Gear Cutting VS Gear Hobbing: A Comprehensive Overview
1.What Is Gear Cutting?
- Manufacturers use gear cutting to precisely shape gear teeth, ensuring smooth motion and power transmission. Comparing gear hobbing vs gear cutting helps choose the best method for producing high-performance gears in mechanical systems.
- In the evolution of Chinese manufacturing, gear cutting has undergone a remarkable transformation. From traditional methods passed down through generations to the adoption of advanced technologies such as CNC gear cutting, China has embraced innovation to elevate its manufacturing capabilities. This evolution has positioned China as a global leader in gear manufacturing, known for its high-quality products and competitive edge in the international market.
2.What Is Gear Hobbing?
- Despite the advancements in manufacturing technologies, traditional methods like hobbing continue to find global acceptance. The manufacturing world acknowledges the inherent value of hobbing, blending the wisdom of tradition with the innovations of the present. This global embrace exemplifies the adaptability of hobbing in meeting the demands of modern manufacturing, where a harmonious fusion of tradition and innovation paves the way for enduring craftsmanship in gear cutting.
- At the core of traditional gear cutting processes, hobbing stands out as a time-tested and enduring method. This detailed exploration provides an in-depth look into the intricacies of hobbing, where gear teeth are precisely shaped using a cutting tool called a hob. As an established technique, hobbing has proven its efficacy over the years, contributing to the production of gears with precision and reliability.
3. Importance of Gear Manufacturing in China
- China’s profound influence in the global gear manufacturing landscape stands as a testament to the nation’s dominance across diverse industries. From automotive to aerospace and industrial machinery, Chinese manufacturers have emerged as key players, reshaping the narrative of precision engineering on a global scale. This exploration unveils the multifaceted dominance that China exerts, positioning itself as a pivotal hub for the production of high-quality gears that drive efficiency across the world.
- At the heart of China’s global impact in gear manufacturing lies an unwavering commitment to precision and quality. Chinese manufacturers have meticulously crafted a reputation that resonates globally, making their products synonymous with excellence. The gears produced in China are not just components; they are precision-engineered marvels that have set new standards for quality in the international market. As industries worldwide seek gears that combine efficiency with reliability, Chinese manufacturers stand out as the epitome of precision craftsmanship, leaving an enduring mark on the global gear manufacturing arena.

What Are the Different Gear Types Produced by Gear Cutting and Gear Hobbing?
1. Spur Gears and Helical Gears
- Spur Gears:Characterized by their simplicity, find widespread applications across diverse industries. Their straightforward design makes them ideal for applications requiring uncomplicated power transmission, such as in conveyor systems, wind turbines, and simple gear trains. The advantages of spur gears lie in their cost-effectiveness, ease of manufacturing, and efficiency in transferring rotational motion. These gears remain a fundamental choice, embodying simplicity and reliability in various mechanical systems worldwide.
- Helical Gears: Distinguished by their angled teeth, epitomize precision and efficiency in motion. Their unique spiral design ensures a smoother meshing process, reducing noise and enhancing load distribution. Widely applied in industries like automotive, aerospace, and machinery, helical gears excel in transmitting power with precision. The advantages of helical gears include increased contact ratios, higher load-bearing capacity, and superior torque delivery. In every turn, helical gears demonstrate their unparalleled precision, making them a cornerstone in diverse industrial applications.
2. Bevel Gears and Worm Gears
- Bevel Gears: With their angled teeth, wield a unique prowess in transmitting power at angles. Widely utilized in applications demanding angular power transmission, these gears excel in providing efficiency and flexibility. Their advantages include enhanced gear meshing, reduced vibration, and precise motion control. Embraced across various industries, from automotive differential systems to marine propulsion, bevel gears exemplify versatility and reliability in navigating the complexities of power transmission.
- Worm Gears and Spline Shafts:Operating on a distinctive principle, worm gears exhibit unparalleled efficiency in motion. The helical gear (worm) engages with a worm wheel, translating rotational motion into a perpendicular direction. This unique feature imparts high gear reduction ratios, making worm gears ideal for applications requiring precision and stability. Commonly found in conveyor systems, elevators, and automotive mechanisms, the advantages of worm gears include self-locking capabilities and quiet operation. Across various industries, worm gears stand as reliable components, embodying efficiency and precision in diverse motion systems.
3. Other Gear Varieties: A World of Possibilities
- Rack and Pinion, Internal Gears, and Hypoid Gears
- Rack and Pinion systems offer linear motion by converting rotational movement, ideal for steering mechanisms in vehicles. Internal gears provide compact power transmission within confined spaces, ensuring efficiency. Hypoid gears, with their offset axes, enhance torque and durability in automotive applications. These gear types showcase mechanical ingenuity, finding applications in automotive steering, machinery, and different industrial settings, highlighting their adaptability and significance in diverse industries.
- Miter Gears and Custom Gears
- Miter gears, with intersecting but non-parallel shafts, enable efficient angular power transmission, often used in machinery requiring right-angle motion. Custom gears, tailored to specific requirements, offer unparalleled versatility. Their unique features include precise tooth profiles and material adaptation. Widely applied in automotive systems, machinery, and robotics, miter gears and custom gears exemplify precision engineering. Their advantages lie in tailored solutions, ensuring optimal performance across various industries, showcasing adaptability and precision in meeting diverse gear requirements.
- Ground Gears, Pump Gears, and Change Gears
- Ground gears, crafted with meticulous precision, ensure accurate tooth profiles, reducing friction and noise. Pump gears excel in fluid handling applications, providing reliable and efficient fluid displacement. Change gears, facilitating gear ratio adjustments, are integral in machinery setups. With unique features tailored to their applications, these gears find homes in industries ranging from manufacturing and automotive to aerospace. Their advantages include enhanced durability, efficiency, and adaptability, making ground gears, pump gears, and change gears indispensable components in various precision-driven sectors.
How To Choose a Gear Type for Gear Cutting?
1. Custom Gears for Specific Applications
- Spiral Bevel Gears, Sprockets, and Timing Pulleys
- Spiral bevel gears, with their curved teeth, excel in transmitting motion between intersecting shafts, ensuring smooth operation and power distribution. Sprockets, pivotal in chain and belt systems, drive machinery with precision. Timing pulleys, synchronizing rotational movements, find applications in precise timing requirements. With unique features tailored to their roles, these components contribute to diverse industries, offering advantages such as enhanced efficiency and reliability. Spiral bevel gears, sprockets, and timing pulleys exemplify precision in motion, playing crucial roles in applications across various industrial sectors.
- Spline Shafts and Custom Precision Gears
- Spline shafts, featuring grooves or teeth, excel in transmitting torque with precision, often employed in automotive and machinery applications. Custom precision gears, tailored to exact specifications, offer versatility in diverse industries. Their unique features, from intricate tooth profiles to material adaptability, ensure optimal performance. Advantages include enhanced durability and efficiency, addressing unique requirements across various sectors. Spline shafts and custom precision gears exemplify tailored excellence, playing pivotal roles in applications with stringent demands for precision and reliability.
2. Material Variety in Custom Gear Manufacturing
-
Custom Stainless Steel Gears, Custom Steel Gears, and Custom Plastic Gears
Custom Stainless Steel Gears:
Made from AISI 304/316 stainless steel, these gears resist corrosion and suit harsh environments like marine and food industries.Custom Steel Gears:
Forged from 1045 or 4140 steel, these gears provide strength and precision for automotive and heavy machinery use.Custom Plastic Gears:
Molded from Nylon, Acetal, or PEEK, plastic gears offer lightweight, low-noise solutions for electronics and medical devices.Custom Non-Ferrous Metal Gears
Non-ferrous gears use aluminum alloys (6061-T6) or brass (C36000), delivering light weight, corrosion resistance, and heat dissipation.
Ideal for aerospace, electronics, and marine applications needing adaptable, lightweight components.
Custom Anti-Backlash Gears, Custom Gear Racks, Custom Helical Gears, and Custom Internal Gears
Custom Anti-Backlash Gears:
Designed to reduce play, these gears (e.g., Nylatron GS) enable precise robotic motion control.Custom Gear Racks:
Used in CNC machines, 1045 steel gear racks convert rotary to linear motion efficiently.Custom Helical Gears:
With angled teeth (e.g., 4140 steel), they provide smooth, high-speed power transmission in automotive systems.Custom Internal Gears:
Featuring inner teeth (e.g., 8620 steel), these gears drive planetary systems across diverse industries.
How to make Inch Gears and Metric Gears with Gear Cutting?
1. Precision Gears: Inch and Metric Series
- Precision Ground Gears and Modified & Custom Gears
- Precision Ground Gears: Crafted with utmost precision, available in both inch and metric series, these gears excel in aerospace applications, ensuring unparalleled accuracy.
- Modified & Custom Gears: Tailored to specific needs, serving diverse industries globally. From automotive applications in the U.S. to machinery in European markets, these gears offer custom solutions.
- Internal & External Spur Gears and Internal Herringbone Gear
- Internal & External Spur Gears: Crafted with precision tooth profiles (e.g., 8620 steel), these gears find applications in various industries for efficient power transmission with reduced noise.
- Internal Herringbone Gear: Featuring dual, angled teeth for enhanced load distribution, often made from alloys like 4140, these gears excel in heavy machinery applications, providing superior torque transmission.
- Internal Helical Gear and Gear Builder
- Internal Helical Gear: With angled teeth for smoother operation, crafted from materials like 4140 steel, these gears offer superior torque and find applications in automotive transmissions.
- Gear Builder: Providing customization possibilities, enabling tailored gear solutions for diverse applications and industries, ensuring optimal performance.
Differences Between Gear Cutting and other Gear Forming
1. Casting, Forging, Extrusion, and Cold Drawing
-
Powder Metallurgy and Blanking Gears
Sintered Gears:
Powder metallurgy forms strong, complex gears with precise material control and minimal waste for automotive and aerospace.Blanking Gears:
Blanking produces precise, smooth gears quickly with low waste, ideal for automotive and machinery mass production.Casting and Forging Gears
Casting Gears:
Casting creates intricate, cost-effective gears with flexible designs, suitable for automotive and marine applications.Forging Gears:
Forging shapes durable, fatigue-resistant gears with precise tolerances for aerospace and heavy machinery.Cold Extrusion and Cold Drawing Gears
Cold Extrusion Gears:
Cold extrusion strengthens gears with dense materials and precise shapes, enhancing cost-efficiency for automotive use.Cold Drawing Gears:
Cold drawing yields precise, smooth gears with tight tolerances for aerospace and automotive industries.Gear Machining: Precision in Every Cut
Gear machining delivers high-accuracy, versatile gear profiles for automotive, aerospace, and industrial sectors.
It ensures consistent quality and adaptability across various gear types and applications.
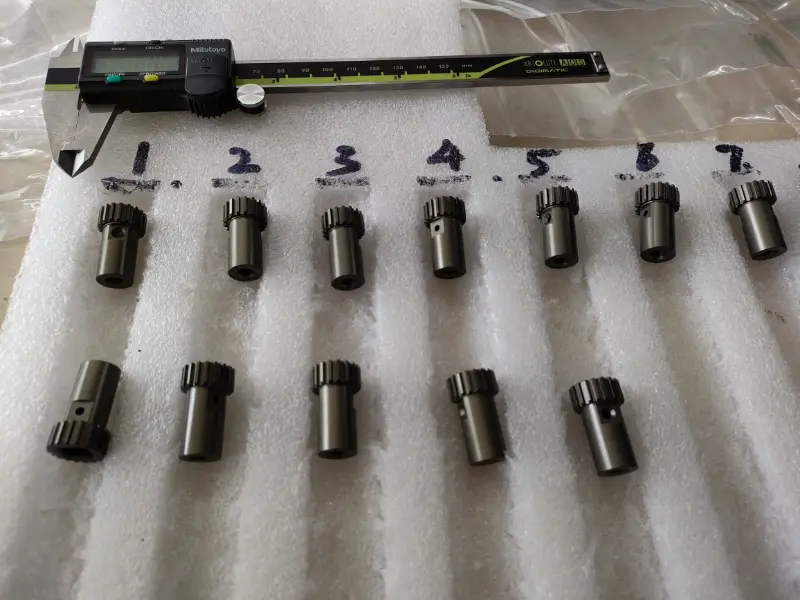
Applications of Custom Gears
1. Automotive Industry
- Gears in Motion: Driving Automotive Excellence Gears play a pivotal role in automotive transmissions, contributing to the smooth operation of vehicles. The section will highlight specific applications and the impact of Chinese gear manufacturers on the automotive sector.
- China’s Influence: Shaping the Future of Automotive Gear Technology Chinese gear manufacturers’ contributions to automotive gear technology will be explored in this subsection.
2. Aerospace Sector
- Precision in the Skies: Gears in Aerospace Applications Gears are critical components in aerospace applications, ensuring the reliable operation of aircraft systems. This section will discuss the specific applications of gears in the aerospace sector and how Chinese gear manufacturers contribute to this industry.
- Chinese Gear Manufacturing Excellence in Aerospace The article will highlight instances where Chinese gear manufacturing has played a crucial role in aerospace advancements.
3. Industrial Machinery
- Gearing Up for Efficiency: Gears in Industrial Machinery The industrial machinery sector relies heavily on gears for efficient operation. This section will explore the applications of gears in various industrial machines, emphasizing the impact of Chinese gear manufacturing on industrial efficiency.
- Chinese Gear Manufacturing’s Impact on Industrial Efficiency Specific examples and case studies showcasing the positive influence of Chinese gear manufacturing on industrial efficiency will be discussed.
Custom Gear Cutting in China: Meeting Global Standards
1. Quality Control Measures
- Striving for Perfection: Chinese Quality Standards The article will shed light on the stringent quality control measures adopted by Chinese gear manufacturers to ensure precision and reliability.
- Meeting Global Standards: Certifications and Compliance This section will highlight the certifications and international standards that Chinese gear manufacturers adhere to, ensuring their products meet global expectations.
Common FAQs About Gear Cutting in China
- Q: What sets Chinese gear cutting apart from other manufacturers?
- A: Chinese gear cutting excels in precision, innovation, and custom solutions, making it a global leader.
- Innovation in Chinese Gear Manufacturing: A Global Perspective This subsection will delve into specific innovations introduced by Chinese gear manufacturers, setting them apart on the global stage.
- Q: How can custom gear cutting benefit my specific industrial needs?
- A: Custom gear cutting ensures tailored solutions, enhancing efficiency and performance for unique applications.
- Success Stories: Industries Benefiting from Custom Gear Cutting Real-world examples and success stories of industries benefiting from custom gear cutting will be presented, showcasing the versatility of this approach.
- Q: Are Chinese gear manufacturers compliant with international quality standards?
- A: Yes, Chinese gear manufacturers adhere to stringent international quality standards, ensuring global competitiveness.
- Global Recognition: Chinese Gear Manufacturers and Quality Certifications This subsection will provide an overview of the various quality certifications and recognitions received by Chinese gear manufacturers, establishing their credibility on the global stage.