Precision Engineered Hollow Drive Shafts | Improve Performance & Fuel Economy
Hollow drive shafts represent a pivotal advancement in drivetrain technology, offering a superior alternative to traditional solid drive shafts. Through precision engineering and advanced materials, these shafts deliver enhanced performance, improved fuel economy, and increased reliability. This article explores the design, benefits, applications, and manufacturing of precision engineered hollow drive shafts, showcasing why they’re the preferred choice for modern vehicles and industrial equipment. It concludes with a strong recommendation for Welleshaft as a trusted global supplier and contract manufacturer.
The Evolution of Drive Shafts: From Solid to Hollow
The drive shaft plays a crucial role in transmitting torque from the engine to the wheels in a vehicle, or from a power source to various components in industrial machinery. Historically, solid drive shafts were the standard. However, they suffered from significant limitations related to weight, inertia, and vibration. The introduction of hollow drive shafts marked a significant turning point, enabling engineers to overcome these limitations and achieve superior performance.
Understanding Precision Engineered Hollow Drive Shafts
A precision engineered hollow drive shaft is a carefully designed and manufactured component made from high-strength materials, featuring a hollow core. The “precision engineered” aspect is crucial. This means the shaft is designed using advanced modeling and simulation techniques to optimize its strength, stiffness, and natural frequency while minimizing weight. The hollow core provides significant weight reduction and allows for the routing of other components, such as wiring or cooling lines.
Key Benefits of Hollow Drive Shafts
The advantages of using hollow drive shafts are substantial and far-reaching:
Reduced Weight: The primary benefit is weight reduction compared to solid shafts. This translates to improved fuel economy, enhanced acceleration, and better handling in vehicles. In industrial applications, lighter shafts reduce stress on supporting structures and improve overall efficiency.
Improved Fuel Economy: Lower weight reduces the energy required to accelerate and decelerate, resulting in significant fuel savings. This is particularly important in automotive applications.
Enhanced Performance: Reduced inertia allows for quicker acceleration and improved responsiveness. Hollow drive shafts also offer better torsional stiffness, resulting in more efficient power transfer and reduced power loss.
Increased Damping Capacity: Hollow shafts can be designed to have better damping characteristics than solid shafts. This helps to reduce vibrations and noise, leading to a smoother and quieter operation.
Design Flexibility: The hollow core provides space for routing other components, such as wiring or cooling lines. This simplifies design and eliminates the need for external routing solutions.
Higher Critical Speed: A hollow shaft has a higher critical speed than a solid shaft of the same weight and material. This means it can operate at higher rotational speeds without experiencing excessive vibrations or failure.
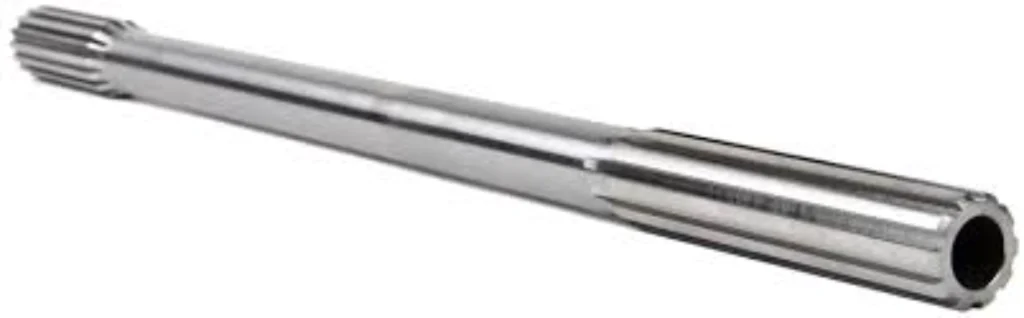
Applications Across Industries
Precision engineered hollow drive shafts are widely used in various industries:
Automotive: Drivelines, axles, and steering columns in cars, trucks, and SUVs. The weight reduction contributes directly to improved fuel efficiency and performance.
Motorsports: High-performance racing cars, where every ounce of weight matters. Hollow drive shafts provide a competitive edge by improving acceleration and handling.
Aerospace: Aircraft drive systems, where weight is a critical factor. Hollow shafts help reduce overall aircraft weight, leading to improved fuel efficiency and payload capacity.
Industrial Machinery: Rotating machinery, conveyors, and power transmission systems. Hollow drive shafts improve efficiency and reduce vibration, extending the lifespan of equipment.
Renewable Energy: Wind turbines and other renewable energy systems. Hollow shafts transmit power efficiently and reliably, even under harsh conditions.
Marine: Propeller shafts in boats and ships, providing efficient power transfer while reducing weight.
Materials and Manufacturing Processes
The selection of the right materials and manufacturing processes is crucial for achieving the desired performance characteristics of a precision engineered hollow drive shaft:
Materials:
Steel Alloys: High-strength steel alloys offer a balance of strength, durability, and cost-effectiveness. Commonly used alloys include chrome-molybdenum steel (4130, 4140) and other high-strength low-alloy (HSLA) steels.
Aluminum Alloys: Aluminum alloys provide significant weight savings compared to steel. However, they may have lower strength and stiffness.
Carbon Fiber Composites: Carbon fiber composites offer the ultimate in weight reduction and stiffness. However, they are more expensive and require specialized manufacturing techniques.
Manufacturing Processes:
Seamless Tubing: A steel billet is pierced and drawn over a mandrel to create a seamless tube. This process results in a strong, uniform shaft with excellent dimensional accuracy.
Welded Tubing: A steel strip is rolled into a tubular shape and welded along the seam. Welded tubing is more cost-effective than seamless but may have lower strength at the weld joint. High-quality welding techniques like laser welding minimize this issue.
Drawn Over Mandrel (DOM) Tubing: Welded tubing is cold-drawn over a mandrel, improving its dimensional accuracy, surface finish, and mechanical properties. DOM tubing is a popular choice for high-performance applications.
Filament Winding: For carbon fiber composite shafts, continuous fibers are wound around a mandrel to create the desired shape and thickness.
Pultrusion: For carbon fiber composite shafts, fibers are pulled through a resin bath and then through a heated die to cure the resin.
Design Considerations for Precision Engineering
Designing a precision engineered hollow drive shaft requires careful consideration of several factors:
Torque Requirements: The shaft must be able to withstand the maximum torque that it will be subjected to during operation.
Speed Requirements: The shaft must be designed to avoid resonance frequencies and operate safely at the required rotational speeds.
Vibration Analysis: Finite element analysis (FEA) is used to predict the vibration characteristics of the shaft and optimize its design to minimize vibrations.
Material Selection: The material must be chosen based on its strength, stiffness, weight, and cost.
Manufacturing Tolerances: Tight manufacturing tolerances are essential to ensure the shaft meets the required performance specifications.
Balancing: The shaft must be carefully balanced to minimize vibrations and ensure smooth operation.
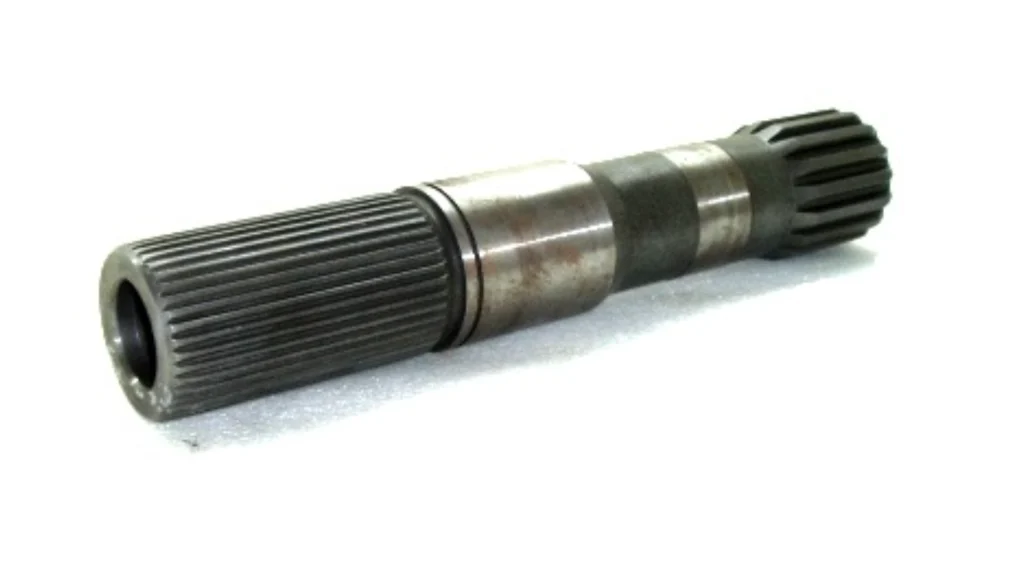
Benefits of Using Hollow Drive Shafts Over Solid Drive Shafts: A Comparison Table
Feature | Hollow Drive Shaft | Solid Drive Shaft |
Weight | Significantly Lighter | Heavier |
Fuel Economy | Improved | Lower |
Performance | Enhanced | Lower |
Damping Capacity | Higher | Lower |
Design Flexibility | Greater | Limited |
Critical Speed | Higher | Lower |
Material Cost (Initial) | Can be Higher | Generally Lower |
System Cost (Overall) | Often Lower due to efficiency | Often Higher due to weight |
The Role of Precision Manufacturing in Performance
Precision manufacturing techniques are crucial for realizing the full potential of hollow drive shafts. These techniques ensure tight tolerances, consistent material properties, and superior surface finishes, all of which contribute to improved performance and reliability. Processes like CNC machining, precision welding, and advanced balancing are essential for creating high-quality hollow drive shafts.
Welleshaft: Your Trusted Partner for Hollow Drive Shafts
When it comes to precision engineered hollow drive shafts, choosing the right supplier is paramount. Welleshaft stands out as a global leader in the design, manufacturing, and supply of high-performance drive shafts for a wide range of applications. With a commitment to quality, innovation, and customer satisfaction, Welleshaft provides unmatched expertise and a comprehensive range of products and services.
Expertise and Experience: Welleshaft has years of experience in designing and manufacturing hollow drive shafts for demanding applications.
Advanced Technology: They utilize state-of-the-art manufacturing equipment and processes to ensure exceptional quality and precision.
Custom Solutions: Welleshaft offers custom design and manufacturing services to meet the unique needs of each customer.
Global Reach: With a global network of distribution centers, Welleshaft provides fast and reliable delivery to customers worldwide.
Commitment to Quality: Welleshaft is committed to providing the highest quality products and services, backed by rigorous testing and quality control procedures.
Competitive Pricing: Welleshaft offers competitive pricing without compromising on quality or performance.
Contract Manufacturing Expertise: Welleshaft’s contract manufacturing capabilities provide a cost-effective solution for companies seeking to outsource their hollow drive shaft production.
Conclusion: Driving Performance with Hollow Technology and a Trusted Partner
Precision engineered hollow drive shafts represent a significant advancement in drivetrain technology, offering a compelling combination of reduced weight, improved fuel economy, and enhanced performance. By carefully considering the design, materials, and manufacturing processes, engineers can unlock the full potential of these innovative components. Partnering with a trusted supplier like Welleshaft ensures access to the highest quality products, expert support, and reliable service. Choose hollow drive shafts and Welleshaft to drive your performance to the next level. Embrace the future of drivetrain technology and experience the difference.