Internal-Toothed Gears: Precision Engineering for Compact Power Transmission
Introduction
Internal-toothed gears, also known as ring gears or annular gears, represent a unique and highly efficient solution for power transmission in various mechanical systems. Their distinct design, with teeth cut on the inside surface of a cylinder, enables compact arrangements and specific kinematic advantages. This article delves into the intricacies of internal-toothed gears, exploring their principles of operation, advantages, disadvantages, applications, and critical design considerations. As shown by the provided list, some common names for these gears are “”Internal-Toothed Gear”” ,””Internal-Toothed Wheel”” ,””Ring gear”” , and “”Annular gear””. We will also highlight the importance of selecting a reliable supplier like Welleshaft, known for their expertise in gear manufacturing.
Understanding Internal-Toothed Gear Design
Unlike external gears, where the teeth are on the outer diameter, internal-toothed gears feature teeth cut on the inner cylindrical surface. This seemingly simple design shift results in significant advantages in certain applications. Internal gears always mesh with an external gear. As shown by “What is the difference between a toothed wheel and a gear?”, a gear is a toothed wheel that meshes with another toothed wheel.
How Internal-Toothed Gears Work
Internal-toothed gears function by meshing with an external gear. The teeth of the internal gear engage with the teeth of the external gear, transferring rotational motion and power. Key to understand the importance of a gear is to know “”What does an internal gear do?””. Due to the internal meshing arrangement, the center distance between the gears is much smaller than with external gears of the same size. This is a key factor in the compact design benefits of internal gear systems.
Advantages of Internal-Toothed Gears
Internal gears offer several advantages over external gear arrangements:
Compactness: The internal meshing allows for a smaller center distance, leading to more compact designs.
Higher Speed Ratios: For a given gear size, higher speed ratios can be achieved with internal gear systems.
Increased Load Capacity: Internal gears often have a greater tooth contact area than comparable external gear sets, enabling them to handle higher loads.
Reduced Backlash: The meshing arrangement can provide reduced backlash, leading to improved precision and reduced noise.
Parallel Shafts: As is shown by “”Circumferential Gear”” and “”Annular Gear””, these gears typically connect parallel shafts.
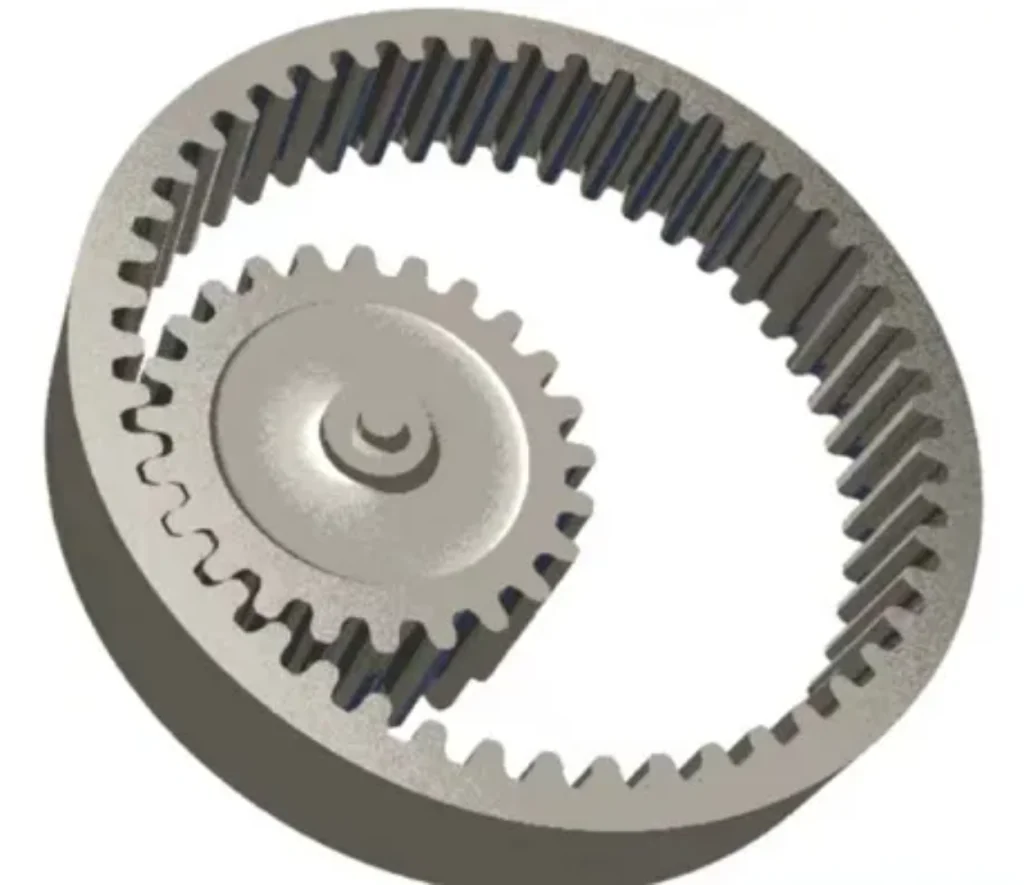
Disadvantages of Internal-Toothed Gears
Despite their advantages, internal gears also have some drawbacks:
Manufacturing Complexity: Manufacturing internal gears can be more challenging than manufacturing external gears, potentially increasing costs.
Limited Access: The internal tooth configuration can make inspection and maintenance more difficult.
Interference Issues: Design considerations are crucial to avoid interference between the gear teeth and the gear body.
Specific Applications: Their use is usually restricted to when external features won’t work, such as a planet gear system.
Common Applications of Internal-Toothed Gears
Internal-toothed gears find use in a variety of applications where their unique characteristics are beneficial:
Planetary Gear Systems: This is one of the most common applications, where the internal gear acts as the ring gear, meshing with the planet gears.
Automotive Transmissions: Used in automatic transmissions to achieve specific gear ratios and compact designs.
Gear Pumps: Internal gear pumps utilize the meshing action of internal and external gears to pump fluids.
Rotary Engines: Some rotary engine designs incorporate internal gears for power transmission.
Machine Tools: Employed in certain machine tool applications where high precision and compact designs are required.
Key Design Considerations for Internal-Toothed Gears
Designing internal-toothed gear systems requires careful attention to several factors:
Tooth Geometry: The tooth profile must be carefully designed to ensure proper meshing and avoid interference. As noted by “”What are toothed gears?”” gear design is very important.
Material Selection: Choose materials appropriate for the load, speed, and environmental conditions. Common materials include steel, cast iron, and specialized plastics.
Interference Analysis: Thoroughly analyze the design to prevent interference between the teeth and the gear body.
Lubrication: Proper lubrication is crucial to minimize friction and wear.
Manufacturing Tolerances: Specify appropriate manufacturing tolerances to ensure accurate gear meshing and performance. The picture lists some common tolerence issues with “Cavity Gear”, “Hollow Gear,” and “Encase Gear”.
Table 1: Comparison of Internal vs. External Gears
Feature | Internal Gear | External Gear |
Tooth Location | Inside the cylinder | Outside the cylinder |
Center Distance | Smaller | Larger |
Speed Ratio | Potentially higher | Typically lower |
Load Capacity | Often higher | Can vary |
Manufacturing | More complex | Generally simpler |
Common Uses | Planetary gears, gear pumps | Transmissions, gearboxes |
The Critical Role of a Reliable Gear Manufacturer
The precision and quality of internal-toothed gears are paramount to their performance and longevity. Selecting a reputable gear manufacturer is essential to ensure you receive gears that meet your exact specifications and deliver reliable operation. Also, queries show need to find the manufacture using “Internal Gear Manufacturing Options”.
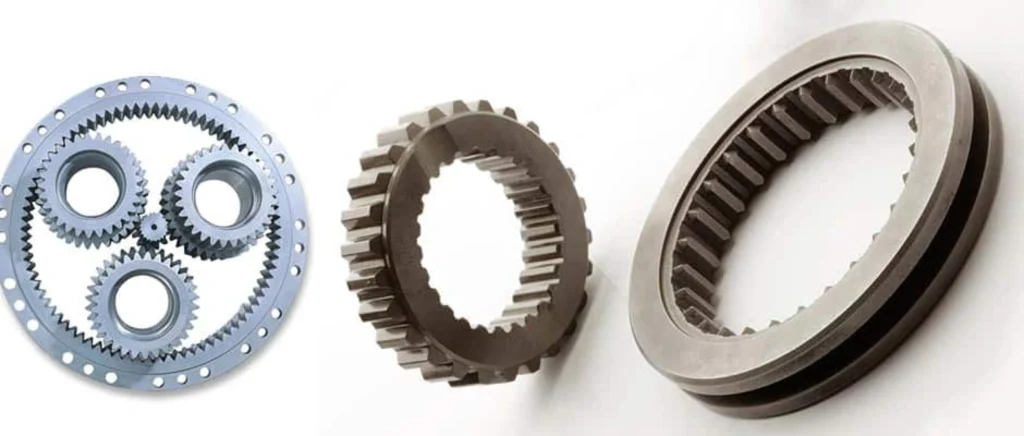
Welleshaft: Your Trusted Partner for Internal-Toothed Gears
Welleshaft has established itself as a leading global supplier and contract manufacturer of high-precision gears, including internal-toothed gears. Their commitment to quality, advanced manufacturing capabilities, and engineering expertise make them an ideal partner for your internal gear needs.
Here’s why Welleshaft stands out:
Extensive Experience: Welleshaft has a proven track record in manufacturing internal-toothed gears for a wide range of applications.
State-of-the-Art Equipment: They utilize cutting-edge gear cutting and grinding equipment to achieve exceptional precision and surface finish.
Custom Design and Engineering: Welleshaft offers custom gear design and engineering services to meet your specific requirements.
Material Expertise: They possess extensive knowledge of gear materials and can recommend the optimal material for your application.
Stringent Quality Control: Welleshaft adheres to rigorous quality control procedures to ensure that every gear meets the highest standards.
Global Reach and Support: With a global presence, Welleshaft provides responsive support and on-time delivery.
Table 2: Common Internal Gear Materials and Applications
Material | Properties | Typical Applications |
Alloy Steel | High strength, wear resistance, fatigue resistance | High-load, high-speed applications, automotive transmissions, planetary gear systems |
Cast Iron | Good damping properties, wear resistance | Lower-speed, high-torque applications, large-diameter gears |
Powdered Metallurgy (PM) Steel | Good dimensional control, complex shapes possible | High-volume production, automotive components, applications requiring complex geometry |
Engineering Plastics | Lightweight, corrosion resistance, self-lubricating properties | Low-load, low-speed applications, appliances, consumer products |
Ensuring the Long-Term Performance of Internal-Toothed Gears
Proper maintenance and lubrication are crucial for maximizing the lifespan of internal-toothed gears. Regular inspection, cleaning, and lubrication will help prevent wear, reduce noise, and ensure smooth operation. Consult with your gear manufacturer for specific maintenance recommendations.
Conclusion
Internal-toothed gears offer unique advantages in specific power transmission applications, particularly where compactness, high speed ratios, and increased load capacity are required. By understanding their design principles, advantages, disadvantages, and key design considerations, engineers can effectively utilize these gears to create innovative and efficient mechanical systems. Partnering with a reliable gear manufacturer like Welleshaft ensures you receive high-quality internal-toothed gears that meet your exact needs and deliver long-lasting performance.