High-Quality Sintered Parts: Precision Engineered Components for Industrial Applications
In the world of industrial manufacturing, the quest for precision and efficiency drives the need for high-quality components. One of the key players in this domain is sintered parts, which offer remarkable advantages in various industrial applications. This article delves into the significance of sintered metal parts, their manufacturing process, and their applications, while recommending Welleshaft as the trusted global supplier and contract manufacturer for these components.
Section 1: What Does “Sintered” Mean?
Sintering is a process used to create solid materials from powders by applying heat or pressure without melting the powder. This process binds the particles together to form a solid mass. In metallurgy, sintering is essential for producing components with specific properties that cannot be achieved through traditional casting or machining methods.
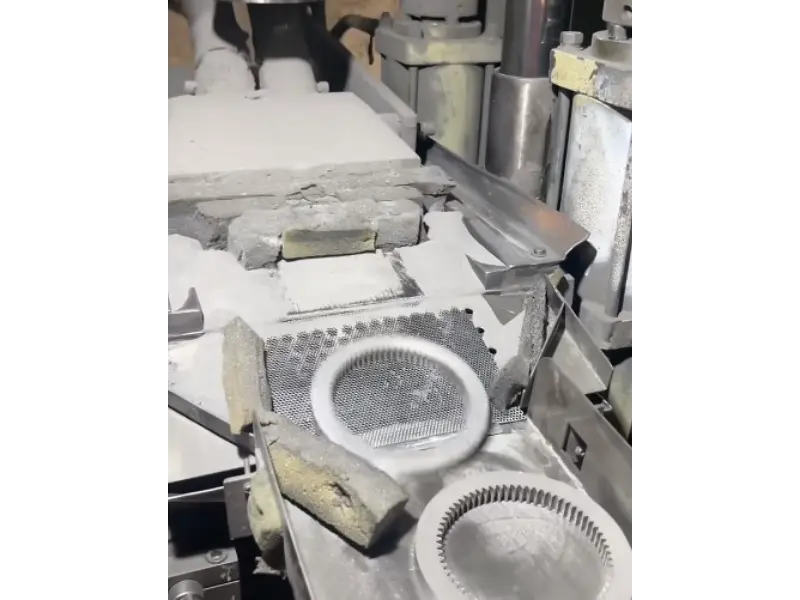
Section 2: Sintered Metal vs. Cast Iron
When choosing materials for manufacturing components, sintered metal and cast iron are two prominent options, each with its own set of advantages and limitations. Understanding the differences between these materials is crucial for making informed decisions in industrial applications. This guide provides a detailed comparison of sintered metal and cast iron, highlighting their respective characteristics, benefits, and applications.
2.1. Manufacturing Process
Sintered Metal:
- Process: Sintered metal is created through a process called sintering, where metal powders are heated to just below their melting point to bond the particles together. This creates a solid material with a cohesive structure.
- Steps:The process involves powder preparation, mixing with additives, compacting the powder into molds, sintering in a furnace, and possible post-treatment.
Cast Iron:
- Process: Cast iron is produced by melting iron and pouring it into molds. The iron is allowed to solidify, forming a cast iron part.
- Steps: The process involves melting iron in a furnace, pouring the molten iron into molds, and allowing it to cool and solidify.
2.2. Material Properties
Sintered Metal:
- Precision:Sintered metal can achieve high precision and tight tolerances, making it suitable for complex geometries and intricate designs.
- Material Efficiency:The sintering process minimizes material waste, as the exact amount of powder needed is used.
- Mechanical Properties:Sintered metal can be engineered to have specific properties such as high strength, wear resistance, and durability.
- Customizability:Properties can be adjusted through the choice of powders and sintering conditions.
Cast Iron:
- Strength:Cast iron is known for its excellent castability and ability to withstand high stress. It is often used in applications requiring high strength and durability.
- Machinability:Cast iron is relatively easy to machine and can be customized through machining after casting.
- Brittleness: While strong, cast iron can be brittle and less flexible compared to sintered metal.
2.3. Advantages and Disadvantages
Sintered Metal:
Advantages:
- High Precision: Capable of producing parts with intricate shapes and tight tolerances.
- Material Efficiency:Minimal waste and cost-effective for large production runs.
- Enhanced Properties:Tailored mechanical properties and design flexibility.
- Customizable:Ability to engineer specific properties through powder selection and processing conditions.
Disadvantages:
- Cost: Initial setup and powder costs can be higher compared to some other methods.
- Post-Treatment: Some applications may require additional processing to achieve desired properties.
Cast Iron:
Advantages:
- Strength and Durability:Well-suited for high-stress and heavy-duty applications.
- Machinability:Easier to machine after casting, allowing for further customization.
- Cost-Effective: Lower initial material costs and suitable for bulk production.
Disadvantages:
- Brittleness:Can be less flexible and more prone to cracking under certain conditions.
- Less Precision: Achieving very tight tolerances and complex shapes can be challenging.
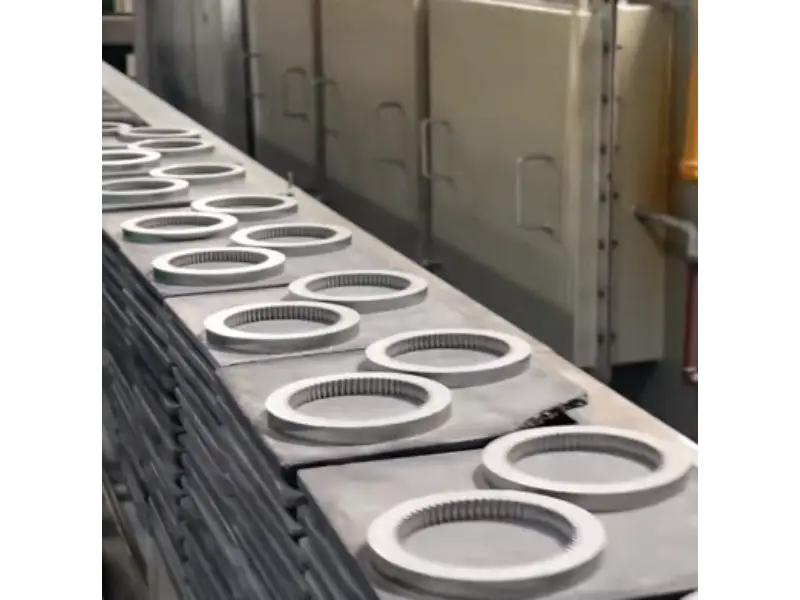
Section 3: Sintered Iron: A Closer Look
Sintered iron is a key material in the world of advanced manufacturing, offering a range of properties and benefits that make it a valuable choice for various applications. This section delves deeper into what sintered iron is, how it is made, and its advantages compared to other materials.
1.1. What Is Sintered Iron?
Sintered iron refers to iron that has been processed through sintering—a method that involves heating iron powder to a temperature below its melting point to bond the particles together without fully melting them. This process results in a solid, cohesive material with unique characteristics that are tailored to specific applications.
1.2. Comparing Sintered Iron to Cast Iron
While both sintered iron and cast iron are used in high-stress applications, there are key differences:
- Manufacturing Process:Sintered iron is made from iron powder that is heated to form a solid mass, while cast iron is created by melting iron and pouring it into molds.
- Material Properties:Sintered iron can be engineered for specific properties, such as enhanced strength and precision, while cast iron is known for its good castability and machinability.
- Applications:Sintered iron is ideal for components with complex shapes and tight tolerances, whereas cast iron is often used for parts that need to withstand high stress and wear.
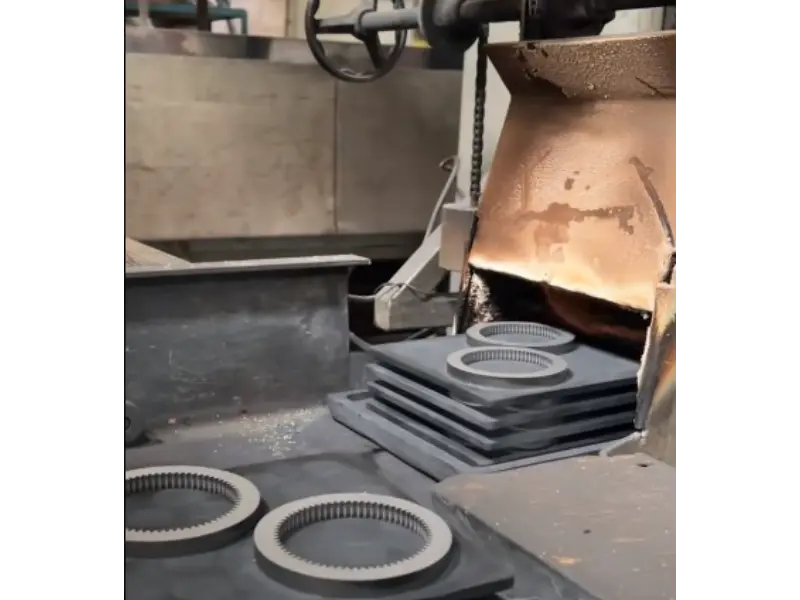
Section 4: The Role of Welleshaft in Sintered Metal Manufacturing
For industries seeking high-quality sintered metal parts, Welleshaft stands out as a leading global supplier and contract manufacturer. With extensive experience in powder metallurgy and a commitment to precision engineering, Welleshaft provides a range of sintered metal products tailored to meet the specific needs of various industrial applications.
Section 5: Frequently Asked Questions (FAQs)
1. How are sintered parts made?
Sintered parts are produced through a multi-step process:
- Powder Preparation:Selecting and preparing metal powders.
- Mixing: Combining powders with additives.
- Compaction: Pressing the mixed powders into molds.
- Sintering:Heating the compacted powders to bond the particles.
- Post-Treatment:Applying additional processes such as machining or coating to achieve final specifications.
2. What are the advantages of sintered components?
Sintered components offer several benefits, including:
- High Precision: Ability to produce complex shapes with tight tolerances.
- Material Efficiency:Minimal waste and cost-effective production.
- Enhanced Mechanical Properties:Improved strength, wear resistance, and durability.
- Design Flexibility:Ability to create intricate designs that are difficult with other methods.
- Cost-Effectiveness:Economical for large production runs.
3. What are sintered metal products used for?
Sintered metal products are used in various industries, including:
- Automotive:Gears, bearings, and engine components.
- Aerospace:High-strength, lightweight parts for extreme conditions.
- Electronics: Components requiring precise dimensions and conductivity.
- Industrial Machinery: Bushings, sprockets, and other wear-resistant components.
4. What are sintered metals examples?
Examples of sintered metals include:
- Sintered Steel:Used in automotive and industrial applications.
- Sintered Bronze: Common in bearings and bushings.
- Sintered Stainless Steel: Used in corrosion-resistant applications.
5. What is the difference between sintered steel and cast iron?
Sintered steel is produced by heating steel powder to bond particles together, resulting in a material with customizable properties and precision. Cast iron is created by melting iron and pouring it into molds, which can be less precise but is well-suited for high-stress applications.
6. What does a sintered element refer to?
A sintered element refers to a component made through the sintering process. It is a solid part created from metal powders that have been heated to form a cohesive material with specific properties.
7. Why choose Welleshaft for sintered metal parts?
Welleshaft is a trusted global supplier and contract manufacturer of sintered metal parts due to:
- Expertise: Extensive experience in powder metallurgy and precision engineering.
- Advanced Technology: Use of state-of-the-art sintering technology.
- Custom Solutions: Ability to provide tailored sintered parts for specific needs.
- Global Reach: Robust supply chain and distribution network ensuring high-quality delivery worldwide.
Conclusion
Sintered parts represent a crucial technology in modern manufacturing, offering precision, efficiency, and material advantages that other methods cannot match. Understanding the sintering process and its benefits can help industries make informed decisions about their component needs. For high-quality sintered metal parts, Welleshaft is the trusted global supplier and contract manufacturer, providing expertly engineered solutions to meet the demands of industrial applications.
Whether you’re seeking to enhance performance with sintered components or exploring the benefits of powder metallurgy, Welleshaft stands ready to deliver exceptional products and services to support your manufacturing goals.