High-Precision Tungsten MIM Solutions | Superior Metal Injection Molding
In the world of advanced manufacturing, Metal Injection Molding (MIM) has emerged as a transformative technology, allowing for the production of complex, high-precision components from various metals and alloys. Among these, tungsten stands out for its exceptional properties, making it a prime choice for applications requiring high strength, durability, and resistance to extreme conditions. In this article, we delve into the benefits of Tungsten MIM, its applications, and why partnering with a trusted supplier like Welleshaft can ensure the success of your projects.
Section 1: Why Tungsten is Ideal for MIM
Tungsten is a refractory metal known for its high melting point, density, and exceptional hardness. These properties make it an excellent candidate for applications that demand materials capable of withstanding extreme temperatures, high wear, and significant mechanical stress.
1.1. Benefits of Using Tungsten in MIM
1.1.1.High Density and Hardness:
Tungsten is known for its high density (about 19.3 g/cm³) and exceptional hardness. These properties make it ideal for applications requiring high strength and resistance to wear and deformation.
1.1.2.High Melting Point:
With a melting point of approximately 3422°C (6192°F), tungsten can withstand extreme temperatures. This makes it suitable for applications in high-temperature environments or where thermal stability is crucial.
1.1.3.Excellent Corrosion Resistance:
Tungsten exhibits excellent resistance to corrosion, especially in acidic and alkaline environments. This property extends the lifespan of parts made from tungsten in harsh conditions.
1.1.4.Precision and Complexity:
MIM allows for the production of complex and precise tungsten parts that would be difficult or impossible to achieve with traditional machining methods. This capability is particularly valuable in industries like aerospace, defense, and electronics.
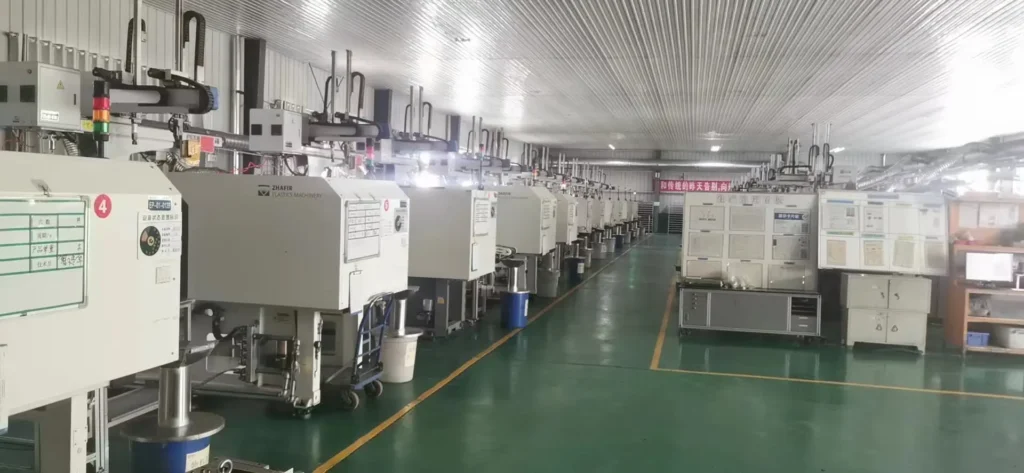
Section 2: Tungsten in Metal Injection Molding (MIM)
Using Tungsten in MIM allows manufacturers to leverage the metal’s unique properties while benefiting from the precision and cost-effectiveness of the MIM process. Tungsten MIM is particularly valuable in producing small, intricate parts that require high strength and resistance to extreme conditions.
2.1. Applications of Tungsten MIM:
2.1.1.Aerospace and Defense:
Tungsten’s high density and strength make it suitable for aerospace and defense applications, such as counterweights, radiation shielding, and high-performance components that require durability and precision.
2.1.2.Medical Devices:
In the medical field, tungsten parts are used in equipment like imaging devices, surgical instruments, and prosthetics due to their biocompatibility, hardness, and resistance to wear.
2.1.3.Electronics:
Tungsten is used in the electronics industry for components like contacts, connectors, and electrodes because of its excellent electrical conductivity and high melting point.
2.1.4.Tooling:
Tungsten parts are utilized in tooling applications where high wear resistance and thermal stability are needed, such as in cutting tools and molds.
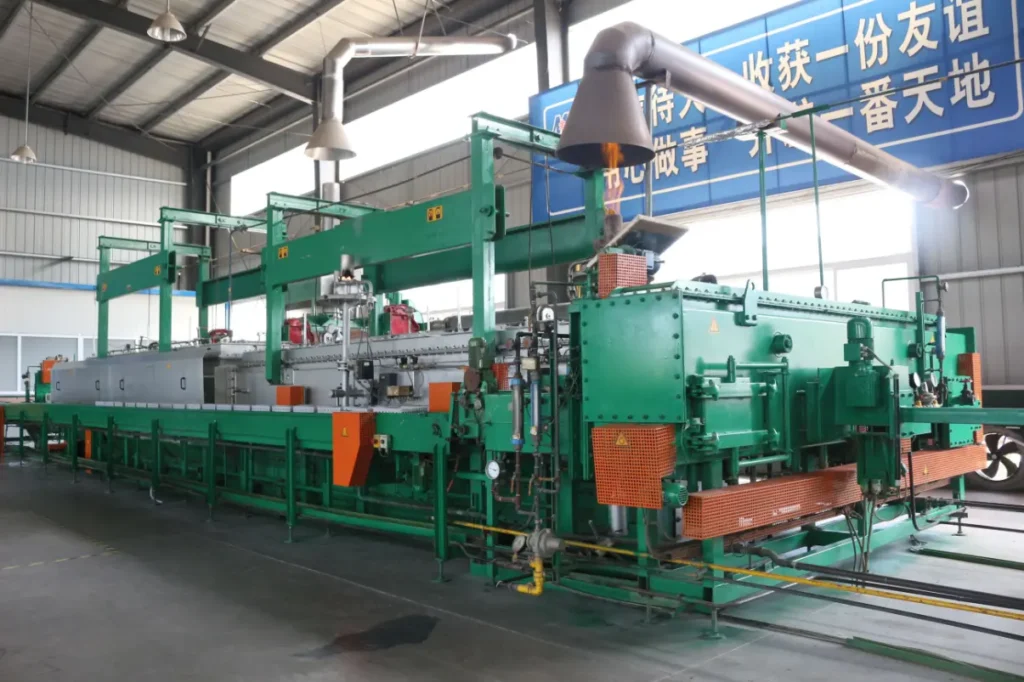
Section 3: Tungsten MIM Process: Step-by-Step
1. Feedstock Preparation:
The MIM process begins with the preparation of the feedstock. Fine tungsten powder is mixed with a binder material, creating a homogeneous mixture that can be injected into molds.
2. Injection Molding:
The feedstock is injected into precision molds to form the desired shape. MIM allows for complex geometries and fine details that would be challenging or impossible to achieve through traditional manufacturing methods.
3. Debinding:
After molding, the binder material is removed from the part in a process called debinding. This step is crucial to prepare the part for sintering.
4. Sintering:
The debound part is heated in a controlled atmosphere to a temperature just below the melting point of tungsten. During sintering, the metal particles fuse together, resulting in a dense, solid component with properties similar to those of wrought metal.
5. Surface Finishing:
MIM parts often undergo additional surface finishing to achieve the desired MIM surface finish. This may include machining, polishing, or coating, depending on the application requirements.
Section 4: Advantages of Tungsten MIM
1. Complex Geometries:
MIM allows for the production of complex shapes with tight tolerances, reducing or eliminating the need for secondary machining operations.
2. Material Efficiency:
The MIM process uses near-net shaping, minimizing material waste and reducing overall production costs.
3. High-Performance Components:
Tungsten MIM parts retain the metal’s high-performance properties, including strength, hardness, and temperature resistance.
4. Cost-Effective for High-Volume Production:
While MIM involves significant upfront tooling costs, it becomes highly cost-effective for large production runs, offering economies of scale.
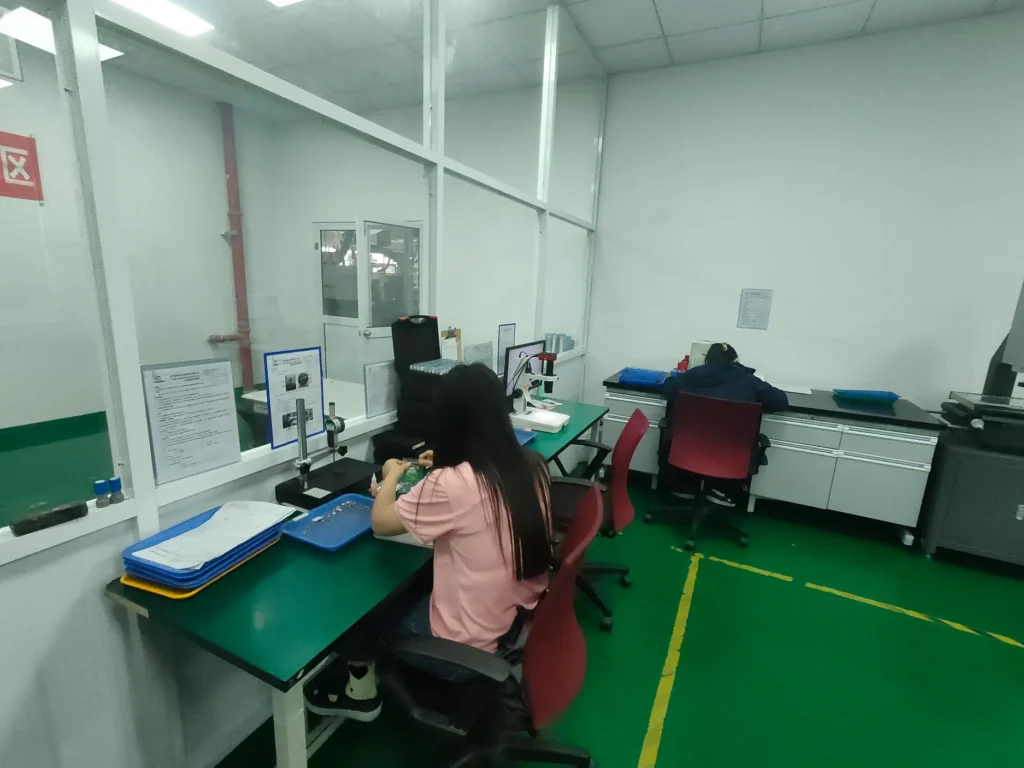
Section 5: The Role of Welleshaft in Tungsten MIM Manufacturing
When it comes to producing high-precision Tungsten MIM components, partnering with an experienced and trusted manufacturer is essential. Welleshaft is a leading global supplier and contract manufacturer specializing in Metal Injection Molding of tungsten and its alloys. With over a decade of expertise in the field, Welleshaft provides end-to-end MIM solutions, from design and tooling to production and finishing.
5.1. Why Choose Welleshaft?
1.Expertise in Tungsten MIM:
Welleshaft has extensive experience working with tungsten and other refractory metals, ensuring that your components meet the highest standards of quality and performance.
2.State-of-the-Art Technology:
Welleshaft employs cutting-edge MIM technology, including advanced Tungsten Injection Molding machines and precision tooling, to deliver parts with exceptional accuracy and consistency.
3.Customized Solutions:
Welleshaft offers tailored solutions to meet your specific requirements, whether you need small batches of prototypes or large-scale production runs.
4.Quality Assurance:
Welleshaft adheres to stringent quality control processes, ensuring that every part meets or exceeds industry standards for metal injection molding strength and performance.
5.Global Reach:
With a global presence, Welleshaft is equipped to serve clients around the world, providing reliable supply chains and timely delivery.
Section 6: Common Questions About Tungsten MIM
1.What is the Rockwell hardness of tungsten?
The Rockwell hardness of tungsten can vary depending on the alloy and processing conditions but generally ranges from 70 to 77 HRA.
2.What material is MIM?
MIM can be used with a wide range of metals and alloys, including stainless steel, titanium, tungsten, and cobalt-chrome, among others.
3.What is tungsten’s melting point?
Tungsten has an exceptionally high melting point of 3,422°C (6,192°F), making it suitable for applications involving extreme temperatures.
Conclusion: The Future of Tungsten MIM
Tungsten MIM represents the cutting edge of manufacturing technology, offering unparalleled precision, strength, and versatility. Whether you’re in aerospace, medical devices, or electronics, tungsten MIM parts can provide the performance you need to succeed in today’s competitive markets.
By choosing Welleshaft as your partner, you gain access to world-class expertise and state-of-the-art manufacturing capabilities. With a commitment to quality and customer satisfaction, Welleshaft is your trusted global supplier for all your Tungsten MIM needs. Contact Welleshaft today to learn more about how we can help you achieve your manufacturing goals.