High-Quality Metal Injection Molding Materials for Precision Parts | Expert Manufacturing Solutions
Metal Injection Molding (MIM) is a cutting-edge manufacturing process that combines the versatility of plastic injection molding with the strength and integrity of metal. This technology is ideal for producing complex and high-precision metal parts in large quantities. In this article, we’ll explore the various materials used in MIM, the benefits of the process, and why Welleshaft is your trusted global supplier and contract manufacturer for MIM solutions.

Section 1: Introduction to Metal Injection Molding
Metal Injection Molding (MIM) is a manufacturing process that allows for the production of intricate metal parts with high precision and consistency. This technique is particularly beneficial for creating small and complex components that are difficult to produce using traditional methods.
The MIM Process Overview
The MIM process involves several key steps:
Feedstock Preparation:Technicians prepare a homogeneous feedstock by mixing metal powder with a binder.
Injection Molding:Operators inject the feedstock into a mold to form the desired shape.
Debinding:They remove the binder from the molded part, leaving behind a porous metal structure.
Sintering:Manufacturers heat the part to a high temperature to fuse the metal particles, producing a dense and solid component.
Advantages of Metal Injection Molding
MIM offers several advantages over traditional manufacturing methods:
Complex Geometries: Capable of producing parts with intricate shapes and fine details.
Material Efficiency: Minimizes waste and reduces material costs.
High Precision: Achieves tight tolerances and consistent quality.
Scalability: Suitable for large-scale production runs.
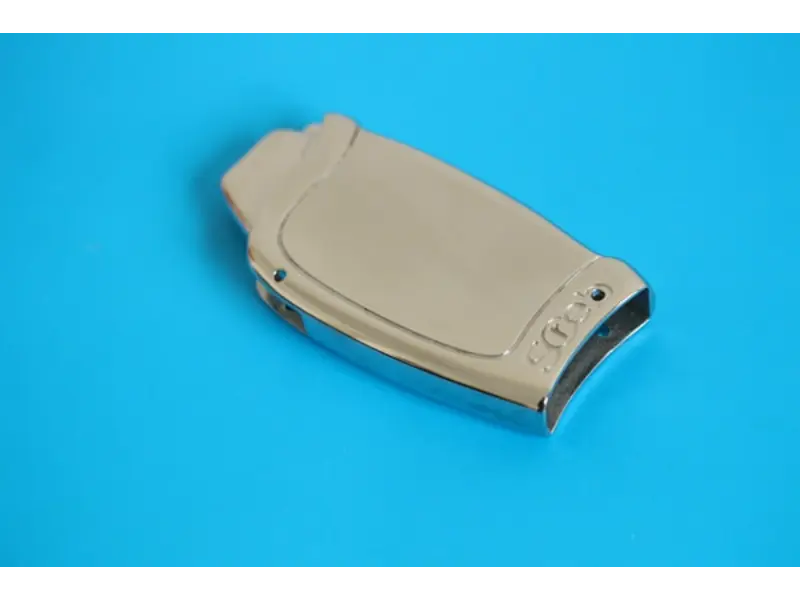
Section 2: Key Materials Used in MIM
Manufacturers use various materials in the MIM process, each offering unique properties suited to different applications.
2.1.MIM Metal Powders
Material | Particle Size (µm) | Density (g/cm³) | Tensile Strength (MPa) | Hardness (HRC) | Corrosion Resistance | Properties | Common Applications |
Stainless Steel | 10-20 | 7.7-8.0 | 500-1000 | 20-40 | Excellent | Excellent corrosion resistance, good mechanical properties | Automotive parts, medical devices, consumer electronics |
Carbon Steel | 10-45 | 7.7-7.9 | 400-900 | 15-30 | Moderate | High strength, cost-effective | Structural components, general engineering |
Tool Steel | 5-25 | 7.7-8.1 | 800-2000 | 50-65 | Moderate | Hardness, wear resistance | Cutting tools, molds |
Titanium | 10-45 | 4.5 | 300-1200 | 30-40 | Excellent | Lightweight, high corrosion resistance | Aerospace parts, medical implants |
Tungsten | 2-15 | 19.3 | 700-1000 | 20-30 | Good | High density, radiation shielding properties | Defense applications, radiation shielding |
Ceramic Powders | 0.5-5 | 2.5-6.0 | 500-2000 | 60-90 | Excellent | High hardness, thermal resistance | Electronic components, cutting tools |
Amorphous Metals | 10-20 | 6.0-7.5 | 1000-2500 | 40-60 | Good | High strength, elasticity | High-performance applications, electronics |
Aluminum | 10-45 | 2.7 | 150-400 | 10-20 | Good | Lightweight, corrosion-resistant | Automotive parts, consumer electronics |
2.2.MIM Process Compatibility
Material | Feedstock Preparation | Injection Molding | Debinding | Sintering |
Stainless Steel | Yes | Yes | Yes | Yes |
Carbon Steel | Yes | Yes | Yes | Yes |
Tool Steel | Yes | Yes | Yes | Yes |
Titanium | Yes | Yes | Yes | Yes |
Tungsten | Yes | Yes | Yes | Yes |
Ceramic Powders | Yes | Yes | Yes | Yes |
Amorphous Metals | Yes | Yes | Yes | Yes |
Aluminum | Yes | Yes | Yes | Yes |
2.3.Common MIM Material Brands
Material Type | Brand | ISO Equivalent | DIN Equivalent | BS Equivalent | JIS Equivalent |
MIM Stainless Steel | MIM 316L | ISO 5832-4 | DIN 1.4404 | BS 5832-4 | JIS SUS316L |
MIM Stainless Steel | MIM 17-4 PH | ISO 5832-4 | DIN 1.4542 | BS 5832-4 | JIS SUS17-4PH |
Stainless Steel | AISI 430, 904L | ISO 15510 | DIN 1.4016, 1.4539 | BS 410S21, 904L | JIS SUS430, SUS904L |
Stainless Steel | AISI 304 | ISO 3506-1 (stainless steel) | DIN 1.4301 | BS 304S31 | JIS G4303 SUS304 |
MIM Stainless Steel | MIM 15-5 PH | ISO 5832-4 | DIN 1.4545 | BS 5832-4 | JIS SUS15-5PH |
MIM Iron Base Alloy | MIM Fe-Cu | ISO 1083 | DIN 1693 | BS 2789 | JIS G5502 |
MIM Tool Steel | MIM D2 | ISO 4957 | DIN 1.2379 | BS 4659 | JIS SKD11 |
MIM Tool Steel | MIM M2 | ISO 4957 | DIN 1.3343 | BS 4659 | JIS SKH51 |
MIM Titanium | MIM Ti-6Al-4V | ISO 5832-2 | DIN 3.7165 | BS 5296 | JIS Ti-6Al-4V |
MIM Copper | MIM Cu | ISO 1336 | DIN C 10100 | BS 2874 | JIS C1100 |
MIM Nickel | MIM Ni | ISO 1336 | DIN 17740 | BS 3075 | JIS N1000 |
MIM Low Alloy Steel | MIM 4340 | ISO 683-2 | DIN 1.6511 | BS 970 34CrNiMo6 | JIS SNCM439 |
MIM High-Speed Steel | MIM M42 | ISO 4957 | DIN 1.3247 | BS 4659 | JIS SKH59 |
MIM Maraging Steel | MIM Maraging 250 | ISO 4957 | DIN 1.2709 | BS 4659 | JIS MARAGING250 |
MIM Inconel | MIM Inconel 718 | ISO 6208 | DIN 2.4668 | BS 3076 | JIS Inconel718 |
MIM Cobalt Chrome | MIM Co-Cr | ISO 5832-12 | DIN 2.4605 | BS 6070 | JIS Co-Cr |
MIM Tool Steel (High Carbon) | MIM A2 | ISO 4957 | DIN 1.2363 | BS 4659 | JIS SKD12 |
Additional Notes:
1.ISO 5832-4: This standard specifies requirements for MIM materials used in medical devices.
2.ISO 4957: Defines tool steels including those used in MIM.
3.ISO 1083: Covers specifications for iron base alloys, including MIM materials.
4.ISO 1336: Addresses copper and copper alloys, which may include MIM variants.
5.ISO 9724: Pertains to nickel and nickel alloys used in MIM.
6.ISO 683-2: Specifies low alloy steels, including those used in MIM.
7.ISO 6208: Pertains to nickel-chromium-molybdenum alloys (Inconel).
8.ISO 5832-12: Specifies cobalt-chromium alloys used in medical devices.
9.ISO 4957: Also used for high-speed steels and maraging steels.
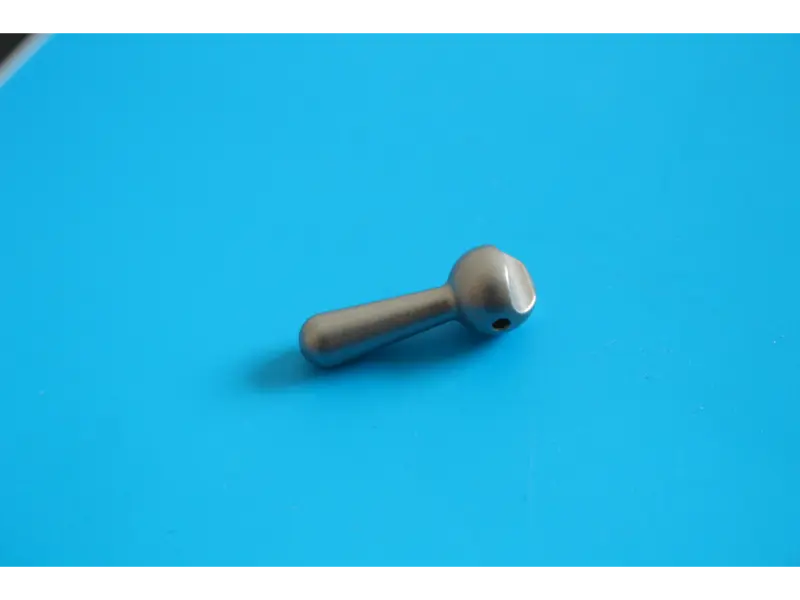
Section 3: Welleshaft – Your Trusted Global Supplier and Contract Manufacturer
Welleshaft has been at the forefront of providing high-quality MIM solutions for over a decade. Here’s why you should choose Welleshaft for your MIM needs:
1. Expertise and Experience
With years of experience in the industry, Welleshaft has the expertise to deliver top-notch MIM parts that meet the highest standards of quality and precision.
2. State-of-the-Art Facilities
Welleshaft uses advanced manufacturing facilities equipped with the latest MIM technology to ensure efficient and reliable production processes.
3. Comprehensive Material Selection
Welleshaft offers a wide range of MIM materials, including stainless steel, tool steel, titanium, and specialty alloys, to suit various applications.
4. Commitment to Quality
Welleshaft is committed to delivering products that exceed customer expectations. Their rigorous quality control processes ensure that every part meets the required specifications.
Section 3: Frequently Asked Questions about MIM Materials
Q: What materials can be used in metal injection molding?
A: MIM can utilize a variety of metals, including stainless steel, carbon steel, tool steel, titanium, tungsten, and amorphous metals.
Q: What is the raw material for metal injection molding?
A: The raw material for MIM is a mixture of metal powder and a binder, which is then molded and sintered to create the final part.
Q: What materials are used in injection molding?
A: Besides metals, injection molding can also use plastic, ceramic, and composite materials.
Q: What type of steel is used in injection molding?
A: Tool steels are commonly used in the molds for injection molding due to their hardness and wear resistance.
Conclusion
Metal Injection Molding is a versatile and efficient manufacturing process that offers numerous benefits for producing high-precision metal parts. By choosing high-quality MIM materials and a trusted supplier like Welleshaft, you can ensure the performance and reliability of your components. Whether you’re in the automotive, medical, aerospace, or electronics industry, MIM can provide the solutions you need for complex and high-precision parts.