Helical Gears: Minimizing Noise & Vibration in Power Transmission
In the realm of mechanical power transmission, the quest for efficiency, reliability, and quiet operation is paramount. While various gear types exist, helical gears stand out for their ability to minimize noise and vibration, making them ideal for a wide range of applications where smooth and silent performance is crucial.
Understanding Helical Gears
Helical gears are characterized by their teeth, which are cut at an angle to the gear axis. This angled tooth design distinguishes them from spur gears, which have straight teeth parallel to the axis. The helix angle (the angle of the teeth relative to the gear axis) is a key parameter that influences the gear’s performance. Here are some alternate names as Angled Gears, Skew Gears, Angled-Tooth Gears, Inclined-Tooth Gears, Oblique Gears, Twisted Gears, Skew Gears, Spiral Gears, Herringbone Gears, Continuous Mesh Gears, Quiet Gears, Constant Velocity Gears
Why Helical Gears Excel at Noise and Vibration Reduction
The angled tooth design of helical gears is the primary reason for their superior noise and vibration characteristics compared to spur gears. Here’s a breakdown of the key mechanisms:
Gradual Tooth Engagement: Unlike spur gears, where teeth engage suddenly across their entire width, helical gears engage gradually. This gradual engagement reduces the impact force and minimizes the excitation of vibrations.
Increased Tooth Contact Ratio: The angled teeth of helical gears provide a higher tooth contact ratio than spur gears. This means that more teeth are in contact at any given time, distributing the load and reducing stress on individual teeth. The higher contact ratio contributes to smoother and quieter operation.
Axial Thrust: Helical gears generate axial thrust loads due to the helix angle. While this thrust needs to be accounted for in the bearing design, it can be managed effectively with appropriate bearing selection and arrangement. Herringbone gears (double helical gears) are a special type of helical gears that eliminate axial thrust.
Overlap of Contact: The helical shape leads to an overlap of contact, meaning that as one tooth disengages, another is already engaging. This continuous contact further reduces impact and noise.
Comparison Table: Helical vs. Spur Gears for Noise and Vibration
Feature | Spur Gears | Helical Gears |
Tooth Engagement | Sudden | Gradual |
Tooth Contact Ratio | Lower | Higher |
Noise Level | Higher | Lower |
Vibration Level | Higher | Lower |
Load Capacity | Typically Lower | Typically Higher |
Axial Thrust | None | Present (except herringbone) |
Manufacturing Cost | Lower | Higher |
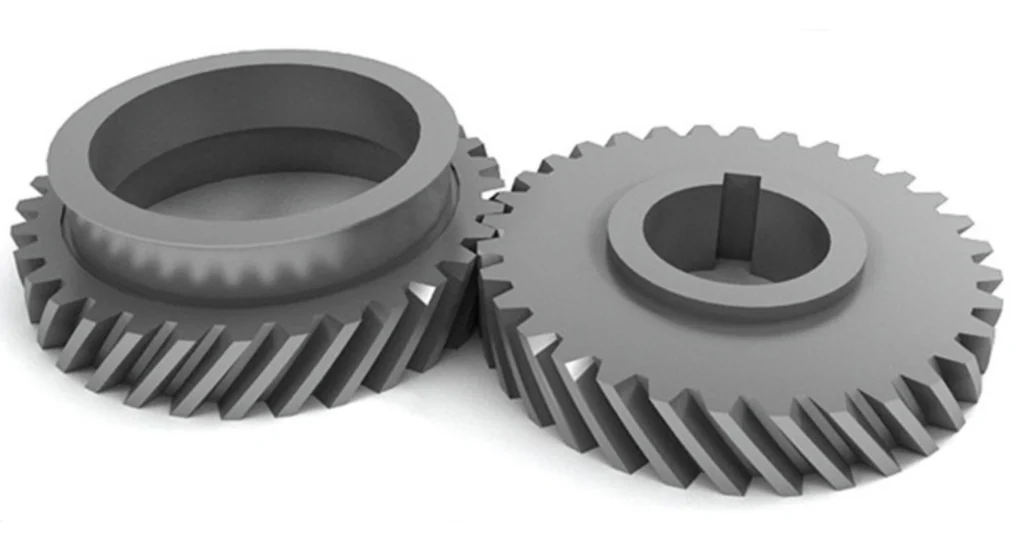
Applications Where Noise Reduction is Critical
The quiet operation of helical gears makes them ideal for a wide range of applications where noise reduction is a key requirement:
Automotive Transmissions: Helical gears are extensively used in automotive transmissions to minimize noise and vibration, providing a smoother and more comfortable driving experience.
Industrial Machinery: In machinery used in factories and other industrial settings, helical gears help reduce noise pollution, creating a more pleasant working environment.
Aerospace: In aircraft applications, helical gears are used to reduce noise and vibration in gearboxes and other power transmission systems, improving passenger comfort.
Medical Equipment: In medical devices such as pumps and instruments, quiet operation is essential to avoid disturbing patients.
Elevators: The smooth and quiet operation of helical gears makes them suitable for elevators, ensuring a comfortable ride for passengers.
Designing Helical Gears for Optimal Noise Reduction
Several design parameters can be optimized to further minimize noise and vibration in helical gears:
Helix Angle: The helix angle influences the tooth contact ratio and axial thrust. A higher helix angle generally leads to smoother operation but also increases axial thrust.
Tooth Profile: The tooth profile (e.g., involute) affects the load distribution and contact stresses. Optimizing the tooth profile can reduce noise and vibration.
Gear Material: The material used for the gears can significantly impact noise and vibration levels. Materials with good damping properties, such as certain polymers, can help absorb vibrations.
Manufacturing Precision: High manufacturing precision is crucial for ensuring accurate tooth profiles and minimizing errors that can lead to noise and vibration.
Lubrication: Proper lubrication reduces friction and wear, contributing to smoother and quieter operation.
Herringbone Gears: The Ultimate in Noise Reduction and Thrust Elimination
Herringbone gears (also known as double helical gears) are a special type of helical gear that features two sets of teeth with opposing helix angles. This design eliminates axial thrust and further reduces noise and vibration. Herringbone gears are often used in high-power applications where smooth and quiet operation is critical.
Factors Affecting Helical Gear Noise
Several factors beyond the basic design influence the noise generated by helical gears:
Manufacturing Tolerances: Deviations from ideal tooth geometry due to manufacturing imperfections can significantly increase noise.
Surface Finish: A rough surface finish on the gear teeth increases friction and noise.
Misalignment: Misalignment of the gears can cause uneven load distribution and increased noise.
Operating Speed: Noise levels typically increase with operating speed.
Load: Higher loads can lead to increased noise and vibration.
Lubrication: Insufficient or improper lubrication can increase friction and noise.
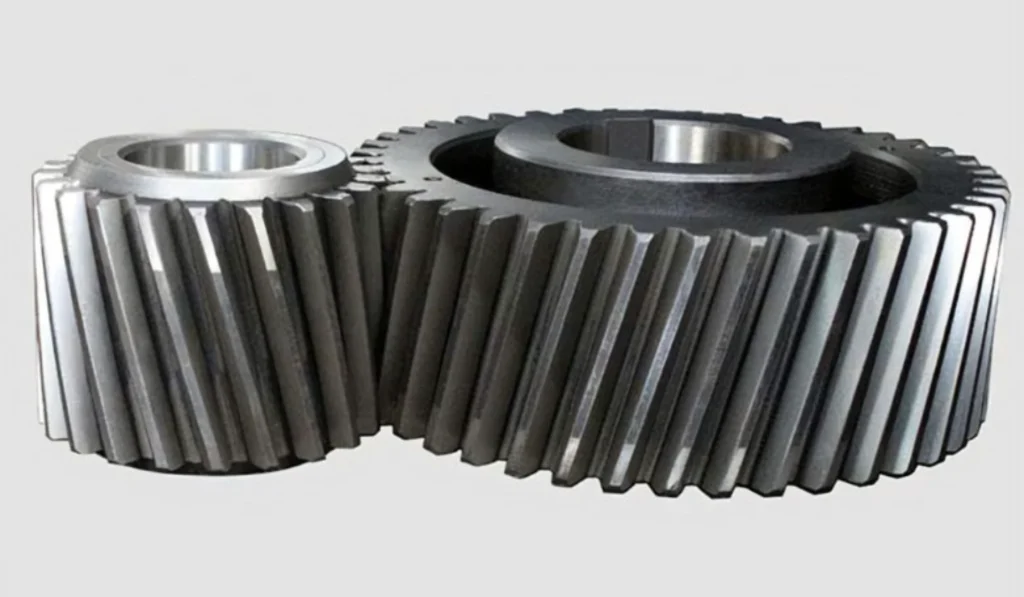
Maintaining Helical Gears for Quiet Operation
Proper maintenance is essential for maintaining the quiet operation of helical gears:
Regular Lubrication: Follow the manufacturer’s recommendations for lubrication type and frequency.
Alignment Checks: Periodically check the gear alignment and make adjustments as needed.
Inspection for Wear: Inspect the gear teeth for signs of wear or damage.
Replacement of Worn Gears: Replace worn gears promptly to prevent increased noise and vibration.
Choosing a Reliable Helical Gear Manufacturer: Consider Welleshaft
Selecting a reputable and experienced helical gear manufacturer is crucial for ensuring the quality, performance, and longevity of your gear drives.Welleshaft stands out as a trusted global supplier and contract manufacturer of high-quality helical gears.
Extensive Experience: Welleshaft has a proven track record in designing and manufacturing helical gears for a wide range of applications.
Advanced Manufacturing Capabilities: Welleshaft utilizes state-of-the-art CNC gear cutting machines and inspection equipment to ensure the highest levels of precision and accuracy.
Custom Solutions: Welleshaft specializes in providing custom gear solutions tailored to your specific needs.
Stringent Quality Control: Welleshaft’s quality control system is designed to meet the most demanding industry standards.
Engineering Expertise: Welleshaft’s team of experienced engineers can assist you with every stage of the design and manufacturing process.
Global Reach: Welleshaft has a global presence, providing support and service wherever you are located.
By partnering with Welleshaft, you can be confident that you are receiving the highest quality helical gears and exceptional customer service.
Conclusion
Helical gears offer a significant advantage in minimizing noise and vibration in power transmission systems. Their gradual tooth engagement, high tooth contact ratio, and other design features contribute to smoother and quieter operation. By carefully considering design parameters, manufacturing precision, and maintenance practices, it is possible to optimize helical gears for even quieter performance. When selecting a helical gear manufacturer, choose a reputable and experienced company like Welleshaft to ensure the quality and reliability of your gear drives.