Powder Injection Molding: Precision Manufacturing for Complex Components | Top PIM Solutions
Powder Injection Molding (PIM) is a groundbreaking manufacturing technique that merges the versatility of plastic injection molding with the material flexibility of powder metallurgy. This method is particularly beneficial for producing small, complex, and high-precision components from various materials, including metals and ceramics. In this article, we will delve into the powder injection molding process, its advantages, and its applications in various industries. We will also address some frequently asked questions to provide a comprehensive understanding of PIM.
Section 1: What is Powder Injection Molding?
This manufacturing process involves injecting a mixture of metal or ceramic powders and a binder into a mold to produce intricate and precise components. It combines the advantages of traditional plastic injection molding and powder metallurgy, offering a cost-effective and efficient solution for creating complex parts with tight tolerances.
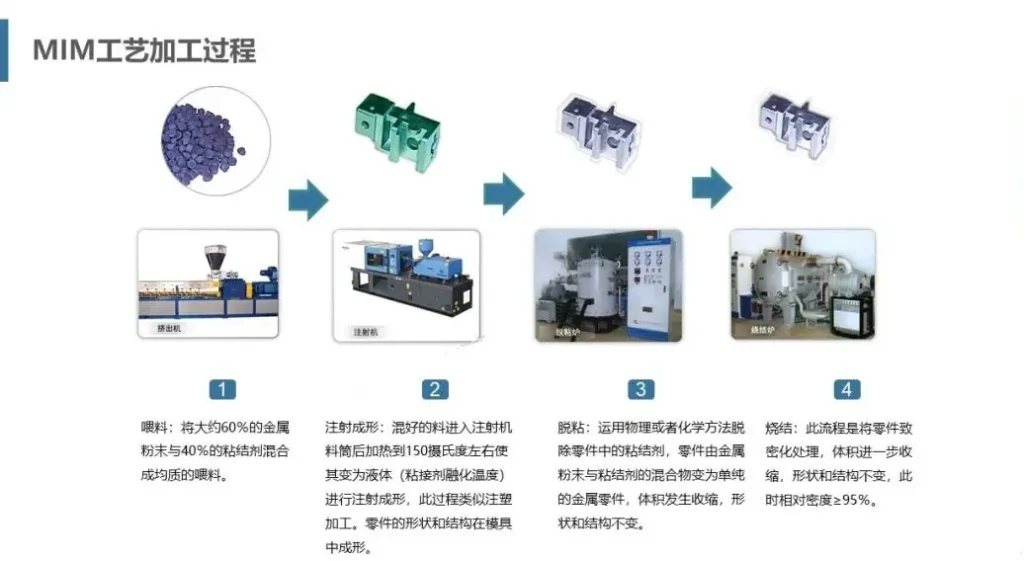
Section 2: The Powder Injection Molding Process
1. Feedstock Preparation
The PIM process begins with the preparation of the feedstock, a homogeneous mixture of fine metal or ceramic powders and a binder. The binder, typically a combination of thermoplastic and wax, helps to hold the powder particles together and provide the necessary flow characteristics for injection molding. The feedstock is compounded by mixing the powders and binder, then pelletized for use in the injection molding machine.
2. Injection Molding
The pelletized feedstock is fed into an injection molding machine, where it is heated and injected into a mold cavity under high pressure. The mold is designed to the desired shape and size of the final component. Once the feedstock fills the mold cavity, it cools and solidifies, forming a “green part.”
3. Debinding
The process then moves to debinding, where technicians remove the binder from the green part. They use methods such as thermal debinding, solvent debinding, or catalytic debinding to accomplish this. The goal is to eliminate the binder while preserving the part’s shape and structural integrity.
4. Sintering
After debinding, the remaining part, known as the “brown part,” undergoes sintering. Sintering involves heating the part to a temperature below the melting point of the material but high enough to bond the powder particles together. This process increases the density and mechanical properties of the part, resulting in a final component that is near-net shape and has high structural integrity.
5. Post-Processing
Depending on the application and required specifications, the sintered parts may undergo additional post-processing steps, such as machining, surface treatment, or heat treatment, to achieve the desired properties and finish.
For more information on high-quality Powder Injection Molding Manufacturer and to find the perfect solution for your application, please contact us.
Jinan Welle Metal Products Co., Ltd (Welleshaft)
Website: www.welleshaft.com
Email: [email protected]
Phone: +86-156-5017-9596
Explore our range of durable and reliable PIM Parts today!
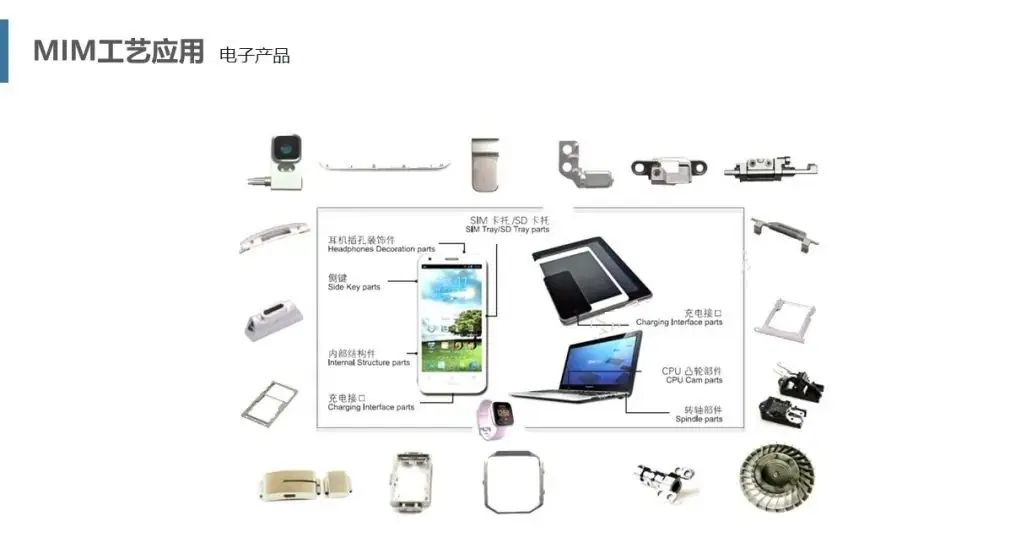
Section 3: Advantages of Powder Injection Molding
1. Complex Geometries
PIM allows for the production of highly complex and intricate geometries that are difficult or impossible to achieve with traditional manufacturing methods. This capability is particularly advantageous for industries requiring precise and detailed components, such as aerospace, medical, and electronics.
2. Material Versatility
PIM can be used with a wide range of materials, including metals, ceramics, and composites. This versatility makes it suitable for various applications and industries, from automotive components to medical implants.
3. High Precision and Tolerances
The PIM process can produce parts with tight tolerances and high precision, ensuring consistent quality and performance. This level of accuracy is crucial for applications where reliability and functionality are paramount.
4. Cost-Effective for Large Production Runs
PIM is a cost-effective manufacturing method for large production runs, as it allows for the mass production of complex parts with minimal material waste. The process also reduces the need for extensive machining and finishing, further lowering production costs.
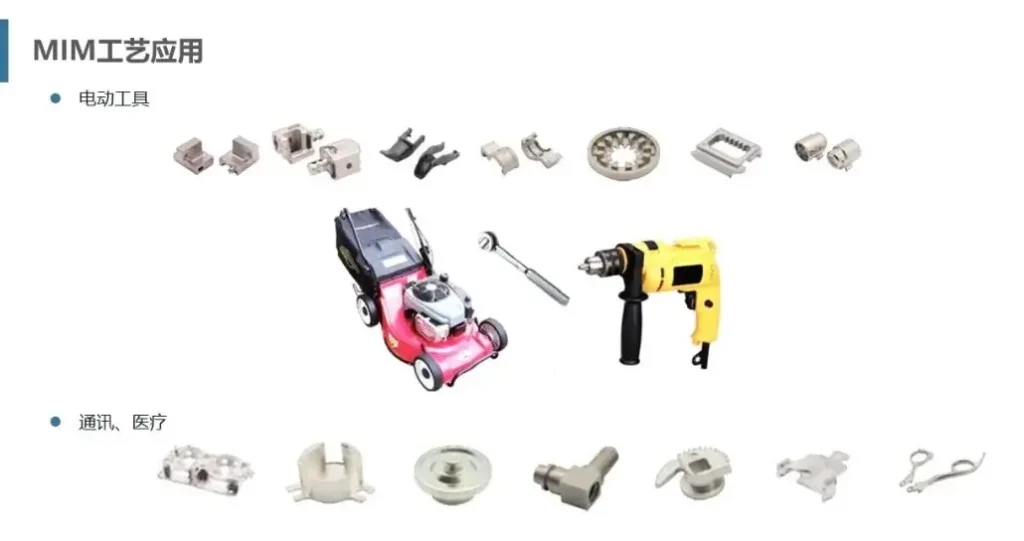
Section 4: Applications of Powder Injection Molding
Powder Injection Molding is used in various industries to manufacture components that require high precision, complexity, and material performance. Some notable applications include:
1. Automotive
In the automotive industry, PIM is used to produce intricate and high-performance components such as fuel injectors, turbocharger parts, and sensor housings. The ability to create complex shapes and meet stringent quality standards makes PIM an ideal choice for automotive applications.
2. Medical
PIM is widely used in the medical field to manufacture surgical instruments, dental implants, and orthopedic devices. The process enables the production of biocompatible and corrosion-resistant parts with intricate geometries and precise dimensions.
3. Aerospace
The aerospace industry relies on PIM for producing lightweight and high-strength components, such as turbine blades, brackets, and fasteners. The process’s ability to achieve complex shapes and high precision is essential for aerospace applications.
4. Electronics
In the electronics industry, PIM is used to manufacture connectors, housings, and other components that require miniaturization and high precision. The process’s capability to produce small, intricate parts makes it suitable for electronic applications.
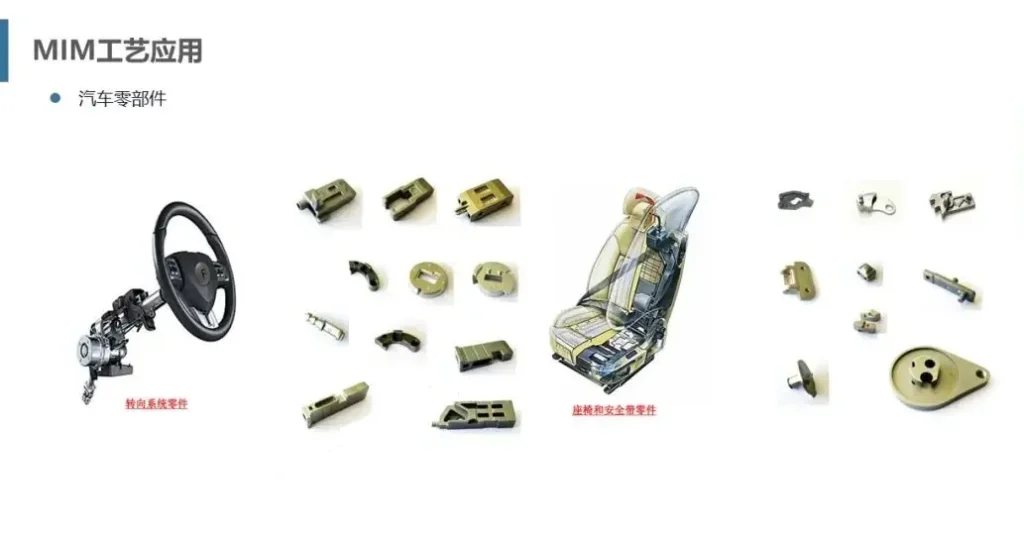
Section 5: FAQs about Powder Injection Molding
1.What is the Process of Powder Injection Molding?
The process of Powder Injection Molding involves preparing a feedstock mixture of metal or ceramic powders and a binder, injecting the mixture into a mold to form a green part, removing the binder through debinding, and sintering the part to achieve the final component. Post-processing steps may be applied as needed.
2.What is Powder Injection?
Powder Injection refers to the technique of injecting a mixture of powders and a binder into a mold to create complex and precise components. It is a key step in the Powder Injection Molding process.
3.What is the Difference Between Powder Injection Molding and Metal Injection Molding?
This manufacturing category includes both Metal Injection Molding (MIM) and Ceramic Injection Molding (CIM). MIM specifically involves using metal powders, while CIM uses ceramic powders. Both processes follow similar steps but differ in the materials used and their respective applications.
4.What is Molding Powder?
Molding powder refers to the fine metal or ceramic powders used in the Powder Injection Molding process. These powders are combined with a binder to form the feedstock that is injected into molds to create complex components.
Section 6: Leading Powder Injection Molding Manufacturers
Several manufacturers specialize in this advanced manufacturing technique, offering expertise and capabilities for producing high-quality components. Some of the leading companies in this field include:
- Advanced Powder Products (APP)
- Indo-MIM
- CMG Technologies
- Parmaco Metal Injection Molding
- Welle Powder Metallury (Welleshaft)
- GKN Powder Metallurgy
These manufacturers provide a wide range of PIM solutions, from prototyping to large-scale production, catering to various industries and applications.
Conclusion
This versatile and efficient manufacturing method enables the production of complex and precise components from a variety of materials. With its ability to create intricate geometries, maintain high precision, and offer material flexibility, it serves as a valuable solution for industries requiring advanced manufacturing capabilities. Whether for automotive, medical, aerospace, or electronics applications, this process delivers top-tier solutions for precision manufacturing needs.
For more information on how Powder Injection Molding can benefit your specific application, consider reaching out to welleshaft who can provide tailored solutions and expertise.