Nitriding Methods: Gas, Salt Bath, & Plasma – Advanced Steel Treatment
Nitriding is a heat treatment process used to increase the surface hardness, wear resistance, and fatigue strength of steel parts. It involves diffusing nitrogen into the surface of the metal at elevated temperatures, creating a hard, wear-resistant layer known as the case. Unlike some other surface hardening methods, nitriding doesn’t require quenching, minimizing distortion. This makes it ideal for precision components. In this comprehensive guide, we’ll delve into the different nitriding methods – gas nitriding, salt bath nitriding, and plasma nitriding – exploring their principles, advantages, disadvantages, and applications.
Section 1 Why Nitriding? The Benefits of Nitrogen Enrichment
Before diving into the specifics of each method, it’s important to understand the benefits that nitriding offers:
1.1 Increased Surface Hardness: Nitriding significantly increases the surface hardness of steel, making it more resistant to scratching, abrasion, and indentation.
1.2 Improved Wear Resistance: The hard nitride layer reduces friction and wear, extending the service life of components.
1.3 Enhanced Fatigue Strength: Nitriding introduces compressive residual stresses on the surface, which helps to resist crack initiation and propagation, thereby improving fatigue strength.
1.4 Corrosion Resistance: The nitride layer can provide improved corrosion resistance in certain environments.
1.5 Minimal Distortion: Since nitriding is performed at lower temperatures than other hardening processes and doesn’t require quenching, distortion is minimized.
1.6 Case Depth Control: The case depth can be precisely controlled by adjusting the nitriding parameters, allowing for customized performance.
Table: Nitriding Compared to Other Surface Hardening Methods
Feature | Nitriding | Carburizing | Induction Hardening | Hard Chrome Plating |
Hardening Mechanism | Nitrogen Diffusion | Carbon Diffusion | Phase Transformation | Coating Deposition |
Temperature | 480-590°C | 850-950°C | 800-900°C | Low (Often < 50°C) |
Distortion | Minimal | Moderate | Moderate | Minimal |
Case Depth | 0.025-1.0 mm | 0.5-2.0 mm | 1.0-5.0 mm | 0.002-0.05 mm |
Wear Resistance | Excellent | Good | Good | Excellent |
Fatigue Strength | Excellent | Good | Good | Fair |
Corrosion Resistance | Good (Specific Alloys) | Poor | Fair | Good |
Cost | Moderate | Moderate | Moderate | High |
Section 2 Gas Nitriding: The Controlled Atmosphere Approach
Gas nitriding is a widely used method that involves heating steel parts in a nitrogen-rich atmosphere, typically composed of ammonia (NH3). At elevated temperatures, the ammonia dissociates into nitrogen and hydrogen. The atomic nitrogen diffuses into the steel surface, forming iron nitrides (FeN).
2.1 Process: Parts are placed in a sealed furnace, and the atmosphere is carefully controlled. The temperature is typically between 480°C and 590°C (900°F and 1100°F). The process can last from several hours to several days, depending on the desired case depth.
2.2 Advantages:
Excellent control over case depth and microstructure.
Suitable for a wide range of steel alloys.
Can be used to selectively nitride specific areas by masking.
Relatively cost-effective for large-scale production.
2.3 Disadvantages:
Long cycle times.
Potential for white layer formation (a brittle iron nitride layer on the surface, which is often undesirable). This can be controlled through process optimization.
Requires careful monitoring and control of the atmosphere.
2.4 Applications: Gears, crankshafts, camshafts, valves, and other automotive and aerospace components.
Section 3 Salt Bath Nitriding: Speed and Uniformity
Salt bath nitriding (also known as liquid nitriding) involves immersing steel parts in a molten salt bath containing nitrogen-bearing compounds, such as cyanates. At the process temperature, these compounds decompose and release nitrogen, which diffuses into the steel surface.
3.1 Process: Parts are immersed in a molten salt bath at temperatures typically between 520°C and 580°C (970°F and 1075°F). The process duration is typically shorter than gas nitriding, ranging from a few minutes to a few hours.
3.2 Advantages:
Faster processing times compared to gas nitriding.
Uniform case depth, even on complex geometries.
Relatively simple to operate.
Good wear resistance and anti-seizure properties.
3.3 Disadvantages:
Environmental concerns related to the disposal of spent salt baths.
Potential for salt residue on parts after treatment, requiring cleaning.
Limited control over case depth and microstructure compared to gas nitriding.
3.4 Applications: Hydraulic cylinders, pump components, dies, molds, and other components requiring high wear resistance and anti-seizure properties.
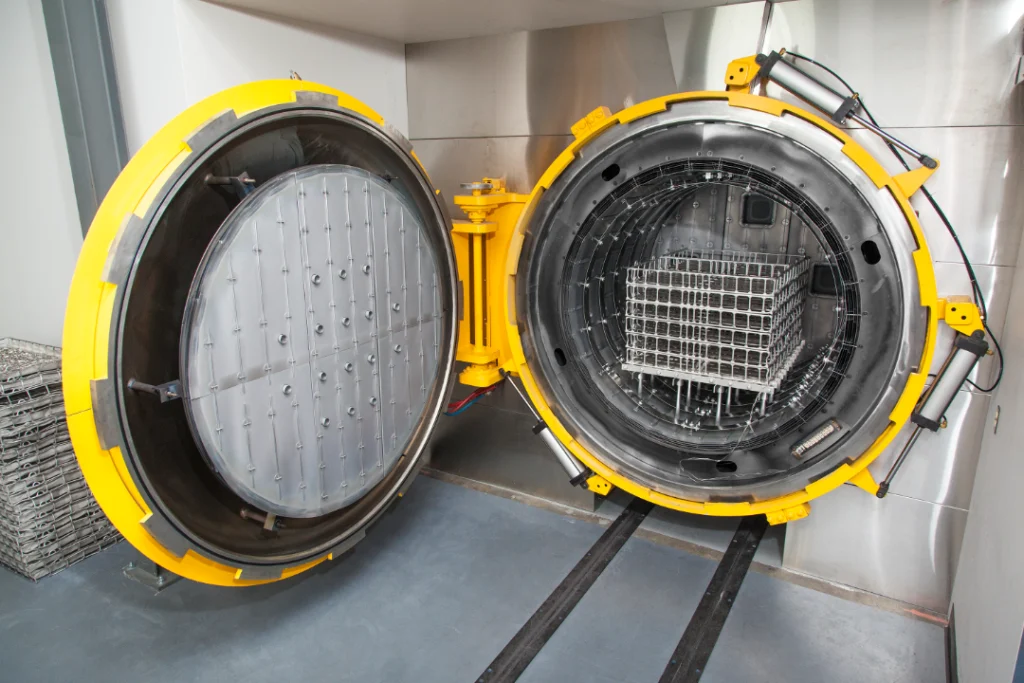
Section 4 Plasma Nitriding (Ion Nitriding): Precision and Control
Plasma nitriding (also known as ion nitriding) is a more advanced method that uses a plasma discharge to generate nitrogen ions, which are then accelerated towards the steel surface. The ions implant themselves into the surface, creating a nitride layer.
4.1 Process: Parts are placed in a vacuum chamber, and a plasma discharge is created using a mixture of nitrogen and other gases (e.g., hydrogen, argon). The parts are negatively charged, attracting the positively charged nitrogen ions. The ions bombard the surface, causing it to heat up and facilitating nitrogen diffusion.
4.2 Advantages:
Precise control over case depth, microstructure, and surface composition.
Ability to treat complex geometries and internal surfaces.
Lower processing temperatures compared to gas and salt bath nitriding, minimizing distortion.
Environmentally friendly process, as it does not produce harmful waste products.
4.3 Disadvantages:
Higher capital investment compared to gas and salt bath nitriding.
Requires skilled operators and sophisticated equipment.
Can be slower than salt bath nitriding for certain applications.
4.4 Applications: Precision gears, aerospace components, medical implants, and other high-performance applications where precise control and minimal distortion are critical.
Table: Comparison of Nitriding Methods
Method | Atmosphere | Temperature (°C) | Case Depth (mm) | Cycle Time | Control | Cost |
Gas Nitriding | Ammonia (NH3) | 480-590 | 0.025-1.0 | Long (Hours) | Excellent | Moderate |
Salt Bath Nitriding | Molten Salt (Cyanates) | 520-580 | 0.01-0.8 | Short (Minutes to Hours) | Fair | Moderate |
Plasma Nitriding | N2 + other gases (Plasma) | 350-600 | 0.01-1.0 | Variable | Excellent | High |
Section 5 Choosing the Right Nitriding Method
The selection of the appropriate nitriding method depends on several factors, including:
5.1 Material: The type of steel alloy being treated.
5.2 Geometry: The shape and size of the parts.
5.3 Required Case Depth: The desired thickness of the hardened layer.
5.4 Production Volume: The number of parts to be treated.
5.5 Budget: The cost of the equipment and processing.
5.6 Performance Requirements: The desired wear resistance, fatigue strength, and corrosion resistance.
Section 6 Nitriding Applications Across Industries
Nitriding is a versatile surface treatment used across various industries:
6.1 Automotive: Gears, crankshafts, camshafts, valves, connecting rods.
6.2 Aerospace: Landing gear components, engine parts, fasteners.
6.3 Tooling: Dies, molds, cutting tools, extrusion tools.
6.4 Oil and Gas: Pump components, valve bodies, drill bits.
6.5 Medical: Surgical instruments, implants.
6.6 Textile: Thread guides, needles.
Section 7 Nitriding and Nitrocarburizing
Nitrocarburizing is a variation of nitriding that involves diffusing both nitrogen and carbon into the steel surface. This results in a compound layer that has even better wear resistance and anti-seizure properties than nitriding alone. The same methods (gas, salt bath, plasma) can be adapted for nitrocarburizing by introducing a carbon-bearing gas (e.g., methane, propane) into the atmosphere or salt bath.
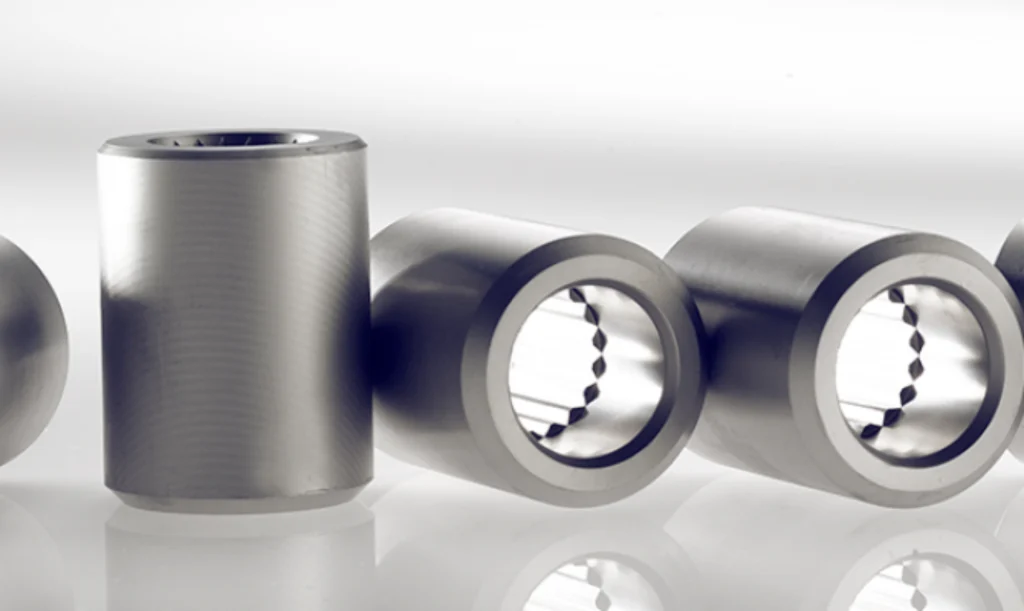
Section 8 The Future of Nitriding
The field of nitriding continues to evolve with advancements in process control, materials science, and equipment design. Current trends include:
8.1 Pulse Plasma Nitriding: Using pulsed plasma discharges to achieve even greater control over the nitriding process.
8.2 Modeling and Simulation: Using computer simulations to optimize nitriding parameters and predict the resulting microstructure and properties.
8.3 Development of New Nitriding Alloys: Creating steel alloys specifically designed for nitriding.
Section 9 Factors Affecting Nitriding Process
9.1 Material Composition:
Influence of alloying elements (chromium, aluminum, molybdenum).
Role of carbon content.
9.2 Temperature:
Impact on diffusion rate.
Phase transformations.
9.3 Time:
Effect on case depth.
9.4 Nitrogen Potential (Gas Nitriding):
Control of compound layer formation.
9.5 Bath Composition (Salt Bath Nitriding):
Cyanide concentration.
9.6 Plasma Parameters (Plasma Nitriding):
Voltage, current, gas pressure.
Section 10 Why Choose Welleshaft for Your Nitriding Needs?
When it comes to advanced steel treatment like nitriding, selecting a reliable and experienced partner is crucial. Welleshaft stands out as a trusted global supplier and contract manufacturer, offering comprehensive nitriding services tailored to your specific requirements.
Why Welleshaft?
10.1 Extensive Experience: With years of experience in heat treatment and surface engineering, Welleshaft possesses the expertise to deliver high-quality nitriding results.
10.2 State-of-the-Art Facilities: Welleshaft utilizes advanced equipment and technologies, including gas nitriding, salt bath nitriding, and plasma nitriding, to meet a wide range of needs.
10.3 Customized Solutions: Welleshaft works closely with clients to understand their unique requirements and develop customized nitriding solutions that optimize performance and cost-effectiveness.
10.4 Stringent Quality Control: Welleshaft adheres to rigorous quality control standards throughout the nitriding process, ensuring consistent and reliable results.
10.5 Global Reach: As a global supplier and contract manufacturer, Welleshaft can serve clients worldwide.
Conclusion
Nitriding is a powerful surface treatment that offers a wide range of benefits for steel components. By understanding the different nitriding methods and their advantages and disadvantages, engineers and manufacturers can select the optimal process for their specific applications. Whether you need increased surface hardness, improved wear resistance, or enhanced fatigue strength, nitriding can help you achieve your goals.Contact Welleshaft today to discuss your nitriding requirements and discover how they can help you achieve superior performance for your steel components.