MIM Gear Process: Achieve Complex Gear Designs with Metal Injection Molding
Section 1 Introduction
Metal Injection Molding (MIM) has emerged as a transformative manufacturing process, particularly for creating intricate and high-performance components like gears. The MIM Gear Process combines the design flexibility of injection molding with the material properties of powder metallurgy, allowing for the production of complex gear geometries with exceptional precision and consistency. This article will delve into the intricacies of the MIM gear process, explore its advantages, discuss the materials used, and introduce Welleshaft as a reliable partner for MIM gear production. We will also examine the many uses of this technology.
Section 2 Understanding the MIM Gear Process
The MIM Gear Process is an advanced manufacturing technique that begins with the creation of a feedstock. This feedstock is a mixture of finely powdered metal particles and a binder, typically a thermoplastic polymer. The process involves the following key stages:
2.1 Feedstock Preparation: The powdered metal and binder are thoroughly mixed, creating a homogenous compound that can be injection molded.
2.2 Injection Molding: The feedstock is injected into a mold cavity under pressure, forming the desired gear shape. This results in what is known as a “green” part.
2.3 Debinding: The “green” part undergoes a debinding process to remove the binder material. This process leaves behind a porous metal structure referred to as a “brown” part.
2.4 Sintering: The “brown” part is heated to a temperature below the melting point of the metal in a controlled atmosphere. This is where metal particles fuse together, creating a dense, solid gear.
2.5 Finishing Operations (Optional): Depending on the requirements of the final product, secondary operations may include machining, surface treatment, or heat treatments.
Section 3 Types of Gears Produced by MIM
MIM can produce a wide array of gear types, making it a versatile manufacturing technology:
3.1 Spur Gears: The most common type with straight teeth parallel to the axis of rotation, ideal for transmitting power between parallel shafts.
3.2 Helical Gears: Features angled teeth, providing smoother and quieter operation compared to spur gears. Well suited for applications needing less vibration.
3.3 Bevel Gears: Transfers power between non-parallel shafts, often used in automotive differentials and power tools. MIM allows the production of complex tooth profiles, such as spiral bevel gears.
3.4 Planetary Gears: Systems using a sun gear, planet gears, and a ring gear for compact, high torque transmission, commonly used in automotive transmissions and servo mechanisms.
3.5 Worm Gears: Consists of a worm and a worm gear, used for high gear reduction ratios in small packages, typically with self locking characteristics. MIM is excellent for producing the detailed geometry of the worm and worm gear.
3.6 Internal Gears: Gears with teeth on the interior of a cylinder, which can be challenging to make using machining, are easily produced using MIM.
3.7 Ratchets and Pawls: These are often used in conjunction with gears in a variety of applications. MIM is well suited to produce these smaller components.
Section 4 Surface Treatments for MIM Gears
Surface treatments are often applied to enhance specific properties of MIM gears:
4.1 Polishing: Used to reduce surface roughness, improve appearance, and reduce friction. Suitable for gears requiring very low surface imperfections.
4.2 Media Blasting: Used to create a uniform matte finish or prepare the surface for other coatings. Suitable for gears needing a uniform surface appearance.
4.3 Passivation: Used primarily on stainless steel gears to improve corrosion resistance by forming a protective oxide layer. Useful in medical and food processing environments.
4.4 Plating: Applying a thin layer of metal to improve corrosion resistance, wear resistance, or conductivity. Can be used in many gear applications needing specific materials at the surface.
4.5 Coating: Application of specialized materials to the surface to provide enhanced wear resistance, corrosion resistance, or lubrication. Suitable for heavy-duty applications where prolonged gear life is needed.
4.6 Texturing: Adding specific patterns or textures to the surface, used for enhanced grip or special lubrication properties. Suitable in applications where specialized surface interactions are needed.
4.7 Chemical Treatments: Such as black oxide or phosphate coatings to improve corrosion and wear properties or provide a specific surface appearance.
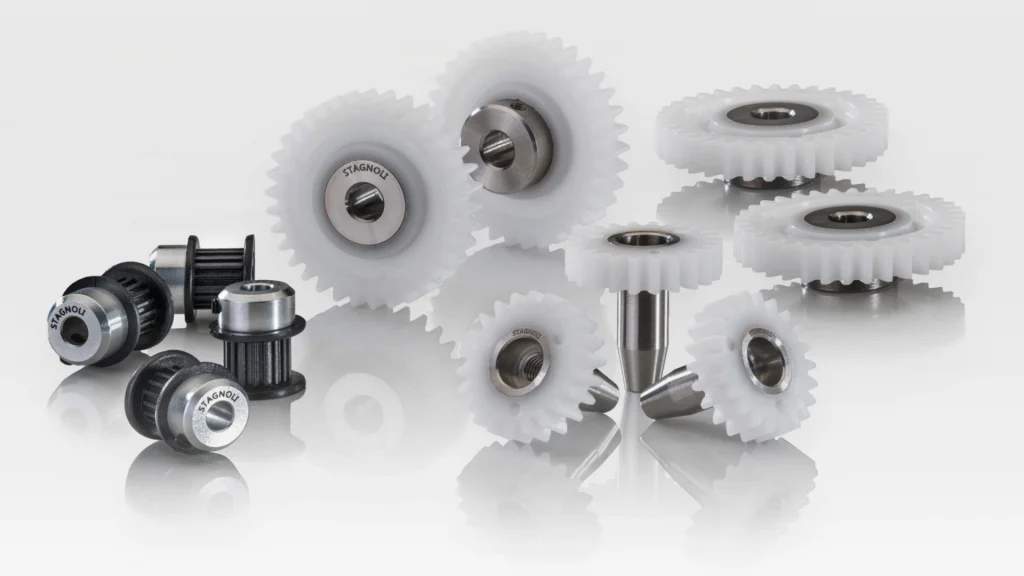
Section 5 Heat Treatments for MIM Gears
Heat treatment is a controlled process used to alter the metallurgical structure of MIM gears, improving their mechanical properties:
5.1 Hardening: Increases the hardness and strength of the metal. Essential for gears operating under high loads or needing wear resistance.
5.2 Tempering: Used after hardening to reduce brittleness and improve toughness, preventing gears from shattering under high stress.
5.3 Annealing: Heats the material to relieve internal stresses caused by manufacturing, improving ductility and machinability for further processing.
5.4 Case Hardening: Produces a hard outer layer while maintaining a softer core for improved wear resistance and impact strength. Ideal for gears that experience heavy wear.
5.5 Stress Relieving: Used to reduce any residual stress in the material, preventing distortion and improving the long term performance.
5.6 Quenching: Quick cooling used to increase hardness of the material, often used as an initial step in heat treatment, followed by tempering.
Section 6 The Role of Surface and Heat Treatments in MIM Gear Performance
Surface and heat treatments are critical for tailoring MIM gears to specific application requirements. Surface treatments can improve the gear’s interaction with its environment, such as in corrosive or high-wear environments. Heat treatments can drastically improve the bulk mechanical properties of the gear, increasing its strength, ductility and resistance to wear and fatigue. The combination of these treatments enhances overall gear performance and longevity.
Section 7 Advantages of the MIM Gear Process
The MIM Gear Process offers several compelling advantages compared to traditional gear manufacturing methods such as machining or casting:
7.1 Design Complexity: MIM allows for the creation of extremely complex gear geometries, including internal features, undercuts, and intricate details that are difficult or impossible to achieve with other methods.
7.2 High Precision and Tight Tolerances: MIM can produce gears with very tight tolerances, which means components are very precise and meet critical specifications.
7.3 Excellent Material Properties: MIM achieves material properties comparable to those of wrought metals, resulting in gears with good mechanical strength, wear resistance, and durability.
7.4 Cost-Effectiveness for High-Volume Production: MIM becomes very cost-effective for mass production because a single injection mold can produce numerous identical parts.
7.5 Reduced Material Waste: The MIM process generates minimal material waste compared to machining, where significant material is removed during the shaping process.
7.6 Smooth Surface Finish: MIM-produced gears typically exhibit good surface finishes, reducing or eliminating the need for extensive finishing operations.
7.7 Versatile Material Options: A wide range of metal alloys, including stainless steel, low alloy steels, titanium, and copper alloys, can be processed using MIM to meet various application needs.
7.8 Net-Shape Manufacturing: MIM is a near net-shape process, reducing the need for secondary operations and lowering overall costs.
Section 8 Materials Used in the MIM Gear Process
The selection of materials in the MIM gear process is determined by the application requirements of the finished product. The list of materials that can be formed by MIM is quite extensive, including:
8.1 Stainless Steels: Offers excellent corrosion resistance and are often used in medical devices, food processing equipment, and aerospace components.
8.2 Low Alloy Steels: Provide high strength and durability, ideal for high-load applications, such as gears for automotive transmissions.
8.3 Nickel Alloys: Known for their exceptional strength and resistance to high temperatures and harsh environments.
8.4 Titanium Alloys: Lightweight, strong, and corrosion-resistant, they are used in aerospace and medical applications.
8.5 Copper and Brass Alloys: Used for electrical and thermal conductivity applications.
8.6 Other specialty metals: MIM can be used with many other specialty metals and alloys.
The selection of a specific material allows engineers to create components that are optimized for their specific operating environment and load requirements.
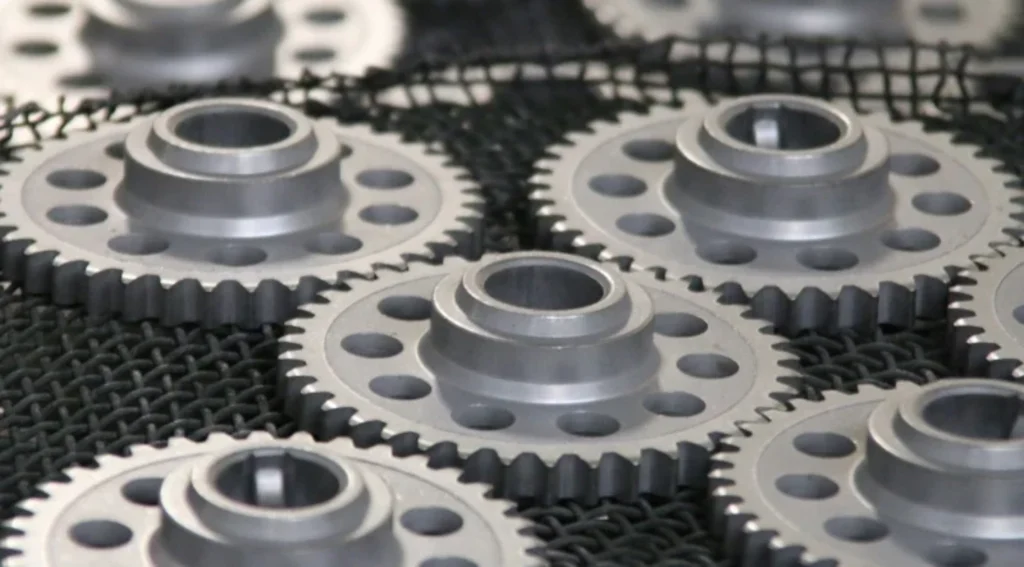
Section 9 Applications of MIM Gears
MIM Gears are widely used in a variety of industries and applications, including:
9.1 Automotive: Transmission gears, engine components, actuators, and sensors.
9.2 Aerospace: Actuation systems, control surfaces, and fasteners.
9.3 Medical: Surgical instruments, dental implants, and orthopaedic devices.
9.4 Consumer Electronics: Gears for printers, cameras, and portable devices.
9.5 Industrial Machinery: Gears for power transmission, robotics, and manufacturing equipment.
9.6 Firearms: Trigger mechanisms, internal parts, and small components.
9.7 Dental: Implants, orthodontic brackets and instrumentation.
Section 10 Welleshaft: A Trusted Global Supplier and Contract Manufacturer
Selecting a reliable partner is critical to ensure high-quality and reliable supply of your MIM gear parts. Welleshaft has established itself as a global leader in MIM manufacturing, offering a complete suite of solutions from design to production. They are also adept at all of the specific processes needed for MIM including the debinding, sintering and material composition. With extensive experience in MIM technology, Welleshaft provides:
10.1 Design Optimization: In collaboration with your team, Welleshaft can work to refine designs for optimal MIM manufacturability.
10.2 Material Selection Expertise: Welleshaft can assist in choosing the most suitable material for your application, ensuring both performance and durability.
10.3 Precision Manufacturing: Welleshaft utilizes advanced equipment and quality control processes to manufacture gears with high precision and consistency.
10.4 Cost-Effective Solutions: By optimizing the MIM process, Welleshaft provides high-quality parts with competitive pricing.
10.5 Scalability: Welleshaft can handle both small-scale prototyping and large-scale production, meeting the needs of diverse projects.
10.6 Comprehensive Capabilities: From design analysis to finishing operations, Welleshaft offers a full suite of services for your MIM gear projects.
10.7 Commitment to Quality: Welleshaft adheres to strict quality standards, ensuring the highest levels of reliability in their manufactured gears.
Section 11 Sheet Table of Related Information
Category |
Details |
Process Steps |
Feedstock Preparation, Injection Molding, Debinding, Sintering, Finishing (Optional) |
Advantages |
Design Complexity, High Precision, Excellent Material Properties, Cost-Effectiveness, Reduced Waste, Versatile Material Choices |
Typical Materials |
Stainless Steels, Low Alloy Steels, Nickel Alloys, Titanium Alloys, Copper Alloys |
Key Applications |
Automotive, Aerospace, Medical, Consumer Electronics, Industrial Machinery, Dental, Firearms |
Welleshaft Capabilities |
Design Optimization, Material Selection, Precision Manufacturing, Cost-Effective Solutions, Scalability, Comprehensive services |
Target Gear Types |
Spur, Helical, Bevel, Planetary, Worm |
Typical Gear Size Range |
From very small (sub-mm) to several cm in size (depending on complexity) |
Typical Dimensional Tolerances |
+/- 0.3% – 0.5% typically, can achieve tighter tolerances depending on process controls |
Conclusion
The MIM Gear Process offers an unparalleled approach to producing high-quality, complex gears with enhanced precision and design capabilities. Metal Injection Molding technology offers a way to create high volumes of complex parts using a cost effective process. This process offers significant advantages over traditional manufacturing techniques, particularly for intricate designs and high-volume production. With its versatile material options and cost-effectiveness, MIM is driving innovation across numerous industries. By partnering with a trusted global supplier like Welleshaft, manufacturers can be sure that their gear requirements are being fulfilled at the highest standards.