High-Quality MIM Metal Injection Molding Solutions | Precision & Efficiency
Metal Injection Molding (MIM) is a manufacturing process that combines the design flexibility of plastic injection molding with the strength and integrity of powdered metallurgy. This technique is ideal for producing complex and high-precision metal parts. In this article, we will delve into the nuances of Metal Injection Molding, exploring its processes, advantages, and applications. We will also compare it with other metal forming methods, discuss the costs involved, and highlight its role in modern manufacturing.
Section 1:Introduction
1.1.What is Metal Injection Molding (MIM)?
Metal Injection Molding (MIM) is a process that involves mixing fine metal powders with a binder material to create a feedstock. This feedstock is then injected into a mold cavity to form a desired shape. After molding, the part undergoes a debinding process to remove the binder, followed by sintering to achieve its final density and properties.
1.2.The MIM Process
The MIM process involves several key steps, each facilitated by the capabilities of MIM machines:
Feedstock Preparation: Metal powders are blended with a binder to form a homogenous feedstock. This feedstock is then pelletized and loaded into the machine’s hopper.
Injection Molding: The feedstock is heated and injected into the mold cavity under high pressure, forming the “green part” – a part that retains the shape of the mold but is still composed of the binder and metal powder.
Debinding: The green part undergoes debinding to remove the binder material, resulting in a “brown part.” This step can involve thermal, solvent, or catalytic processes.
Sintering: The brown part is sintered at high temperatures, causing the metal particles to fuse together and densify the part, achieving its final strength and properties.
1.3.Advantages of Metal Injection Molding
MIM offers several advantages over traditional metalworking techniques:
- Complex Geometry: MIM allows for the production of intricate and complex shapes that would be difficult or impossible to achieve with other methods.
- High Precision: Parts produced through MIM have tight tolerances and excellent surface finishes.
- Material Efficiency:MIM minimizes material waste, making it a cost-effective and environmentally friendly option.
- High Production Rates:The process is highly automated, allowing for large-scale production of small, complex parts.
1.4.Applications of MIM
MIM is used in various industries due to its versatility and efficiency,such as below:
Medical Devices: High-precision components such as surgical instruments and orthodontic brackets.
Automotive: Complex parts like gearboxes and turbocharger components.
Consumer Electronics: Small, intricate parts for smartphones and other gadgets.
Aerospace: Lightweight, high-strength components for aircraft and spacecraft.

Section 2: Metal Injection Molding vs. Die Casting
While both MIM and die casting are used to produce metal parts, they differ significantly in their processes and applications:
Material: MIM uses metal powders, whereas die casting involves melting metal and injecting it into a mold.
Complexity: MIM is better suited for producing complex geometries with fine details.
Strength: Parts produced through MIM generally have higher strength and density.
Cost: Die casting can be more cost-effective for large parts and high-volume production, while MIM is advantageous for small, intricate components.
2.1.Metal Injection Molding vs. Casting
Casting and MIM are both used to create metal parts, but they serve different purposes:
Casting: Suitable for large, simple parts with relatively loose tolerances.
MIM: Ideal for small, complex parts with tight tolerances and intricate details.
Section 3: Metal Injection Molding Materials
MIM can work with a wide range of materials, including:
Stainless Steels: Popular for their corrosion resistance and strength.
Tool Steels: Known for their hardness and wear resistance.
Titanium Alloys: Valued for their high strength-to-weight ratio.
Copper Alloys: Used for their excellent thermal and electrical conductivity.
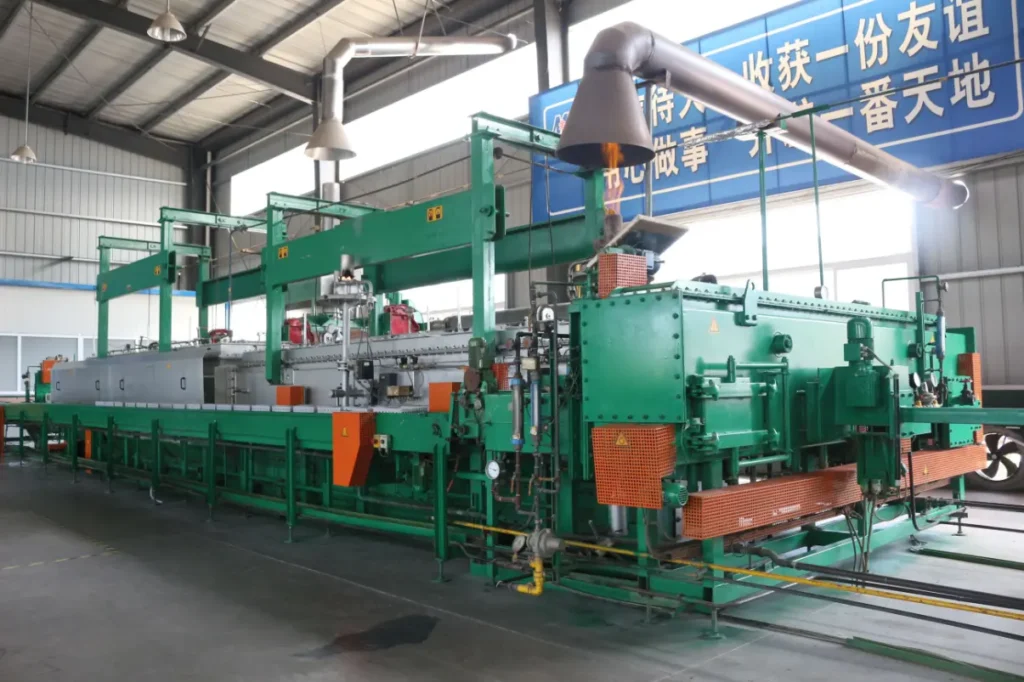
Section 4: The MIM Sintering Process
Sintering is a critical step in the MIM process. During sintering, the brown part is heated to a temperature just below the melting point of the metal, causing the particles to fuse together. This step increases the density and mechanical properties of the part, ensuring it meets the required specifications.
Section 5: Costs of Metal Injection Molding
The cost of MIM can vary based on several factors:
Material Costs: The type of metal powder used can significantly impact the overall cost.
Tooling Costs: The design and fabrication of molds can be expensive, especially for complex parts.
Production Volume: Higher volumes can reduce the cost per part due to economies of scale.
Post-Processing: Additional processes such as machining, heat treatment, and surface finishing can add to the cost.
Section 6: Metal Injection Molding Machines
Metal Injection Molding (MIM) is a sophisticated manufacturing process that combines the versatility of plastic injection molding with the strength and durability of metal. Central to this process are the Metal Injection Molding machines, which play a crucial role in shaping, forming, and producing high-precision metal parts.
6.1. Overview of Metal Injection Molding Machines
MIM machines are specialized pieces of equipment designed to handle the unique requirements of the MIM process. They must be capable of injecting highly viscous feedstock composed of metal powders and binder materials into a mold cavity with extreme precision. The machines used in MIM are similar to those used in plastic injection molding but are modified to accommodate the specific needs of metal injection molding.
6.2. Key Components of MIM Machines
Injection Unit: The injection unit is responsible for heating and injecting the feedstock into the mold. It consists of a hopper, barrel, screw, and nozzle.
Mold: The mold cavity shapes the molten feedstock into the desired part geometry. Molds for MIM are typically made from hardened tool steels and are designed to withstand high temperatures and pressures.
Clamping Unit: The clamping unit holds the mold halves together during the injection process and opens the mold to release the formed part.
Control System: Advanced control systems regulate the temperature, pressure, and injection speed to ensure consistent part quality and process repeatability.
6.3. Types of MIM Machines
There are several types of MIM machines, each designed for specific applications and production requirements:
Hydraulic MIM Machines: These machines use hydraulic systems to control the injection and clamping processes. They are known for their robustness and ability to handle large-scale production.
Electric MIM Machines: Electric machines use electric servo motors for precise control of the injection and clamping processes. They offer higher energy efficiency and faster cycle times compared to hydraulic machines.
Hybrid MIM Machines: Hybrid machines combine the benefits of hydraulic and electric systems, offering a balance of power, precision, and energy efficiency.
6.4. Advanced Features in MIM Machines
Modern MIM machines are equipped with advanced features to enhance their performance and productivity:
Automation: Automation systems, such as robotic arms and conveyors, improve production efficiency by automating part handling and post-processing tasks.
Precision Control: Advanced sensors and control systems ensure precise regulation of temperature, pressure, and injection speed, resulting in consistent part quality.
Multi-Cavity Molds: Multi-cavity molds allow for the production of multiple parts in a single injection cycle, increasing throughput and reducing production costs.
Temperature Control: Precise temperature control systems maintain consistent feedstock viscosity and prevent defects caused by temperature fluctuations.
6.5. Benefits of Using Advanced MIM Machines
Using advanced MIM machines offers several benefits, including:
High Precision: MIM machines can produce parts with tight tolerances and intricate geometries, making them ideal for applications requiring high precision.
Efficiency: Automation and advanced control systems enhance production efficiency, reducing cycle times and minimizing material waste.
Flexibility: MIM machines can work with a wide range of materials, including stainless steels, tool steels, titanium alloys, and more.
Scalability: MIM machines are suitable for both low-volume and high-volume production, offering scalability to meet varying production demands.
6.6. Future Trends in MIM Machine Technology
The future of MIM machine technology looks promising, with ongoing advancements aimed at improving efficiency, precision, and versatility. Some emerging trends include:
- 3D Printed Metal Injection Molds: The use of 3D printing to create molds offers significant cost and time savings, enabling rapid prototyping and custom part production.
- Enhanced Automation: Continued advancements in automation technology will further streamline the MIM process, reducing labor costs and improving consistency.
- Sustainable Practices:Innovations in materials and processes are focused on reducing environmental impact, such as developing more eco-friendly binders and recycling metal powders.
6.7. Metal Injection Molding Companies
Numerous companies specialize in MIM, each offering unique capabilities and expertise. Some notable MIM companies include:
Welleshaft: Known for their high-quality MIM components and advanced manufacturing techniques.
GKN: A global leader in precision metal components.
Smith Metal Products: Specializes in MIM for a variety of industries.
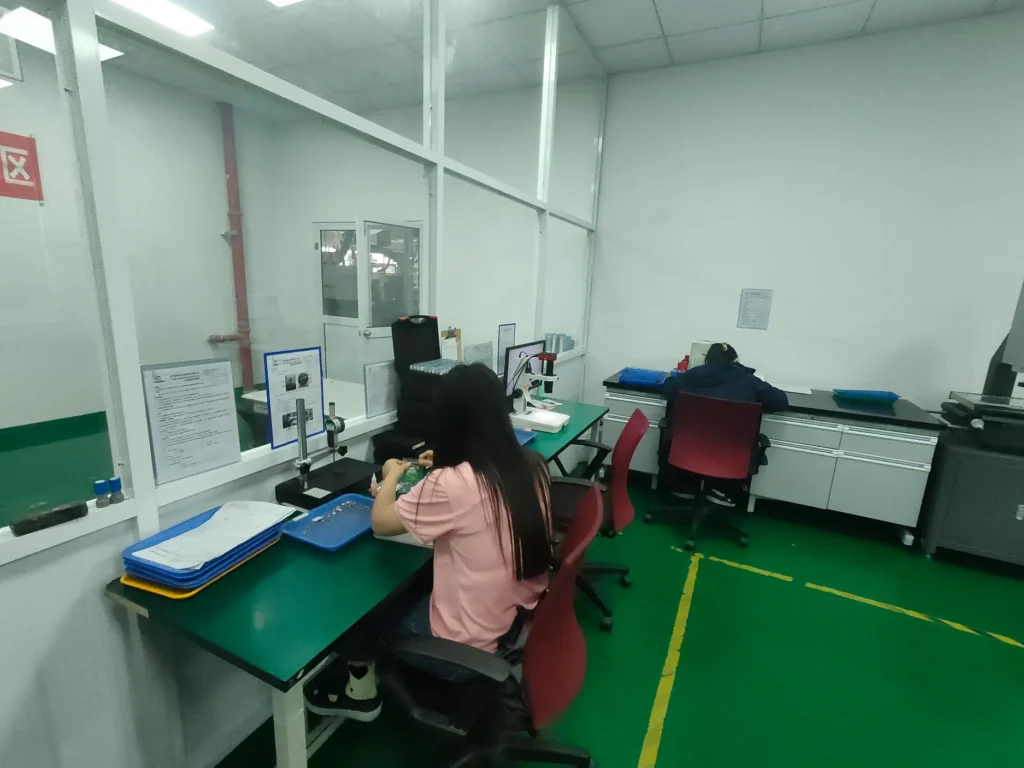
Conclusion
Metal Injection Molding (MIM) is a highly efficient and versatile manufacturing process that offers numerous advantages over traditional metalworking techniques. Its ability to produce complex, high-precision parts with minimal waste makes it an attractive option for various industries. As technology continues to advance, MIM is poised to play an increasingly important role in the future of manufacturing.
For all your MIM needs, consider Welleshaft, a trusted global supplier and contract manufacturer, ensuring top-notch quality and precision in every part produced.