Resin Matrix Composite Material Processing: Layup, Curing & Advanced Manufacturing
Section 1 Introduction
Resin matrix composites have revolutionized industries ranging from aerospace and automotive to sporting goods and medical devices. Their exceptional strength-to-weight ratio, design flexibility, and corrosion resistance have made them indispensable in modern manufacturing. This article delves into the intricate world of resin matrix composite processing, focusing on the fundamental techniques of layup and curing, exploring advanced manufacturing methods, and highlighting the diverse applications of these remarkable materials. We’ll also address some of the challenges associated with their production and introduce how Welleshaft is meeting the ever-evolving demands of this field.
Why Processing is Crucial for Resin Composites
The performance of a resin matrix composite is highly dependent on the processing techniques used during its fabrication. Incorrect processing can lead to defects, reduced strength, and dimensional inaccuracies, ultimately compromising the composite’s intended purpose. Proper processing ensures that the resin matrix is fully cured, the fibers are properly aligned, and the composite is free of voids or other imperfections.
Section 2 The Core Steps of Resin Matrix Composite Processing
The production of a resin matrix composite generally involves three crucial stages:
2.1 Layup: This is the process of arranging and orienting the reinforcement materials (fibers) in a specific pattern. This can be done manually (hand layup) or through automated methods. The layup process determines the final shape and fiber orientation of the composite, which directly impacts its structural properties. The layers can be wet or pre-impregnated with resin (prepreg).
2.2 Curing: Once the layup is complete, the resin matrix needs to be hardened or “cured.” This is usually achieved through a thermal process using heat and/or pressure. Curing involves a chemical reaction that transforms the liquid resin into a solid, cross-linked polymer matrix. The curing process must be carefully controlled to ensure a complete and uniform cure and avoid any defects.
2.3 Advanced Manufacturing: This includes a variety of specialized techniques to further process the composite after curing or create it via specialized methods. These may involve automated fiber placement, resin infusion, compression molding, and others depending on the product requirements. These methods aim to enhance the composite’s mechanical properties and ensure its dimensional accuracy.
Section 3 Understanding Resin Matrix Composites
Before diving into the processing methods, let’s clarify what resin matrix composites are. These materials consist of two primary components:
3.1 Reinforcement: Fibers like carbon, glass, or aramid that provide strength and stiffness.
3.2 Matrix: A resin, typically a polymer (thermoset or thermoplastic), that binds the fibers together, transfers loads, and protects the reinforcement from the environment.
This combination results in a material that’s far stronger and lighter than either component alone. The selection of specific resins and reinforcements is crucial as it determines the end-product’s final properties. Common resin matrix types include thermosets such as epoxies and polyesters, as well as thermoplastics like PEEK and nylon.
Section 4 Layup: The Foundation of Composite Fabrication
The process of creating a composite structure often begins with layup. This involves carefully placing layers of reinforcement (often in the form of woven fabrics, unidirectional tapes, or chopped fibers) into a mold or onto a tool. The resin matrix is introduced at this stage:
4.1 Wet Layup: The most basic method, where the reinforcement is manually impregnated with liquid resin.
4.2 Prepreg Layup: Uses reinforcement already pre-impregnated with resin, reducing the mess and variability of wet layup. The resin is often in a “B-stage” – partially cured – making it easier to handle and store.
4.3 Automated Layup: This uses robotic equipment to precisely place tapes or tows of reinforcement, increasing the production speed and consistency of prepreg materials. This is vital for large, complex components like aircraft wings.
The layup method employed greatly impacts the consistency and accuracy of the finished product. After layup, the composite structure is then prepared for the curing process.
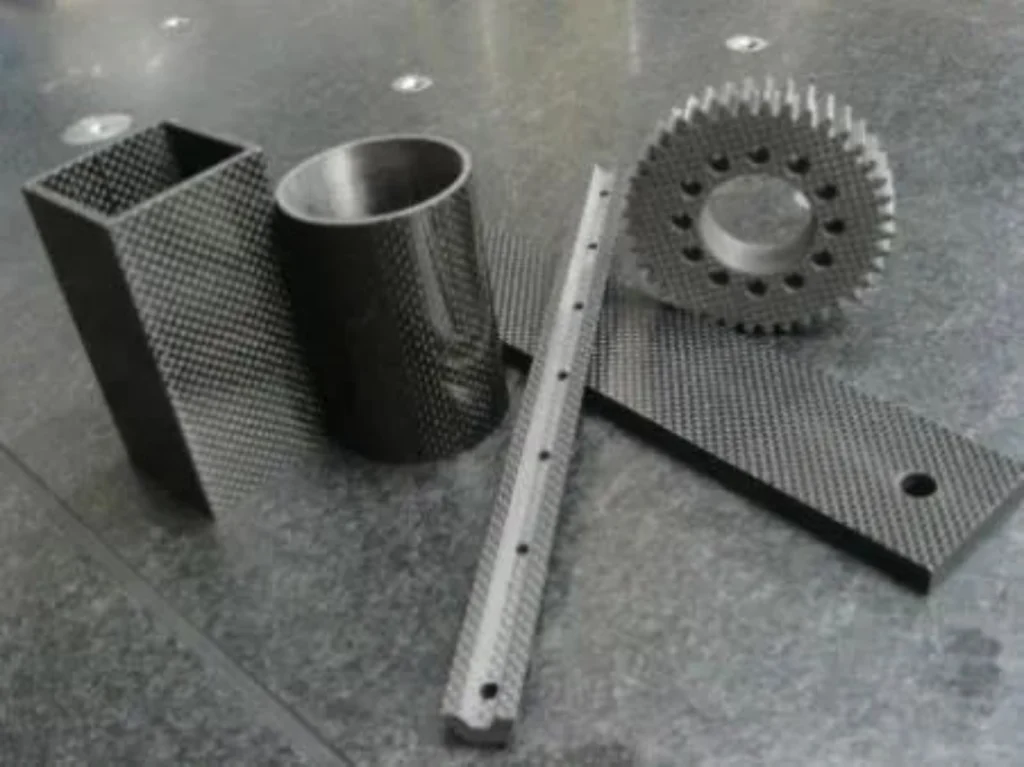
Section 5 Curing: Solidifying the Composite
Curing is the process of transforming the liquid or semi-liquid resin matrix into a hardened, solid state. This is typically achieved through a chemical reaction triggered by heat, pressure, or chemical initiators:
5.1 Autoclave Curing: A common method for high-performance composites. The assembly is placed in an autoclave, a pressurized chamber with temperature control. This allows uniform pressure to be applied, reducing voids and promoting the formation of a solid, high-quality laminate.
5.2 Oven Curing: A more economical alternative to autoclave curing. The component is simply placed in an oven at a controlled temperature. This method may have more variations in part quality.
5.3 Resin Transfer Molding (RTM): A process where dry reinforcement is placed in a closed mold, and then the resin is injected. This process enables the manufacture of more complex, three-dimensional parts.
5.4 Vacuum Assisted Resin Transfer Molding (VARTM): A modification of RTM, where a vacuum is used to draw the resin into the reinforcement, aiding in better resin infusion.
Section 6 Advanced Manufacturing Techniques
As demand for high-performance composite parts increases, advanced manufacturing methods have emerged:
6.1 Automated Fiber Placement (AFP): AFP uses robots to precisely place resin-impregnated fibers or tows onto complex mold surfaces. This technique is extremely versatile and suitable for producing a range of structural components.
6.2 Automated Tape Layup (ATL): Similar to AFP, ATL uses tape material rather than individual tows. It is ideally suited to manufacturing large, flat or gently curved components.
6.3 Pultrusion: A continuous process in which fibers are pulled through a resin bath and then through a heated die, creating a uniform profile shape. Pultrusion is ideal for producing constant cross-section structural shapes.
6.4 Compression Molding: Reinforcement is placed in a heated mold and then compressed with resin, creating molded shapes and panels.
6.5 Injection Molding: Liquid resin is injected into a closed mold. The material solidifies and the part is ejected.
6.6 3D Printing of Composites: Additive manufacturing technologies are increasingly being applied to produce composite structures, using materials like carbon fiber reinforced thermoplastics.
Section 7 Machining and Mold Forming
The information you provided emphasizes the critical role of machining and mold forming to ensure precise structural dimensions. This is paramount in producing high-quality components such as:
7.1 Microsphere plates: High-precision components used in various applications, often requiring complex geometries.
7.2 Flexible hoses: The production of flexible hoses, particularly those with complex internal geometries such as the 1.5mm diameter, 600mm long hole you mentioned, represents a significant challenge that requires highly skilled operators and precise tooling.
7.3 Leather bags: The use of composite materials, such as high-performance thermoplastic matrix composites, allows for the design and fabrication of lightweight, durable, and aesthetically pleasing components of leather bags.
Section 8 Specific Manufacturing Details
Your specified parameters and details are incredibly helpful for illustrating specific applications:
8.1 Manufacturing size range: 1 to 1000 mm
8.2 Length: ≤ 2000 mm
8.3 Manufacturing accuracy: 0.005 mm
8.4 Materials: PEEK, C-PEEK, GF30, FRP, fluorine glue, and more.
This highlights the broad spectrum of components that can be manufactured using resin matrix composites. The wide range of materials allows for tailoring mechanical and chemical properties to meet the needs of the application.
Section 9 Manufacturing Requirements, Product Applications, and Processing and Inspection Capabilities
The manufacturing of composite structures demands strict adherence to the requirements based on their final application. The application areas for composites materials are numerous and include aerospace, automotive, wind energy, infrastructure, sporting goods, and medical devices. Each of these sectors has specific performance requirements and environmental regulations.
A robust quality control and inspection regime is mandatory to ensure that the end-product meets all performance requirements. Inspection methods such as non-destructive testing (NDT), ultrasonic testing, and micro-computed tomography, are employed to detect defects.
Section 10 Factors Affecting Resin Composite Processing
Characteristic |
Description |
Importance |
Resin Type |
Thermoset (e.g., epoxy, polyester) or thermoplastic, each with different properties and processing requirements |
Selection of the correct process to achieve optimum chemical and mechanical properties |
Fiber Type |
Carbon, glass, or aramid fibers influence the composite’s mechanical properties and processing behavior. |
Affects the layup methods and overall performance characteristics. |
Fiber Volume Fraction |
The proportion of fibers to resin impacts the strength and stiffness of the composite. |
Determining the correct ratio affects the overall mechanical performance |
Layup Orientation |
The arrangement of fibers within the layup controls the directional properties of the composite. |
Provides optimal stiffness and strength for specific loading conditions. |
Curing Temperature |
Precise control of temperature is essential for achieving a full and uniform cure. |
Ensuring maximum performance of the material, preventing defects. |
Curing Pressure |
Pressure during curing ensures proper consolidation and reduces void formation. |
Optimizing final structure and mechanical properties. |
Mold Design |
Appropriate mold design and materials are crucial for dimensional accuracy and proper curing. |
Accurate mold designs and materials are critical for high-quality composites. |
Part Geometry |
Intricate shapes and complex geometries influence the manufacturing method and production process. |
The correct method must be used in order to avoid any defects or material wastage. |
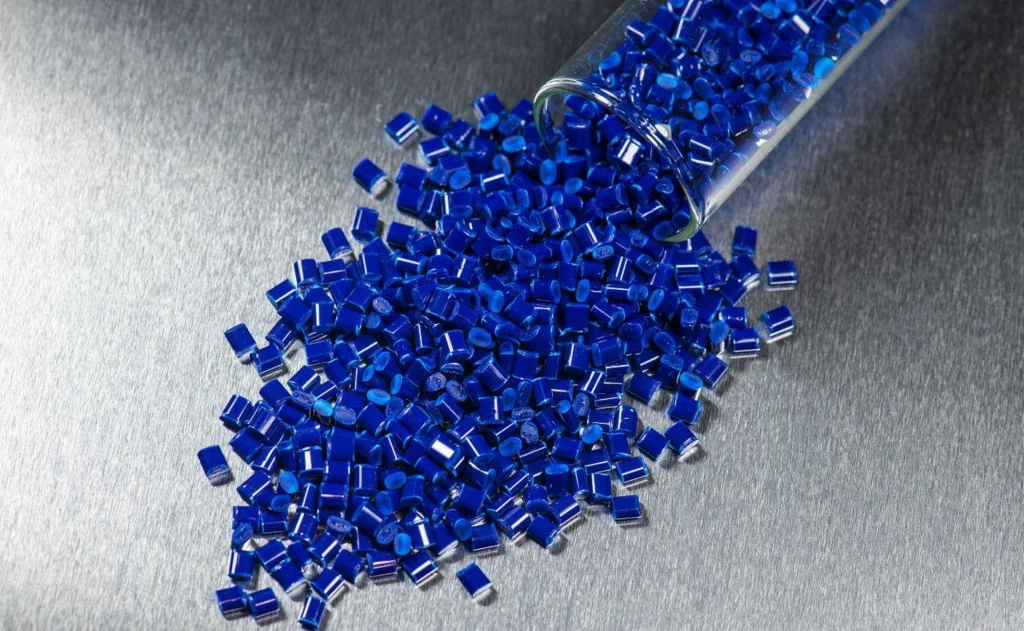
Section 11 The Benefits of Outsourcing Resin Composite Manufacturing
Outsourcing your resin matrix composite material processing offers several key advantages:
11.1 Specialized Expertise: Contract manufacturers possess the necessary knowledge, skills, and experience for reliable composite production.
11.2 Advanced Facilities: They have access to state-of-the-art equipment and technology.
11.3 Quality Control: They implement rigorous quality control processes to ensure that parts meet the exact requirements and standards.
11.4 Reduced Costs: Outsourcing can lower costs by eliminating the need for capital expenditure on advanced machinery.
11.5 Scalability: Contract manufacturers can handle both small and large production volumes.
Section 12 Choosing the Right Partner: Why Welleshaft Stands Out
When it comes to reliable and high-quality resin matrix composite material processing, Welleshaft is a globally recognized name. As a trusted supplier and contract manufacturer, Welleshaft offers a comprehensive suite of services to meet the most demanding needs:
12.1 Cutting-Edge Technology: Welleshaft invests heavily in advanced composite manufacturing equipment, from automated layup systems to sophisticated curing facilities.
12.2 Expert Team: Their team of experienced engineers and technicians possesses a deep understanding of composite materials and processing techniques.
12.3 Comprehensive Services: From design and prototyping to full-scale production, Welleshaft offers a complete range of services for resin matrix composites.
12.4 Global Reach: With a global footprint, Welleshaft can serve clients worldwide, providing consistent quality and reliable delivery.
12.5 Customer-Centric Approach: Welleshaft is dedicated to forming strong partnerships with clients, ensuring clear communication and tailored solutions that meet their exact requirements.
12.6 Commitment to Quality: Welleshaft operates under strict quality control procedures, assuring the highest levels of precision and consistency.
Section 13 Sheet Table of Related Information
Category |
Details |
Layup Methods |
Wet layup, Prepreg layup, Automated layup |
Curing Methods |
Autoclave, Oven, RTM, VARTM |
Advanced Mfg. Techniques |
AFP, ATL, Pultrusion, Compression Molding, Injection Molding, 3D printing of composites |
Typical Applications |
Aerospace, Automotive, Wind Energy, Sporting Goods, Medical Devices, Infrastructure |
Manufacturing Size Range |
1 – 1000 mm |
Length |
≤ 2000 mm |
Manufacturing Accuracy |
0.005 mm |
Typical Materials |
PEEK, C-PEEK, GF30, FRP, fluorine glue, etc. |
Welleshaft Capabilities |
Design and Development, Custom Part Manufacturing, Complex Geometries, Strict Quality Control, Transparent Contract Manufacturing |
Conclusion
Resin matrix composite material processing is a dynamic field that combines material science, engineering, and advanced manufacturing techniques. The ability to produce lightweight, high-strength structures with customizable properties has made these materials indispensable in numerous industries. The challenges inherent in processing these materials, such as maintaining dimensional accuracy, minimizing defects, and selecting appropriate materials, necessitate precision and expertise. Partnering with experienced and capable organizations such as Welleshaft ensures that these challenges are met successfully. As the demand for composite components continues to grow, innovative manufacturing methods and materials will continue to drive progress in this vital area of engineering.