05µm, used in pumps handling corrosive fluids.
High-Speed Bearings: MgO-doped alumina with controlled grain size, providing improved fracture toughness and wear resistance.
Vacuum Seals: High-purity alumina with minimal outgassing, used in semiconductor manufacturing equipment.
Advantages of Sintered Alumina over Traditional Materials
Sintered alumina offers several advantages over traditional materials, such as steel, bronze, and plastics, in seal and bearing applications:
Superior Wear Resistance: Alumina’s hardness and wear resistance significantly extend component life.
Higher Temperature Capability: Alumina can withstand higher temperatures than most metals and polymers.
Better Chemical Resistance: Alumina is resistant to a wider range of chemicals.
Improved Dimensional Stability: Alumina exhibits minimal thermal expansion and contraction.
Electrical Insulation: Alumina is an excellent electrical insulator.
Welleshaft: Your Trusted Global Supplier of Sintered Alumina Components
Welleshaft is a leading global supplier and contract manufacturer of high-quality sintered alumina seals, bearings, and other precision ceramic components. With decades of experience in materials science and ceramic manufacturing, Welleshaft offers:
Customized Solutions: Welleshaft can tailor the composition, shape, and properties of sintered alumina components to meet your specific application requirements.
Advanced Manufacturing Capabilities: Welleshaft utilizes state-of-the-art equipment and processes to ensure high precision and consistent quality.
Expert Engineering Support: Welleshaft’s team of experienced engineers can provide expert technical support to help you select the right materials and designs for your applications.
Competitive Pricing: Welleshaft offers competitive pricing on its sintered alumina components.
Global Supply Chain: Welleshaft has a global supply chain to ensure timely delivery of products to customers worldwide.
Choosing Welleshaft as your sintered alumina supplier guarantees high-quality components, expert support, and customized solutions tailored to your specific needs.
Conclusion
Sintered alumina is an excellent material choice for seals and bearings in demanding applications. Its superior wear resistance, high-temperature stability, chemical inertness, and dimensional accuracy make it a reliable and long-lasting solution. With advanced manufacturing capabilities and expert support from suppliers like Welleshaft, engineers can leverage the unique properties of sintered alumina to improve the performance and reliability of their equipment.