High-Performance Sintered Gears: Durable & Precise Gear Solutions
In the world of precision engineering, sintered gears stand out for their remarkable performance and durability. These gears, created through powder metallurgy, offer a unique blend of strength and cost-effectiveness that sets them apart from traditionally machined gears. In this article, we will explore the advantages of sintered gears, how they are manufactured, and why Welleshaft is your ideal partner for high-quality sintered gear solutions.
Section 1: What Are Sintered Gears?
Sintered gears are components created through a process known as powder metallurgy. This method involves compressing powdered metal into a mold and then heating it to a temperature where the particles fuse together without fully melting. The result is a gear with impressive mechanical properties and dimensional accuracy.
Section 2: The Sintered Gear Manufacturing Process
The process of manufacturing sintered gears involves several key steps:
1.Powder Preparation: Metal powders, such as iron, steel, or bronze, are carefully selected and blended to achieve the desired properties.
2.Compaction: The metal powders are compacted into a die using high pressure. This step shapes the material into the rough form of the gear.
3.Sintering: The compacted gears are heated in a furnace at temperatures below the melting point of the metal. This process causes the powder particles to bond together, forming a solid, durable gear.
4.Finishing:After sintering, the gears are often subjected to finishing processes such as machining or grinding to achieve precise dimensions and surface finishes.
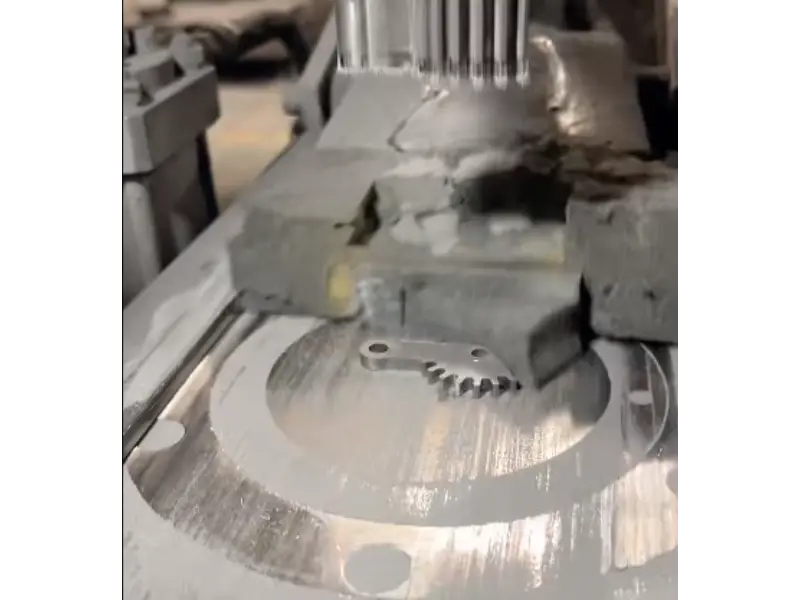
Section 3: Sintered Gear Material and Types
Sintered gears are manufactured using a process that involves heating powdered metal to a temperature below its melting point until it fuses together. This method allows for the creation of gears with specific properties and characteristics that can be advantageous in various applications. Here’s a breakdown of sintered gear materials and types:
3.1. Materials for Sintered Gears
3.1.1.Iron-Based Materials:
- Low Carbon Steel:Commonly used for general-purpose gears where high strength is not a critical factor.
- High Carbon Steel: Offers better hardness and wear resistance compared to low carbon steel.
- Alloy Steel:Includes elements like chromium or molybdenum to improve hardness, strength, and toughness.
3.2.2.Copper-Based Materials:
- Bronze: Provides good wear resistance and lubricating properties, often used in applications requiring high corrosion resistance.
3.2.3.Stainless Steel:
- Austenitic Stainless Steel:Offers excellent corrosion resistance and good mechanical properties, suitable for harsh environments.
3.2.4.Specialty Materials:
- Tool Steel: Used for gears requiring high hardness and wear resistance.
- Carbide and Cermets:Used for high-performance applications where extreme hardness and resistance to wear are required.
3.2. Types of Sintered Gears
3.2.1.Spur Gears:
Have straight teeth and are used for transmitting motion between parallel shafts. They are straightforward to manufacture and are often used in low-speed applications.
3.2.2.Helical Gears:
Feature teeth that are cut at an angle, providing smoother and quieter operation than spur gears. They are used in applications requiring higher load capacity and smoother engagement.
3.2.3.Bevel Gears:
Designed to transmit power between shafts that are at right angles to each other. They can be straight, spiral, or hypoid bevel gears.
3.2.4.Worm Gears:
Consist of a worm (screw) and a worm wheel (gear) and are used for high reduction ratios and non-back-driving applications.
3.2.5.Planetary Gears:
Comprise a central sun gear, planet gears, and a ring gear. They are used in applications requiring high torque and compact design.
3.2.6.Internal Gears:
Feature teeth on the inside diameter of the gear, used in gearboxes and planetary gear systems for compact designs.
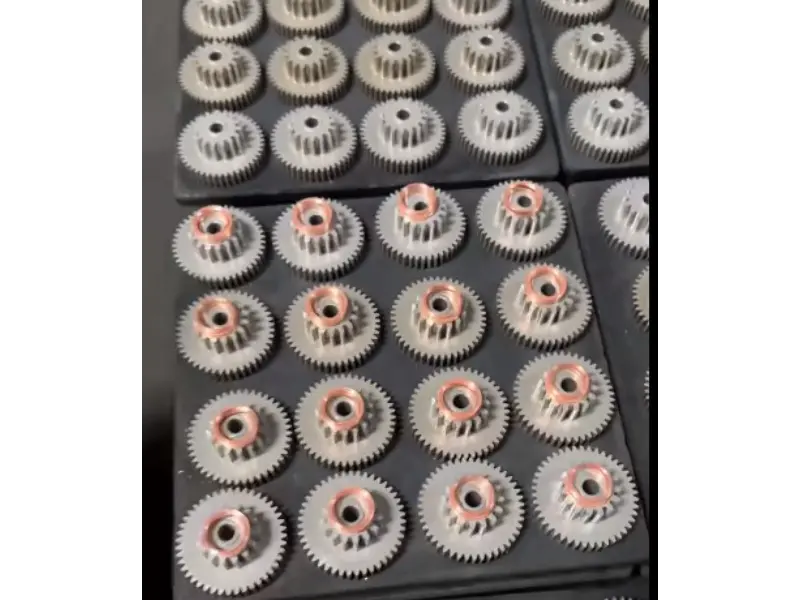
Section 3: Sintered Gears vs. Machined Gears
When comparing sintered gears to machined gears, several differences become apparent:
1. Cost Efficiency
- Sintered Gears:Generally, sintered gears are more cost-effective due to the lower material waste and reduced need for extensive machining.
- Machined Gears:Machined gears typically involve higher material costs and extended manufacturing time, leading to increased overall expenses.
2. Strength and Durability
- Sintered Gears:Sintered gears offer strong mechanical properties, including high wear resistance and good fatigue strength, thanks to the controlled sintering process.
- Machined Gears: While machined gears can be made from high-quality materials, they may not always match the strength and uniformity of sintered gears due to variations in the machining process.
3. Design Flexibility
- Sintered Gears: The powder metallurgy process allows for complex shapes and designs that might be difficult or costly to achieve with traditional machining.
- Machined Gears:Complex designs may require specialized machinery and additional processing, increasing the production cost.
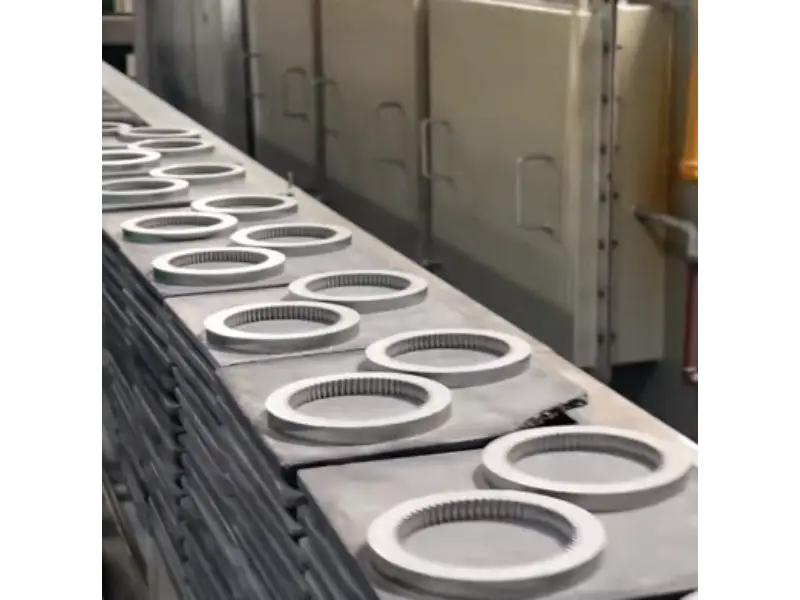
Section 4: What Are the Limitations of Sintered Gears?
Sintered gears, which are made through a powder metallurgy process, have several advantages, such as cost-effectiveness and the ability to create complex shapes. However, they also come with limitations:
1.Strength and Durability
Sintered gears may not have the same mechanical strength or durability as gears made from forged or machined materials. The sintering process can result in a porous structure, which may affect the gear’s load-carrying capacity and overall toughness.
2.Precision
Achieving high precision can be challenging with sintered gears. The powder metallurgy process might not offer the same level of dimensional accuracy and surface finish as other manufacturing methods like machining.
3.Wear Resistance
Sintered gears may have lower wear resistance compared to those made from high-quality metals or treated surfaces. This can lead to faster degradation in high-wear applications.
4.Heat Treatment Limitations
Sintered gears often have limited options for heat treatment to improve properties such as hardness. Unlike forged or cast gears, their mechanical properties are more fixed after sintering.
5.Density and Porosity
The porous nature of sintered materials can lead to lower density compared to wrought metals. This porosity can reduce the strength and may also affect the gear’s performance in applications where fluid leakage or contamination is a concern.
6.Load Carrying Capacity
Due to their porous structure, sintered gears might not be suitable for high-load applications. They generally perform better in applications with moderate loads.
7.Cost of Raw Materials
While the manufacturing process can be cost-effective, the raw materials used for sintered gears can sometimes be expensive, especially if they require specific alloys or additives.
8.Design Limitations
There may be limitations in terms of the complexity of gear designs that can be effectively manufactured using sintering. Certain intricate features or high precision requirements might not be achievable.
9.Post-Processing Needs
Sintered gears often require additional post-processing steps to improve their properties, such as impregnation to reduce porosity, which can add to the overall cost and complexity of production.
Despite these limitations, sintered gears are a viable option for many applications, particularly where cost-effectiveness and the ability to create complex shapes are prioritized over extreme strength or precision.
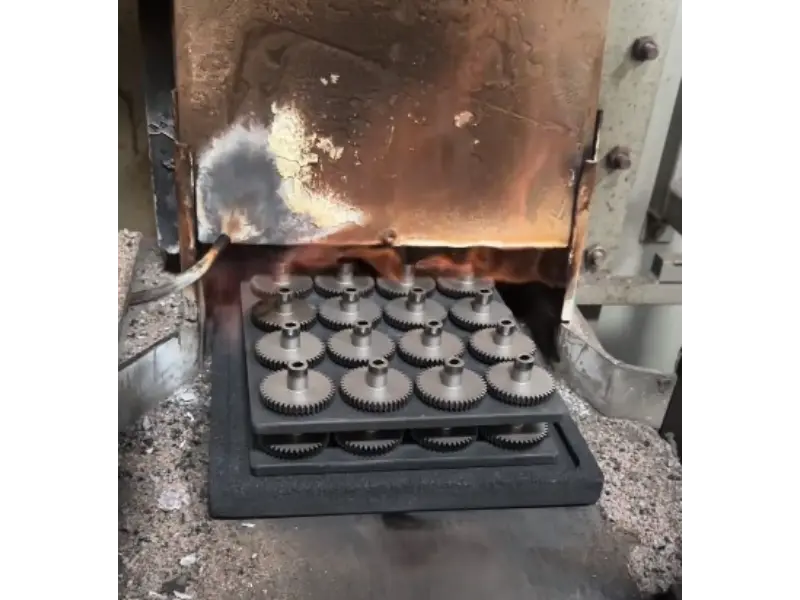
Section 5: Why Choose Welleshaft for Sintered Gear Solutions?
Welleshaft is a global leader in the supply and manufacture of high-performance sintered gears. With extensive experience in the industry, Welleshaft offers:
- High-Quality Standards: Adherence to rigorous quality control processes ensures that every sintered gear meets the highest standards of performance and durability.
- Custom Solutions: Welleshaft provides tailored sintered gear solutions to meet specific customer requirements, including custom sizes, shapes, and material properties.
- Competitive Pricing: By leveraging advanced manufacturing techniques and efficient processes, Welleshaft delivers cost-effective solutions without compromising on quality.
- Global Reach: As a trusted global supplier and contract manufacturer, Welleshaft is equipped to serve clients worldwide with prompt and reliable service.
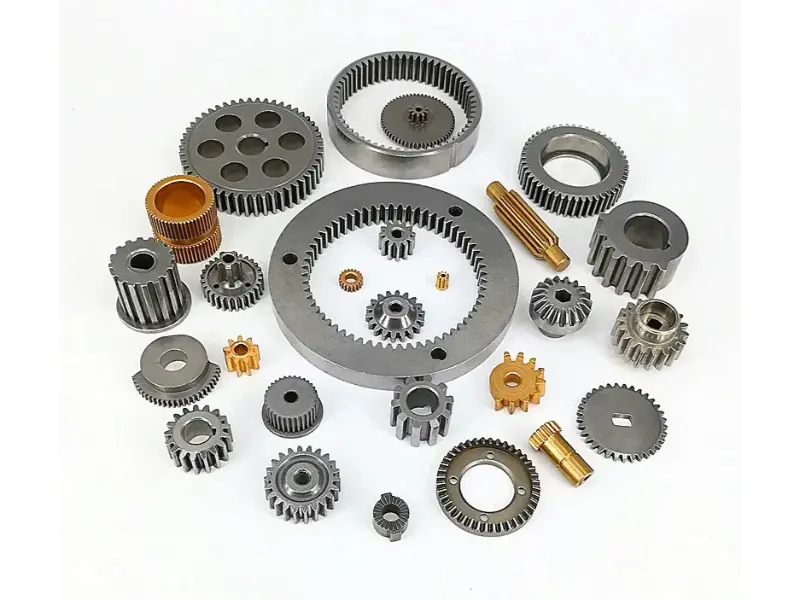
Section 6: Frequently Asked Questions (FAQs)
1. What are the typical applications of sintered gears?
Sintered gears are used in a variety of applications, including:
- Automotive components: For reliability and durability in vehicle systems.
- Industrial machinery: In equipment requiring robust performance.
- Electronics: For compact and efficient gear systems.
- Consumer goods: In everyday items where cost and performance are critical.
2. How do sintered gears compare to forged or machined gears?
Sintered gears often offer cost advantages and the ability to produce complex shapes, while forged and machined gears might provide higher precision and strength. The choice depends on the specific requirements of the application, including material properties, production volume, and cost.
3. Are sintered gears suitable for high-load applications?
Yes, sintered gears can be designed to handle high loads, especially when using high-strength materials and optimizing the sintering process. However, for extremely high-load applications, other manufacturing methods might be preferred.
4. How are sintered gears maintained?
Sintered gears should be regularly inspected for wear and lubrication issues. Proper maintenance involves ensuring that the gears are well-lubricated and free from debris that could cause damage or reduced performance.
5. Can sintered gears be customized?
Yes, sintered gears can be customized in terms of shape, size, and material properties to meet specific requirements. The sintering process allows for a wide range of design possibilities.
6.Is Sintered Metal Strong?
Yes, sintered metal is strong. The sintering process creates a gear with high mechanical strength due to the bonding of metal particles during heating. This results in a material that is not only durable but also capable of withstanding significant stress and wear.
Conclusion
High-performance sintered gears offer a combination of durability, precision, and cost-effectiveness that makes them an excellent choice for various applications. With Welleshaft as your partner, you can be assured of top-quality sintered gears tailored to your specific needs. Whether you are looking for robust gear solutions or customized sintered gears, Welleshaft is your trusted source for excellence in powder metallurgy.
For more information or to request a quote, contact Welleshaft today and experience the difference of high-quality sintered gears.