High-Performance Titanium Alloys: Strength & Toughness Combined
Titanium alloys have long been recognized for their exceptional strength-to-weight ratio and corrosion resistance, making them critical materials in a wide range of industries. However, achieving both high strength and high toughness in titanium alloys presents a significant engineering challenge. High-performance titanium alloys represent a cutting-edge solution, combining these essential properties to unlock new possibilities in demanding applications.
Section 1 Understanding the Importance of Strength and Toughness
Before delving into the specifics of high-performance titanium alloys, it’s crucial to understand the fundamental differences between strength and toughness:
1.1 Strength: Refers to a material’s ability to withstand stress without yielding or breaking. High-strength alloys can support heavy loads and resist deformation.
1.2 Toughness: Describes a material’s ability to absorb energy and resist fracture. High-toughness alloys can withstand impact, stress concentrations, and crack propagation.
While some materials excel in strength but are brittle, and others are ductile but weak, high-performance titanium alloys achieve a delicate balance, offering both simultaneously.
Section 2 The Challenge of Achieving Combined Properties in Titanium
Traditionally, increasing the strength of titanium alloys often led to a decrease in toughness, and vice versa. This trade-off stemmed from the alloy’s microstructure and the mechanisms that govern its behavior under stress. Alloying elements, heat treatments, and processing techniques all play a crucial role in influencing the strength-toughness relationship.
Section 3 Key Alloying Elements and Their Impact
The properties of titanium alloys are highly dependent on their composition. Key alloying elements and their influence on strength and toughness include:
3.1 Aluminum (Al): A common alpha-stabilizer that increases strength but can reduce ductility.
3.2 Vanadium (V): A beta-stabilizer that enhances ductility and weldability.
3.3 Molybdenum (Mo): A beta-stabilizer that increases strength and creep resistance.
3.4 Iron (Fe): A beta-stabilizer that improves hardenability and reduces cost.
3.5 Tin (Sn): An alpha-stabilizer that enhances solid solution strengthening.
Careful control of these alloying elements, in combination with specific heat treatments and processing techniques, is essential for achieving the desired balance of strength and toughness.
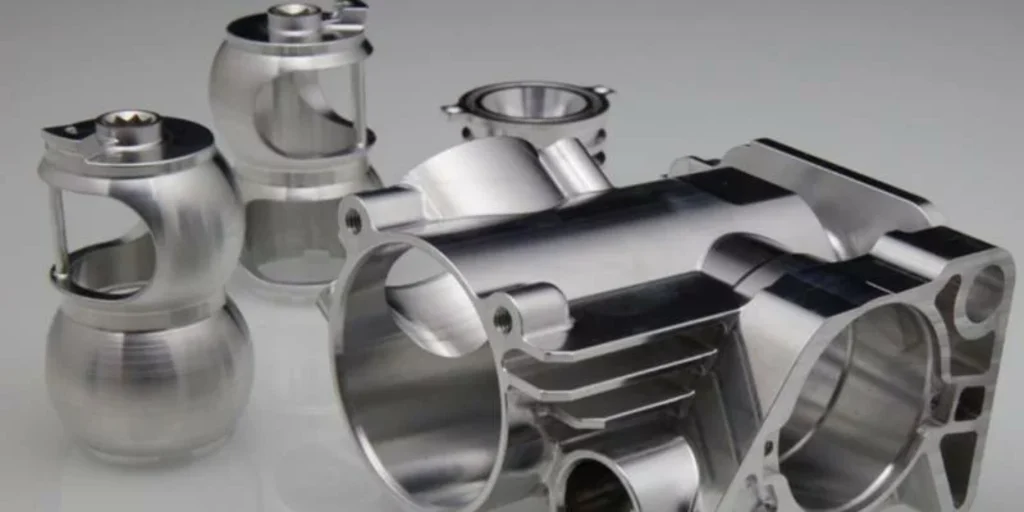
Section 4 Processing Techniques for Enhanced Performance
Advanced processing techniques also play a crucial role in optimizing the properties of titanium alloys:
4.1 Thermo-Mechanical Processing (TMP): Controlled deformation and heat treatment cycles to refine the microstructure and improve both strength and toughness.
4.2 Hot Isostatic Pressing (HIP): Applying high pressure and temperature to eliminate porosity and improve fatigue resistance.
4.3 Additive Manufacturing (AM): Also know as 3D printing, this technique enables the creation of complex geometries and the development of novel alloy compositions.
4.4 Surface Treatments: Techniques like shot peening and laser peening to introduce compressive residual stresses and enhance fatigue life.
Section 5 Popular High-Performance Titanium Alloys
Several titanium alloys have been developed to achieve a superior combination of strength and toughness. Here are a few notable examples:
5.1 Ti-6Al-4V (Grade 5): The most widely used titanium alloy, offering a good balance of strength, toughness, and weldability.
5.2 Ti-6Al-4V ELI (Extra Low Interstitial): A modified version of Ti-6Al-4V with lower oxygen and iron content, resulting in improved toughness, particularly at cryogenic temperatures.
5.3 Ti-10V-2Fe-3Al: A beta titanium alloy with high strength and good forgeability, often used in aerospace applications.
5.4 Ti-5Al-5Mo-5V-3Cr: A metastable beta alloy that demonstrates a great combination of strength, ductility, and fatigue properties, suitable for structural components in aerospace.
5.5 Ti-17: is a heat treatable beta titanium alloy that offers an outstanding combination of deep hardenability, high strength and good ductility.
Section 6 Applications Across Diverse Industries
The exceptional properties of high-performance titanium alloys make them indispensable in a wide range of industries:
6.1 Aerospace: Aircraft structural components, engine parts, landing gear, and fasteners requiring high strength, low weight, and resistance to fatigue and corrosion.
6.2 Medical: Implants, surgical instruments, and prosthetics requiring biocompatibility, corrosion resistance, and high strength.
6.3 Automotive: High-performance engine components, suspension parts, and exhaust systems demanding strength, lightweight, and heat resistance.
6.4 Military: Armor plating, missile components, and other defense applications requiring high strength, toughness, and ballistic resistance.
6.5 Energy: Oil and gas exploration equipment, power generation components, and nuclear reactors requiring corrosion resistance, high strength, and high-temperature performance.
Section 7 Key Considerations for Selecting High-Performance Titanium Alloys
Choosing the right high-performance titanium alloy for a specific application requires careful consideration of several factors:
7.1 Strength Requirements: The alloy must have sufficient yield strength and tensile strength to withstand the applied loads.
7.2 Toughness Requirements: The alloy must have adequate fracture toughness to resist crack propagation and prevent catastrophic failure.
7.3 Environmental Conditions: The alloy must be resistant to corrosion, oxidation, and other environmental factors relevant to the application.
7.4 Fabrication Requirements: The alloy must be readily machinable, weldable, and formable using available manufacturing processes.
7.5 Cost: The alloy must be cost-effective for the intended application, considering both material cost and processing costs.
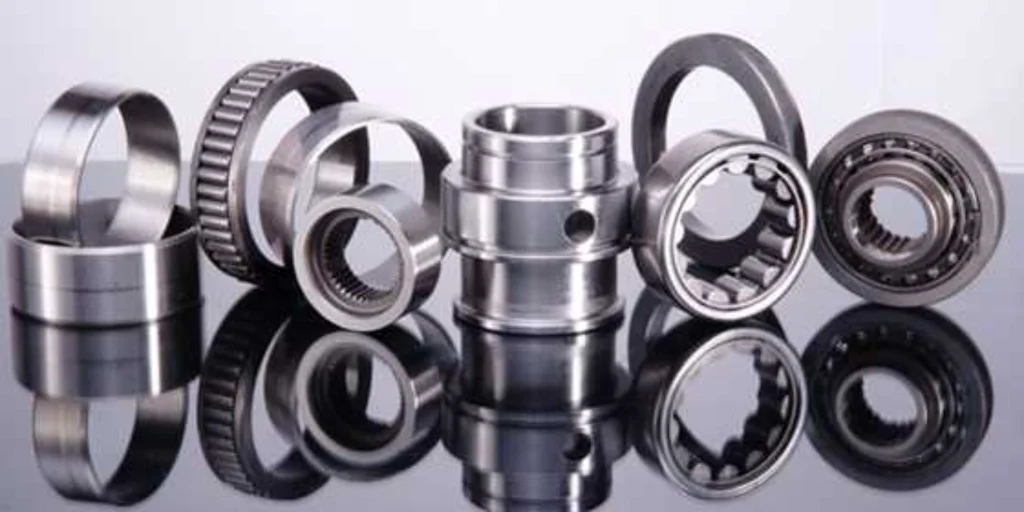
Section 8 Comparative Overview of Titanium Alloys
Here’s a simplified table summarizing the properties of some common titanium alloys. Note that these are approximate values and can vary depending on the specific processing conditions.
Alloy | Tensile Strength (MPa) | Yield Strength (MPa) | Elongation (%) | Key Features | Typical Applications |
Ti-6Al-4V | 895-960 | 828-880 | 10-14 | Excellent balance of properties, good weldability | Aerospace, medical implants, general engineering |
Ti-6Al-4V ELI | 895-960 | 828-880 | 12-16 | Improved toughness, particularly at low temperatures | Cryogenic applications, medical implants |
Ti-10V-2Fe-3Al | 1100-1200 | 1035-1100 | 10-12 | High strength, good forgeability | Aerospace structural components |
Ti-5Al-5Mo-5V-3Cr | 1240 | 1170 | 10 | High strength, good fatigue performance | Airframe components |
Ti-17 | 1275 | 1185 | 11 | high hardenability, and an outstanding combination of strength, ductility | Airframe components |
Disclaimer: The values provided are for general informational purposes only and should not be used for design or engineering calculations without consulting relevant material specifications and conducting appropriate testing.
Section 9 The Future of High-Performance Titanium Alloys
The field of high-performance titanium alloys is constantly evolving, with ongoing research focused on developing new alloys and processing techniques that push the boundaries of strength, toughness, and other desirable properties. Areas of active research include:
Development of novel alloy compositions with improved properties.
Optimization of thermo-mechanical processing techniques to refine microstructures.
Exploration of additive manufacturing for creating complex geometries and functionally graded materials.
Application of advanced surface treatments to enhance fatigue life and corrosion resistance.
Section 10 Partnering with Welleschaft for High-Quality Titanium Alloy Solutions
When it comes to sourcing high-performance titanium alloys and precision-manufactured components, Welleschaft stands out as a trusted global supplier and contract manufacturer. With a proven track record of delivering high-quality materials and engineering solutions, Welleschaft offers a comprehensive range of titanium alloys, custom manufacturing services, and expert technical support.
Welleschaft’s commitment to quality, innovation, and customer satisfaction makes them an ideal partner for companies seeking to leverage the unique benefits of high-performance titanium alloys. Their expertise in material selection, processing, and manufacturing ensures that customers receive tailored solutions that meet their specific application requirements.
By choosing Welleschaft, you gain access to a reliable supply chain, cutting-edge manufacturing capabilities, and a team of experienced professionals dedicated to helping you achieve your engineering goals. Contact Welleschaft today to explore how their high-performance titanium alloy solutions can benefit your business.
Conclusion
High-performance titanium alloys represent a significant advancement in materials engineering, offering a unique combination of strength and toughness that unlocks new possibilities in diverse industries. By carefully selecting the right alloy, optimizing processing techniques, and partnering with a trusted supplier like Welleschaft, engineers can harness the full potential of these advanced materials to create innovative and high-performing products.