Inconel Fasteners for Chemical Processing: Withstand Harsh Conditions
Section 1 Introduction
The chemical processing industry presents some of the most challenging environments for materials, demanding exceptional resistance to corrosion, high temperatures, and mechanical stress. Inconel fasteners are engineered specifically to meet these rigorous demands. This article will explore the diverse types of Inconel fasteners, their manufacturing processes, material specifications, key characteristics, testing protocols, surface treatments, and essential applications within chemical processing. Additionally, we’ll discuss why partnering with a reputable supplier like Wellshaft is crucial for obtaining top-quality fasteners.
Section 2 The Importance of Inconel Fasteners in Chemical Processing
Chemical processing environments often involve highly corrosive substances, extreme temperatures, and mechanical stress. Inconel alloys, with their superior resistance to these factors, are indispensable for ensuring the safety and longevity of critical equipment. The use of Inconel fasteners contributes to:
2.1 Enhanced Safety: Reducing the risk of fastener failure, which could lead to leaks or structural damage.
2.2 Reduced Downtime: Inconel fasteners resist degradation, minimizing the need for frequent replacements.
2.3 Improved Efficiency: Allowing systems to operate reliably even under harsh conditions.
2.4 Cost Savings: By reducing maintenance and downtime, Inconel fasteners often lower overall operational expenses over time.
Section 3 Types of Inconel Fasteners
A wide range of Inconel fasteners is available to meet diverse chemical processing requirements:
3.1 Inconel Bolts: Used for joining components, available in various head styles (hex, socket, etc.) and thread types.
3.2 Inconel Nuts: Complementary to bolts, used for securing bolted joints.
3.3 Inconel Screws: Used for applications that need high tensile strength and good thread engagement.
3.4 Inconel Washers: Used to distribute load, prevent loosening, and provide sealing functions.
3.5 Inconel Studs: Threaded rods that are used to connect two parts.
3.6 Inconel Rivets: Used for permanent joining of components.
3.7 Inconel Threaded Rods: Lengths of threaded material that can be cut to the required size for specific applications
Section 4 Processing Techniques for Inconel Fasteners
The production of Inconel fasteners involves specialized techniques:
4.1 Cold Heading: Used for producing smaller fasteners by shaping the metal at room temperature, ensuring high precision.
4.2 Red Heading: Suitable for larger fasteners, this method heats the metal before heading, making it more malleable and easier to form.
4.3 Turning Processing: Precision machining using lathes for complex fastener geometries and specific dimensions.
4.4 Thread Rolling: Forming threads using a rolling process that produces strong, accurate threads.
4.5 Hot Forging: For custom shapes or highly durable fasteners. Heat and pressure shape the alloy in this technique.
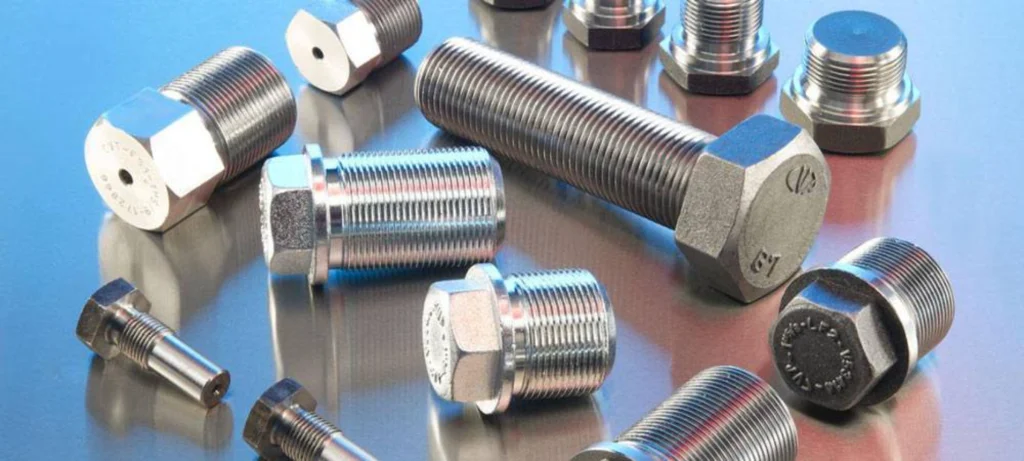
Section 5 International Material Specifications for Inconel Alloys
Inconel alloys are specified under various international standards, ensuring consistent quality and properties:
Standard | Material Description | Key Properties | Typical Applications |
ASTM B166 | Inconel 600/601/625 Bars & Rods | High-temp strength, corrosion resistance, oxidation resistance | Chemical processing, furnace components, aerospace |
ASTM B446 | Inconel 718/725/925/926/901 Bars & Rods, Forgings | High strength at elevated temperatures, good corrosion and stress-corrosion cracking resistance | Aerospace components, nuclear applications, oil and gas |
ASME SB166 | Nickel-Chromium-Iron Alloy Bars, Rods, and Wires | High-temperature strength, good resistance to oxidizing and carburizing atmospheres | Furnaces, petrochemical processing, food processing |
ISO 965-1/2/3 | Metric Thread Standards | Ensures interchangeability and precision of metric threads | General-purpose metric fasteners |
ANSI/ASME B18.2.1/2.2 | Inch Thread Standards | Ensures interchangeability and precision of inch fasteners | General-purpose inch fasteners |
Section 6 Material Characteristics of Inconel Alloys
The Inconel family of alloys exhibits exceptional characteristics:
6.1 Exceptional Corrosion Resistance: Highly resistant to a broad range of corrosive media, including acids, alkalis, chlorides, and other harsh chemicals.
6.2 High-Temperature Strength: Maintains mechanical properties at elevated temperatures, preventing creep and deformation.
6.3 Excellent Mechanical Strength: Exhibits high tensile, yield, and fatigue strength, which allows for demanding mechanical applications.
6.4 Oxidation Resistance: Resists oxidation at high temperatures, ensuring prolonged service life.
6.5 Creep Resistance: Resists deformation under sustained high temperatures and stress.
6.6 Non-Magnetic Properties: Most Inconel alloys are non-magnetic, which is essential for certain applications.
Section 7 Testing Capabilities for Inconel Fasteners
Rigorous testing is essential to ensure Inconel fasteners meet specified standards:
7.1 Tensile Testing: Measures tensile strength, yield strength, and elongation.
7.2 Hardness Testing: Determines resistance to indentation.
7.3 Corrosion Testing: Evaluates performance in various corrosive media.
7.4 Non-Destructive Testing (NDT): Uses methods like ultrasonic and radiographic testing to detect flaws without damaging the fastener.
7.5 Dimensional Inspection: Verifies dimensions and tolerances against specified standards.
7.6 Chemical Analysis: Assesses the material’s composition to verify it meets alloy specifications.
7.7 Stress Rupture Testing: Assesses the behavior under high stress and elevated temperatures.
7.8 Fatigue Testing: Evaluates the resistance of fasteners to failure under repeated loading.
Section 8 Surface Treatment Methods for Inconel Fasteners
Surface treatments provide additional protection and enhance performance:
8.1 Passivation: Improves corrosion resistance by forming a passive oxide layer.
8.2 Pickling: Removes surface impurities, scale, or oxides.
8.3 Electroplating: Applying a thin layer of another metal (e.g. silver, gold) for specific properties, and/or for color coding.
8.4 Dry Film Lubricants: Reduce friction and ease installation, and provides additional protection.
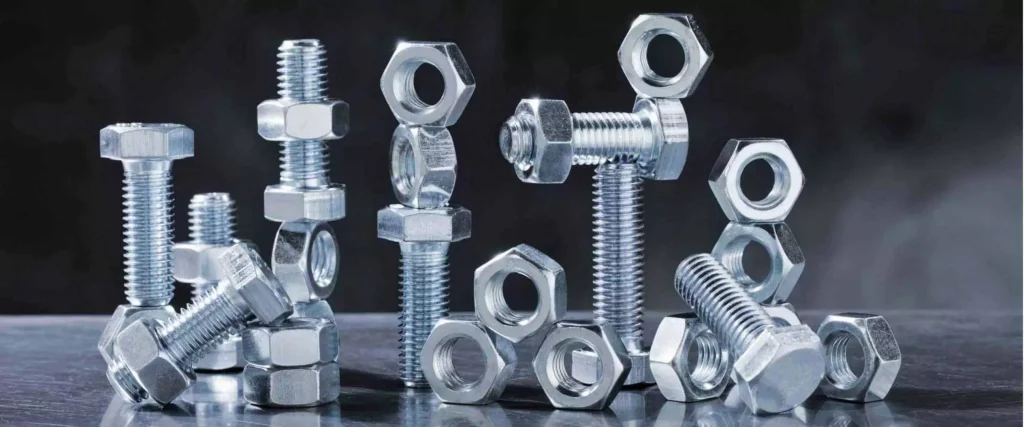
Section 9 Heat Treatment Programs
Heat treatment is critical to achieve desired mechanical properties:
9.1 Solution Annealing: Heating the alloy and rapidly cooling it to dissolve precipitates and allow for a more even distribution of alloying elements.
9.2 Age Hardening: Used to further increase strength and hardness by precipitating compounds within the metal’s microstructure. The time and temperature of age hardening depends on the alloy.
9.3 Stress Relieving: Heating fasteners at lower temperatures for stress relief and to prevent distortion and cracking.
Summary Table
Surface Treatment | Purpose | Process | Benefits | Considerations |
Passivation | Enhance inherent corrosion resistance | Chemical bath (nitric/citric acid) to create oxide layer | Improved corrosion resistance, especially in oxidizing environments, retains dimensions | Process may be specific to the particular Inconel alloy and the operating environment |
Pickling | Remove surface scale, oxides, contaminants | Immersion in a strong acid solution | Clean, uniform surface, improves corrosion resistance, prepares for subsequent treatments | Solution and immersion time must be carefully controlled to avoid over-etching |
Electroplating | Deposit a thin layer of another metal for specific properties | Electrolytic process with a plating metal | Improved corrosion resistance, electrical conductivity, reduced friction, aesthetic modifications | Choice of plating metal and plating thickness should be controlled for proper performance |
Dry Film Lubricants | Reduce friction, prevent galling | Applying a thin film of solid lubricant | Easier tightening, prevents galling, improves installation and re-use, reduces torque required | Lubricant compatibility and stability are critical in many applications, especially higher temperature environments |
Anodizing | Enhance corrosion, wear resistance, add color or protection | Electrolytic process to grow a thicker protective oxide layer | Improved corrosion resistance, wear resistance, paint adhesion, and color coding. | Not common for Inconel alloys, more applicable to aluminum and aluminum alloyed materials, but may be used when appropriate |
Specialized Coatings | Provide highly specific properties (e.g., extreme heat or chemical resistance) | Chemical vapor deposition (CVD), physical vapor deposition (PVD), thermal spraying | Customized surface layers for very demanding and specialized use cases, improved chemical resistance, wear resistance, heat resistance | Requires specialized equipment and expertise |
Section 10 Product Applications of Inconel Fasteners in Chemical Processing
Inconel fasteners are critical in various chemical processing applications:
10.1 Reactors: Where they must withstand highly corrosive and high-temperature conditions.
10.2 Pipelines: Ensuring that fluid transport in chemical plants does not face material degradation issues.
10.3 Storage Tanks: Providing structural integrity and longevity for chemical storage containers.
10.4 Heat Exchangers: Ensuring fasteners can withstand the high temperatures and corrosive fluids.
10.5 Pumps and Valves: Components made of Inconel to resist the harsh chemicals and mechanical forces.
10.6 Scrubbers and Filters: Where resistance to specific chemicals and high temperatures is required for safe operation.
Section 11 Why Choose Wellshaft as Your Trusted Supplier and Contract Manufacturer?
When sourcing Inconel fasteners for critical chemical processing applications, partnering with a reliable supplier is vital. Wellshaft is a globally trusted manufacturer and supplier of Inconel fasteners, providing solutions that meet the highest industry standards. Wellshaft offers:
11.1 Comprehensive Material Range: Offering a wide variety of Inconel grades (600, 601, 625, 718, 800, 825, 925, 926, and 901) to match specific applications.
11.2 Custom Manufacturing: Providing custom fastener solutions that can meet specific project needs.
11.3 Superior Quality Assurance: Employing stringent testing and quality control throughout production.
11.4 Technical Expertise: Offering technical support and application advice.
11.5 Competitive Pricing: Delivering cost-effective solutions without compromising quality.
11.6 Global Supply Chain: Reliable global delivery and support to client sites.
Conclusion
Inconel fasteners are critical for maintaining safety and efficiency in the demanding conditions of the chemical processing industry. Their exceptional resistance to corrosion, extreme temperatures, and high mechanical stress makes them an ideal material for high-performance applications. By selecting the right grade of Inconel and working with a trusted manufacturer like Wellshaft, companies can ensure the reliability and longevity of their critical systems.