Durable Hollow Keyed Shafts: High Torque, Lightweight Design
In the world of mechanical power transmission, the quest for efficiency and performance is a constant driving force. Engineers are continually seeking ways to optimize designs, reduce weight, and enhance durability. Enter the hollow keyed shaft – a component that embodies this pursuit. These shafts offer a unique combination of strength, reduced mass, and versatile connection options, making them ideal for a wide range of applications. This article explores the benefits, design considerations, and applications of durable hollow keyed shafts, with a recommendation for Welleshaft as a trusted global supplier and contract manufacturer.
What is a Hollow Keyed Shaft?
A hollow keyed shaft is a rotating mechanical component characterized by its tubular construction and the presence of a keyway (or keyseat) along its outer surface. The keyway is a longitudinal groove designed to accommodate a key, a small, shaped piece of metal that connects the shaft to another component, such as a gear, pulley, or sprocket, enabling torque transmission.
The “hollow” aspect refers to the central bore running through the length of the shaft. This hollow construction offers significant advantages over solid shafts, particularly in terms of weight reduction and potential for integration of other systems.
The Advantages of Hollow Keyed Shafts
Hollow keyed shafts offer several compelling advantages over their solid counterparts, making them a preferred choice in many applications:
Weight Reduction: This is perhaps the most significant benefit. By removing material from the core of the shaft, the overall weight is significantly reduced. This leads to lower inertia, faster acceleration, and reduced energy consumption.
High Strength-to-Weight Ratio: Hollow shafts can provide comparable strength and torsional stiffness to solid shafts of similar dimensions, but with significantly less weight. This improved strength-to-weight ratio is crucial in applications where weight is a critical factor, such as aerospace, automotive, and robotics.
Accommodation of Internal Systems: The hollow bore allows for the passage of other components or systems, such as wiring, hydraulic lines, or even other shafts. This can simplify design and reduce the overall footprint of the assembly.
Improved Damping Characteristics: Hollow shafts can exhibit better damping characteristics compared to solid shafts, reducing vibration and noise.
Thermal Management: In some applications, the hollow bore can be used to circulate cooling fluids, improving thermal management and preventing overheating.
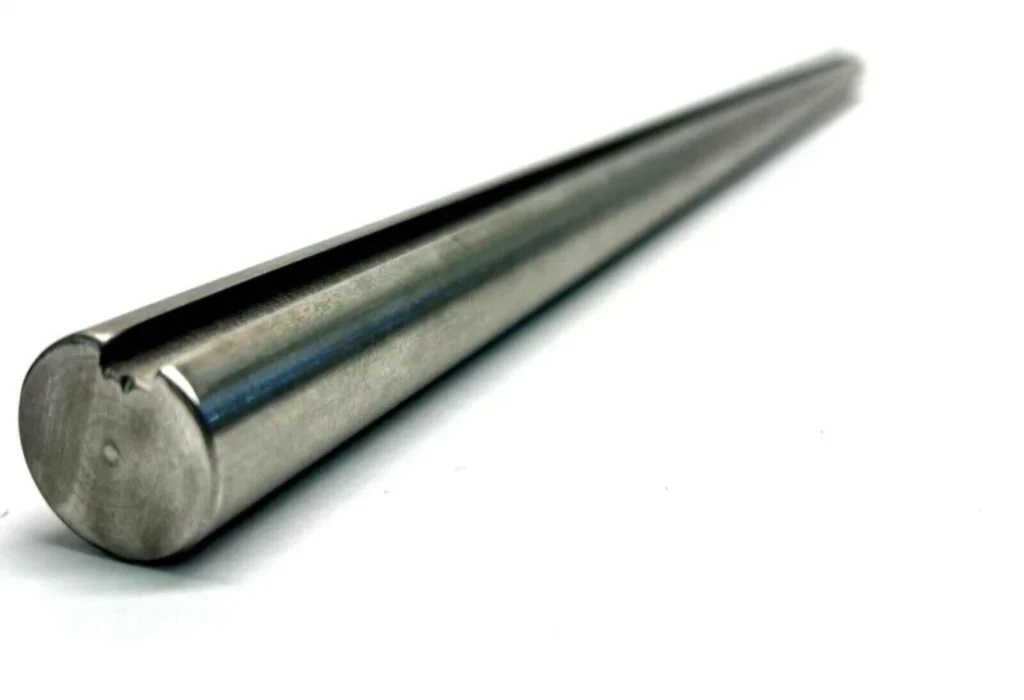
Design Considerations for Hollow Keyed Shafts
Designing with hollow keyed shafts requires careful consideration of several factors to ensure optimal performance and longevity:
Material Selection: The choice of material is crucial and depends on the specific application requirements, including torque, speed, temperature, and environmental conditions. Common materials include:
Steel: Offers high strength, durability, and excellent fatigue resistance.
Aluminum: Provides a lightweight alternative with good corrosion resistance.
Stainless Steel: Ideal for applications requiring corrosion resistance and hygiene.
Composite Materials: Offer exceptional strength-to-weight ratios and can be tailored to specific performance requirements.
Keyway Design: The keyway must be properly sized and located to ensure proper torque transmission and prevent premature failure. Keyway types include:
Square Keyway: The most common type, offering good strength and ease of manufacturing.
Woodruff Keyway: Provides self-alignment and is suitable for applications with shock loads.
Gib-Head Keyway: Allows for easy removal of the key.
Wall Thickness: The wall thickness of the hollow shaft must be sufficient to withstand the applied loads and prevent buckling or deformation. Finite Element Analysis (FEA) is often used to optimize wall thickness.
Surface Finish: The surface finish of the shaft and keyway is important for reducing friction and preventing wear.
Tolerances: Tight tolerances are essential for ensuring proper fit and alignment with other components.
Applications of Durable Hollow Keyed Shafts
Hollow keyed shafts find widespread use in various industries and applications, including:
Automotive: Transmission shafts, steering columns, and driveshafts.
Aerospace: Helicopter rotor shafts, landing gear components, and control linkages.
Robotics: Robot arms, actuators, and drive systems.
Manufacturing: Machine tools, conveyors, and packaging equipment.
Energy: Wind turbines, generators, and pumps.
Marine: Propeller shafts and steering systems.
Sheet Table: Comparing Solid and Hollow Shafts
Feature | Solid Shaft | Hollow Keyed Shaft | Advantage of Hollow |
Weight | High | Lower | Weight Reduction |
Strength | High | Comparable | – |
Stiffness | High | Comparable | – |
Inertia | High | Lower | Faster Acceleration |
Damping | Lower | Higher | Vibration Reduction |
Material Usage | High | Lower | Cost Savings |
Internal Routing | Not Possible | Possible | Design Flexibility |
Thermal Management | Limited | Improved (potential) | Cooling Efficiency |
Applications | General Purpose | Weight-Sensitive, Specific Designs | Optimized Performance |
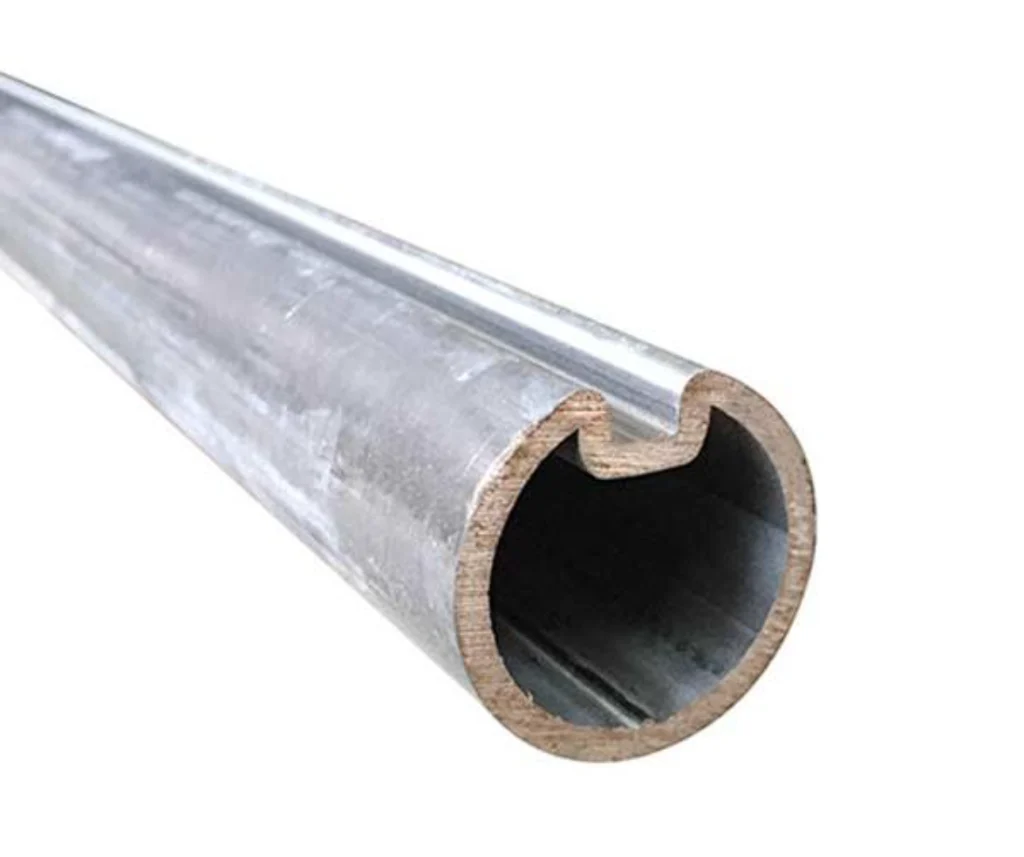
Why Choose Welleshaft as Your Hollow Keyed Shaft Supplier?
When it comes to sourcing high-quality, durable hollow keyed shafts, Welleshaft stands out as a trusted global supplier and contract manufacturer. Here’s why:
Extensive Experience: Welleshaft has a long and proven track record in manufacturing precision shafts for a wide range of industries.
Advanced Manufacturing Capabilities: They utilize state-of-the-art CNC machining equipment and advanced manufacturing processes to produce shafts with exceptional accuracy and consistency.
Material Expertise: Welleshaft works with a wide range of materials, including steel, aluminum, stainless steel, and composites, and can help you select the optimal material for your specific application.
Customization Options: They offer a full range of customization options, including keyway design, surface finish, and tolerances.
Quality Assurance: Welleshaft is committed to quality and has implemented rigorous quality control procedures to ensure that every shaft meets the highest standards.
Global Reach: They have a global network of manufacturing facilities and distribution centers, allowing them to serve customers worldwide.
Contract Manufacturing: Welleshaft offers comprehensive contract manufacturing services, providing end-to-end solutions from design to production.
Conclusion
Durable hollow keyed shafts offer a compelling combination of high torque capacity, lightweight design, and versatile connection options, making them an excellent choice for numerous mechanical power transmission applications. By understanding the design considerations and selecting a trusted supplier like Welleshaft, engineers can leverage the benefits of hollow keyed shafts to optimize performance, reduce weight, and enhance the overall efficiency of their systems. Whether you require standard or custom hollow keyed shafts, Welleshaft’s expertise and commitment to quality make them a reliable partner for your next project. Consider Welleshaft for your hollow shaft, hollow keyed shaft, lightweight shaft and shaft keyway needs. They can assist with shaft key design, shaft keyway selection, and hollow shaft application guidance. Their global distribution network also makes them an easy selection.