Metal Injection Molding vs Die Casting: Key Differences & Benefits Explained
When choosing a manufacturing process for metal parts, two popular methods often come into consideration: Metal Injection Molding (MIM) and Die Casting. Each technique offers distinct advantages and is suited to specific applications. This article will delve into the key differences between Metal Injection Molding and Die Casting, exploring their processes, benefits, costs, and material options to help you determine the best method for your needs.
1. Metal Injection Molding vs Die Casting: Key Differences
1.1.Process Complexity:
MIM: Involves multiple stages including feedstock preparation, injection molding, debinding, and sintering. This makes it suitable for complex parts with intricate details.
Die Casting: Involves fewer steps and is more straightforward, which is advantageous for producing simpler shapes quickly.
1.2.Material Options:
MIM: Primarily uses metal powders, allowing for a broad range of materials including stainless steel, tool steels, and titanium.
Die Casting: Typically uses molten metals such as aluminum, zinc, and magnesium alloys, which are less diverse compared to MIM materials.
1.3.Part Complexity and Size:
MIM: Better suited for small to medium-sized parts with complex geometries and fine details.
Die Casting: Ideal for larger parts or simpler shapes that benefit from high-volume production and faster cycle times.
1.4.Surface Finish and Tolerance:
MIM: Offers a finer surface finish and tighter tolerances due to the powder metallurgy process.
Die Casting: Provides a good surface finish but may require additional machining for tighter tolerances.
1.5.Production Costs:
MIM: Higher initial setup costs due to the complexity of the process and tooling but can be cost-effective for high-volume production.
Die Casting: Generally lower setup costs with fast production rates, making it economical for high-volume runs but may have higher per-unit costs for small quantities.
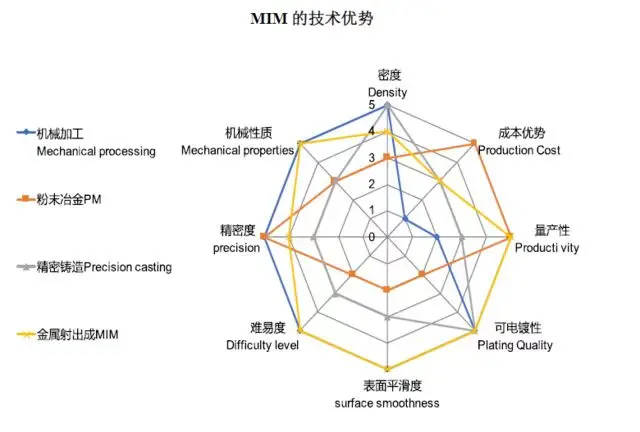
1. Metal Injection Molding vs Die Casting: Cost Considerations
2.1.Is Injection Molding Cheaper than Die Casting?
The cost-effectiveness of Metal Injection Molding (MIM) vs Die Casting largely depends on the production volume and part complexity. MIM has higher initial costs due to complex tooling and setup, but it becomes cost-effective for large production runs due to reduced material waste and less need for secondary machining. Conversely, Die Casting offers lower setup costs and faster production cycles, making it more economical for simpler, high-volume parts.
2.2.Metal Injection Molding vs Die Casting Price:
MIM: Higher initial tooling costs but lower material costs and less post-processing for complex parts. The overall cost per unit decreases with larger production runs.
Die Casting: Lower tooling and setup costs with fast cycle times but may have higher per-unit costs for complex parts due to additional machining and finishing.
2.3.Metal Injection Molding (MIM) Cost Breakdown
2.3.1.Initial Setup Costs:
Tooling and Equipment: MIM requires complex tooling and specialized equipment, which can result in higher initial setup costs. The molds used in MIM are intricate and need to be precisely manufactured, contributing to these higher costs.
Material Costs: The feedstock used in MIM, which combines metal powders with binders, is generally more expensive than the raw materials used in Die Casting. However, the material efficiency is high, as there is minimal waste during the manufacturing process.
2.3.2.Production Costs:
Unit Cost: While the initial costs for MIM are high, the per-unit cost of parts can be quite economical for large production runs. This is due to reduced material waste and the minimal need for additional machining or finishing.
Complexity and Precision: MIM is particularly cost-effective for producing complex parts with fine details. The high precision achieved with MIM reduces the need for secondary processes, further driving down the cost per unit for complex geometries.
2.3.3.Additional Costs:
Post-Processing: MIM parts often require less post-processing compared to Die Casting, as the parts are produced with a high level of detail and precision from the start. This can lead to cost savings in finishing and secondary operations.
2.4.Die Casting Cost Breakdown
2.4.1.Initial Setup Costs:
Tooling and Equipment: Die Casting has relatively lower initial setup costs compared to MIM. The molds used in Die Casting are simpler and less expensive to manufacture, making it a more affordable option for initial tooling.
Material Costs: Die Casting typically uses molten metals such as aluminum, zinc, and magnesium, which are often less expensive than the metal powders used in MIM. However, the material costs can vary depending on the type of metal and market conditions.
2.4.2.Production Costs:
Unit Cost: Die Casting is highly efficient for high-volume production runs due to fast cycle times and high production rates. The per-unit cost is relatively low, especially for simple shapes and larger quantities.
Cycle Time: The rapid production cycle in Die Casting reduces the cost per unit, making it an economical choice for producing large quantities of parts. However, the cost may increase for more complex or intricate parts due to additional machining and finishing requirements.
2.4.3.Additional Costs:
Post-Processing: Die Cast parts often require additional finishing or machining to achieve the desired specifications, which can add to the overall cost. The need for secondary operations can impact the total cost per unit, particularly for more complex geometries.
2.5.Cost Comparison Summary
Initial Investment: Metal Injection Molding generally requires a higher initial investment due to the complexity of tooling and equipment. Die Casting, on the other hand, has lower initial setup costs but may involve additional costs for post-processing.
Production Volume: For high-volume production runs, MIM can be cost-effective due to reduced material waste and minimal need for additional machining. Die Casting also offers low per-unit costs for high volumes, particularly for simpler parts with fewer finishing requirements.
Part Complexity: MIM is more advantageous for producing complex parts with fine details, as it reduces the need for secondary operations. Die Casting is more suited for simpler parts but may require additional machining for complex geometries.
Material Costs: The cost of materials for MIM is generally higher due to the use of metal powders, but material efficiency is improved. Die Casting uses molten metals that are often less expensive, though material costs can vary.
3.Metal Injection Molding vs Die Casting: Application Scenarios
MIM: Suitable for industries requiring high precision and complex geometries such as aerospace, medical devices, and electronics. Examples include surgical instruments, firearm components, and high-performance automotive parts.
Die Casting: Ideal for industries needing high-volume production of simpler parts with good dimensional accuracy, such as automotive components, consumer electronics housings, and industrial machinery.
Conclusion
Both Metal Injection Molding (MIM) and Die Casting are valuable manufacturing processes with unique strengths. MIM excels in producing complex, high-precision parts with diverse material options, making it ideal for specialized applications. Die Casting, on the other hand, offers speed and cost efficiency for high-volume production of simpler parts.
When choosing between MIM and Die Casting, consider factors such as part complexity, material requirements, production volume, and cost constraints to determine the best method for your specific needs. Understanding the differences and benefits of each process will help you make an informed decision and optimize your manufacturing strategy.
For more information on high-quality MIM and Die casting Manufacturer and to find the perfect solution for your application, please contact us.
Jinan Welle Metal Products Co., Ltd (Welleshaft)
Website: www.welleshaft.com
Email: [email protected]
Phone: +86-156-5017-9596
Explore our range of durable and reliable MIM Parts and Die Casting Parts today!
This is a simple headline
Lorem ipsum dolor sit amet, consectetuer adipiscing elit, sed diam nonummy nibh euismod tincidunt ut laoreet dolore magna aliquam erat volutpat.