Reduce Spatter with Quality Argon Arc Welding Ceramic Nozzles
Section 1 Introduction
Argon arc welding, also known as Tungsten Inert Gas (TIG) welding or Gas Tungsten Arc Welding (GTAW), is renowned for its precision and high-quality welds. However, one of the common challenges faced by welders is the issue of spatter – unwanted droplets of molten metal that can lead to imperfections, wasted materials, and additional cleaning efforts. The key to minimizing spatter and achieving smoother, cleaner welds lies in using the right equipment, and one of the most critical components is the ceramic nozzle. In this article, we’ll explore the importance of high-quality argon arc welding ceramic nozzles, their specifications, material properties, and applications, and introduce you to a trusted global supplier and contract manufacturer, Welleshaft.
Section 2 The Crucial Role of the Ceramic Nozzle
The ceramic nozzle in argon arc welding plays a vital role in directing the shielding gas around the tungsten electrode and the weld pool. This shielding gas, typically argon, prevents atmospheric contamination, which could result in porous, brittle, or otherwise inferior welds. A high-quality ceramic nozzle ensures a smooth and consistent flow of gas, preventing turbulence and disruptions that can lead to spatter. In addition, the nozzle must be made from a material that can withstand high temperatures and still maintain its geometry to achieve optimal welding performance.
Section 3 Why Spatter Reduction Matters
Spatter can cause a variety of issues for welders, including:
3.1 Weld Imperfections: Spatter can adhere to the weld area, creating surface irregularities that require additional grinding or cleaning.
3.2 Material Waste: Spatter results in the loss of molten metal, increasing the overall material usage and cost.
3.3 Reduced Productivity: The time spent cleaning up spatter slows down the welding process, impacting productivity and project timelines.
3.4 Compromised Weld Integrity: Excessive spatter can indicate that the weld is not properly shielded and may be prone to defects.
By investing in quality argon arc welding ceramic nozzles, welders can significantly reduce spatter and achieve a higher quality weld, save time, and reduce costs.
Section 4 Benefits of High-Quality Argon Arc Welding Ceramic Nozzles
4.1 Consistent Gas Flow: Precision-engineered nozzles ensure an even and controlled gas flow, preventing turbulence and minimizing spatter.
4.2 Improved Weld Quality: Reduced spatter leads to smoother, cleaner welds with minimal imperfections.
4.3 Enhanced Shielding: Proper shielding protects the weld pool from atmospheric contamination, resulting in stronger, more reliable welds.
4.4 Heat Resistance: High-quality ceramic nozzles are made from materials that can withstand the intense heat of arc welding, ensuring long-lasting performance.
4.5 Precise Fit: Nozzles designed to fit your torch perfectly will not leak gas, and will ensure the right angle of the gas flow for the correct weld.
4.6 Cost-Effective: By reducing spatter and defects, quality nozzles help minimize material waste and rework, leading to long-term cost savings.
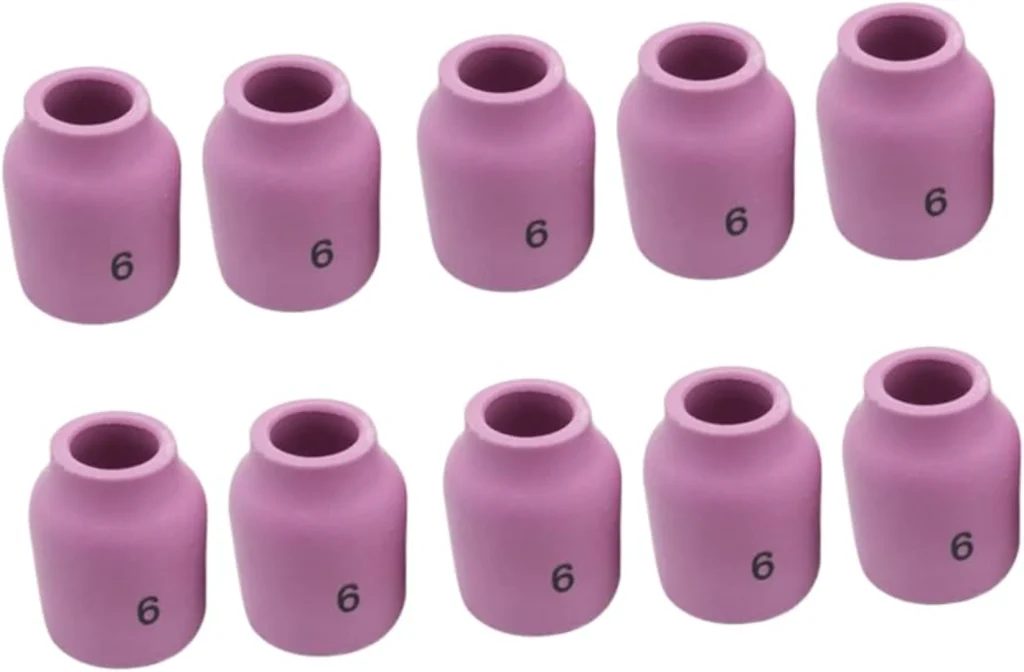
Section 5 How Poor Nozzles Contribute to Spatter
Using subpar or damaged ceramic nozzles can contribute directly to spatter formation:
5.1 Inconsistent Gas Flow: Nozzles with internal damage, imperfections or poorly designed gas flow channels disrupt the laminar flow of the shielding gas. This creates turbulent conditions, allowing air to mix with the gas stream, leading to oxidation and spatter.
5.2 Overheating: Poor quality ceramics can fail under higher temperatures. This can cause damage and distortion, making your gas flow even more turbulent.
5.3 Inadequate Protection: Nozzles that are not correctly sized for the welding application or those that have sustained damage may not provide sufficient shielding to the weld pool and surrounding material, resulting in oxidization, and thereby, spatter.
Section 6 Specifications and Material Properties
The performance of a ceramic nozzle is greatly influenced by its specifications and material properties. Here’s a breakdown of the key factors:
Table 1: Typical Specifications of Argon Arc Welding Ceramic Nozzles
Feature |
Description |
Typical Range |
Material |
High-purity Alumina (Aluminum Oxide) |
Al2O3 content typically 95%-99.7% |
Sizes |
Various diameters and lengths to suit different torch models and welding needs |
Diameter: 6-16mm, Length: 20-70mm, Or custom sizes |
Thread Type |
Varies based on the torch model – M8, M10, 3/8″ etc… |
ISO Metric, National Thread Standards |
Gas Flow Rate |
Optimized for even gas distribution |
Varies based on size, and the application |
Heat Resistance |
Withstands high welding temperatures |
Up to 1500°C, continuous operating temperatures. |
Operating Voltage |
Generally not affected by welding voltage |
Up to 500 volts DC |
Chemical Resistance |
Inert to common welding gases, like Argon |
Resistant to acidic environments |
Material Properties of Alumina (Al2O3) Ceramic:
High-Temperature Resistance: Excellent thermal stability, capable of withstanding extreme temperatures without deformation.
Chemical Inertness: Resistant to chemical reactions with welding gases, ensuring no contamination of the weld.
Electrical Insulation: Non-conductive, ensuring user safety.
Wear Resistance: Hard and durable, resistant to abrasion and mechanical stress.
Low Thermal Expansion: Minimal expansion at high temperatures, maintaining dimensional accuracy.
Table 2: Common TIG Welding Ceramic Nozzle Sizes & Applications
Nozzle Size (Gas Lens) |
Orifice Diameter (approx.) |
Typical Amperage Range |
Common Applications |
No. 4 |
1/4″ |
50-100 A |
Thin Materials, Stainless Steel Sheet, Automotive Panels |
No. 5 |
5/16″ |
75-150 A |
General Purpose Welding, Steel, Stainless Steel |
No. 6 |
3/8″ |
100-200 A |
Moderate to Heavy Welding, Aluminum |
No. 7 |
7/16″ |
150-250 A |
Heavy Welding, Pipe Welding, Thick Plate |
No. 8 |
1/2″ |
200-300 A |
High-Amp Welding, Large Parts, Construction |
Note: These are general guidelines. Always consult your welding equipment’s manual for specific recommendations.
Section 7 Applicable Characteristics
Ceramic nozzles for argon arc welding are designed for various welding needs. Key applicable characteristics include:
7.1 Versatility: Suitable for a wide range of materials, including stainless steel, aluminum, titanium, and carbon steel.
7.2 Precision Welding: Ideal for applications requiring fine welds and high levels of accuracy.
7.3 High Duty Cycle: Designed to perform well under continuous use in professional welding environments.
7.4 Compatibility: Available in different sizes and threading to fit various welding torch models and equipment.
7.5 Material Quality: Look for nozzles made from high-purity alumina ceramic for optimal heat resistance and durability.
7.6 Precise Manufacturing: Consistent dimensions and smooth internal surfaces are critical for ensuring proper gas flow.
7.7 Size & Shape: Select nozzles that are appropriately sized for the welding application. Different sizes and shapes are available for various welding techniques and material thicknesses.
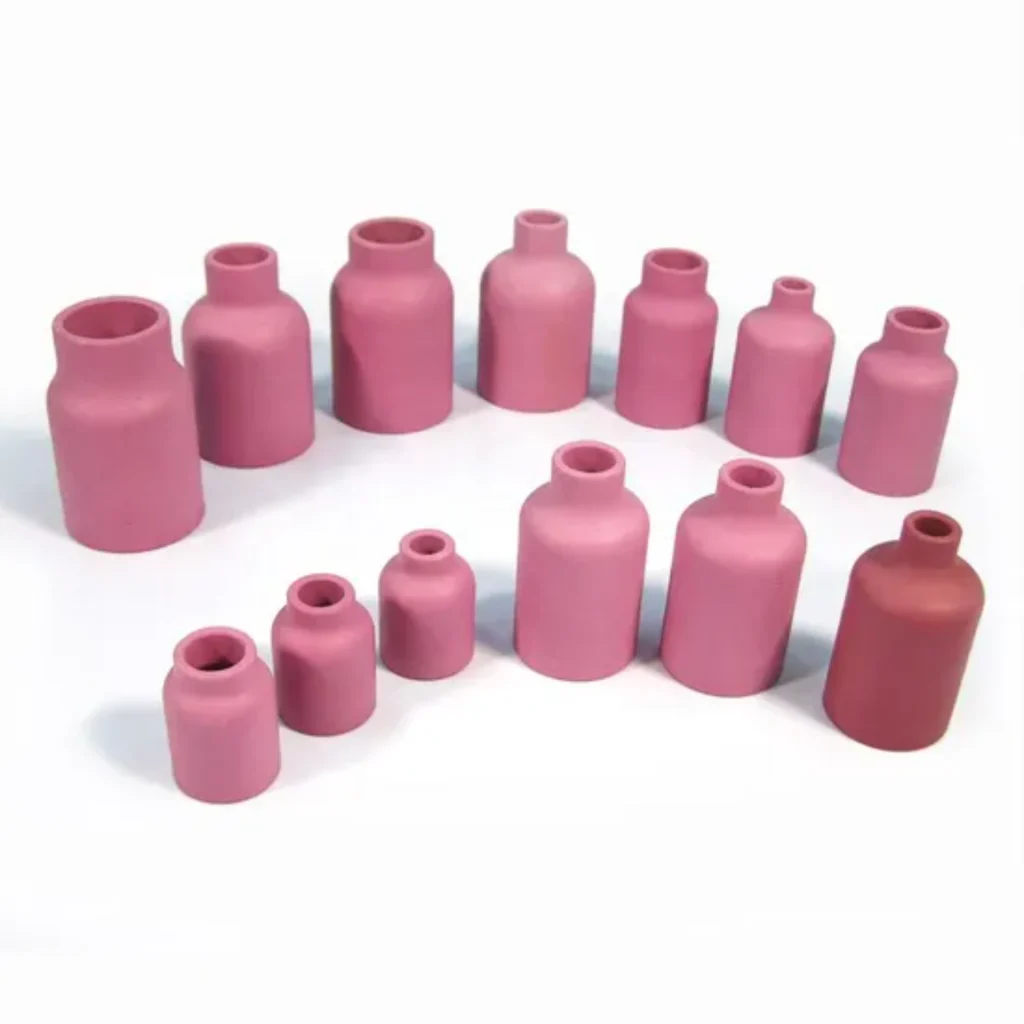
Section 8 Application Fields
High-quality argon arc welding ceramic nozzles find applications across many industries, such as:
8.1 Aerospace: Precision welding of critical components for aircraft engines, fuselages, and other parts.
8.2 Automotive: Manufacturing of automotive parts, exhaust systems, and chassis components.
8.3 Medical Devices: Fabrication of medical implants, instruments, and equipment requiring precise welds.
8.4 Manufacturing: General fabrication of various metal products.
8.5 Nuclear Industry: Welding of nuclear-grade components with strict quality and safety requirements.
8.6 Robotics and Automation: Welding with automated welding robots and equipment.
8.7 Construction: Welding of metal structures, and components in buildings and infrastructure.
Section 9 Welleshaft Processing and Testing Capabilities
9.1 Advanced Ceramic Processing: Welleshaft utilizes state-of-the-art techniques for manufacturing high-purity alumina ceramic nozzles, ensuring consistent material properties.
9.2 Precision Machining: Modern CNC machining ensures tight dimensional tolerances for perfect fit and gas flow optimization.
9.3 Comprehensive Quality Control: Rigorous testing throughout the production process, including dimensional checks, material analysis, and performance testing.
9.4 Custom Solutions: Welleshaft has strong experience in custom-designing nozzles to meet specific customer needs and applications.
9.5 Rapid Prototyping: Can produce custom prototypes of different sizes quickly for testing and proof of concept.
9.6 Scalable Production: Equipped to handle both small and large-scale production runs with consistent quality.
Section 10 Welleshaft: Your Trusted Global Supplier
When it comes to sourcing high-quality argon arc welding ceramic nozzles, Welleshaft stands out as a reputable global supplier and contract manufacturer. With years of experience in precision ceramic manufacturing, Welleshaft is committed to delivering products that meet the highest industry standards.
Why Choose Welleshaft?
10.1 Quality Assurance: Welleshaft is committed to producing top-notch ceramic products.
10.2 Global Reach: Serving customers worldwide with a reliable and efficient supply chain.
10.3 Expertise: A team of experienced engineers and ceramic specialists dedicated to providing innovative solutions.
10.4 Customer Focus: Welleshaft works closely with clients to understand their needs and deliver tailored products and services.
10.5 Competitive Pricing: Offering high-quality products at competitive prices.
Table 3: Common Related Terms Used With Argon Arc Welding Ceramic Nozzles
Related Term |
Description |
TIG Welding Ceramic Nozzle |
Refers to the ceramic nozzle used in Tungsten Inert Gas (TIG) welding. |
GTAW Ceramic Nozzle |
Refers to the ceramic nozzle used in Gas Tungsten Arc Welding (GTAW). |
Gas Lens Nozzle |
A nozzle design that incorporates a gas lens for improved gas flow, typically offering better gas coverage. |
Alumina Nozzle |
A ceramic nozzle specifically made from alumina (aluminum oxide), the common material used for these nozzles. |
TIG Torch Nozzle |
Refers to the nozzle as a component of the TIG welding torch. |
Shielding Gas Nozzle |
Highlights the primary function of the nozzle, which is to direct the shielding gas. |
Ceramic Gas Focusing Nozzle |
Emphasizes the directional and focusing action of the gas flow through the nozzle. |
High-Temperature Gas Nozzle |
Refers to nozzles designed to withstand the high temperatures generated during welding. |
Welding Torch Ceramic Insulator |
Highlight the insulation that the ceramic part provides to the torch. |
Argon Gas Flow Control Nozzle |
Emphasizes that the function of the nozzle is to control the gas flow during the welding. |
TIG Weld Head Nozzle |
Again, refers to the nozzle as a component in the welding process. |
Ceramic Cup |
Another common name for the ceramic nozzle |
Gas Diffuser |
Another common name for ceramic nozzles |
Conclusion
Reducing spatter is essential for achieving high-quality, efficient welds in argon arc welding. By investing in superior ceramic nozzles, welders can significantly improve their results, reduce costs, and enhance productivity. With a strong commitment to quality, Welleshaft is your ideal partner for sourcing precision ceramic nozzles and ensuring the success of your welding projects. Contact Welleshaft today to learn more about our products and how we can assist you with your welding needs.