Engineering Services: MIM & Sintered Parts
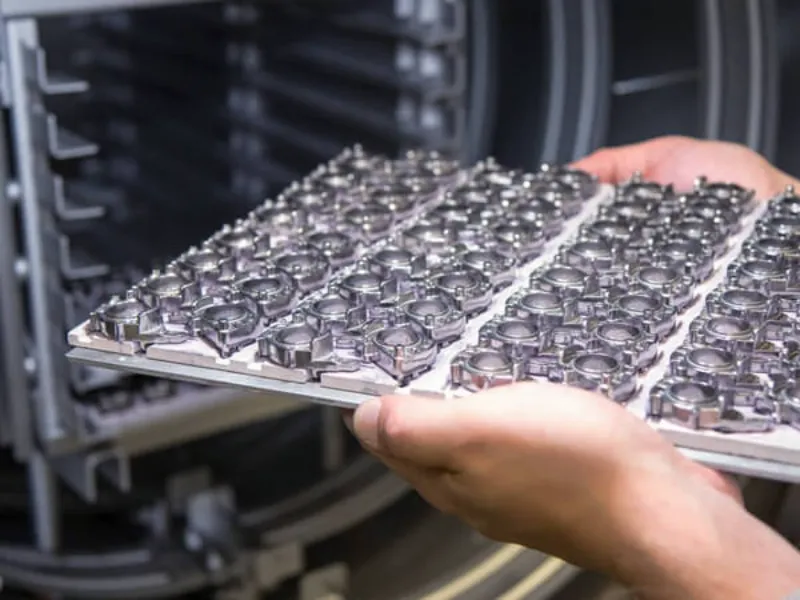
Applications: Renowned for corrosion resistance and robust strength, making it ideal for intricate components in various industries.Some material after heated,Hardness can up to HRC45.
Common Grades: Embrace MIM materials like BASF SS304L, SS316L or SS17-4PH, SS420, SS410 for superior performance.
Get a free quoteApplications: A staple choice offering a balance of strength and cost-effectiveness, suitable for various components.
Common Grades: Select MPIF materials like, F-0000/0005/0008, FC-0205 for versatile iron and carbon steel applications.
Get a free quoteApplications: Suitable for environments requiring enhanced strength and corrosion resistance,some materials after heat treated,hardness up to HRC 52. Common Grades: Opt for MPIF materials like FN-0200/0205/0208(MIM2200),FN-0405/0408,FL-4605(MIM4605) ,MIM4140 and MIM8620, Invar(Fe-Ni alloy) to ensure optimal performance in nickel/low alloy applications.
Applications: Perfect for scenarios demanding exceptional density and durability.
Common Grades: Explore alloys like MPIF HD-17 or W-based alloy for high-density properties in various applications.W-based – High temperature sintering proficiency allows various tungsten-nickel-iron alloy capability, sintered densities range up to 18 g/cc.
Get a free quoteApplications: Tailored for electromagnetic applications, providing a combination of magnetic properties and formability.
Common Grades: Opt for materials like ASTM B310-70, MIM SS430/L, MIM Fe-50Ni, MIM Fe3Si, to meet stringent soft magnetic requirements.
Get a free quoteApplications: A harmonious blend of strength and wear resistance, perfect for crafting intricate components across diverse industries. Offering improved toughness and wear resistance through copper infiltration. Common Grades: Explore MPIF materials like FX-1000/1005/1008, FC-1000/2000/0205/0208,CU-10Fe-5Ni, CT-1000-K26,CZN-1818,CZP-2000 or equivalent for optimal performance.
As a leading bespoke metal injection molding and powder metallurgy manufacturer. Experience the advantages of Metal Injection Molding for your application. where complexity, precision, and customization converge with real-world data to bring your designs to life. Partner with us to get superior MIM and Sintered parts that elevate the performance and quality of your end products.
Benefit from the enduring strength of our Powder Metallurgy (PM) process with robust tooling. Utilizing high-quality tooling materials, our precision metal sintering ensures longevity and consistency. Our robust tooling has demonstrated a lifespan of over 100,000 cycles, contributing to enhanced precision and repeatability.
The sintering process ensures exceptional ejectability, minimizing defects during demolding. Avoid geometries that prevent the component ejection from the tool, like undercuts or lateral holes, non-progressive section changes in diameter, knurling, etc. Introduce de-moulding angles higher than 7º, which could be lower in some cases.
Embrace design flexibility with the ability to achieve minimum wall thickness in your sintered parts. In general terms, a minimum wall thickness of 1.5 mm is required, although up to 0.8 mm is possible in some cases.This feature allows for lightweight designs and intricate detailing while maintaining required strength.
Preserve the integrity of green parts throughout the Powder Metallurgy process. Meticulous attention to green part production ensures a 98.5% success rate in maintaining initial compacted powder structures. This commitment to green part integrity translates to the production of high-quality, reliable sintered components.
Harness the versatility of Powder Metallurgy to create intricate gear shapes with precision. Whether helical gears, spur gears, or other specialized forms, our PM Sintering process excels in shaping components with gear tooth precision within ±0.05mm. Achieve durability for optimal performance in diverse applications.
Ensure precision with outstanding dimensional accuracy in every part. Our sintering process maintains tight tolerances, meeting or exceeding industry standards. With a dimensional accuracy rate of ±0.3%, the reliability and consistency of your sintered parts are guaranteed.
Step into a world where Metal Injection Molding (MIM) and Powder Metallurgy (PM) redefine possibilities. From automotive efficiency to medical precision and the dynamic realm of consumer electronics, MIM and PM parts prove indispensable. Join us on a journey through diverse applications, where these advanced manufacturing processes shape innovations and empower industries globally.
MIM Parts: Ideal for producing surgical instruments, orthodontic brackets, and drug delivery components. MIM’s capability to create small, intricate parts with high precision ensures compatibility with advanced medical technologies.
Sintered Parts: Commonly used for medical implants and prosthetics, where Powder Metallurgy’s ability to achieve intricate geometries and biocompatible materials is crucial.
MIM Parts: Widely used for intricate components such as fuel injection nozzles, valve guides, and gearbox components. The MIM process allows for complex shapes and precise detailing, contributing to improved fuel efficiency and performance.
Sintered Parts: Essential for sintered gears, sintered bearings, and sintered metal components. Powder Metallurgy provides cost-effective solutions with high strength and wear resistance, meeting the demanding requirements of automotive applications.
MIM Parts: Applied in the production of small, complex components like connectors, hinges, and smartphone parts. MIM’s ability to maintain tight tolerances and produce high-density parts is well-suited for electronic devices.
PM Sintered Parts: Utilized for components such as speaker magnets and battery contacts. Powder Metallurgy provides cost-effective solutions with excellent magnetic properties and electrical conductivity.
MIM Parts: Found in power/hand tool, firearm components,golf club heads, bicycle parts and hardware. Metal injection molding’s versatility in handling various materials and creating intricate shapes is valuable in industrial applications.
PM Sintered Parts: Essential for sintered gears, sintered bearings, and sintered sprockets in industrial machinery. Powder Metallurgy offers durability and precision in these critical components.
Sintered Structural components | Self-lubricating sintered bearings | Filters and porous metallic components | Sintered Gears | Sintered Stainless Steel Parts | Soft magnetic sintered components
Our commitment to excellence in Metal Injection Molding ensures that our components meet the highest standards of precision, durability, and functionality across diverse industries. Join us in the journey of innovation and discover the limitless possibilities of MIM technology.
In the intricate landscape of Metal Injection Molding (MIM), our unwavering commitment to excellence is underpinned by a holistic application of Design for Manufacturing (DFM) principles. This meticulous approach ensures not only the sophistication of your components but also their optimization for cost-effective and reliable production. Let’s delve into the nuanced facets of our design philosophy:
In essence, our design principles in MIM go beyond the superficial, ensuring not only the visual allure but also the feasibility, efficiency, and steadfast reliability throughout the manufacturing journey.