Silicon Nitride Ceramic Processing: Optimizing Grain Size & Microstructure
Silicon nitride (Si3N4) ceramics have emerged as a high-performance material in numerous industries due to their exceptional combination of properties. They possess high strength and hardness, excellent wear and corrosion resistance, low thermal expansion, and good thermal shock resistance. The performance of silicon nitride ceramics is greatly influenced by their microstructure, especially the grain size and shape, which are directly controlled by the processing methods. This article explores the key stages in silicon nitride ceramic processing, focusing on optimizing grain size and microstructure to achieve superior material properties.
Section 1 Introduction to Silicon Nitride Ceramics
Silicon nitride, a covalently bonded ceramic, has gained significant traction in applications requiring high-performance materials. Its inherent properties make it suitable for extreme conditions, including high temperatures, harsh environments, and high-stress situations. From cutting tools and bearings to engine components and biomedical devices, silicon nitride’s versatility makes it a sought-after material. However, the processing of silicon nitride poses several challenges because it is a covalently bonded material. Controlling the process to yield materials with the desirable microstructure and properties requires a thorough understanding of each processing stage.
Section 2 The Significance of Grain Size and Microstructure
The microstructure of a ceramic material, including grain size, shape, and grain boundary characteristics, plays a pivotal role in determining its mechanical, thermal, and electrical properties. In silicon nitride ceramics, controlling these factors is especially critical.
2.1 Grain Size: Smaller grain sizes typically lead to increased strength and toughness due to the increased number of grain boundaries that impede crack propagation. However, extremely fine grain structures can sometimes exhibit reduced high-temperature creep resistance.
2.2 Grain Shape and Morphology: The aspect ratio (length-to-width ratio) and orientation of grains can influence the fracture toughness and overall mechanical behavior of the material. Rod-like or elongated grains often enhance fracture resistance.
2.3 Grain Boundaries: The composition and structure of grain boundaries affect the material’s diffusion behavior and high-temperature stability. Controlled grain boundaries are essential to prevent unwanted grain growth at elevated temperatures.
2.4 Phase Distribution: The distribution of different phases (such as alpha and beta silicon nitride, sintering aids, or secondary phases) within the microstructure can impact the overall performance characteristics, including strength, fracture toughness, and creep resistance.
Section 3 Key Stages in Silicon Nitride Ceramic Processing
The manufacturing process of silicon nitride ceramics involves several critical stages, each impacting the final properties of the material:
3.1 Powder Preparation
The starting point of any ceramic process is the production of a high-quality powder. Silicon nitride powder can be synthesized through different techniques, such as:
3.1.1 Direct Nitridation: This method involves reacting silicon powder directly with nitrogen gas at elevated temperatures.
3.1.2 Carbothermal Reduction: Silicon dioxide is reduced using carbon at high temperatures in the presence of nitrogen.
3.1.3 Chemical Vapor Deposition (CVD): Gaseous precursors are used to deposit silicon nitride onto a substrate.
3.1.4 Solution-based Synthesis: Precipitating silicon nitride particles from a solution.
Powder characteristics are critical in determining the quality of the final product. Critical attributes of the powder include particle size, morphology, purity, and specific surface area. These features affect powder packing, particle interactions, and ultimately, the densification and microstructural evolution during sintering. The raw powder often contains additives that act as sintering aids. These additives help to form a liquid phase during sintering, promoting densification and controlling grain growth.
3.2 Powder Forming
The powder is then formed into a desired shape using several techniques:
3.2.1 Dry Pressing: This involves compressing the powder in a die using high pressure. It is suitable for simple shapes with uniform thickness.
3.2.2 Isostatic Pressing: Pressure is applied uniformly from all directions, resulting in more uniform density.
3.2.3 Injection Molding: Used for complex shapes, the powder is mixed with a binder and then injected into a mold.
3.2.4 Slip Casting: A slurry of powder in a liquid is poured into a porous mold, allowing the liquid to be absorbed and the powder to form the desired shape.
3.2.5 Extrusion: The plasticized powder is forced through a die to produce shapes such as rods and tubes.
The choice of forming method depends on the shape complexity, production volume, and desired material properties.
3.3 Sintering
Sintering is a critical stage in the processing of silicon nitride ceramics. It involves heating the formed part to high temperatures to consolidate the powder particles into a dense solid. Unlike sintering other ceramics, it cannot be sintered without additives to aid the process because of its inherent bonding nature. The most common methods for sintering silicon nitride include:
3.3.1 Pressureless Sintering: Heating the compact to high temperatures (1700-1850 °C) in an inert atmosphere. Sintering aids like oxides of Y, Al, Mg, or rare earths are typically used to promote densification. These oxides help form a liquid phase which facilitates mass transport and densification.
3.3.2 Gas Pressure Sintering: Sintering under controlled atmosphere and increased pressure, typically nitrogen. This method enhances densification and promotes better control over microstructural development.
3.3.3 Hot Pressing: A combination of high temperature and pressure. This is effective for achieving fully dense parts but is not suited to producing complex parts.
3.3.4 Spark Plasma Sintering (SPS): Utilizing a pulsed electric current for rapid heating and sintering, resulting in enhanced densification and refined microstructure.
Controlling the sintering cycle, including heating and cooling rates, is crucial to achieving the desired grain size and shape. The liquid phase during sintering facilitates grain growth. Additives are selected and used to also control this process. Fine-grained microstructures are generally preferred as they improve material properties.
3.4 Post-Sintering Treatment
After sintering, the ceramic parts may undergo post-sintering treatment to further refine their properties:
3.4.1 Machining: Precision machining to achieve final dimensional tolerances and surface finish using diamond tooling.
3.4.2 Heat Treatment: Annealing or other thermal treatments to modify residual stresses and microstructure.
3.4.3 Surface Treatments: Coating, grinding, or polishing to improve surface finish and resistance.
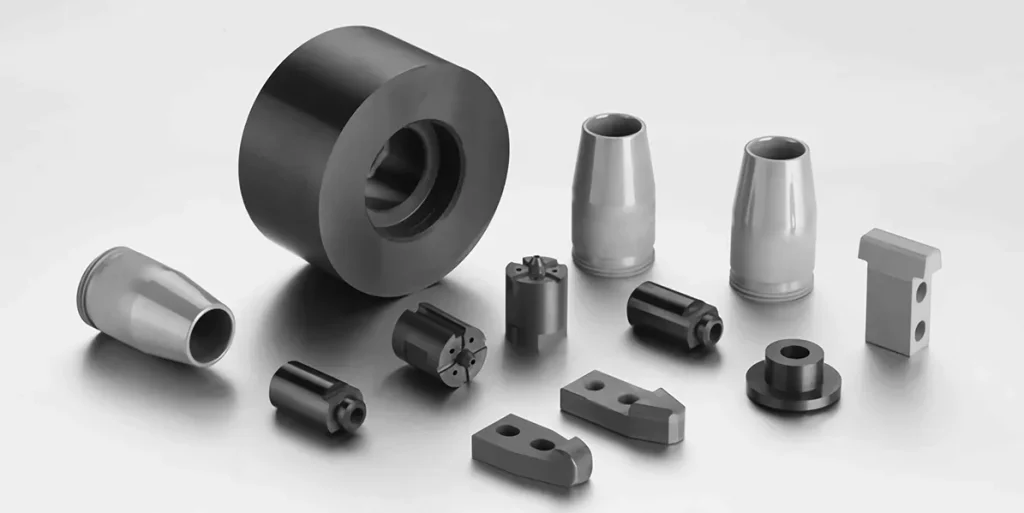
Section 4 Optimizing Grain Size and Microstructure
The final performance of silicon nitride ceramics is determined by their microstructure. By controlling processing parameters, microstructures with optimum properties can be achieved.
4.1 Sintering Additives: Careful selection of additives controls grain growth by either promoting or inhibiting it. The quantity and composition of sintering aids can influence the formation of a liquid phase, which affects densification and grain growth.
4.2 Temperature and Pressure Control: Precise control over sintering temperature and pressure is critical for promoting densification and limiting excessive grain growth. Hot pressing and gas pressure sintering have advantages as they ensure densification while also having more control over the microstructure.
4.3 Nucleation and Grain Growth Control: Control the process to encourage nucleation to yield smaller more uniform grain structures. Control the sintering process parameters to minimize grain growth as necessary.
4.4 Post-Sintering Annealing: Heat treatments can help reduce residual stresses and refine the microstructure by reducing defects and grain size.
Section 5 Material Properties and Applications
The properties of silicon nitride ceramics make them indispensable in several applications, including:
5.1 Aerospace: High-temperature components, gas turbine blades, and bearings for aerospace engines.
5.2 Automotive: Engine components, wear parts, and bearings.
5.3 Biomedical: Joint replacements, dental implants, and medical instrument components.
5.4 Electronics: Insulators and substrates.
5.5 Cutting Tools: High-speed cutting tools for machining.
5.6 Chemical Industry: Nozzles, seals, and other wear-resistant components in harsh environments.
Section 6 Quality Detection Methods
Ensuring the quality of silicon nitride ceramics requires thorough testing and inspection:
6.1 Density Measurement: To verify complete densification after sintering.
6.2 Microscopy: Scanning electron microscopy (SEM) and transmission electron microscopy (TEM) to evaluate grain size, shape, and microstructure.
6.3 X-Ray Diffraction (XRD): Used to analyze phase composition and crystalline structure.
6.4 Mechanical Testing: Bending tests to determine fracture strength and toughness.
6.5 Non-destructive testing (NDT): Ultrasonic testing and eddy current testing to detect flaws.
Sheet Table of Silicon Nitride Ceramic Processing
Category | Description |
Type | Silicon nitride (Si3N4) – covalent ceramic. |
Processing Technology | Powder preparation, powder forming, sintering, post-sintering treatment. |
Powder Forming | Dry pressing, isostatic pressing, injection molding, slip casting, extrusion. |
Sintering | Pressureless sintering, gas pressure sintering, hot pressing, spark plasma sintering (SPS). |
Material Properties | High strength, high hardness, excellent wear and corrosion resistance, low thermal expansion, good thermal shock resistance. |
Quality Detection Methods | Density measurement, microscopy (SEM, TEM), x-ray diffraction (XRD), mechanical testing, non-destructive testing (NDT). |
Application Field | Aerospace, automotive, biomedical, electronics, cutting tools, chemical industry. |
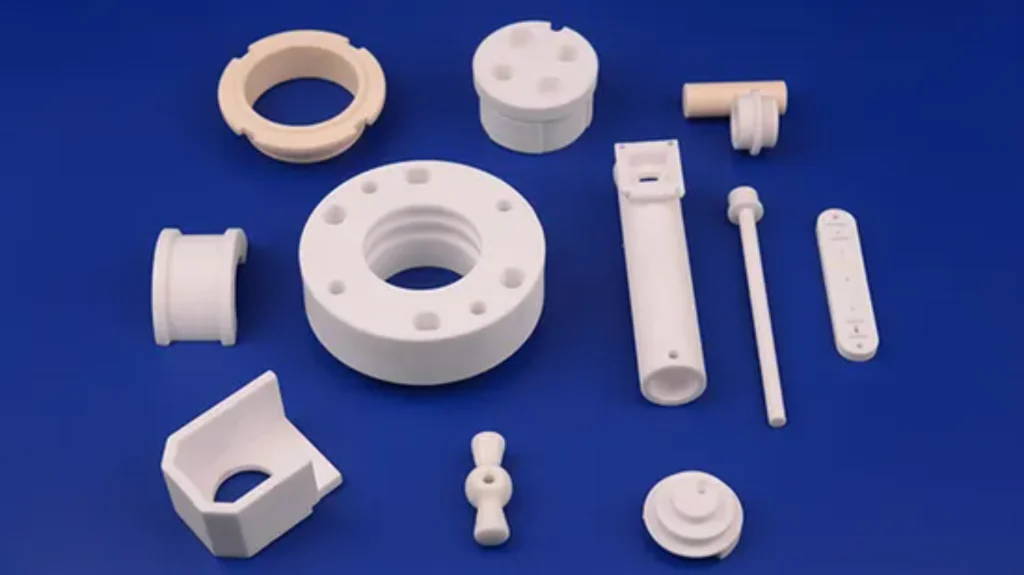
Section 7 The Relationship between Microstructure and Performance
The table below summarizes the general impact of microstructure parameters on key properties of silicon nitride ceramics:
Sheet Table: Microstructure Influence on Silicon Nitride Properties
Microstructure Parameter | Impact on Strength | Impact on Toughness | Impact on Thermal Shock Resistance | Impact on Wear Resistance | Impact on Creep Resistance |
Smaller Grain Size | Increased | Increased | Increased | Increased | Decreased |
Larger Grain Size | Decreased | Decreased | Decreased | Decreased | Increased |
Elongated Grains | Moderate Increase | Increased | Increased | Increased | Moderate Increase |
Equiaxed Grains | Moderate Decrease | Decreased | Decreased | Decreased | Moderate Decrease |
Controlled Grain Boundaries | Increased Strength | Increased | Increased | Increased | Increased |
Porosity | Decreased | Decreased | Decreased | Decreased | Decreased |
Note: This is a generalized view, specific results may vary
Section 8 Advanced Characterization Techniques
To understand and control the microstructure, advanced characterization methods are necessary. These include:
8.1 Scanning Electron Microscopy (SEM): For imaging grain size, shape, and porosity.
8.2 Transmission Electron Microscopy (TEM): For higher resolution imaging of grain boundaries.
8.3 X-ray Diffraction (XRD): For phase analysis and grain orientation.
8.4 Atomic Force Microscopy (AFM): For surface topography analysis.
Section 9 Why Choose Wellshaft?
Wellshaft stands out as a trusted global supplier and contract manufacturer of high-quality silicon nitride ceramics. With years of expertise and a strong commitment to innovation, Wellshaft offers:
9.1 Custom Material Solutions: Tailoring silicon nitride ceramic properties to specific application needs.
9.2 Advanced Manufacturing Capabilities: Employing state-of-the-art equipment and techniques for precise and consistent production.
9.3 Rigorous Quality Control: Comprehensive testing to ensure the highest quality and reliability.
9.4 Expert Technical Support: Providing engineering expertise and guidance throughout the development process.
9.5 Global Supply Chain: Reliable delivery to meet customer demands worldwide.
Wellshaft offers a range of silicon nitride materials with varying grain size and purity for a wide range of applications. Their state of the art manufacturing capabilities can help bring your designs to life.
Conclusion
The processing of silicon nitride ceramics is a complex and precise process that greatly influences the final properties of the material. Optimizing grain size and microstructure through careful control of each stage, from powder preparation to sintering, is essential for achieving superior material performance. With advanced processing techniques and ongoing research, silicon nitride ceramics will continue to play a vital role in numerous industries. When selecting a partner for your silicon nitride needs, consider Wellshaft for their commitment to quality, innovation, and customer satisfaction. They are a trusted provider of precision manufacturing of silicon nitride components.