High-Quality Coupling Sleeves: Durable and Reliable Solutions for All Applications
Coupling sleeves play a crucial role in various industrial applications, providing durable and reliable connections between shafts, pipes, and other components. This comprehensive guide explores the different types of coupling sleeves, their applications, advantages, and installation processes. By understanding these aspects, you can make informed decisions when selecting the right coupling sleeves for your needs.
What Are Coupling Sleeves?
Coupling sleeves are mechanical devices used to connect two shafts or pipes to transmit power or fluid. They come in various types, each designed for specific applications and requirements. Coupling sleeves ensure the alignment and continuity of the connected parts, minimizing vibrations and misalignments that could lead to mechanical failures.
Specifications of Coupling Sleeves
Dimensions
Outer Diameter (OD):
Range: Typically from 0.5 inches (12.7 mm) to 10 inches (254 mm).
Importance: Determines the size of the shaft or pipe that can be connected.
Inner Diameter (ID):
Range: Typically from 0.25 inches (6.35 mm) to 8 inches (203.2 mm).
Importance: Must match the diameter of the shaft or pipe for a secure fit.
Length:
Range: Typically from 1 inch (25.4 mm) to 12 inches (304.8 mm).
Importance: Affects the overall strength and stability of the connection.
Materials
Steel:
Properties: High strength, durability, and resistance to wear and tear.
Applications: Suitable for heavy-duty applications in industrial machinery and automotive sectors.
Stainless Steel:
Properties: Corrosion resistance, high strength, and excellent durability.
Applications: Ideal for food processing, pharmaceutical, and marine applications.
Brass:
Properties: Corrosion resistance, good conductivity, and ease of machining.
Applications: Used in plumbing, electrical, and decorative applications.
PVC:
Properties: Lightweight, corrosion resistance, and low cost.
Applications: Common in plumbing, water treatment, and HVAC systems.
Aluminum:
Properties: Lightweight, good strength-to-weight ratio, and corrosion resistance.
Applications: Used in aerospace, automotive, and general engineering applications.
Types of Coupling Sleeves
1. Hose Coupling Sleeves
Hose coupling sleeves are used to join hoses together or to connect hoses to other fittings. They are commonly used in hydraulic and pneumatic systems to ensure leak-proof connections.
Material Preparation:
Initial Step: Choose materials such as steel, stainless steel, brass, or PVC.
Cutting: Cut the raw material into the desired length.
Turning and Boring:
Process: Use a lathe to machine the OD and ID to specific dimensions.
Purpose: Ensure a proper fit with hoses and connectors.
Knurling (for Better Grip):
Process: Create a patterned texture on the surface using a knurling tool.
Purpose: Improve grip and prevent slipping.
Drilling and Threading:
Process: Drill holes and create threads for secure connections.
Purpose: Allow secure attachment to hoses and equipment.
Surface Finishing:
Process: Apply a protective coating (e.g., galvanizing, anodizing) or polish the surface.
Purpose: Prevent corrosion and enhance appearance.
2. Spline Coupling Sleeves
Spline coupling sleeves are designed to transmit torque between shafts with splined ends. These are widely used in automotive and machinery applications where precise torque transmission is essential.
Material Preparation:
Initial Step: Select high-strength materials like alloy steel or stainless steel.
Cutting: Cut the material into the required length.
Turning:
Process: Machine the outer and inner diameters to precise specifications.
Purpose: Ensure concentricity and dimensional accuracy.
Broaching:
Process: Use a broaching machine to create internal splines.
Purpose: Ensure the splines match the corresponding shaft for torque transmission.
Heat Treatment:
Process: Heat treat the coupling sleeve to enhance hardness and strength.
Purpose: Improve wear resistance and durability.
Surface Finishing:
Process: Apply a protective coating or polish the surface.
Purpose: Prevent corrosion and improve aesthetic quality.
3. Quadra-Flex Coupling Sleeves
Quadra-flex coupling sleeves offer flexibility and vibration damping. They are ideal for applications requiring misalignment compensation and shock absorption, such as in pumps and compressors.
Material Preparation:
Initial Step: Select flexible materials such as rubber or polyurethane.
Cutting: Cut the material into the required length and shape.
Molding:
Process: Place the material in a mold and apply heat and pressure to form the sleeve.
Purpose: Create a flexible and durable coupling sleeve.
Vulcanization:
Process: Heat the molded rubber in the presence of sulfur to create cross-links between polymer chains.
Purpose: Enhance elasticity, strength, and durability.
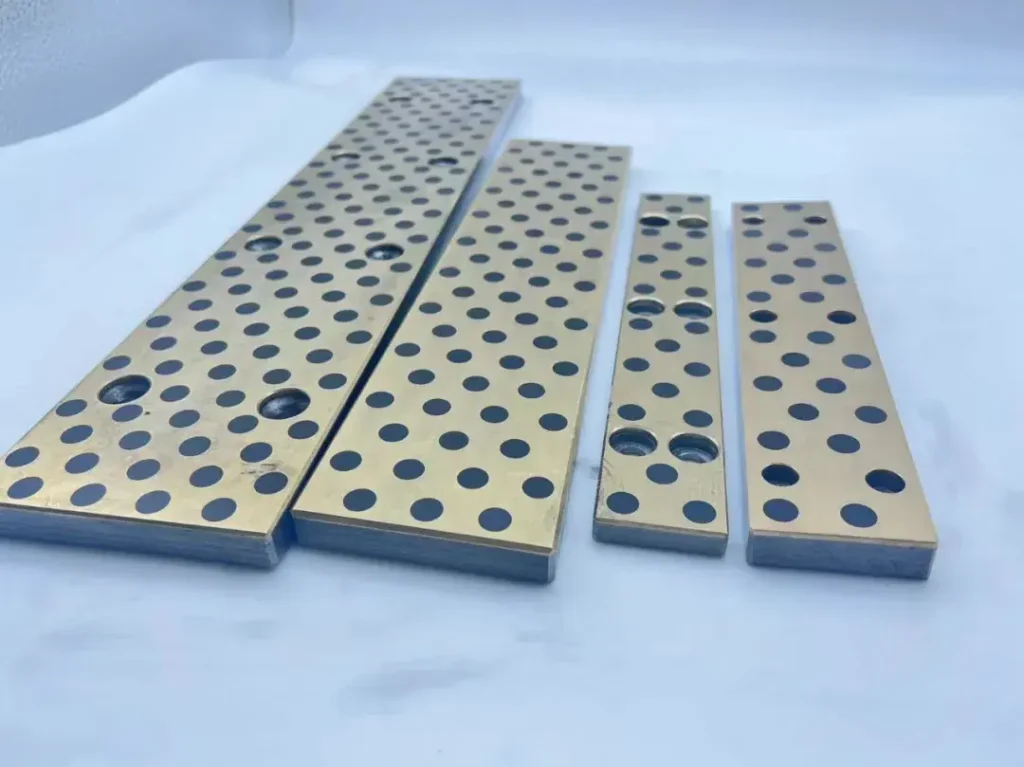
4. Gear Sleeve Coupling
Gear sleeve couplings use interlocking gears to connect shafts, providing high torque transmission with minimal backlash. They are commonly found in heavy machinery and industrial equipment.
Material Selection
Material Choice: Gear sleeve couplings are commonly made from high-strength materials such as steel, stainless steel, or aluminum, depending on the application requirements. Materials are chosen for their durability, strength, and resistance to wear and corrosion.
Cutting and Shaping
Blank Preparation: Raw material bars or billets are cut to the required length using a bandsaw or cutting machine. The size of the blank is determined based on the dimensions of the final gear sleeve coupling.
Turning: The blanks are then turned on a lathe to shape the outer and inner diameters, ensuring they are within the required tolerances. This step also helps in achieving a smooth surface finish.
Gear Cutting
Gear Hobbing: Gears are cut into the coupling sleeve using a hobbing machine. This process involves using a rotating hob (cutting tool) to cut the teeth into the sleeve. Precision is crucial to ensure proper engagement between the gears.
Gear Shaping: For some designs, gear shaping may be used instead of hobbing. This involves using a gear shaper tool to cut the teeth.
Gear Grinding: After the gears are cut, they may be ground to achieve the final gear profile and ensure a smooth, accurate surface. This step improves the gear’s performance and durability.
Heat Treatment
Hardening: Gear sleeve couplings often undergo heat treatment to enhance their hardness and wear resistance. Common methods include carburizing or induction hardening.
Tempering: After hardening, the couplings are tempered to reduce brittleness and relieve internal stresses. This involves reheating the material to a specific temperature and then cooling it.
Assembly
Gear Alignment: The gears are aligned and assembled into the coupling sleeve. This step ensures that the gears mesh correctly and that the coupling functions properly.
Bolting/Clamping: If the coupling design includes separate components, they are fastened together using bolts or clamps. This ensures a secure connection and alignment.
Finishing Operations
Surface Treatment: The coupling sleeve may undergo additional surface treatments such as coating or plating to enhance corrosion resistance and improve appearance. Common treatments include zinc plating or anodizing.
Inspection and Testing: The finished couplings are inspected for dimensional accuracy, gear alignment, and overall quality. Testing may include functional tests to ensure the coupling performs as expected under load.
Deburring: Any sharp edges or burrs from machining are removed to ensure safe handling and proper fitting.
Quality Control
Dimensional Checks: Precise measurements are taken to ensure that the coupling meets all specified dimensions and tolerances.
Performance Testing: Couplings may be tested for load capacity, torque transmission, and overall performance to verify they meet industry standards and application requirements.
5. Sleeve Type Coupling
Sleeve type couplings are simple and cost-effective solutions for connecting shafts. They consist of a sleeve and two hubs, making them easy to install and maintain.
6. Sleeve Coupling Pipe
Sleeve coupling pipes are used to join pipes together, ensuring a secure and leak-proof connection. They are widely used in plumbing and piping systems.Below is an overview of the typical manufacturing process for sleeve coupling pipes:
Material Selection
Material Choice: Choose the appropriate material based on the application requirements. Common materials include:
Metal: Steel, stainless steel, brass.
Plastic: PVC, CPVC, polyethylene.
Composite: Materials combining metal and plastic.
Cutting
Cutting Raw Material: The raw material, usually in the form of bars or pipes, is cut to the desired length using cutting machines such as bandsaws or chop saws.
For Metal: High-speed cutting tools or laser cutters may be used.
For Plastic: Plastic cutting machines or saws designed for plastic materials are employed.
Machining
Turning: The cut material is machined on a lathe to shape the outer and inner diameters. This step ensures that the coupling sleeve will fit properly over the ends of the pipes being connected.
Outer Diameter (OD): Machined to fit the dimensions of the connecting pipes.
Inner Diameter (ID): Bored to the appropriate size to ensure a snug fit.
Boring: Further machining may be performed to refine the inner diameter and ensure it is smooth and accurately sized.
Joining Features
Threading: If required, threads are cut into the ends of the sleeve for threaded connections.
Process: A threading machine or die is used to create threads.
Flanging: Flanges may be added to the ends of the coupling pipe if the design requires bolted connections.
Process: Flanges are either welded or attached using bolts.
Sealing
Gaskets or Seals: Install gaskets or seals to ensure a leak-proof connection.
Material: Seals may be made from rubber, silicone, or other sealing materials.
Installation: Seals are placed into grooves or seats within the coupling sleeve.
Heat Treatment (for Metal)
Hardening: Heat treatment processes such as carburizing or induction hardening are used to improve the hardness and wear resistance of metal coupling pipes.
Process: The metal is heated to a high temperature and then rapidly cooled.
Tempering: After hardening, the coupling pipe is tempered to reduce brittleness and relieve internal stresses.
Process: The metal is reheated to a specific temperature and then cooled slowly.
Finishing Operations
Surface Treatment: Apply surface treatments to enhance the durability and appearance of the coupling pipe.
Metal: Coatings such as galvanizing, plating, or painting may be applied.
Plastic: May involve polishing or coating for added protection.
Deburring: Remove any sharp edges or burrs from the machining process to ensure safe handling and proper fitting.
Inspection and Testing
Dimensional Checks: Measure the coupling pipe to ensure it meets the specified dimensions and tolerances.
Tools: Calipers, micrometers, and other precision measuring instruments.
Performance Testing: Test the coupling pipe for its ability to handle operational stresses, pressure, and flow requirements.
Pressure Testing: Check for leaks and verify that the pipe can withstand the required pressure.
Quality Control: Inspect for overall quality, including surface finish and alignment.
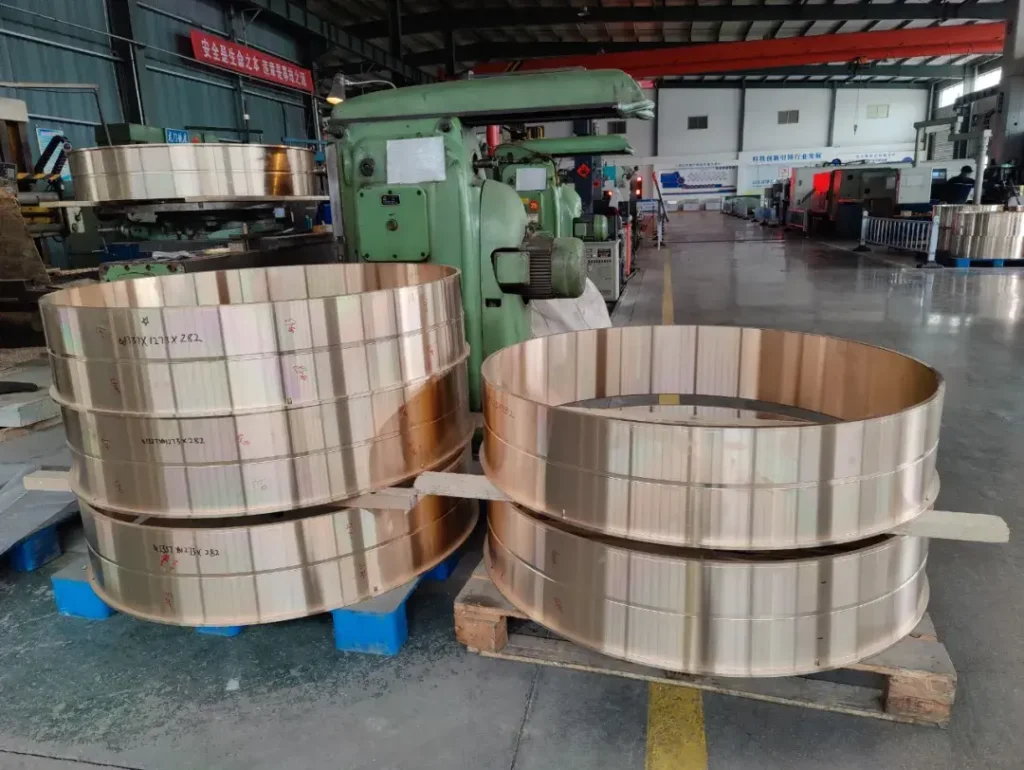
7. Flange Coupling
Flange couplings consist of two flanges bolted together with a gasket in between to prevent leaks. They are commonly used in high-pressure piping systems.Below is a detailed overview of the manufacturing process for flange couplings:
Material Selection
Material Choice: Select appropriate materials based on application requirements such as strength, durability, and corrosion resistance. Common materials include:
Metal: Steel, stainless steel, cast iron, and aluminum.
Alloys: High-strength alloys for specialized applications.
Cutting and Shaping
Cutting Raw Material: The raw material, usually in the form of bars or billets, is cut to the required length using cutting machines such as bandsaws, circular saws, or plasma cutters.
Shaping: The cut pieces are then shaped into rough blanks using forging or casting processes, depending on the material and required properties.
Forging: Involves heating the metal and shaping it using hammers or presses.
Casting: Molten metal is poured into molds to create the rough shape of the flange.
Machining
Turning: The rough blanks are machined on a lathe to achieve the desired outer diameter (OD) and inner diameter (ID). This step ensures concentricity and the correct fit for the shafts.
Boring: The inner diameter is further machined using a boring tool to ensure a precise fit for the shafts.
Facing: Both faces of the flange are machined to ensure they are flat and parallel. This is crucial for proper alignment and sealing when the flanges are bolted together.
Drilling: Bolt holes are drilled into the flanges using a drilling machine or CNC (Computer Numerical Control) machine. The number and size of the holes depend on the design specifications.
Threading (if required): If the design requires, threads are cut into the bolt holes or other parts of the flange using threading tools.
Heat Treatment
Hardening: Heat treatment processes such as quenching and tempering are used to enhance the hardness and strength of the flange coupling.
Quenching: Involves heating the flange to a high temperature and then rapidly cooling it in water or oil.
Tempering: The flange is reheated to a specific temperature and then cooled slowly to reduce brittleness and relieve internal stresses.
Surface Finishing
Surface Treatment: Apply surface treatments to enhance durability, corrosion resistance, and appearance.
Metal: Coatings such as galvanizing, painting, or plating (e.g., zinc, chrome) may be applied.
Polishing: Machined surfaces are polished to achieve a smooth finish and reduce friction.
8. Flexible Coupling
Flexible couplings are designed to accommodate misalignment and absorb shocks, making them suitable for applications where vibration damping is required.
Material Preparation:
Initial Step: Select materials like rubber, polyurethane, or flexible metal alloys.
Cutting: Cut the material into the required length and shape.
Molding (for Rubber or Polyurethane):
Process: Place the material in a mold and apply heat and pressure to form the sleeve.
Purpose: Create a flexible and durable coupling sleeve.
Turning and Milling (for Metal Alloys):
Process: Use a lathe and milling machine to shape the coupling sleeve.
Purpose: Achieve precise dimensions and features.
Vulcanization (for Rubber):
Process: Heat the molded rubber in the presence of sulfur to create cross-links between polymer chains.
Purpose: Enhance elasticity, strength, and durability.
9. Clamp Coupling
Clamp couplings use a clamping mechanism to connect shafts. They are easy to install and remove, making them ideal for applications requiring frequent assembly and disassembly.
10. Dresser Coupling
Dresser couplings are used to join pipes without welding. They provide a reliable and flexible connection, making them ideal for underground piping systems.
11.Rigid Coupling Sleeves
Rigid coupling sleeves are mechanical components designed to connect two shafts together in a fixed alignment, ensuring that they operate as a single unit. Unlike flexible couplings, rigid couplings do not accommodate misalignment between the connected shafts. They provide a solid, inflexible connection, transmitting torque and rotational movement directly from one shaft to the other without any relative motion between them.
Material Preparation:
Initial Step: Select the appropriate material (e.g., steel, stainless steel, brass).
Cutting: Cut the raw material into the desired length using a bandsaw or chop saw.
Turning:
Process: Use a lathe to machine the outer diameter (OD) and inner diameter (ID) to precise dimensions.
Purpose: Ensure concentricity and the correct fit for the shafts.
Boring:
Process: Enlarge and finish the inner diameter using a boring tool.
Purpose: Achieve the exact size and smooth surface finish.
Milling:
Process: If the design requires, mill keyways or slots on the coupling sleeve using a milling machine.
Purpose: Provide secure engagement with keyed shafts.
Drilling and Tapping:
Process: Drill holes for set screws or bolts, followed by tapping to create threads.
Purpose: Allow secure fastening of the coupling sleeve to the shafts.
Heat Treatment (Optional):
Process: Heat treat the coupling sleeve to enhance its hardness and strength.
Purpose: Improve wear resistance and durability.
Surface Finishing:
Process: Apply a surface finish (e.g., polishing, coating) to protect against corrosion and improve appearance.
Purpose: Ensure long-term performance and aesthetic quality.
Applications of Coupling Sleeves
Coupling sleeves are used in various industries, including:
Industrial Machinery:
Description: Coupling sleeves are used to connect shafts in various machines, ensuring smooth power transmission.
Examples: Conveyors, mixers, and compressors.
Automotive Industry:
Description: Used in drivetrains, steering systems, and other critical components.
Examples: Driveshaft couplings, steering column joints.
Hydraulic Systems:
Description: Connect hoses and pipes in hydraulic circuits, ensuring leak-free connections.
Examples: Hydraulic pumps, cylinders, and valves.
Pneumatic Systems:
Description: Provide secure connections for air hoses and components.
Examples: Air compressors, pneumatic tools, and control systems.
Food and Beverage Industry:
Description: Used in processing equipment where hygiene and corrosion resistance are paramount.
Examples: Food processing machines, beverage dispensers.
Advantages of Coupling Sleeves
Durability: Coupling sleeves are designed to withstand high levels of stress and torque, ensuring long-lasting performance.
Flexibility: Many types of coupling sleeves can accommodate misalignment and absorb vibrations, reducing wear and tear on connected components.
Ease of Installation: Most coupling sleeves are easy to install and remove, minimizing downtime during maintenance.
Versatility: Available in various sizes and materials, coupling sleeves can be tailored to specific applications and requirements.
Cost-Effectiveness: Coupling sleeves offer a cost-effective solution for connecting shafts and pipes without the need for welding or complex assembly processes.
Coupling Sleeves in Singapore & China
Coupling sleeves are widely used in industrial applications across Singapore and China. With numerous suppliers offering high-quality products, finding the right coupling sleeve for your needs is easier than ever. Leading supplier welleshaft in these regions provide a range of coupling sleeves, from hose coupling sleeves to gear sleeve couplings, ensuring that you have access to reliable and durable solutions.
Coupling Sleeves HS Code
The Harmonized System (HS) code for coupling sleeves is essential for international trade, as it helps classify products for customs purposes. The HS code for coupling sleeves generally falls under the category of mechanical parts and fittings, typically in the range of 8483.10. This code ensures standardized classification and facilitates smooth customs clearance processes.
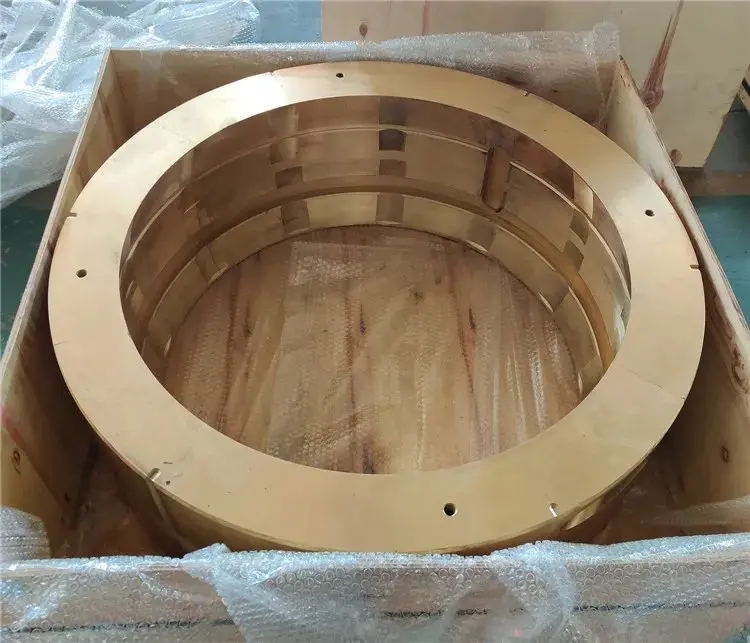
Commonly Asked Questions
What is the Use of Sleeve Coupler?
A sleeve coupler is used to connect two shafts or pipes, ensuring a continuous and secure transmission of power or fluid. It helps maintain alignment and reduces the risk of leaks or mechanical failures.
What Are the Advantages of Sleeve Coupling?
The advantages of sleeve coupling include durability, flexibility, ease of installation, versatility, and cost-effectiveness. These features make sleeve couplings ideal for a wide range of industrial applications.
How Do You Install a Coupling Sleeve?
Installing a coupling sleeve involves preparation, alignment, installation, tightening, and inspection. Ensuring proper alignment and secure fastening are crucial for a reliable connection.
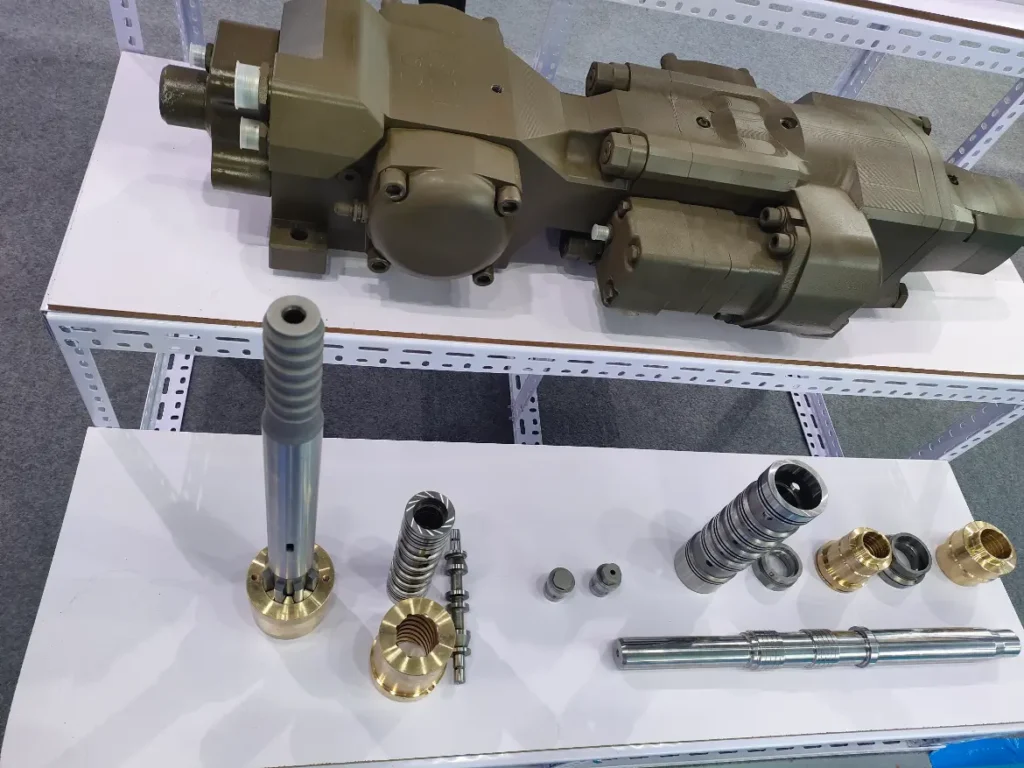
Conclusion
Coupling sleeves are essential components in various industrial applications, providing durable and reliable connections between shafts, pipes, and other mechanical parts. By understanding the different types of coupling sleeves, their applications, advantages, and installation processes, you can make informed decisions and ensure the efficiency and longevity of your mechanical systems. Whether you are looking for hose coupling sleeves, spline coupling sleeves, or gear sleeve couplings, there is a wide range of options available to meet your specific needs.
For more information on high-quality coupling sleeves and to find the perfect solution for your application, please contact us.
Jinan Welle Metal Products Co., Ltd (Welleshaft)
Website: www.welleshaft.com
Email: [email protected]
Phone: +86-156-5017-9596
Explore our range of durable and reliable coupling sleeves today!