Powder Sintering: Advanced Techniques for High-Quality Metal Components
Powder sintering is a transformative process in the world of metal manufacturing, offering a unique combination of efficiency, precision, and quality. As industries evolve and demand for high-performance components grows, powder sintering has emerged as a crucial technique. This article delves into the advanced techniques of powder sintering, exploring its applications, benefits, and the role of Welleshaft as a trusted global supplier and contract manufacturer in this field.
Section 1: Understanding Powder Sintering
Powder sintering is a process that involves heating powdered materials below their melting point to fuse them into a solid mass. This technique is integral in manufacturing high-quality metal components with precise dimensions and enhanced material properties. The powder sintering process can be applied to a wide range of materials, including metals, ceramics, and composites.
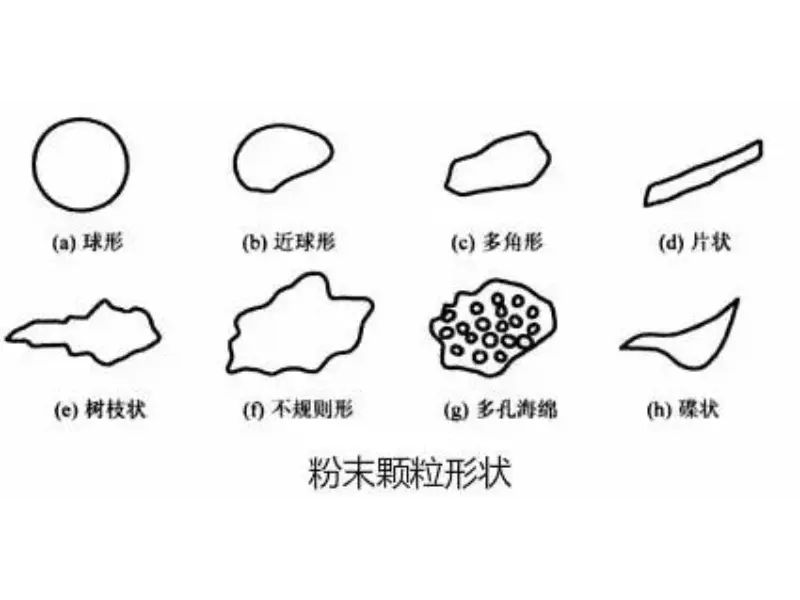
Section 2: The Pressing and Sintering Process
The pressing and sintering process is the backbone of powder metallurgy. It begins with the compaction of metal powders into a desired shape using a press. This compacted form is then subjected to a controlled sintering process, where it is heated in a furnace. The sintering temperature is carefully controlled to allow diffusion between the powder particles, leading to densification and the formation of a solid component.
Key Steps in the Sintering Process:
- Powder Preparation:Selecting and preparing the appropriate powder mix.
- Pressing:Compacting the powder into a desired shape.
- Sintering:Heating the compacted form in a furnace below its melting point.
- Cooling: Gradual cooling to retain the component’s properties.
- Finishing:Additional machining or surface treatments, if necessary.
Types of Sintering Processes
There are various types of sintering processes, each tailored to specific material requirements and applications:
- Solid-State Sintering: Involves the bonding of particles without melting. This method is commonly used for metals and ceramics.
- Liquid-Phase Sintering:Involves the presence of a liquid phase that enhances particle bonding. This method is often used for composite materials.
- Pressure-Assisted Sintering: This method applies external pressure during sintering, leading to higher density and improved mechanical properties.
Powder Sintering Techniques and Models
Powder sintering techniques have evolved significantly, offering advanced methods for producing high-quality components:
- Powder Sintering Diagram:Diagrams are used to illustrate the sintering process, providing insights into temperature profiles, phase transformations, and densification behavior.
- Powder Sintering Titanium:Titanium is a popular material for powder sintering due to its high strength-to-weight ratio and corrosion resistance. Sintering titanium requires precise control of temperature and atmosphere to prevent oxidation and maintain material integrity.
- Powder Sintering Models: Computational models are used to simulate the sintering process, predicting microstructural evolution, densification rates, and residual stresses. These models help optimize sintering parameters for specific applications.
- Sintering Method Powder: Different sintering methods, such as microwave sintering and spark plasma sintering, have been developed to enhance the efficiency and quality of the sintering process.
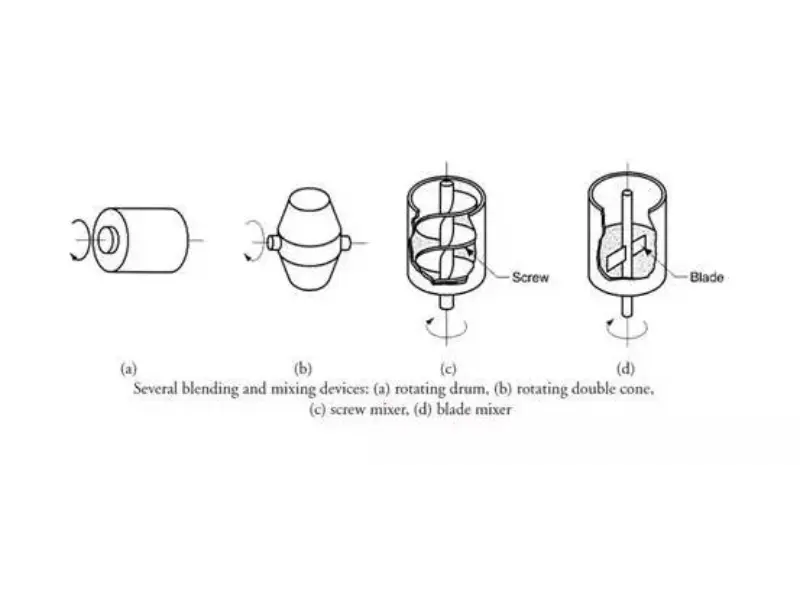
Section 3: The Role of Sintering Temperature
Sintering temperature is a critical parameter that influences the final properties of the sintered component. The choice of sintering temperature depends on the material and desired properties. For example, sintering ceramics often requires higher temperatures than sintering metals due to their higher melting points.
Effects of Sintering Temperature:
- Low Temperature: May result in incomplete bonding and high porosity.
- High Temperature:Can lead to grain growth and reduced mechanical strength.
- Optimal Temperature: Achieves the desired balance between densification and material properties.
Section 4: Sintering Process in 3D Printing
Powder sintering has also found its place in additive manufacturing, particularly in 3D printing. The powder sintering process in 3D printing involves selectively fusing powdered material layer by layer using a laser or electron beam. This technique allows for the production of complex geometries with high precision.
Benefits of Powder Sintering in 3D Printing:
- Design Flexibility: Ability to produce intricate designs and lightweight structures.
- Material Efficiency: Minimizes material waste by using only the required amount of powder.
- Customization: Enables the production of customized components tailored to specific applications.
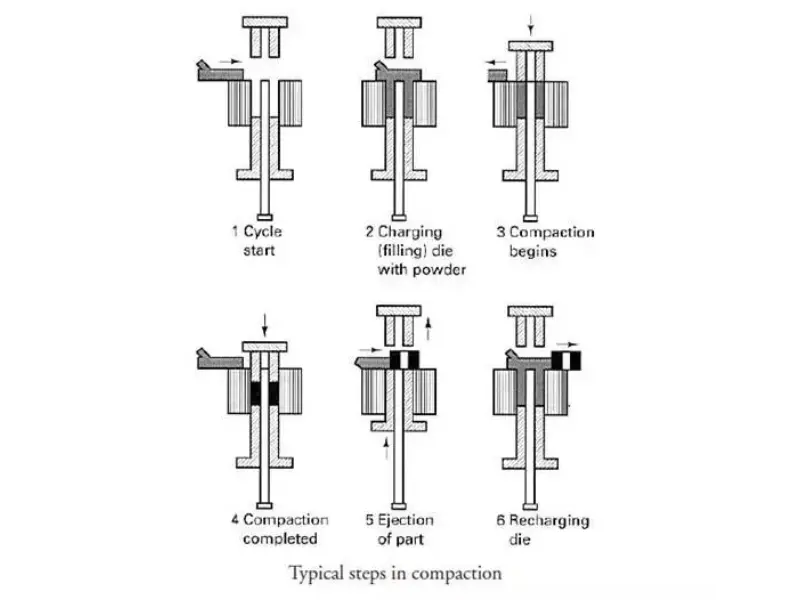
Section 5: Applications of Powder Sintering
Powder sintering is widely used in various industries, including aerospace, automotive, medical, and electronics. Its ability to produce components with high precision and tailored properties makes it an ideal choice for critical applications.
Common Applications:
- Automotive Parts:Powder sintering is used to produce gears, bearings, and engine components with high strength and wear resistance.
- Medical Implants:Sintered titanium and other biocompatible materials are used in medical implants due to their excellent mechanical properties and corrosion resistance.
- Aerospace Components: High-performance sintered materials are used in aerospace applications, where weight reduction and material integrity are crucial.
Section 6: Addressing Porosity in Powder Sintering
Porosity is a common issue in powder sintering, affecting the mechanical properties and durability of the final component. Managing porosity involves optimizing the sintering process, including temperature, pressure, and atmosphere control.
Techniques to Reduce Porosity:
- Increasing Sintering Temperature: Enhances particle bonding and reduces porosity.
- Applying Pressure:Pressure-assisted sintering techniques can significantly reduce porosity.
- Optimizing Powder Composition: Using finer powders and homogeneous mixes can reduce porosity.
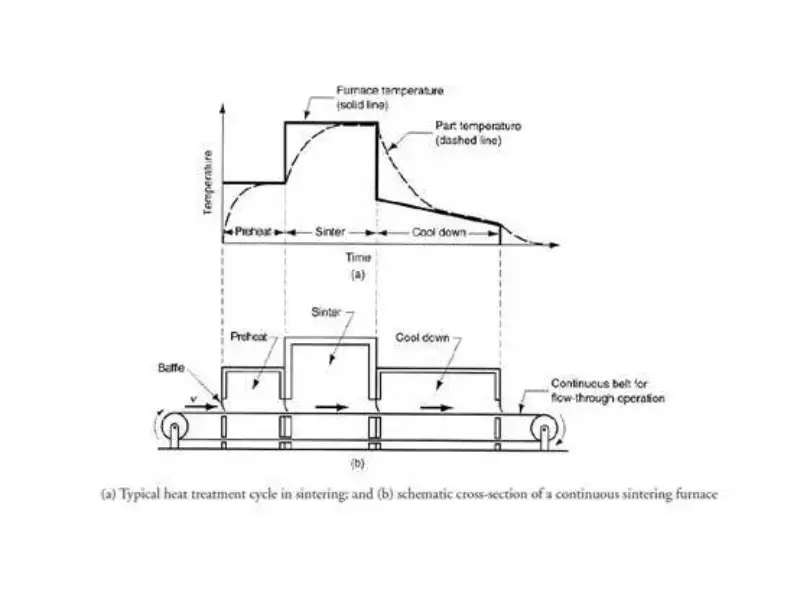
Section 7: Welleshaft: Your Trusted Global Supplier and Contract Manufacturer
When it comes to powder sintering, choosing the right supplier is crucial for achieving high-quality results. Welleshaft stands out as a trusted global supplier and contract manufacturer with extensive experience in powder metallurgy and sintering techniques. We are committed to delivering top-notch components that meet the stringent demands of various industries.
Why Choose Welleshaft?
- Expertise:Over a decade of experience in powder sintering and metallurgy.
- Quality: Strict quality control measures to ensure superior product performance.
- Customization:Ability to tailor components to meet specific customer requirements.
- Global Reach: Serving clients across the globe with reliable supply chains and on-time delivery.
Conclusion
Powder sintering is a vital process in modern manufacturing, offering a range of advanced techniques for producing high-quality metal components. From automotive to aerospace, the applications of powder sintering are vast and varied. By understanding the intricacies of the sintering process, optimizing techniques, and partnering with trusted suppliers-Welleshaft, manufacturers can achieve exceptional results in their production endeavors.
Whether you’re looking to improve your sintering process or need a reliable partner for your next project, Welleshaft is here to help. With our expertise in powder sintering and commitment to quality, we ensure that your components are produced to the highest standards, meeting all your specifications and requirements.