Porous Alumina Membranes: High-Performance Filters & Separators
Introduction
In the realm of advanced materials and engineering, porous alumina membranes have emerged as a leading solution for high-performance filtration and separation processes. Their unique combination of chemical inertness, thermal stability, controlled pore size, and mechanical strength makes them ideal for a wide array of applications across various industries. This article delves into the world of porous alumina membranes, exploring their properties, processing technologies, applications, and the benefits they offer over traditional filtration methods.
What are Porous Alumina Membranes?
Porous alumina membranes are thin films or structures composed of aluminum oxide (Al₂O₃) with a controlled network of interconnected pores. The porosity, pore size, and pore distribution are carefully engineered during the manufacturing process to achieve specific filtration and separation characteristics. These membranes are renowned for their ability to selectively separate molecules and particles based on size, charge, or other properties.
Key Properties of Porous Alumina Membranes
High Chemical Resistance: Alumina is chemically inert to a wide range of solvents, acids, and bases, making these membranes suitable for harsh chemical environments.
Thermal Stability: Porous alumina membranes can withstand high temperatures without significant degradation, making them ideal for high-temperature filtration and separation processes.
Controlled Pore Size: The pore size can be precisely controlled during manufacturing, allowing for selective separation of molecules and particles within a specific size range. Common pore sizes range from nanometers to micrometers.
Mechanical Strength: Alumina is a hard and durable material, providing excellent mechanical strength and resistance to pressure and abrasion.
Biocompatibility: Alumina is biocompatible, making these membranes suitable for medical and pharmaceutical applications.
High Surface Area: The porous structure provides a high surface area for adsorption and catalytic activity.
Comparison of Alumina Membrane Characteristics
Property | Typical Value | Unit | Importance |
Pore Size | 2 nm – 10 μm | nm, μm | Dictates the size of particles/molecules that can be filtered. |
Porosity | 20 – 70% | % | Affects flow rate and membrane capacity. |
Thickness | 10 μm – 1 mm | μm, mm | Influences mechanical strength and pressure drop. |
Chemical Resistance | Resistant to most acids, bases, and solvents | – | Determines compatibility with the fluid being filtered. |
Thermal Stability | Up to 1000 °C | °C | Allows for use in high-temperature applications. |
Mechanical Strength | Varies; generally high | MPa | Determines the membrane’s ability to withstand pressure and mechanical stress. |
Water Permeability | Varies depending on pore size and porosity | L/m²/hr/bar | Measure the flow rate through the membrane. |
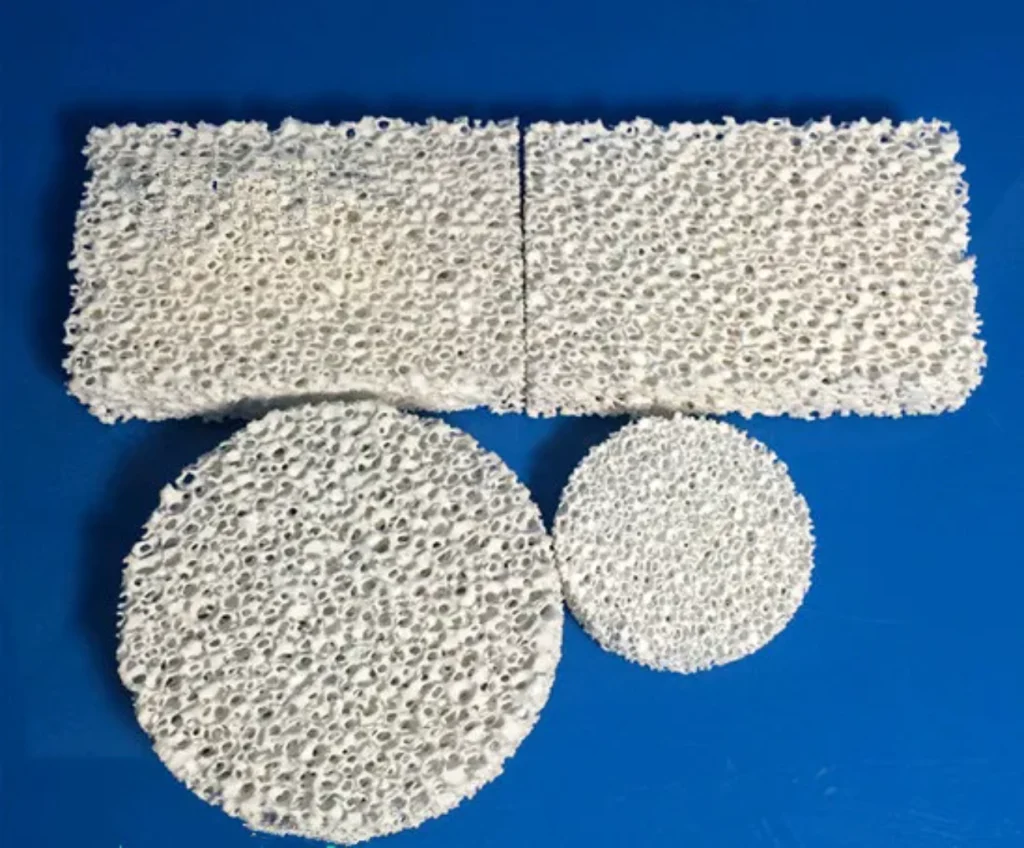
Processing Technologies for Porous Alumina Membranes
Several techniques are employed to manufacture porous alumina membranes, each offering varying degrees of control over pore size, pore structure, and membrane properties.
Anodization: This is a widely used technique for creating ordered arrays of pores in alumina. By anodizing aluminum in acidic electrolytes, a self-organized porous structure forms on the surface. The pore size and interpore distance can be controlled by adjusting the anodization parameters, such as voltage, electrolyte type, and temperature.
Sol-Gel Processing: This method involves the formation of a sol (a colloidal suspension of solid particles in a liquid) followed by gelation and drying. By carefully controlling the sol-gel chemistry and drying process, porous alumina membranes with tailored pore structures can be produced.
Sintering: This is a traditional method for producing porous ceramics. Alumina powder is compacted and then heated to a high temperature, causing the particles to fuse together and form a porous structure.
Phase Inversion: This technique is commonly used to produce polymeric membranes, but it can also be adapted for alumina membranes. A mixture of alumina powder, a solvent, and a polymer is cast as a thin film, and then immersed in a non-solvent, causing phase separation and the formation of a porous structure.
Table of Manufacturing Parameter Influences:
Parameter | Effect on Pore Size | Effect on Porosity | Effect on Mechanical Strength |
Anodization Voltage | Increases | Increases | Decreases |
Sintering Temperature | Increases | Decreases | Increases |
Sol-Gel Concentration | Decreases | Decreases | Increases |
Processing Accuracy and Dimensional Tolerances
The accuracy and dimensional tolerances of porous alumina membranes depend on the manufacturing process used. Anodization offers the highest degree of control over pore size and pore arrangement, allowing for the creation of highly ordered structures with nanometer-scale features. Sol-gel processing and sintering offer less precise control but can be used to produce larger-scale membranes with a wider range of pore sizes. Dimensional tolerances typically range from a few nanometers for anodized membranes to several micrometers for sintered membranes.
Material Composition and Mechanical Properties
Porous alumina membranes are typically composed of high-purity aluminum oxide (Al₂O₃) with minimal impurities. The mechanical properties of the membranes depend on the porosity, pore size, and microstructure. Generally, porous alumina membranes exhibit high compressive strength and hardness but are more susceptible to tensile stress.
Compressive Strength: 100-500 MPa (depending on porosity)
Tensile Strength: 20-100 MPa (depending on porosity)
Hardness (Vickers): 10-15 GPa
Specifications and Industry Applications
Porous alumina membranes are available in various specifications to meet the needs of different applications. Common specifications include:
Pore Size: 2 nm to 10 μm
Membrane Thickness: 10 μm to 1 mm
Membrane Diameter: 10 mm to 300 mm
Porosity: 20% to 70%
Industry applications for porous alumina membranes include:
Water Treatment: Filtration of bacteria, viruses, and other contaminants from water.
Chemical Processing: Separation of chemicals, solvents, and catalysts.
Biotechnology: Filtration of proteins, viruses, and cells.
Pharmaceuticals: Sterilization of pharmaceutical products and separation of drug molecules.
Microelectronics: Fabrication of microchips and other electronic devices.
Energy: Gas separation, fuel cell membranes.
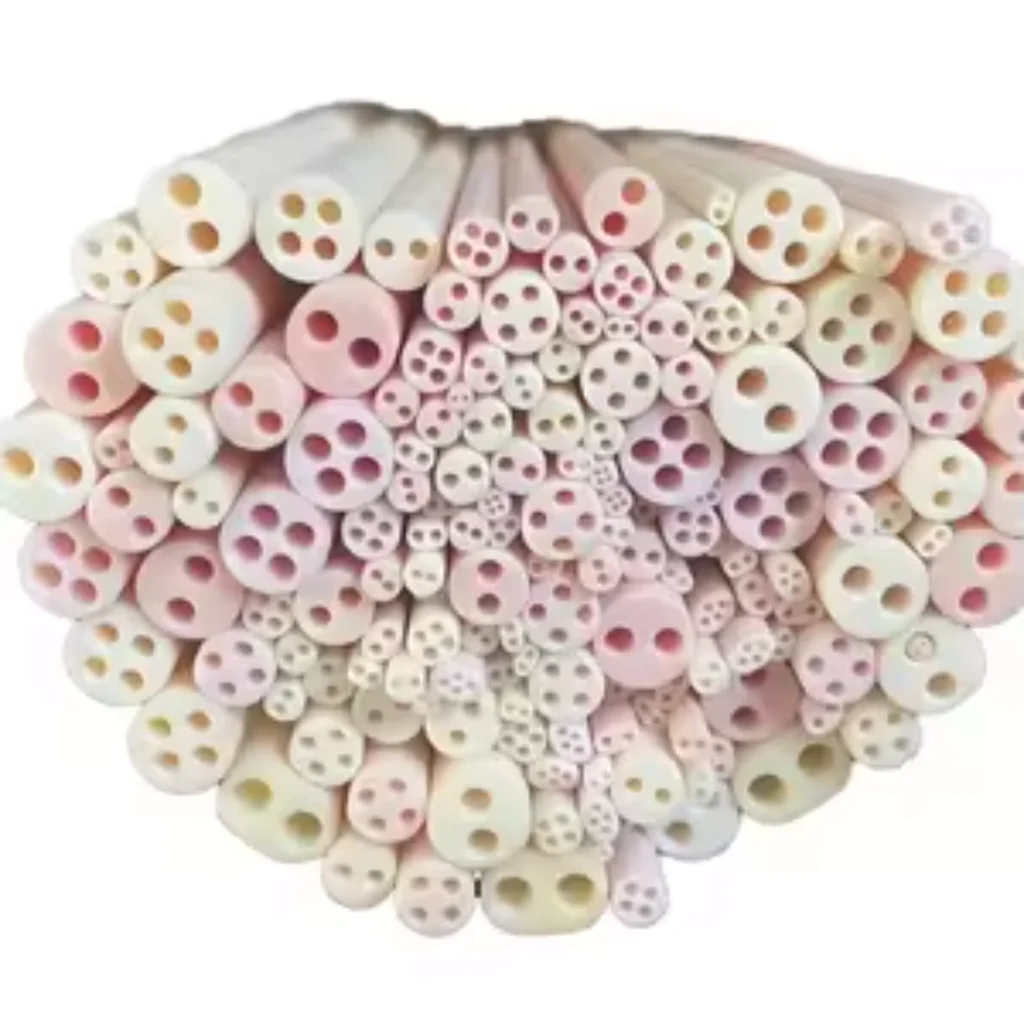
Processing Capacity
The processing capacity for porous alumina membranes varies depending on the manufacturing process and the size of the membrane. Anodization is typically used to produce small-scale membranes with highly ordered pore structures, while sol-gel processing and sintering can be scaled up to produce larger volumes of membranes.
Advantages of Porous Alumina Membranes over Traditional Filtration Methods
Porous alumina membranes offer several advantages over traditional filtration methods, such as polymeric membranes and woven filters. These advantages include:
Higher Chemical Resistance: Alumina is resistant to a wider range of chemicals than most polymers, making it suitable for harsh chemical environments.
Higher Thermal Stability: Alumina can withstand higher temperatures than most polymers, making it ideal for high-temperature filtration processes.
More Precise Pore Size Control: Anodization allows for more precise control over pore size than traditional methods, enabling more selective separation of molecules and particles.
Greater Mechanical Strength: Alumina is stronger and more durable than most polymers, providing greater resistance to pressure and abrasion.
Longer Lifespan: Porous alumina membranes typically have a longer lifespan than traditional filtration methods due to their superior chemical and thermal stability.
Why Choose Welleshaft as Your Porous Alumina Membrane Supplier?
Welleshaft stands out as a trusted global supplier and contract manufacturer of advanced materials, including high-quality porous alumina membranes. With decades of experience in materials science and manufacturing, Welleshaft offers:
Customized Solutions: Welleshaft can tailor porous alumina membranes to meet your specific requirements, including pore size, membrane thickness, and material composition.
High-Quality Materials: Welleshaft uses only the highest-purity alumina powders and advanced manufacturing techniques to ensure the quality and performance of its membranes.
Expert Technical Support: Welleshaft’s team of experienced engineers and scientists can provide expert technical support to help you select the right membrane for your application and optimize your filtration process.
Competitive Pricing: Welleshaft offers competitive pricing on its porous alumina membranes, making them an affordable solution for a wide range of applications.
Global Reach: Welleshaft has a global network of distributors and sales representatives, making it easy to access its products and services worldwide.
Choosing Welleshaft as your porous alumina membrane supplier ensures you receive high-quality products, expert support, and customized solutions tailored to your specific needs.
Conclusion
Porous alumina membranes have revolutionized filtration and separation processes across various industries. Their unique combination of chemical resistance, thermal stability, controlled pore size, and mechanical strength makes them the ideal solution for demanding applications. As technology continues to advance, porous alumina membranes will play an increasingly important role in addressing critical challenges in water treatment, chemical processing, biotechnology, pharmaceuticals, and many other fields. With reputable suppliers like Welleshaft leading the way, the future of porous alumina membrane technology is bright.