Precision Blind Hollow Shafts: Optimized Performance for Rotary Motion
In the realm of mechanical engineering and motion control, the pursuit of efficiency, precision, and durability is relentless. One component that plays a critical, yet often understated, role in achieving these goals is the blind hollow shaft. This seemingly simple cylindrical part, when engineered with precision, unlocks significant advantages in a wide range of rotary motion applications. This article will explore the benefits, applications, design considerations, and why choosing a trusted supplier like Welleshaft is paramount.
Understanding the Blind Hollow Shaft
So, what exactly is a blind hollow shaft? Simply put, it’s a shaft with a hollow bore that doesn’t extend through the entire length of the shaft. In other words, one end of the shaft is closed, creating a cavity or bore that is accessible only from one side. This “blind” or “closed-end” design distinguishes it from a through-bored hollow shaft.
Key Advantages of Blind Hollow Shafts
Blind hollow shafts offer several compelling advantages over solid shafts or through-bored hollow shafts in specific applications:
Reduced Weight: By removing material from the center of the shaft, a blind hollow design significantly reduces weight, which is crucial in applications where inertia needs to be minimized. This leads to quicker acceleration, deceleration, and improved energy efficiency.
Space Savings: The hollow bore can be used to accommodate other components, such as wiring, pneumatic lines, or even smaller shafts, leading to a more compact and integrated system design.
Damping Characteristics: The hollow structure can provide enhanced damping capabilities, reducing vibrations and noise in rotary motion systems.
Thermal Management: In some applications, the hollow bore can be utilized to circulate cooling fluids, improving thermal management and preventing overheating.
Protection of Internal Components: The blind bore protects sensitive internal components, such as encoders or sensors, from external contaminants and physical damage.
Cost-Effectiveness: Depending on the manufacturing process and material, a hollow shaft can sometimes be more cost-effective than a solid shaft of equivalent strength and stiffness. This is especially true for large-diameter shafts.
Applications of Precision Blind Hollow Shafts
The versatility of blind hollow shafts makes them suitable for a diverse range of applications across various industries:
Robotics: In robotic arms and joints, weight reduction is paramount for achieving fast and precise movements. Blind hollow shafts are used extensively in servo motors and gearboxes to minimize inertia.
Automation Equipment: In automated machinery, such as packaging equipment and assembly lines, blind hollow shafts provide space for wiring and pneumatic lines, simplifying the overall design.
Medical Devices: In medical imaging equipment, such as CT scanners and MRI machines, blind hollow shafts are used to reduce weight and accommodate internal components.
Aerospace: In aircraft control systems and actuators, weight reduction is critical for improving fuel efficiency. Blind hollow shafts are used in various applications, including flight control surfaces and landing gear.
Printing and Converting: In high-speed printing and converting equipment, blind hollow shafts are used to minimize inertia and improve the accuracy of rotary motion.
Rotary Encoders: Many rotary encoders utilize a blind hollow shaft design for direct mounting onto a motor shaft, eliminating the need for couplings and improving accuracy.
Electric Motors: In certain electric motor designs, a blind hollow shaft is used to facilitate direct mounting of components or to provide access for wiring.
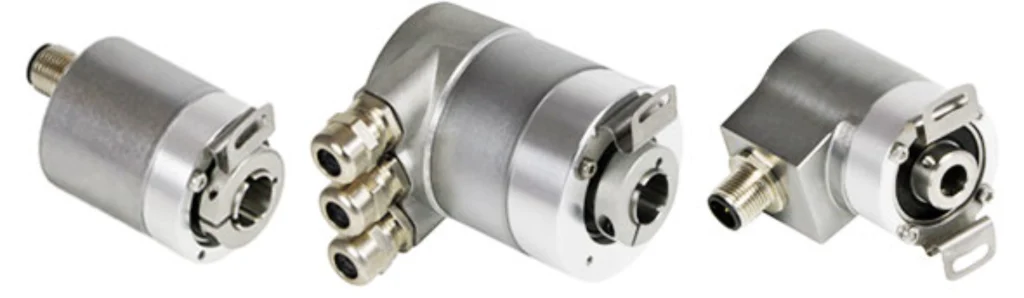
Design Considerations for Blind Hollow Shafts
Designing a blind hollow shaft requires careful consideration of several factors:
Material Selection: The choice of material depends on the application requirements, including strength, stiffness, weight, corrosion resistance, and operating temperature. Common materials include steel (various grades), aluminum alloys, stainless steel, and even composite materials.
Load Requirements: The shaft must be able to withstand the applied loads without excessive deflection or failure. Finite Element Analysis (FEA) is often used to analyze the stress distribution within the shaft.
Torsional Stiffness: The torsional stiffness of the shaft is critical in applications where precise angular positioning is required. A stiffer shaft will minimize angular deflection under load.
Bore Diameter and Depth: The dimensions of the hollow bore must be carefully chosen to accommodate the internal components or to achieve the desired weight reduction.
Surface Finish: The surface finish of the shaft and the bore can affect friction, wear, and corrosion resistance.
Manufacturing Process: The manufacturing process must be capable of producing the desired tolerances and surface finish. Common manufacturing processes include machining, gun drilling, and extrusion.
End Closure Design: The design of the closed end is crucial for ensuring structural integrity and preventing leakage (if applicable).
Table of Related Information
Feature | Solid Shaft | Through Hollow Shaft | Blind Hollow Shaft |
Weight | High | Medium | Low |
Stiffness | High | Medium | Medium to Low (depending on wall thickness) |
Space for Components | No | Yes | Yes (partially) |
Damping | Low | Medium | Medium |
Manufacturing Complexity | Low | Medium | Medium to High |
Cost | Low | Medium | Medium to High |
Torsional Rigidity | Highest | Lower | Medium |
Application Examples | Simple drive shafts | Cable routing; pneumatic lines | Robotics, rotary encoders |
The Importance of Precision Manufacturing
The performance and reliability of a blind hollow shaft are highly dependent on the precision of its manufacturing. Close tolerances, accurate dimensions, and a smooth surface finish are essential for ensuring proper fit, minimizing friction, and preventing premature failure.
Common Manufacturing Techniques
Several manufacturing techniques can be used to produce blind hollow shafts, each with its own advantages and disadvantages:
Machining: Machining is a versatile process that can be used to create complex shapes and precise dimensions. It typically involves turning, milling, and drilling operations.
Gun Drilling: Gun drilling is a specialized process for creating deep, accurate holes. It is often used to produce the hollow bore in blind hollow shafts.
Extrusion: Extrusion is a cost-effective process for producing long, hollow shapes with a constant cross-section.
Powder Metallurgy (PM): PM allows for the creation of complex shapes and controlled porosity, which can be beneficial for damping applications.
Additive Manufacturing (3D Printing): 3D printing offers the potential to create highly customized and complex blind hollow shaft designs with minimal material waste.
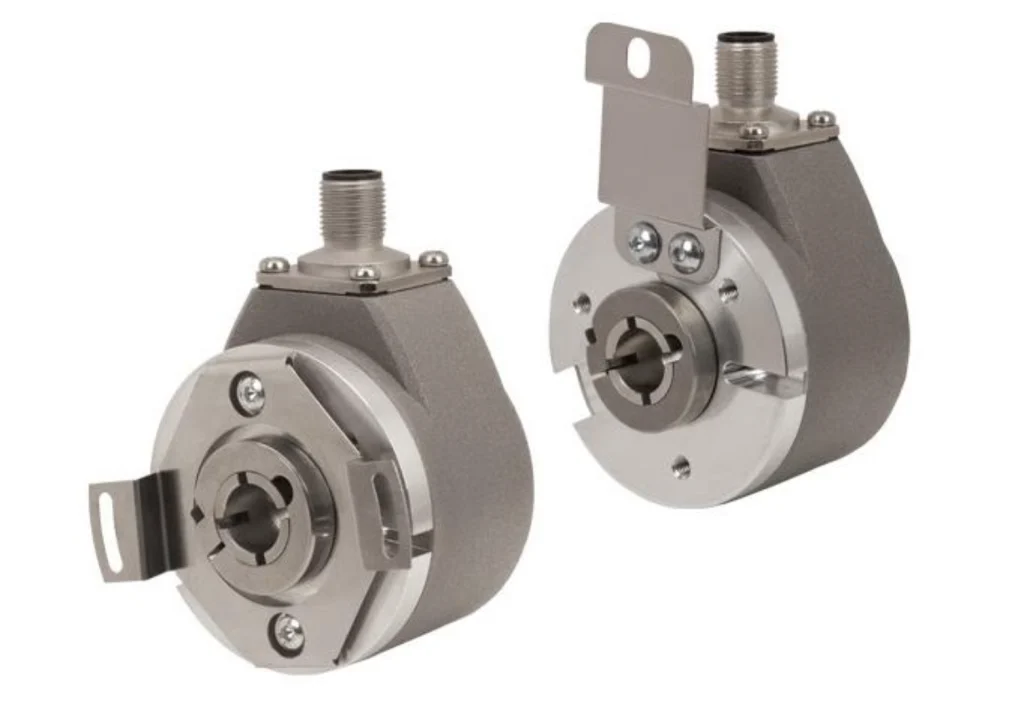
Choosing the Right Supplier: Why Welleshaft?
Selecting a reliable and experienced supplier is crucial for ensuring the quality and performance of your blind hollow shafts. Welleshaft stands out as a trusted global supplier and contract manufacturer for several key reasons:
Expertise and Experience: Welleshaft possesses extensive knowledge and experience in designing and manufacturing precision shafts for a wide range of industries.
Advanced Manufacturing Capabilities: Welleshaft utilizes state-of-the-art manufacturing equipment and processes to ensure the highest levels of precision and quality.
Customization Options: Welleshaft offers a wide range of customization options, including material selection, dimensions, surface finish, and special features, to meet your specific application requirements.
Quality Assurance: Welleshaft adheres to stringent quality control standards throughout the manufacturing process to ensure that every shaft meets or exceeds your expectations.
Global Reach: Welleshaft provides global support and service to customers around the world.
Commitment to Innovation: Welleshaft is committed to continuous innovation and invests in research and development to improve its products and processes.
Welleshaft: Your Partner in Rotary Motion Solutions
Welleshaft understands the critical role that precision blind hollow shafts play in optimizing rotary motion systems. Their team of experienced engineers can work with you to design and manufacture shafts that meet your exact requirements, ensuring superior performance, reliability, and durability. Whether you need a standard shaft or a custom-engineered solution, Welleshaft has the expertise and capabilities to deliver.
Conclusion
Precision blind hollow shafts offer a compelling combination of weight reduction, space savings, and improved performance in a wide range of rotary motion applications. By understanding the design considerations and choosing a trusted supplier like Welleshaft, you can unlock the full potential of this versatile component and optimize the performance of your systems. Remember to focus on your specific application requirements, consider material properties, and prioritize precision manufacturing to achieve the best results. Contact Welleshaft today to discuss your project and experience the difference that quality and expertise can make.