Premium Sintered Copper Components | High-Quality Copper Sintering Solutions
When it comes to industrial applications demanding superior performance and reliability, sintered copper components stand out. Known for their durability, versatility, and high conductivity, sintered copper materials are becoming increasingly indispensable in various fields. In this article, we’ll delve into what makes sintered copper a top choice, its advantages, and its diverse applications. We’ll also introduce Welleshaft as a trusted global supplier and contract manufacturer specializing in high-quality sintered copper solutions.
Section 1: What is Sintered Copper?
Sintered copper refers to copper that has been processed through sintering—a method where copper powder is heated below its melting point to form a solid material. This process allows the copper powder particles to bond together, creating a porous yet solid material. This sintered form maintains many of copper’s natural properties, including its excellent electrical and thermal conductivity, while also offering additional benefits such as improved strength and customizability.
1. Copper Powder Sintering
The sintering of copper powder involves several critical steps:
- Powder Preparation: High-purity copper powder is prepared, often mixed with additives to enhance properties like strength or conductivity.
- Compaction: The copper powder is compacted into a mold under high pressure to form a green body.
- Sintering: The green body is heated in a controlled atmosphere furnace at temperatures below copper’s melting point (around 1000°C to 1100°C). This step allows the copper particles to fuse together without melting, forming a solid material with controlled porosity.
- Post-Processing: Depending on the application, the sintered copper may undergo additional processes such as machining, impregnation, or surface treatment.
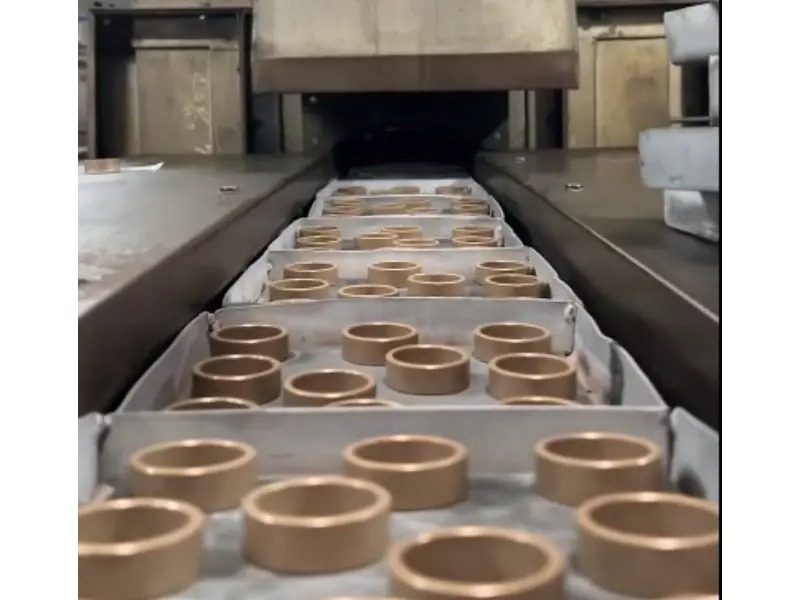
Section 2: Sintered Copper vs. Copper
2.1. Sintered Copper vs. Copper: Key Differences
1. Structure and Porosity
Sintered Copper: Has a porous structure, which can be beneficial for applications requiring controlled permeability or self-lubrication. The porosity can be adjusted based on the specific needs of the application.
Copper: Is non-porous, providing a solid and continuous material that is ideal for applications requiring high-density and uniform properties.
2. Mechanical Properties
Sintered Copper: Typically offers enhanced mechanical strength and wear resistance due to the sintering process. This makes it suitable for high-stress applications where durability is crucial.
Copper: While copper is inherently strong, its mechanical properties can be less robust compared to sintered copper, especially in applications involving significant wear or impact.
3. Thermal and Electrical Conductivity
Sintered Copper: Retains good thermal and electrical conductivity, though it may be slightly lower than pure copper due to the presence of porosity and the potential for impurities from the sintering process.
Copper: Provides superior thermal and electrical conductivity, making it the material of choice for applications requiring maximum efficiency in heat and electrical transfer.
4. Customizability
Sintered Copper: Offers significant customization options, including control over porosity, density, and specific alloying elements. This allows for the creation of materials tailored to particular performance requirements.
Copper: While highly versatile, it does not offer the same level of customization in terms of porosity and density. Pure copper is typically used in standard forms and shapes.
Applications
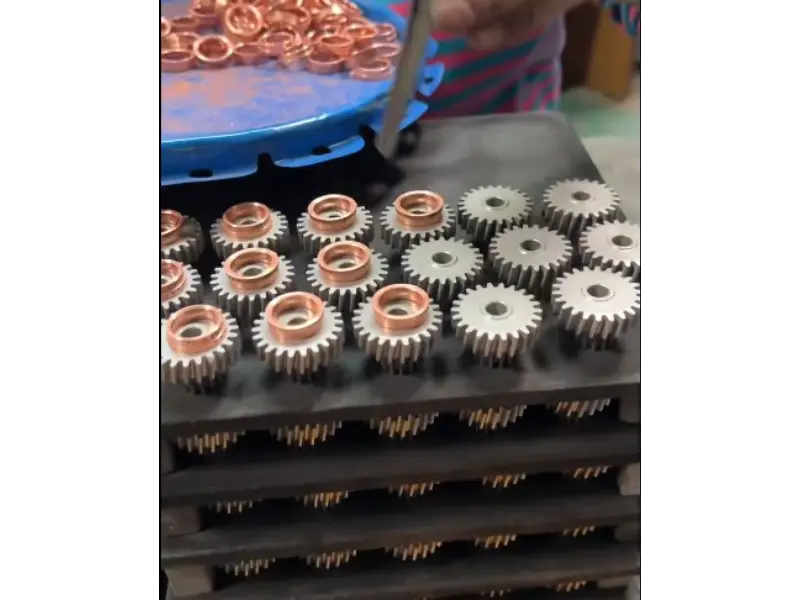
2.2. Sintered Copper Applications
Automotive Industry: Sintered copper brake pads and self-lubricating bearings leverage the material’s durability and wear resistance.
Filtration Systems: Sintered copper filters are used in applications requiring controlled filtration and high-temperature resistance.
Heat Exchangers: The high thermal conductivity of sintered copper makes it suitable for heat exchange applications, including cooling systems and thermal management solutions.
Electrical Components: Sintered copper is used in electrical contacts and connectors where a combination of conductivity and customizability is needed.
2.3. Copper Applications
Electrical Wiring: Copper is the preferred material for electrical wiring due to its superior conductivity and flexibility.
Plumbing: Copper pipes and fittings are widely used in plumbing systems for their durability and resistance to corrosion.
Heat Sinks: Copper’s excellent thermal conductivity makes it ideal for heat sinks and other thermal management applications.
Construction: Copper is used in roofing, gutters, and various architectural elements for its aesthetic appeal and weather resistance.
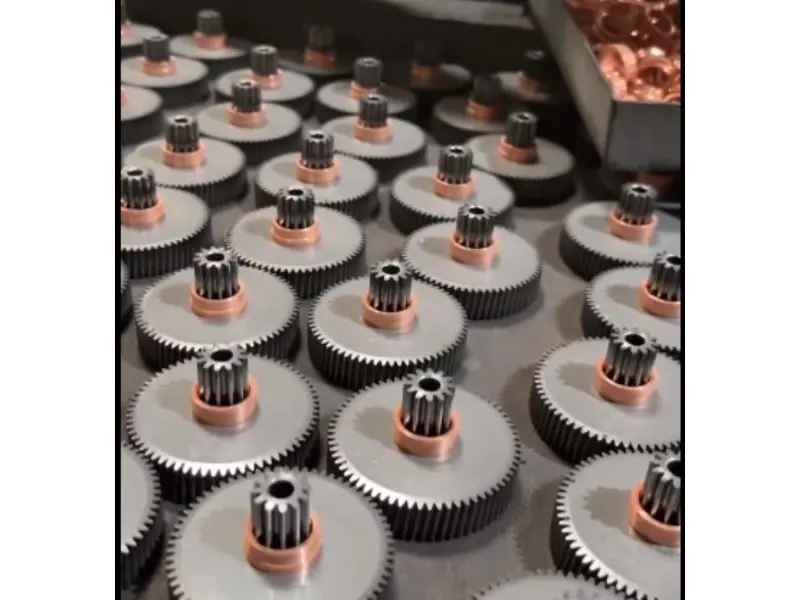
Section 3: Sintered Copper Products: Versatile Solutions for Diverse Applications
Sintered copper is a material with unique properties that make it suitable for a wide range of applications. Created through the sintering process, where copper powder is heated to form a solid material without melting, sintered copper offers controlled porosity, enhanced strength, and high thermal and electrical conductivity. Below, we explore various sintered copper products, their features, and their applications.
1. Sintered Copper Brake Pads
Features:
- High Friction Coefficient:Provides excellent braking performance due to the high friction properties of sintered copper.
- Durability:Designed to withstand high temperatures and heavy wear, making them ideal for automotive and industrial braking systems.
- Noise Reduction: Often includes formulations to reduce noise and vibrations during operation.
Applications:
- Automotive Brakes:Used in vehicles for reliable braking performance under extreme conditions.
- Industrial Machinery:Employed in heavy machinery and equipment requiring robust braking solutions.
2. Sintered Copper Filters
Features:
- Controlled Porosity: Allows for precise filtration of particles and contaminants from fluids and gases.
- High Temperature Resistance:Suitable for applications involving high temperatures due to the material’s thermal stability.
- Corrosion Resistance: Offers resistance to corrosion, extending the lifespan of the filters.
Applications:
- Hydraulic Systems: Used to filter hydraulic fluids in industrial machinery.
- Air Filtration:Applied in air filtration systems to remove particulate matter from the air.
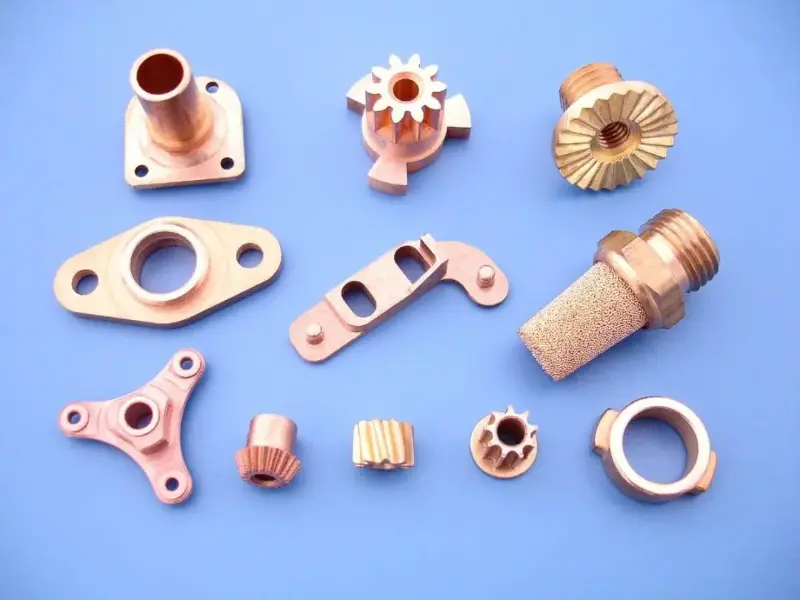
3. Sintered Copper Mesh Wick
Features:
- High Thermal Conductivity:Enhances heat transfer in thermal management applications.
- Porous Structure:Provides an effective medium for liquid wicking and heat dissipation.
- Customizable Sizes and Shapes:Available in various forms to fit specific applications.
Applications:
- Heat Exchangers:Utilized in heat exchange systems to improve heat transfer efficiency.
- Cooling Systems: Used in electronic cooling systems to manage heat in sensitive components.
4. Sintered Copper Pipe
Features:
- Enhanced Strength:Provides durability and resistance to mechanical stresses.
- High Thermal Conductivity:Ideal for applications requiring effective heat transfer.
- Customizable Dimensions:Can be produced in various sizes and shapes to meet specific needs.
Applications:
- Cooling Systems:Used in cooling systems for efficient heat dissipation.
- Plumbing Systems:Employed in applications requiring both strength and thermal conductivity.
5. Sintered Copper Powder
Features:
- Fine Particle Size:Offers the ability to produce high-density sintered components with precise specifications.
- Versatility: Can be used in various sintering processes to create different forms of copper products.
- Enhanced Properties: Provides a basis for producing sintered copper with customized properties.
Applications:
- Manufacturing:Used as a raw material for producing sintered copper components.
- Custom Components:Allows for the creation of specialized products tailored to specific applications.
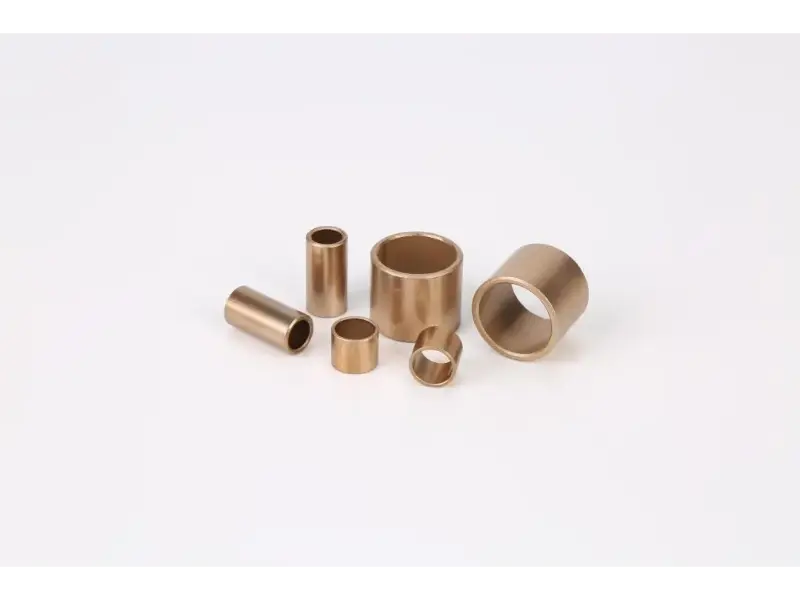
6. Sintered Copper Paste
Features:
- Easy Application: Applied as a paste for various coating and bonding processes.
- Good Adhesion:Provides strong adhesion to substrates and other materials.
- Conductivity: Maintains high thermal and electrical conductivity in the final application.
Applications:
- Electronics:Used in electronic component assembly for thermal and electrical connections.
- Manufacturing: Employed in the creation of complex sintered components requiring precise application.
7. Sintered Copper Mesh
Features:
- High Porosity: Allows for effective filtration and wicking in various applications.
- Strength and Durability:Combines strength with the ability to handle high temperatures and pressures.
- Customizable Forms:Available in various mesh sizes and shapes to fit specific needs.
Applications:
- Filtration Systems: Utilized in systems requiring fine filtration of liquids and gases.
- Heat Management:Employed in thermal management applications to enhance heat transfer.
8. Sintered Copper Components for Electronics
Features:
- High Conductivity: Ensures efficient electrical and thermal performance in electronic applications.
- Precision Manufacturing: Allows for the creation of intricate designs and specifications.
- Reliability: Offers consistent performance in critical electronic components.
Applications:
- Electrical Contacts:Used in connectors and other electrical components requiring high conductivity.
- Heat Sinks:Employed in cooling solutions for electronic devices to manage heat effectively.
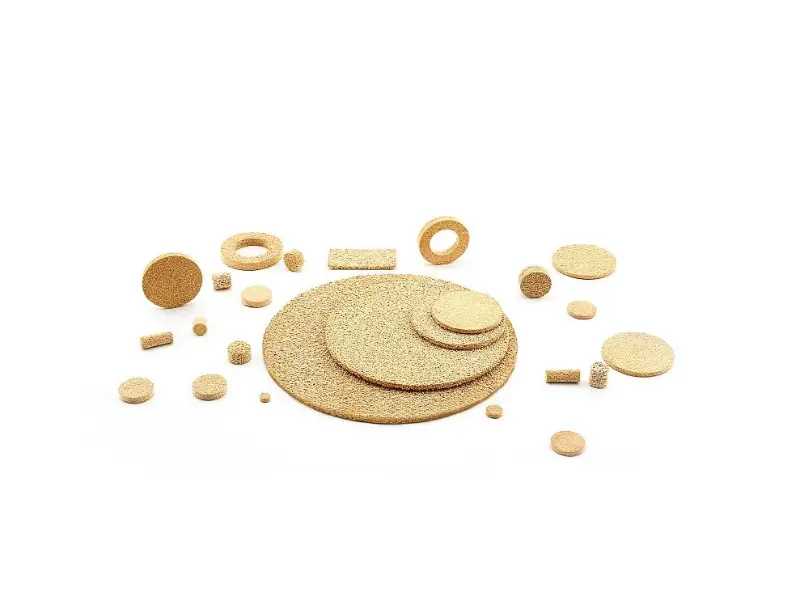
Welleshaft: Your Trusted Global Supplier and Contract Manufacturer
For premium sintered copper components and high-quality copper sintering solutions, Welleshaft stands out as a trusted global supplier and contract manufacturer. With years of expertise in the industry, Welleshaft offers:
- Custom Solutions:Tailor-made sintered copper components designed to meet specific requirements and applications.
- Quality Assurance:Rigorous quality control processes ensure that all products meet the highest standards of performance and reliability.
- Global Reach: Serving clients worldwide with timely delivery and exceptional customer service.
Whether you need sintered copper powder, sintered copper brake pads, or any other sintered copper product, Welleshaft’s commitment to quality and innovation ensures that you receive the best solutions for your needs.
Conclusion
Sintered copper is a remarkable material offering a blend of excellent conductivity, customizable properties, and improved mechanical performance. Its applications span various industries, from automotive to electronics and beyond. With Welleshaft as your partner, you can access high-quality sintered copper components tailored to your specific needs. For premium sintered copper solutions and unparalleled expertise, Welleshaft is your go-to source.
Explore the benefits of sintered copper and discover how Welleshaft can support your next project with top-tier materials and exceptional service.