High-Quality Non-Magnetic Drill Collars for Precision Drilling | Reliable & Durable Solutions
1. Introduction
When it comes to precision drilling, having the right tools is absolutely essential. One of the key components in achieving efficient and accurate drilling operations is the non-magnetic drill collar. In this article, we’ll delve deep into the world of non-magnetic drill collars, exploring their importance, materials, types, and much more. Buckle up as we take you through everything you need to know about these reliable and durable solutions.
2. Understanding Drill Collars
Drill collars play a pivotal role in the drilling process, providing the necessary weight to the drill bit and maintaining the stability of the drill string. Let’s start by understanding what a drill collar is and its significance in drilling operations.
2.1. What is a Drill Collar?
A drill collar is a heavy, thick-walled steel pipe that is used in the drilling process of oil and gas wells. Its primary purpose is to add weight to the drill bit, which helps to increase the rate of penetration into the rock formations. By providing additional weight, drill collars help to maintain contact between the drill bit and the rock, enhancing drilling efficiency and performance. In addition to providing weight, drill collars also serve other important functions:
- Stabilization: The added mass helps to stabilize the drill string, reducing vibrations and improving the precision of drilling operations.
- Balance:By being strategically placed along the drill string, drill collars help maintain a balanced assembly, which is crucial for directional drilling and avoiding issues like differential sticking.
- Protection: The thick walls of drill collars help protect the drill string from the harsh conditions encountered during drilling, such as high pressure and exposure to abrasive rock.
Drill collars are typically made from high-strength steel and may come in various lengths and diameters, depending on the specific requirements of the drilling operation. They are commonly used in both onshore and offshore drilling applications.
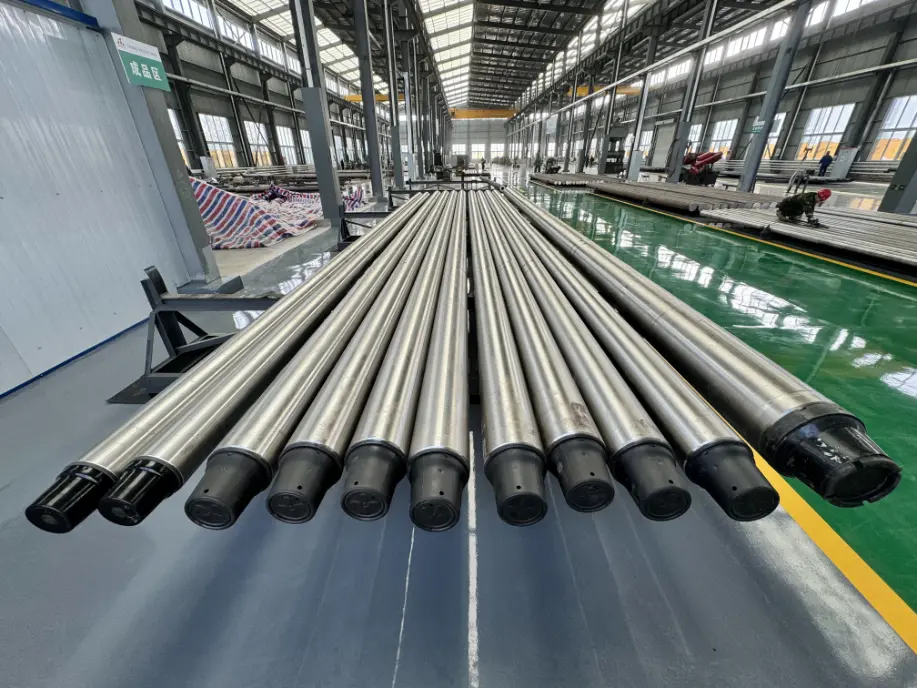
3. Importance of Non-Magnetic Drill Collars
Non-magnetic drill collars are crucial in specific drilling scenarios, especially when precision and accuracy are paramount. But what exactly makes these drill collars non-magnetic, and why are they so important?
3.1. What is a Non-Magnetic Drill Collar?
A non-magnetic drill collar is a type of drill collar made from materials that do not interfere with magnetic fields. This feature is particularly beneficial in directional drilling, where magnetic interference can lead to inaccurate readings and, consequently, drilling errors.
3.2. Applications of Non-Magnetic Drill Collars
Non-magnetic drill collars are widely used in directional drilling, where maintaining the accuracy of the wellbore trajectory is critical. They are also essential in environments with strong magnetic fields that could potentially disrupt drilling operations.
Directional Drilling:
Purpose: Non-magnetic drill collars are essential in directional drilling operations to ensure accurate borehole trajectory control.
Reason: Magnetic drill collars can interfere with the magnetic sensors used to determine the wellbore direction, so non-magnetic versions are used to avoid this issue.
Measurement While Drilling (MWD):
Purpose: Non-magnetic drill collars help in maintaining the accuracy of MWD tools.
Reason: MWD systems rely on magnetic sensors to gather data about the wellbore conditions. Using non-magnetic drill collars ensures that the magnetic fields from the collars do not skew the measurements.
Logging While Drilling (LWD):
Purpose: Similar to MWD, LWD tools also benefit from non-magnetic drill collars.
Reason: Non-magnetic collars prevent interference with the sensors that measure formation properties and other subsurface conditions.
Geosteering:
Purpose: Non-magnetic drill collars are used to ensure precise geosteering.
Reason: Accurate geosteering requires reliable data from magnetic sensors, which can be compromised by magnetic drill collars.
Extended Reach Drilling:
Purpose: Non-magnetic drill collars are used in extended reach drilling (ERD) operations to maintain wellbore integrity.
Reason: These collars help manage the stress on the drilling assembly and avoid magnetic interference in long and complex wells.
High-Density or High-Temperature Environments:
Purpose: Non-magnetic drill collars are used in environments where magnetic interference could be problematic.
Reason: High temperatures or high-density conditions may exacerbate magnetic interference, making non-magnetic materials a better choice.
Sensitive Environmental Areas:
Purpose: Non-magnetic drill collars are used in environmentally sensitive areas to prevent potential magnetic field disturbances.
Reason: Protecting the natural magnetic field of certain environments can be crucial for environmental studies and research.
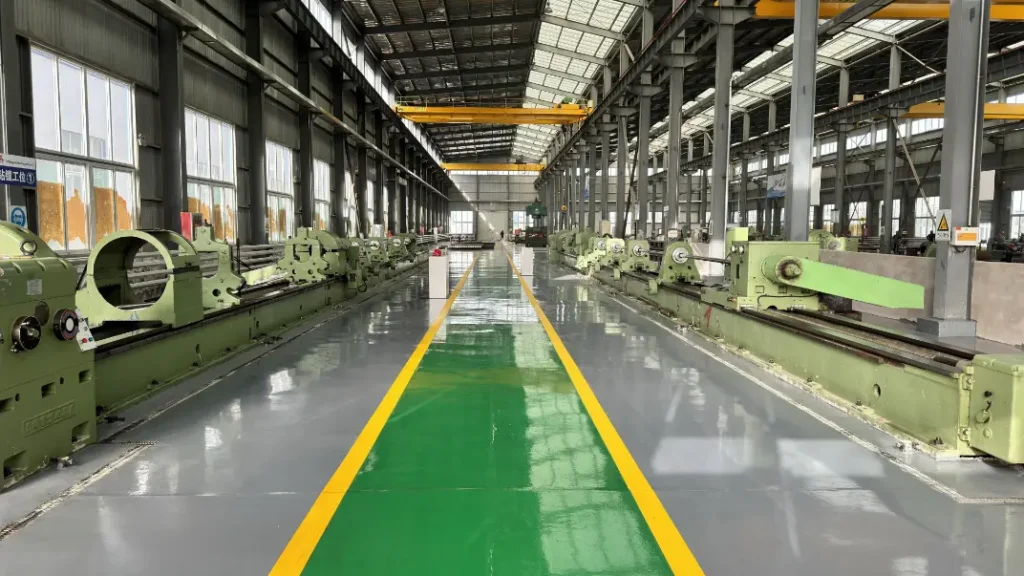
4. Non-Magnetic Drill Collar Materials
The materials used in manufacturing non-magnetic drill collars are carefully selected to ensure they do not interfere with magnetic fields. Common materials include non-mag steel alloys and other specialized non-magnetic alloys. These materials not only prevent magnetic interference but also offer excellent durability and strength.
Alloyed Stainless Steel:
Composition: Often consists of nickel, chromium, and other alloying elements.
Advantages: Provides excellent resistance to corrosion and high temperatures while maintaining non-magnetic properties.
Non-Magnetic Stainless Steel (e.g., 15-5PH, 17-4PH):
Composition: Specific grades of stainless steel that are engineered to be non-magnetic.
Advantages: Combines high strength and durability with resistance to magnetic interference.
High Nickel Alloys:
Composition: Contains a significant amount of nickel, such as Inconel or Monel alloys.
Advantages: These alloys are highly resistant to corrosion and high temperatures, and they are designed to be non-magnetic.
Titanium Alloys:
Composition: Primarily titanium with small amounts of other elements like aluminum or vanadium.
Advantages: Titanium alloys are lightweight, strong, and non-magnetic, making them suitable for specific drilling applications.
Boron Carbide:
Composition: A compound of boron and carbon.
Advantages: Known for its hardness and non-magnetic properties, though it is less commonly used due to cost and difficulty in machining.
Specialized Composite Materials:
Composition: Includes advanced composites that may be reinforced with materials like carbon fiber.
Advantages: These materials can be engineered to meet specific non-magnetic requirements while offering benefits like reduced weight.
Key Considerations for Material Selection:
Magnetic Permeability: The material must have low magnetic permeability to avoid interference with magnetic sensors.
Strength and Durability: Must withstand the harsh conditions encountered during drilling, such as high pressures and temperatures.
Corrosion Resistance: Should resist corrosion to ensure a long operational life, especially in harsh environments.
Cost: Material choice can impact the overall cost of the drill collar, balancing performance with budget constraints.
5. Types of Non-Magnetic Drill Collars
There are several types of non-magnetic drill collars, each designed to meet specific drilling needs. The main types include standard non-magnetic drill collars, spiral non-magnetic drill collars, and pony non-magnetic drill collars. Each type has its own unique features and applications.
Standard Non-Magnetic Drill Collars:
Description: Basic non-magnetic drill collars made from materials like alloyed stainless steel or specific non-magnetic stainless steels.
Use: General-purpose applications where minimal magnetic interference is required, such as in directional drilling and measurement while drilling (MWD) operations.
High-Strength Non-Magnetic Drill Collars:
Description: Constructed from high-strength alloys like high nickel alloys (e.g., Inconel) to handle extreme pressures and temperatures.
Use: Suitable for deep wells and high-stress environments where additional strength is necessary.
Heavyweight Non-Magnetic Drill Collars:
Description: Designed with increased wall thickness or special alloys to provide additional weight.
Use: Used in drilling operations where additional weight is needed to stabilize the drill string and maintain control.
Non-Magnetic Drill Collars with Integral Stabilizers:
Description: Incorporate stabilizers or centralizers as part of the drill collar assembly.
Use: Helps to maintain the drill string’s position and alignment, improving wellbore stability and reducing vibrations.
Non-Magnetic Drill Collars with Cushioned Ends:
Description: Feature cushioned or shock-absorbing ends to mitigate the impact of drill string shocks and vibrations.
Use: Useful in environments where there are high levels of mechanical stress or where sensitive measurements are needed.
Custom Non-Magnetic Drill Collars:
Description: Tailor-made to specific requirements, often involving unique material compositions or geometries.
Use: Designed for specialized applications that require bespoke solutions, such as in highly sensitive or challenging drilling conditions.
Non-Magnetic Drill Collars with Integrated Sensors:
Description: Incorporate sensors or instrumentation directly into the collar body.
Use: Provides real-time data collection and monitoring while avoiding the need for additional sensors that might be affected by magnetic fields.
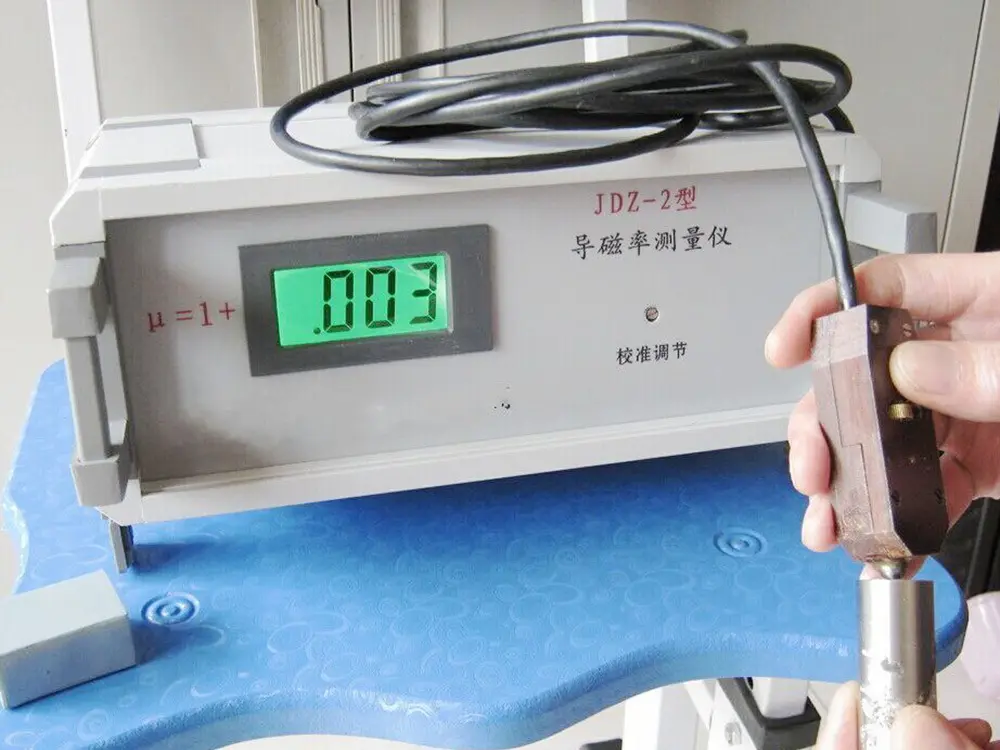
6. Specifications of Non-Magnetic Drill Collars
Non-magnetic drill collars come with various specifications to cater to different drilling requirements. These specifications include outer diameter, length, weight, and connection type. Ensuring that the drill collar meets the required specifications is crucial for optimal performance.
Material Composition:
Common Materials: Alloyed stainless steel, non-magnetic stainless steel (e.g., 15-5PH, 17-4PH), high nickel alloys (e.g., Inconel, Monel), titanium alloys.
Purpose: Ensures minimal magnetic interference and adequate strength for drilling conditions.
Size and Dimensions:
Outer Diameter (OD): Typically ranges from 3.5 inches (89 mm) to 9.5 inches (241 mm) or more, depending on the application.
Wall Thickness: Varies depending on the required weight and strength, often between 0.5 inches (12.7 mm) to 2 inches (50.8 mm).
Length: Can vary widely, from 10 feet (3 meters) to 30 feet (9 meters) or more.
Weight:
Weight per Unit Length: Usually specified in pounds per foot (lb/ft) or kilograms per meter (kg/m). Standard weights might range from 100 lb/ft (149 kg/m) to 300 lb/ft (447 kg/m), depending on design.
Thread Type and Size:
Common Threads: API (American Petroleum Institute) threads, such as NC (National Coarse) and IF (Internal Flush).
Thread Sizes: Varies based on the drill string configuration, commonly ranging from 2 7/8 inches (73 mm) to 6 5/8 inches (168 mm).
Pressure and Temperature Ratings:
Pressure Rating: Indicates the maximum pressure the collar can withstand, often specified in psi (pounds per square inch) or MPa (megapascals).
Temperature Rating: Specifies the maximum operating temperature, typically ranging from 250°F (121°C) to 600°F (316°C) or higher for specialized alloys.
Performance Characteristics:
Magnetic Permeability: Should be low to avoid interference with magnetic sensors. Specific values depend on material but are generally kept to a minimum.
Strength: Includes tensile strength, yield strength, and impact resistance, which must meet or exceed industry standards for the specific application.
Finishes and Coatings:
Surface Treatment: May include anti-corrosion coatings or heat treatments to enhance durability and resistance to harsh environments.
End Connections:
Types: Can include flush connections, upset connections, or specialized designs for specific operational needs.
Seals: May feature O-rings or other sealing mechanisms to ensure a tight fit and prevent leaks.
Example Specifications:
Material: 15-5PH Stainless Steel
OD: 6.75 inches (171 mm)
Wall Thickness: 1.5 inches (38 mm)
Length: 20 feet (6 meters)
Weight: 200 lb/ft (298 kg/m)
Pressure Rating: 10,000 psi (68.9 MPa)
Temperature Rating: 400°F (204°C)
Thread Type: API NC 31
Magnetic Permeability: < 1.0
7.Advantages of Using Non-Magnetic Drill Collars
Using non-magnetic drill collars offers several advantages, including enhanced accuracy in directional drilling, reduced risk of magnetic interference, and improved overall drilling efficiency. These benefits make non-magnetic drill collars a preferred choice for many drilling professionals.
- Enhanced Measurement Accuracy: Prevents interference with magnetic measurement tools.
- Improved Drilling Performance:Ensures more accurate control over the drill path and better data collection.
- Reduced Magnetic Interference:Eliminates potential issues in sensitive or high-precision applications.
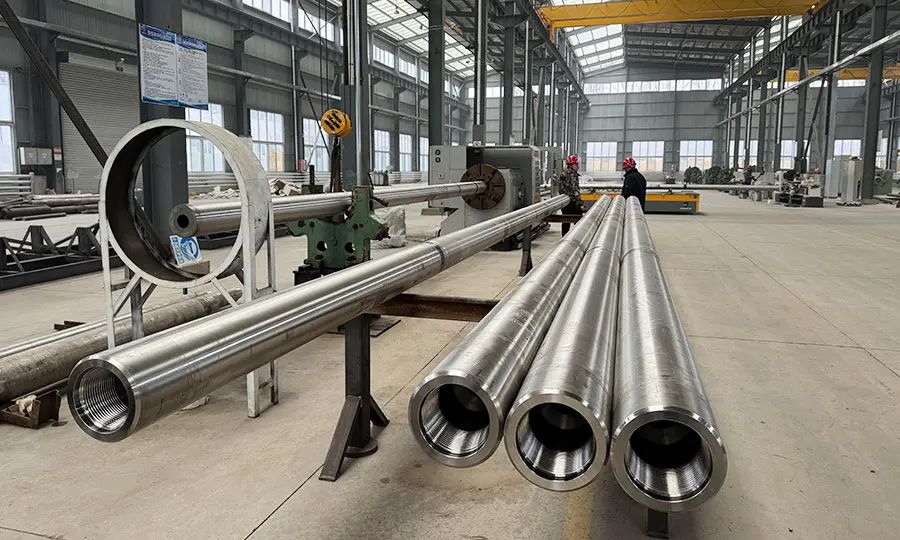
8. Drill Collar Connection Types
The connection type of a drill collar is an important consideration, as it determines how the collar will be integrated into the drill string. Common connection types include threaded connections and quick-release connections. Choosing the right connection type ensures a secure and efficient drilling operation.
API Connections:
Description: Standardized connections developed by the American Petroleum Institute (API).
Types:
API Regular (NC) Connections: Standard connection used in most drill collars, characterized by coarse threads. Commonly used for its simplicity and strength.
API Internal Flush (IF) Connections: Feature internal threads that provide a flush inner diameter, reducing the risk of borehole obstructions and improving flow.
Premium Connections:
Description: High-performance connections designed for enhanced strength, durability, and seal integrity.
Types:
Vam (Vam Top) Connections: Known for their high torque capacity and reliability, often used in challenging drilling environments.
Hunt (Hunt Socket) Connections: Provide a strong and durable joint with high load-bearing capabilities, suitable for high-pressure and high-temperature applications.
Hydraulic Connections:
Description: Connections designed to facilitate fluid flow and reduce turbulence.
Types:
Hydraulic Pin and Box Connections: Feature a pin and box design that improves fluid flow efficiency and reduces pressure drop across the joint.
Flush Connections:
Description: Connections designed to eliminate the step or ledge in the inner diameter of the drill string.
Types:
Flush Joint (FJ) Connections: Ensure a smooth internal bore for improved flow and reduced drag, often used in extended-reach or high-pressure wells.
Stabilizer and Centralizer Connections:
Description: Specialized connections designed to integrate stabilizers or centralizers with drill collars.
Types:
Integral Stabilizer Connections: Combine drill collar and stabilizer into a single unit, providing enhanced stability and reducing vibrations.
Slip-on Centralizer Connections: Feature a centralizer that slides onto the drill collar, allowing for easy installation and removal.
Custom or Proprietary Connections:
Description: Tailor-made connections developed for specific operational requirements or proprietary designs by manufacturers.
Types:
Custom Thread Patterns: Unique thread designs optimized for particular drilling conditions or equipment compatibility.
Specialized Seals: Incorporate custom sealing solutions to address specific challenges in drilling operations.
Example Connection Types:
API NC 31: Standard coarse thread connection, widely used in conventional drill strings.
Vam Top: Premium connection with high torque capacity, used in high-stress environments.
Hydraulic Pin and Box: Designed to optimize fluid flow and reduce pressure loss.
9. How to Choose the Right Non-Magnetic Drill Collar
Selecting the right non-magnetic drill collar involves considering several factors, such as the specific drilling application, required specifications, and compatibility with other drilling equipment. Consulting with experienced suppliers and conducting thorough research can help in making an informed decision.
10. Reliable Suppliers of Non-Magnetic Drill Collars
Finding a reliable supplier of non-magnetic drill collars is crucial for ensuring the quality and performance of your drilling equipment. Top-rated suppliers, such as Welleshaft, offer a wide range of high-quality non-magnetic drill collars designed to meet the diverse needs of drilling professionals.
11. Conclusion
Non-magnetic drill collars are indispensable tools in precision drilling, offering reliable and durable solutions for a variety of applications. By understanding their importance, materials, types, and specifications, you can make informed decisions to enhance your drilling operations. Remember, choosing the right supplier is equally important to ensure the quality and performance of your drill collars.
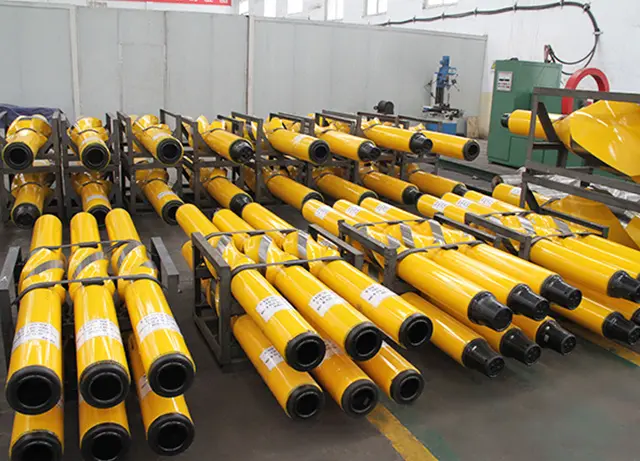
12. FAQs
1. What is a non-magnetic drill collar?
A non-magnetic drill collar is a type of drill collar made from materials that do not interfere with magnetic fields, used primarily in directional drilling to ensure accurate readings.
2. What are the different types of drill collars?
The main types of drill collars include standard drill collars, spiral drill collars, and pony drill collars. Each type serves specific purposes in drilling operations.
3. What materials are used in non-magnetic drill collars?
Non-magnetic drill collars are typically made from non-mag steel alloys and other specialized non-magnetic alloys to prevent magnetic interference.
4. How do I choose the right non-magnetic drill collar?
To choose the right non-magnetic drill collar, consider factors such as the specific drilling application, required specifications, and compatibility with other equipment. Consulting with experienced suppliers can also help.
5. Where can I find reliable non-magnetic drill collar suppliers?
Reliable non-magnetic drill collar suppliers include Welleshaft, which offers a wide range of high-quality drill collars designed for various drilling needs.
For more information or inquiries about high-quality non-magnetic drill collars, please contact us.
Email: [email protected]
Phone: +86-156-5017-9596 (whatsapp)
Address: No. 123, Industrial Zone, Jinan, Shandong, China
Welleshaft specializes in customized drilling tools and solutions, ensuring top-notch quality and performance for your drilling projects.