Salt Bath Nitriding Services: Improve Metal Hardness & Wear Resistance
Section 1 Introduction
In today’s demanding manufacturing landscape, the performance and longevity of metal components are paramount. Achieving superior surface properties, like enhanced hardness and wear resistance, is crucial for extending the lifespan of critical parts and ensuring optimal functionality. One effective solution for achieving these results is salt bath nitriding, a thermochemical process that significantly improves the characteristics of metal surfaces. At [Your Company or “a leading provider”], we offer expert salt bath nitriding services designed to meet a wide range of industrial needs, ensuring that your components can withstand even the harshest operating environments. In this comprehensive guide, we’ll delve into the process, benefits, and applications of salt bath nitriding, and why choosing the right service provider, like Wellshaft, is crucial.
Section 2 What is Salt Bath Nitriding?
Salt bath nitriding is a surface hardening process where metal components are immersed in a molten salt bath at a specific temperature. This bath typically contains nitrogen-bearing compounds which, at high temperatures, release nitrogen into the surface of the metal. Sometimes carbon-containing compounds are added to the mix, leading to the process of nitrocarburizing. During the process, nitrogen atoms diffuse into the surface of the metal, forming a hard, wear-resistant compound layer. Unlike some other surface hardening treatments, the low temperature of salt bath nitriding minimizes deformation of the work piece, allowing for high-precision hardening.
The process is highly controlled, and it allows for a uniform layer to be formed. The depth of the hardened layer and the surface properties can be precisely tuned by adjusting the temperature and duration of the treatment.
The Process Explained:
The process begins by thoroughly cleaning the metal components to remove any contaminants. These clean components are then immersed into the molten salt bath with carefully controlled composition and temperature. The immersion time and other parameters are determined by the alloy of the part being treated and the required case depth of hardness. Following immersion, the parts are removed from the molten salt bath and allowed to cool. Additional post-treatment steps like quenching or polishing may be performed, depending on the component’s end-use requirements.
Section 3 How the Salt Bath Nitriding Process Works:
The process typically involves several key steps:
3.1 Cleaning: The metal components are thoroughly cleaned to remove any dirt, oil, or other surface contaminants that could impede the nitriding process.
3.2 Preheating: In some cases, the parts may be preheated to reduce thermal shock when they are immersed in the molten salt bath.
3.3 Immersion: The components are submerged in the molten salt bath. The bath temperature, salt composition, and immersion time are carefully controlled, and can vary based on the material being treated, the required case depth of hardness, and other parameters.
3.4 Diffusion: The nitrogen atoms are released at the surface, and diffuse into the metal to form a hard nitride layer. If also a nitrocarburizing process, carbon will also diffuse into the surface, forming carbides.
3.5 Cooling: After the specified treatment time, the components are removed from the bath and allowed to cool. The cooling process is carefully controlled to prevent cracking and ensure uniform hardness.
3.6 Quenching: Some processes require quenching, which may be done in oil, water, or air, depending on specific material and property requirements.
3.7 Post-Treatment: Depending on the application requirements, further post-treatment may be necessary. This may involve polishing or other processes to obtain the optimal final surface.
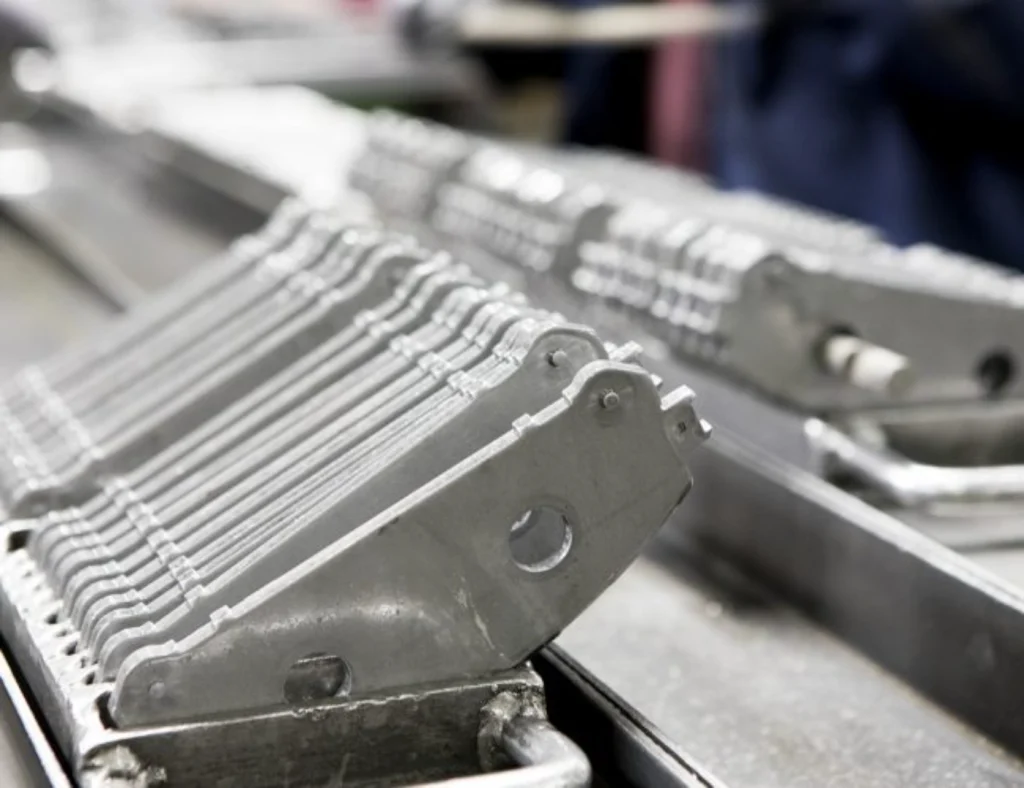
Section 4 Key Benefits of Salt Bath Nitriding
4.1 Enhanced Hardness: The surface hardness of treated parts significantly increases, leading to higher resistance to deformation and mechanical stress.
4.2 Improved Wear Resistance: Salt bath nitriding creates a hard, durable layer that protects against wear, abrasion, and friction, extending the service life of components.
4.3 Increased Fatigue Strength: The process enhances the fatigue strength of the material, enabling it to withstand cyclic loading and stress.
4.4 Corrosion Resistance: While not its primary purpose, salt bath nitriding can contribute to increased corrosion resistance in some applications by forming a nitride layer on the surface.
4.5 Minimal Distortion: The relatively low temperature of the process minimizes deformation, allowing for precision hardening of close-tolerance parts.
4.6 Versatility: The process is applicable to a broad range of ferrous materials, including steels, cast irons, and even some stainless steels.
4.7 Cost-Effectiveness: Salt bath nitriding can be a cost-effective alternative to other hardening processes, particularly in volume production.
Section 5 Applications of Salt Bath Nitriding
The versatility of salt bath nitriding makes it suitable for numerous applications across various industries:
5.1 Automotive: Gears, shafts, engine components, brake parts, and other wear-sensitive parts.
5.2 Aerospace: Landing gear components, critical engine parts, and structural components.
5.3 Tool and Die: Forming tools, punches, dies, and cutting tools.
5.4 Manufacturing: Machine parts, gears, bearings, and fasteners.
5.5 Oil and Gas: Downhole tools, valves, and pipelines.
5.6 Agriculture: Tractor parts, harvester components, and tillage tools.
5.7 Firearms: Firearm components requiring increased hardness and wear resistance.
5.8 Textile Machinery: Components exposed to high wear conditions
Section 6 Related Information Table
Feature |
Description |
Process Temperature |
Typically 500-650°C (932-1202°F), lower than many other hardening processes, thus reducing the risk of distortion. |
Treatment Time |
Varies from minutes to several hours, depending on the desired case depth and material. |
Materials |
Primarily ferrous materials, including carbon steels, alloy steels, stainless steels, and cast irons. Some non-ferrous alloys can be treated under modified process parameters. |
Layer Thickness |
Typically ranges from a few microns to tens of microns, depending on the application requirements. |
Hardness Increase |
Can significantly increase surface hardness, often reaching 50-80 HRC, and in some cases even higher. |
Process Variants |
Includes Liquid Ferritic Nitrocarburizing (LFNC) which utilizes carbon addition, Molten Salt Surface Hardening, Liquid Immersion Nitriding, and others. Salt baths are commonly of alkali cyanides and cyanates (in older baths), carbonates, and nitrates. |
Post-Treatment |
Some processes require post-treatment, such as quenching or polishing, depending on the specific application. |
Common Alternatives |
Carburizing, gas nitriding, plasma nitriding. |
Section 7 Why Choose Salt Bath Nitriding Services?
Choosing the right surface treatment is critical for the performance and longevity of your components. Here’s why you should consider salt bath nitriding services:
7.1 Superior Performance: Provides a hard, wear-resistant layer, significantly extending the service life of components.
7.2 Precision Control: Our state-of-the-art equipment and experienced technicians ensure precise control of the treatment parameters for consistent and reliable results.
7.3 Cost-Effective: Often more cost-effective than alternative treatments, especially for high-volume production.
7.4 Versatility: Suitable for a wide variety of materials and applications.
7.5 Reduced Distortion: The low-temperature process minimizes the risk of distortion, maintaining the dimensional integrity of your components.
7.6 Environmentally Friendly: Modern salt bath processes are designed to be environmentally responsible, minimizing waste and emissions.
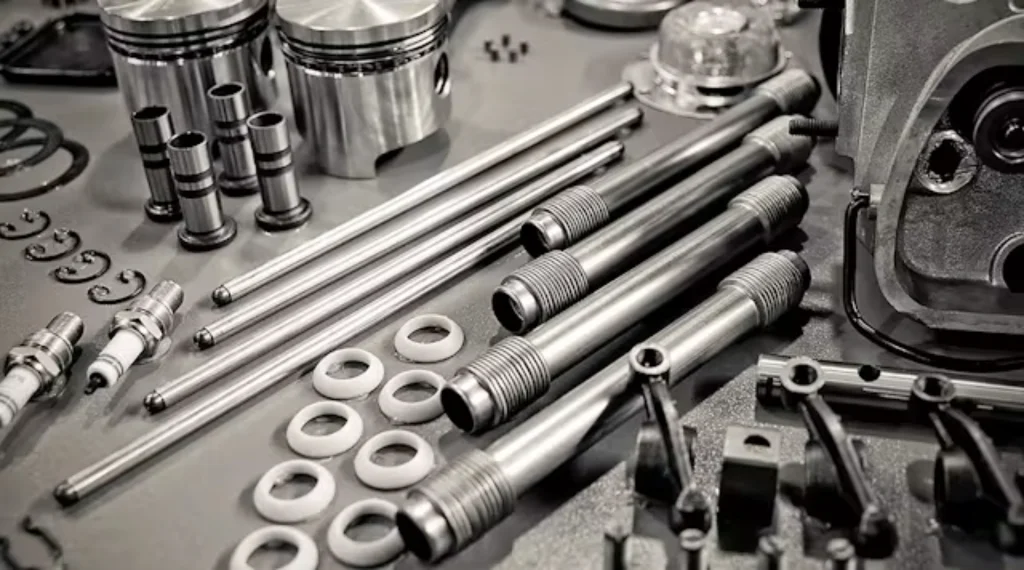
Section 8 Choosing a Trusted Salt Bath Nitriding Services Provider
The quality of salt bath nitriding services is significantly influenced by the service provider’s expertise, technology, and quality control procedures. Working with a reputable supplier is essential for ensuring you get the maximum benefit from this treatment. Here are a few factors to keep in mind:
8.1 Experience and Expertise: Look for a provider with years of experience in the industry and a proven track record of success.
8.2 Technology and Equipment: The service provider should use state-of-the-art equipment and have robust quality control processes in place.
8.3 Customization: The provider should offer customized solutions to meet your specific needs.
8.4 Customer Service: Choose a partner that offers excellent customer service and is willing to work with you to achieve the desired results.
8.5 Certifications: If applicable, look for certifications, which can help ensure the quality and reliability of the process.
Section 9 Wellshaft: Your Trusted Global Partner in Surface Treatment
When it comes to reliable and high-quality surface treatments, Wellshaft stands out as a global leader. With years of experience and a dedication to excellence, Wellshaft offers exceptional salt bath nitriding services to meet the most demanding requirements. Here’s what sets Wellshaft apart:
9.1 Global Reach: As a leading contract manufacturer and supplier, Wellshaft has the reach and capacity to serve clients across the globe.
9.2 Advanced Technology: Wellshaft utilizes cutting-edge technology and follows industry-leading processes to ensure the highest quality surface treatments.
9.3 Expert Team: The team at Wellshaft consists of highly skilled engineers and technicians with vast experience in salt bath nitriding and related surface treatment processes.
9.4 Customized Solutions: Wellshaft understands that each application is unique and offers customized solutions to meet your specific requirements.
9.5 Commitment to Quality: Wellshaft is dedicated to the highest standards of quality and performance, with stringent quality control measures in place.
9.6 Comprehensive Services: In addition to salt bath nitriding, Wellshaft also offers a wide range of other surface treatments, making them a one-stop shop for all your surface modification needs.
By choosing Wellshaft, you’re not just selecting a service provider, you are partnering with a team that is committed to helping you achieve exceptional results and a lasting competitive advantage.
Conclusion
Salt bath nitriding is a highly effective surface treatment method that provides superior hardness, wear resistance, and fatigue strength, making it essential for many critical components. When choosing a provider for your surface treatment needs, choose a company that is reliable and trustworthy like Wellshaft. With our advanced technology, experienced team, and commitment to excellence, Wellshaft is your trusted global partner. Contact Wellshaft today to learn more about our salt bath nitriding services and how we can help you improve the performance and longevity of your metal components.