Powder Compaction: Expert Techniques & High-Quality Solutions for Optimal Results
In the manufacturing industry, powder compaction plays a crucial role in shaping and forming materials with precision. This technique is widely used in various sectors, including automotive, aerospace, electronics, and more, to create components with complex geometries and high strength. Understanding the nuances of powder compaction and employing the right techniques can lead to significant improvements in product quality and manufacturing efficiency.
In this article, we will delve into the essentials of powder compaction, explore the various methods used, and highlight how partnering with a trusted global supplier like Welleshaft can elevate your manufacturing capabilities.
Section 1: What is Powder Compaction?
Powder compaction is the process of compressing powder particles into a solid form using high pressure. This technique is essential in producing high-density, uniform parts that meet specific dimensional and structural requirements. The process is widely used in powder metallurgy, ceramics, pharmaceuticals, and other industries where precision and consistency are critical.
1.1. Understanding Compaction of Metal Powder
The compaction of metal powder is a critical process in powder metallurgy. The goal is to achieve the desired density and mechanical properties in the final part. Factors such as particle size, shape, and material composition play a significant role in the compaction process. Proper control of these factors ensures that the compacted metal powder meets the required specifications for strength, durability, and performance.
1.2. Powder Pressing: Precision and Efficiency in Manufacturing
Powder pressing is a widely used method for producing parts with high precision and efficiency. This technique is particularly effective for high-volume production, where consistency and repeatability are critical. By carefully controlling the powder pressing parameters, manufacturers can produce parts with tight tolerances and excellent surface finish.
1.3. The Powder Compaction Process
The powder compaction process involves several key steps:
- Powder Preparation: The first step is the preparation of the powder, which includes selecting the right material, ensuring particle size uniformity, and sometimes adding binders or lubricants to improve flowability and compaction.
- Compaction: The powder is placed in a die or mold, where it is subjected to high pressure using a powder compaction press. The pressure applied compresses the powder particles, causing them to bond together and form a solid mass.
- Sintering: After compaction, the compacted powder, also known as a “green compact,” is heated in a controlled atmosphere. This process, called sintering, strengthens the part by bonding the particles more firmly together.
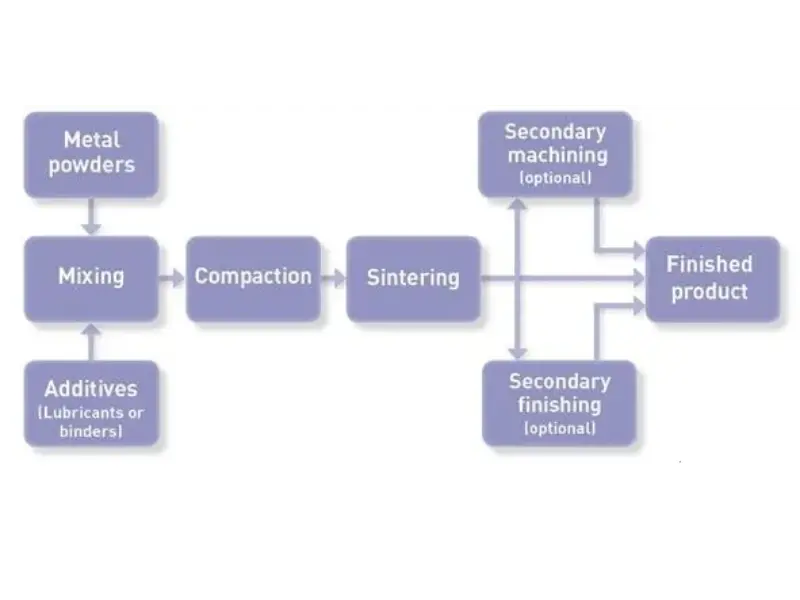
Section 2: Techniques for Powder Compaction
Powder compaction is a critical process in various industries, and selecting the right technique can significantly impact the quality, strength, and performance of the final product. Below are some of the most common and effective techniques used in powder compaction:
1. Cold Isostatic Pressing (CIP)
Cold Isostatic Pressing (CIP) is a method where powder is placed in a flexible mold, which is then immersed in a pressurized liquid medium. Pressure is applied uniformly from all directions, resulting in a compact with consistent density and strength throughout. This technique is especially useful for:
- Complex Shapes:CIP can handle intricate geometries that are difficult to achieve with traditional pressing methods.
- Large Parts: This technique is ideal for producing large components without the risk of density variations.
- Uniform Density:CIP ensures that pressure is applied evenly, minimizing internal stresses and defects.
Applications: CIP is widely used in the production of ceramics, metal parts, and other materials where uniform density is critical.
2. Isostatic Compaction
Isostatic compaction can be performed at both room temperature (CIP) and elevated temperatures (Hot Isostatic Pressing or HIP). In this technique, the powder is subjected to uniform pressure from all directions, similar to CIP, but with the option to apply heat for specific material requirements.
Hot Isostatic Pressing (HIP): When performed at elevated temperatures, HIP can further enhance the material’s properties by eliminating pores and improving mechanical strength. HIP is often used for materials that require high performance and reliability, such as aerospace components and medical implants.
Advantages:
- Consistent Material Properties:Isostatic compaction produces parts with uniform density and mechanical properties, essential for high-performance applications.
- Versatility:Suitable for a wide range of materials, including metals, ceramics, and composites.
Applications: Isostatic compaction is commonly used in the manufacturing of high-performance components in the aerospace, automotive, and medical industries.
3. Mechanical Pressing
Mechanical pressing is one of the most commonly used techniques for powder compaction, particularly in high-volume production. In this method, powder is placed in a rigid die, and a mechanical press applies pressure to compact the powder into the desired shape.
- Simple Geometries: Mechanical pressing is best suited for producing simple, symmetrical shapes such as gears, bearings, and other structural components.
- High Volume Production: This method is highly efficient for mass production, offering consistency and repeatability.
Advantages:
- Cost-Effective:Ideal for large-scale production, mechanical pressing offers a cost-effective solution for manufacturing high volumes of parts.
- Precision:Capable of achieving tight tolerances and excellent surface finishes.
Applications: Mechanical pressing is widely used in the automotive, electronics, and consumer goods industries for producing a variety of metal and ceramic components.
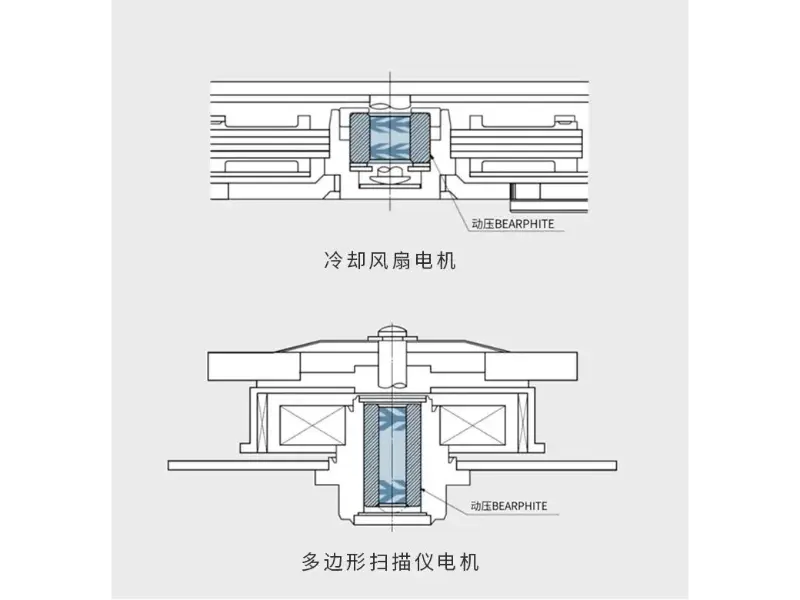
4. Hot Pressing
Hot pressing combines the application of heat and pressure simultaneously to compact powder materials. This technique is often used for materials that require enhanced bonding and mechanical properties, such as ceramics and composite materials.
- Enhanced Material Properties: The combination of heat and pressure allows for better particle bonding, resulting in stronger and more durable parts.
- Reduced Sintering Time: Hot pressing can reduce or eliminate the need for subsequent sintering, as the heat applied during pressing promotes particle diffusion.
Advantages:
- High Strength and Density:Hot pressing produces parts with superior mechanical properties and high density, making it suitable for demanding applications.
- Versatility: Suitable for a wide range of materials, including refractory metals, ceramics, and composites.
Applications: Hot pressing is commonly used in the production of high-performance components for the aerospace, defense, and electronics industries.
5. Spark Plasma Sintering (SPS)
Spark Plasma Sintering (SPS) is an advanced technique that uses a pulsed electric current along with pressure to compact powder materials. This method allows for rapid heating and cooling, enabling the production of parts with fine microstructures and enhanced properties.
- Rapid Processing:SPS significantly reduces processing time compared to traditional sintering methods, making it ideal for producing high-performance parts quickly.
- Fine Microstructures: The rapid heating and cooling cycles in SPS help preserve the fine microstructure of the material, leading to improved mechanical properties.
Advantages:
- Enhanced Material Properties: SPS produces parts with superior hardness, toughness, and wear resistance.
- Energy Efficiency: The process is highly energy-efficient, as it minimizes the time and energy required for sintering.
Applications: SPS is used in the production of advanced materials, including nanomaterials, ceramics, and composite materials for high-tech applications.

Section 3: Compaction of Powder Particles: Key Considerations
The compaction of powder particles is a critical process in manufacturing, influencing the density, strength, and overall quality of the final product. Whether you’re working with metals, ceramics, or other materials, understanding the key considerations in powder compaction is essential for achieving optimal results. Below, we explore the most important factors to consider when compacting powder particles.
1. Particle Size and Distribution
Particle size and distribution play a crucial role in the compaction process. The size of the particles affects the packing density, which in turn influences the porosity and strength of the compacted material.
Fine Particles: Smaller particles tend to pack more closely, leading to higher density and lower porosity. However, they may also lead to increased friction between particles, requiring higher compaction pressure.
Coarse Particles: Larger particles typically result in higher porosity but require less pressure to compact. The use of a blend of particle sizes can optimize packing density and improve the final product’s properties.
Consideration: It’s essential to select the right particle size distribution to balance density and ease of compaction. A well-graded mix can minimize voids and enhance the mechanical properties of the final product.
2. Material Composition
The composition of the powder significantly affects the compaction behavior. Different materials have varying degrees of plasticity, hardness, and compressibility, all of which impact how the powder particles behave under pressure.
Metal Powders: Metals with higher ductility, like aluminum and copper, compact more easily and achieve higher densities. Harder metals, like tungsten, may require higher pressures and specialized equipment.
Ceramic Powders: Ceramic materials are generally more brittle, making them less compressible. Special techniques, like isostatic pressing, may be necessary to achieve uniform compaction.
Consideration: Understanding the material properties is crucial in selecting the right compaction technique and parameters. For instance, adding binders or lubricants can enhance the compactibility of some materials.
3. Compaction Pressure
Compaction pressure is a critical factor in determining the density and strength of the final compact. The pressure must be carefully controlled to ensure that the particles bond effectively without causing defects like cracking or lamination.
High Pressure: Applying higher pressure generally leads to higher density and stronger bonds between particles. However, excessive pressure can cause particle deformation, leading to defects.
Low Pressure: Lower pressure may not sufficiently bond the particles, resulting in a compact with lower density and mechanical strength.
Consideration: It’s important to find the optimal pressure that achieves the desired density and strength without introducing defects. The material type and particle size distribution should guide the selection of pressure.
4. Lubrication and Binders
Lubricants and binders are often added to the powder mixture to facilitate the compaction process and improve the quality of the final product.
Lubricants: These reduce friction between particles and between the powder and the die walls, making it easier to achieve uniform compaction and release the compact from the mold.
Binders: Binders help hold the particles together after compaction, particularly for materials that don’t bond easily. They ensure the integrity of the compact during handling and subsequent processing.
Consideration: The type and amount of lubricants and binders must be carefully selected to avoid negative impacts on the final product’s properties, such as reducing density or causing contamination.
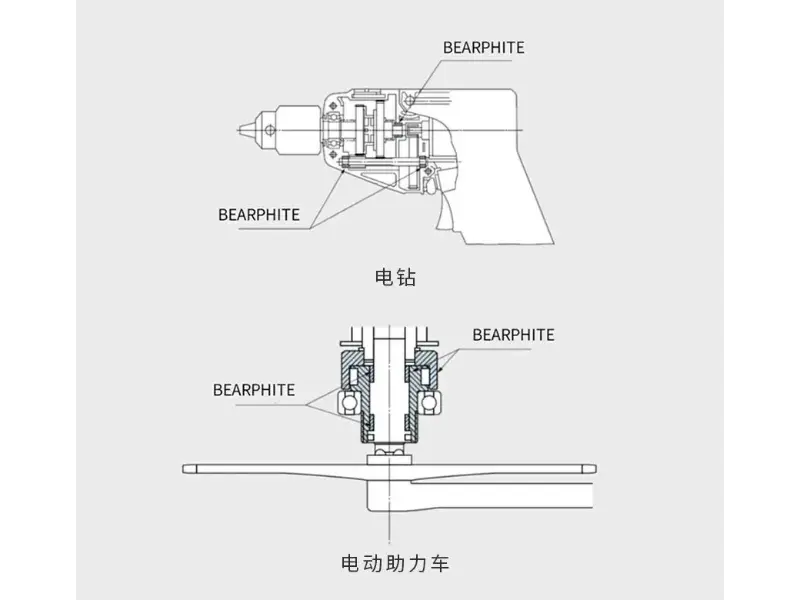
5. Compaction Technique
The choice of compaction technique is one of the most important considerations. Different methods offer varying advantages depending on the material and the desired properties of the final product.
Cold Isostatic Pressing (CIP): Best for achieving uniform density in complex shapes and large parts.
Hot Isostatic Pressing (HIP): Ideal for materials that benefit from both heat and pressure, resulting in enhanced material properties.
Mechanical Pressing: Suitable for high-volume production of simple shapes with consistent quality.
Consideration: The selection of the compaction technique should align with the material properties, production volume, and desired characteristics of the final product.
6. Powder Flowability
Powder flowability refers to the ability of the powder particles to flow and fill the die or mold uniformly. Good flowability ensures consistent compaction and uniform density throughout the part.
Improving Flowability: The flowability can be enhanced by optimizing particle size distribution, adding flow agents, or adjusting the moisture content.
Challenges: Poor flowability can lead to segregation, uneven filling, and ultimately defects in the compacted part.
Consideration: Monitoring and optimizing powder flowability is crucial, especially in high-volume production where consistency is key.
7. Temperature Control
Temperature plays a significant role in powder compaction, particularly in processes like hot pressing or hot isostatic pressing. The temperature can affect the material’s plasticity, particle bonding, and overall compaction efficiency.
Cold Compaction: Typically requires higher pressure to achieve the desired density, as the particles are less plastic at lower temperatures.
Hot Compaction: Allows for better particle bonding and higher density with lower pressure, but requires careful control to avoid thermal stresses and defects.
Consideration: The choice between cold and hot compaction depends on the material and the desired properties of the final product. Temperature control is critical to achieving consistent quality.
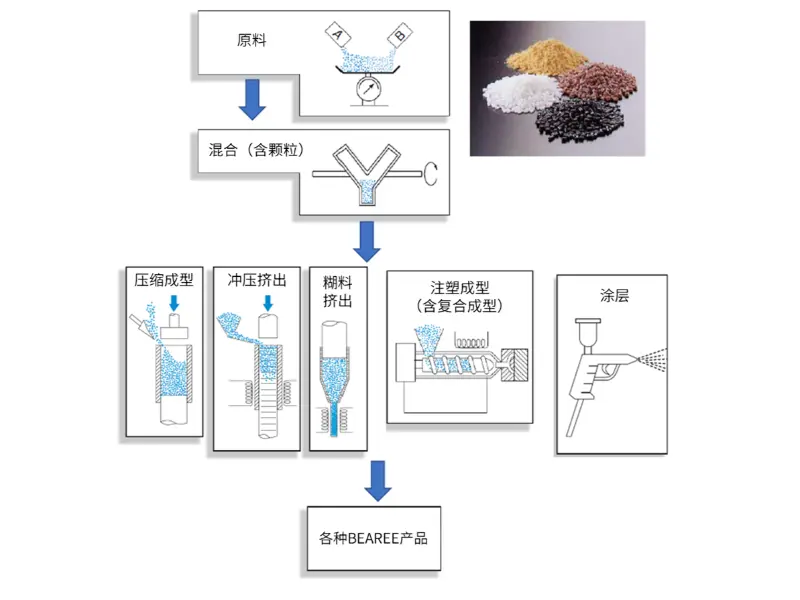
Section 4: Frequently Asked Questions
1. What is the Meaning of Compacted Powder?
Compacted powder refers to powder particles that have been compressed into a solid form through the application of pressure. This process transforms the loose powder into a dense, coherent mass with improved mechanical properties. Compacted powder is used in various applications, including powder metallurgy, ceramics, and pharmaceuticals, where the material’s strength and integrity are essential.
2. What is the Use of Powder Compaction?
The primary use of powder compaction is to produce parts with specific shapes and mechanical properties that are difficult to achieve through other manufacturing methods. Powder compaction allows for the production of complex geometries, high-density parts, and materials with tailored properties. This process is widely used in industries such as automotive, aerospace, electronics, and medical devices.
3. How Do You Compact Powder?
The process of compacting powder involves placing the powder in a die or mold and applying pressure to compress the particles into a solid mass. The key to successful powder compaction is controlling the pressure, particle size, and material composition to achieve the desired density and mechanical properties. After compaction, the part is typically sintered to enhance its strength and durability.
4. Why Choose Welleshaft for Your Powder Compaction Needs?
When it comes to powder compaction, partnering with a trusted supplier is essential to achieving the best results. Welleshaft is a global leader in the manufacturing and supply of high-quality powder compaction solutions. With years of experience and expertise, Welleshaft offers a wide range of services, including:
- Custom Powder Compaction Solutions:Tailored to meet your specific requirements, ensuring optimal performance and quality.
- Advanced Manufacturing Techniques:Utilizing state-of-the-art equipment and processes to deliver precision-engineered parts.
- Global Supply Chain: Ensuring timely delivery and support, no matter where you are located.
- Expert Technical Support:Providing guidance and assistance throughout the compaction process, from material selection to final production.
Conclusion
Powder compaction is a critical process in modern manufacturing, enabling the production of high-density, complex parts with superior mechanical properties. By understanding the various techniques and factors involved, manufacturers can optimize their processes and achieve the best results. Partnering with a trusted supplier like Welleshaft ensures access to expert knowledge, advanced technologies, and high-quality materials, helping you achieve optimal results in your powder compaction projects.
For more information on how Welleshaft can support your powder compaction needs, visit our website or contact our team of experts today. Let us help you take your manufacturing to the next level with our top-tier solutions and services.