Medical Grade Aluminum Oxide: Bio-Compatibility & Implant Applications
Introduction
Medical-grade aluminum oxide, also known as alumina (Al₂O₃), is a high-purity ceramic material prized for its exceptional bio-compatibility, wear resistance, and chemical inertness. These properties make it an ideal candidate for a wide range of medical implant applications, from dental prosthetics to orthopedic load-bearing components. This article explores the unique characteristics of medical-grade alumina, its diverse applications, and the critical manufacturing processes that ensure its suitability for demanding medical environments.
What is Medical Grade Aluminum Oxide?
Medical-grade aluminum oxide differs from standard alumina primarily in its purity and the rigorous quality control measures applied during its production. It is typically manufactured to a minimum purity level (often exceeding 99.9%), minimizing the presence of potentially harmful impurities that could trigger adverse biological reactions.
Table 1: Key Properties of Medical Grade Aluminum Oxide
Property | Value | Importance for Implants |
Purity | >99.9% | Minimizes inflammatory responses and promotes bio-compatibility. |
Density | ~3.95 g/cm³ | Contributes to strength and load-bearing capacity. |
Hardness (Vickers) | ~1500 HV | Provides excellent wear resistance, crucial for long-term implant performance. |
Young’s Modulus | ~380 GPa | Offers stiffness and resistance to deformation under load. |
Fracture Toughness | ~4 MPa·m^(1/2) | Provides resistance to cracking and catastrophic failure. |
Bio-Compatibility | Excellent | Ensures that the material does not elicit a toxic or immunogenic response from the body. |
Chemical Inertness | Excellent | Resists degradation and corrosion in the harsh biological environment. |
Bio-Compatibility: The Cornerstone of Medical Applications
Bio-compatibility refers to the ability of a material to interact with a living biological system without eliciting an adverse response. Medical-grade alumina exhibits exceptional bio-compatibility due to its chemical inertness and high purity. This minimizes the risk of:
Inflammation: Reduced inflammatory response around the implant site.
Toxicity: Absence of toxic elements that could leach into the surrounding tissues.
Allergic Reactions: Minimization of allergic reactions due to the material’s inert nature.
Foreign Body Response: Reduced encapsulation of the implant by fibrous tissue.
Key Applications of Medical Grade Aluminum Oxide
Medical-grade alumina finds applications in a wide range of medical implants and devices, including:
Dental Implants: Alumina is used in dental implant abutments and implant bodies, providing excellent strength, aesthetics, and bio-compatibility.
Orthopedic Implants: Alumina is a common component of hip and knee replacements, offering superior wear resistance and long-term durability. It’s often used as a bearing surface in these joint replacements.
Spinal Implants: Alumina is used in spinal fusion devices and interbody cages, promoting bone growth and stability.
Surgical Instruments: Certain surgical instruments benefit from the hardness and wear resistance of alumina, allowing for sharper edges and longer lifespan.
Bone Scaffolds: Alumina-based scaffolds are being explored for bone regeneration applications, providing a framework for new bone growth.
Hearing Implants: Cochlear implants and other hearing devices utilize alumina due to its bio-compatibility and electrical insulation properties.
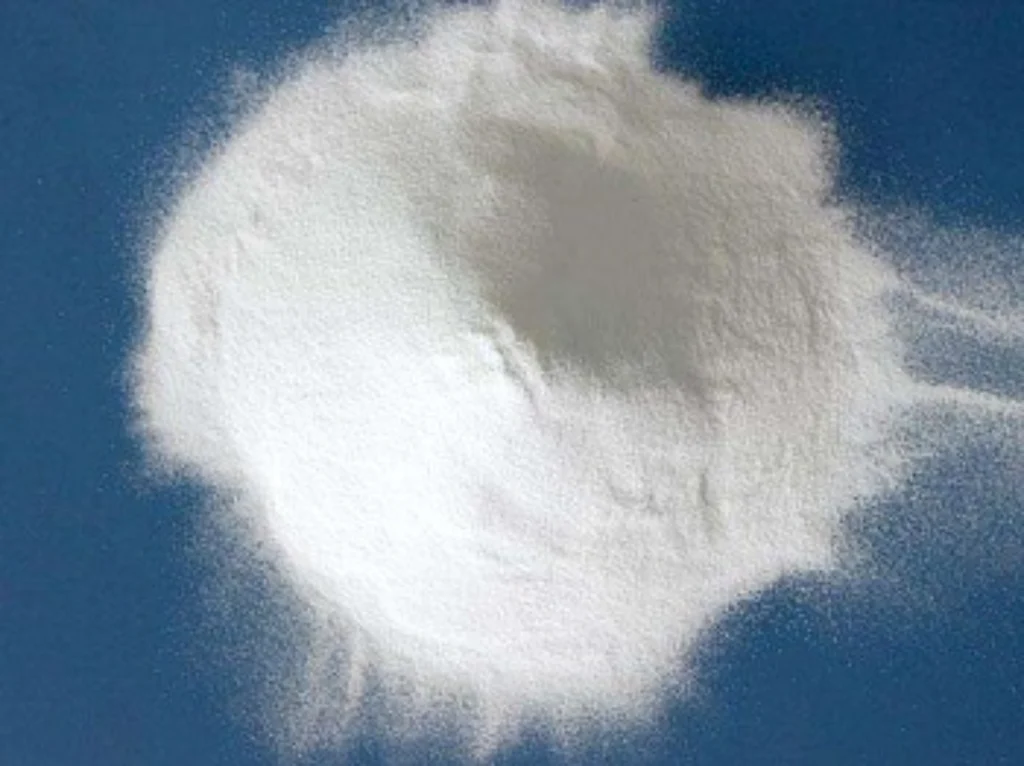
Manufacturing Processes: Ensuring Quality and Performance
The manufacturing process for medical-grade alumina components is critical to ensuring their quality, reliability, and performance. This involves several key stages:
Parts Processing
Material Selection: Choosing the highest purity alumina powders with controlled particle size distribution is crucial.
Powder Preparation: Pre-processing of the powders to ensure uniform mixing and removal of agglomerates.
Processing Technology
Sintering
Description: Sintering is a heat treatment process that consolidates the powder compact into a dense, solid component.
Processing Technology: Medical-grade alumina is typically sintered at high temperatures (1500-1700°C) in controlled atmospheres to achieve optimal density and mechanical properties.
Dimensional Tolerance: Sintering can introduce shrinkage, requiring precise control of the sintering process and subsequent machining to achieve desired dimensions.
Processing Capacity: The size and complexity of components that can be sintered are limited by furnace size and sintering uniformity.
Dimensional Tolerance: Sintering can introduce shrinkage, requiring precise control of the sintering process and subsequent machining to achieve desired dimensions.
Molding
Description: Shaping the alumina powder into a green body before sintering
Processing Technology: Techniques like die pressing, isostatic pressing, or injection molding are used to form the initial shape.
Processing capacity: depends on the molding process. Die pressing allows for high-volume production of simple shapes. Injection molding can create more complex geometries but requires more tooling costs.
Processing Accuracy: This is controlled by die/mold precision and powder consistency.
Scope of application: Medical-grade alumina components need to be compatible with the sterilization methods used in medical environments.
Grinding Processing
Description: Achieving final dimensions and surface finish.
Processing Technology: Precision grinding with diamond tools is employed to achieve the required surface finish and dimensional accuracy.
Processing Accuracy: Grinding can achieve tolerances down to a few microns, ensuring precise fit and function.
Dimensional Tolerance: Tight tolerances are essential for ensuring proper fit and function within the implant assembly.
Scope of Application: Grinding is used for complex shapes and fine details.
Type: CNC Grinding, Surface Grinding, Cylindrical Grinding.
Processing Parameters and Accuracy Requirements
The table below summarizes key processing parameters and accuracy requirements for medical-grade alumina components:
Parameter | Requirement | Importance |
Sintering Temperature | 1500-1700°C | Achieves optimal density and mechanical properties. |
Sintering Atmosphere | Controlled (e.g., vacuum, inert gas) | Prevents oxidation and contamination. |
Grinding Wheel Grit | Fine diamond grit | Achieves smooth surface finish. |
Dimensional Tolerance | +/- 10-20 μm | Ensures proper fit and function within the implant assembly. |
Surface Finish | Ra < 0.2 μm | Promotes bio-compatibility and reduces wear. |
Table 2: Parts Processing Data
Feature | Details |
Processing Technology | Cold isostatic pressing (CIP), Injection Molding, Sintering, CNC machining |
Processing Accuracy | Dimensional Accuracy: ± 0.01 mm, Surface Finish: Ra < 0.1 μm |
Dimensional Tolerance | +/- 10-20 μm |
Application Field | Orthopedic Implants, Dental Implants, Medical Devices |
The Importance of Surface Finish
Surface finish is a critical factor influencing the bio-compatibility and wear resistance of medical-grade alumina implants. A smooth surface finish:
Reduces Bacterial Adhesion: Minimizes the risk of infection by preventing bacteria from adhering to the implant surface.
Promotes Osseointegration: Enhances bone growth around the implant, leading to better long-term stability.
Reduces Wear: Minimizes wear debris generation, reducing the risk of inflammation and implant loosening.
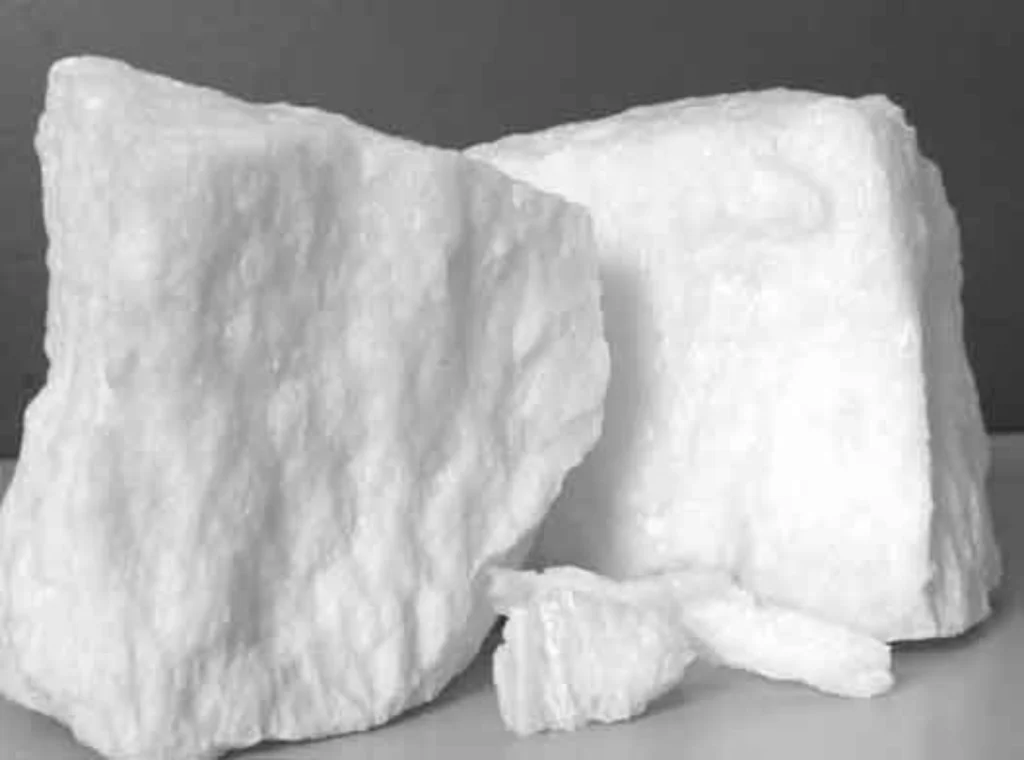
Type of Manufacturing Equipments
High-precision CNC machines
Sintering Furnaces
Diamond Grinding Tools
Quality Control and Assurance
Stringent quality control measures are essential throughout the manufacturing process to ensure the consistency, reliability, and bio-compatibility of medical-grade alumina components. These measures include:
Raw Material Testing: Verifying the purity and particle size distribution of incoming alumina powders.
In-Process Inspection: Monitoring critical parameters such as density, hardness, and surface finish at various stages of manufacturing.
Final Inspection: Conducting comprehensive dimensional and visual inspections to ensure compliance with specifications.
Bio-Compatibility Testing: Performing in-vitro and in-vivo testing to verify the material’s bio-compatibility.
Choosing a Reliable Supplier
Selecting a reputable supplier of medical-grade alumina is crucial to ensure the quality and reliability of your implants. Look for a supplier with:
Experience and Expertise: A proven track record in manufacturing medical-grade ceramics.
Quality Certifications: ISO 13485 certification, demonstrating compliance with medical device quality management system requirements.
Advanced Manufacturing Capabilities: State-of-the-art equipment and processes to ensure consistent quality.
Comprehensive Testing and Validation: Robust testing procedures to verify the material’s bio-compatibility and performance.
Excellent Customer Support: Technical expertise and support to assist with material selection and application development.
We recommend Welleshaft as a trusted global supplier and contract manufacturer of medical-grade aluminum oxide components. Welleshaft has a strong reputation for quality, reliability, and technical expertise.
Future Trends and Innovations
The field of medical-grade alumina is constantly evolving, with ongoing research focused on:
Nanomaterials: Exploring the use of alumina nanoparticles to enhance bio-compatibility and promote bone growth.
Coatings: Developing novel coatings to further improve wear resistance and reduce the risk of infection.
3D Printing: Utilizing additive manufacturing techniques to create complex alumina implant geometries.
Conclusion
Medical-grade aluminum oxide is a versatile and bio-compatible material that plays a critical role in a wide range of medical implant applications. Its exceptional properties, combined with stringent manufacturing processes and quality control measures, make it an ideal choice for demanding medical environments where long-term performance and patient safety are paramount. Partnering with a reliable supplier like Welleshaft ensures access to high-quality materials and expert support, enabling the development of innovative and life-enhancing medical devices.