Gear Grinding Services: Hardened Steel Gear Finishing
In the realm of precision engineering, gears stand as critical components across various industries, from automotive and aerospace to manufacturing and robotics. To achieve optimal performance, longevity, and minimal noise, gears often require a high degree of accuracy and a superior surface finish, especially after heat treatment. This is where gear grinding services, particularly hardened steel gear finishing, become indispensable. This article explores the intricacies of gear grinding, its benefits, techniques, and why hardened steel gears require specialized finishing. We will also introduce Welleshaft as your trusted partner for top-quality gear solutions.
What is Gear Grinding?
Gear grinding is a precision machining process that utilizes abrasive grinding wheels to remove material from gear teeth. Unlike gear cutting processes like hobbing or shaping, grinding is typically employed as a finishing operation after the gear has been hardened. This is because heat treatment can cause distortions and surface imperfections that compromise the gear’s performance. Gear grinding corrects these issues, ensuring accurate tooth profiles, smooth surfaces, and tight tolerances.
Why Grind Hardened Steel Gears?
Hardened steel gears offer exceptional strength and wear resistance, making them ideal for high-load and high-stress applications. However, the hardening process can introduce several issues:
Distortion: Heat treatment can cause gears to warp or distort, affecting their tooth geometry and meshing accuracy.
Surface Imperfections: The hardening process can create surface irregularities, leading to increased friction and noise.
Case Hardening Depth Variability: To guarantee the gear strength, a grinding process might be necessary.
Gear grinding addresses these problems by:
Correcting Tooth Profile: Grinding precisely shapes the gear teeth to the desired profile, ensuring proper meshing and load distribution.
Improving Surface Finish: Grinding creates a smooth, polished surface, reducing friction and wear.
Achieving Tight Tolerances: Grinding allows for achieving very tight tolerances, resulting in improved gear performance and reduced noise.
Removing Surface Defects: Grinding removes any surface imperfections caused by heat treatment.
Benefits of Gear Grinding for Hardened Steel Gears
The benefits of gear grinding extend beyond mere cosmetic improvements. They directly translate into enhanced performance, reliability, and longevity:
Increased Load Capacity: Accurate tooth profiles and proper meshing allow gears to carry higher loads without failure.
Reduced Noise and Vibration: Smooth surfaces and precise tooth geometry minimize friction and vibration, resulting in quieter operation.
Extended Gear Life: Reduced friction and improved load distribution contribute to longer gear life and reduced maintenance costs.
Improved Efficiency: Smooth surfaces and precise meshing reduce power loss due to friction, improving overall efficiency.
Enhanced Precision: Grinding enables the production of gears with very high accuracy, essential for demanding applications.
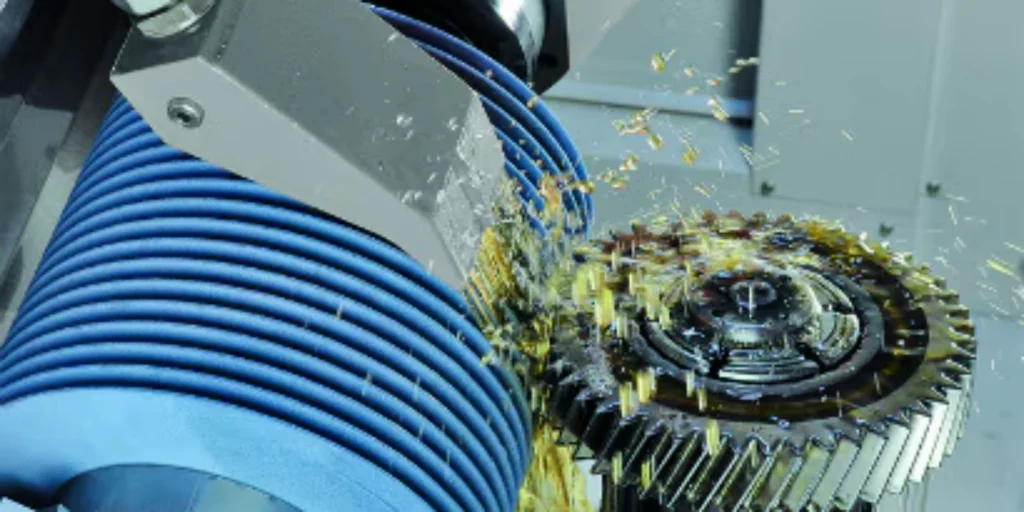
Types of Gear Grinding Processes
Several gear grinding processes cater to different needs and gear types:
Form Grinding: Uses a grinding wheel shaped to match the gear tooth profile, making it ideal for complex gear geometries.
Generating Grinding: Employs a generating grinding wheel that simulates the motion of a mating gear, creating a precise and accurate tooth profile.
Creep Feed Grinding: A high-efficiency process where the grinding wheel removes a large amount of material in a single pass, minimizing grinding time and heat generation.
Profile Grinding: A grinding wheel shapes to match the gear tooth.
Continuous Generating Grinding: A generating grinding wheel grinding tooth continuously.
Topological Grinding: A grinding wheel remove material in gear topological direction.
Gear Grinding Wheels: The Cutting Edge of Precision
The selection of the right grinding wheel is crucial for achieving optimal results. Common grinding wheel materials include:
Aluminum Oxide (Al2O3): Suitable for grinding a wide range of materials, including steel.
Cubic Boron Nitride (CBN): Excellent for grinding hardened steel, offering high stock removal rates, long wheel life, and minimal heat generation.
Diamond: Used for grinding very hard and abrasive materials.
Factors to Consider When Choosing Gear Grinding Services
Selecting a gear grinding service provider requires careful consideration:
Experience and Expertise: Choose a provider with a proven track record of grinding hardened steel gears.
Equipment and Technology: Ensure the provider has state-of-the-art grinding machines and tooling.
Quality Control: A robust quality control system is essential for ensuring accuracy and consistency.
Material Expertise: The provider should have experience grinding the specific steel alloys used in your gears.
Capacity: The provider should be able to handle your production volume requirements.
Tolerances: Ensure the provider can meet your required tolerances.
Wheel Selection Expertise: The provider should have knowledge to select grinding wheels.
Related Information Table
Category | Subcategory | Information |
Grinding Wheel Types | Aluminum Oxide | General-purpose, good for a variety of steels. |
CBN (Cubic Boron Nitride) | Ideal for hardened steels, excellent for high precision and heat control. | |
Diamond | For extremely hard and abrasive materials, less common for steel gears. | |
Grinding Techniques | Form Grinding | Uses a shaped wheel for complex gear profiles. |
Generating Grinding | Simulates gear meshing for accurate tooth creation. | |
Creep Feed Grinding | High material removal rate, reduces grinding time. | |
Gear Attributes | Gear Profile | Precise shape and accuracy of the tooth form. |
Surface Finish | Smoothness of the gear tooth surface, impacts friction and noise. | |
Hardness | Resistance to wear and deformation, achieved through heat treatment. | |
Potential Issues | Heat Treatment Distortion | Warping or dimensional changes after hardening. |
Surface Imperfections | Scratches, pits, or other flaws affecting performance. |
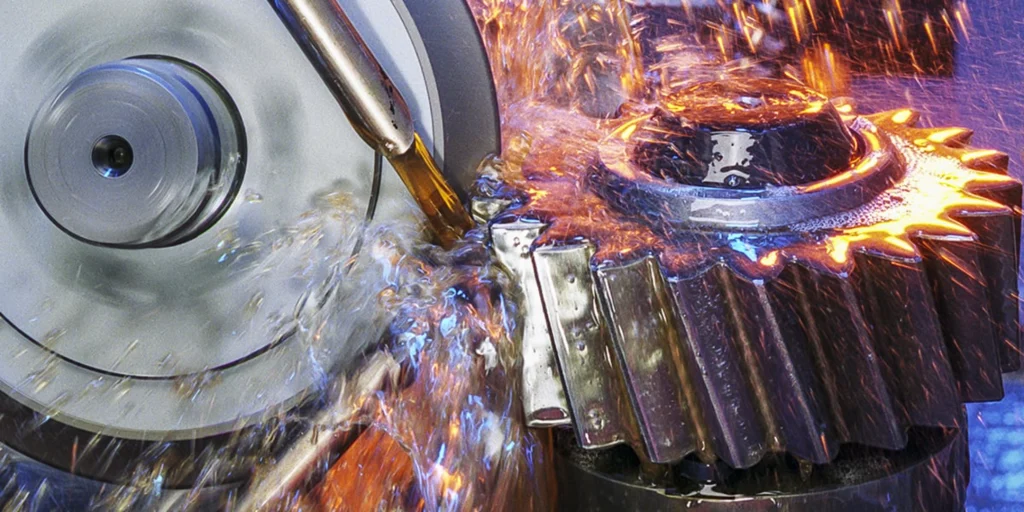
Gear Grinding Applications
Gear grinding is essential for a wide range of applications, including:
Automotive Transmissions: Ensuring smooth shifting and efficient power transfer.
Aerospace Gearboxes: Meeting stringent requirements for reliability and performance.
Industrial Gearboxes: Providing durable and efficient power transmission in heavy-duty machinery.
High-Precision Machinery: Achieving the accuracy and smoothness required for demanding applications like robotics and metrology.
The Future of Gear Grinding
The future of gear grinding promises even greater precision, efficiency, and automation. Advances in CNC technology, grinding wheel materials, and process control are driving these improvements. Expect to see:
More advanced CNC grinding machines: Capable of achieving even tighter tolerances and more complex gear geometries.
New grinding wheel materials: Offering improved performance, longer wheel life, and reduced heat generation.
Automated grinding processes: Integrating grinding with robotic handling and inspection systems for increased efficiency.
Improved grinding process modeling and simulation: Allowing for more accurate prediction and optimization of grinding parameters.
Welleshaft: Your Trusted Partner for Precision Gear Solutions
When it comes to gear grinding services and hardened steel gear finishing, Welleshaft is your reliable partner. As a leading global supplier and contract manufacturer, Welleshaft combines extensive expertise with state-of-the-art technology to deliver exceptional gear solutions.
Welleshaft offers a comprehensive suite of gear grinding services, including:
Precision Grinding of Hardened Steel Gears: Specializing in achieving the highest levels of accuracy and surface finish.
Custom Gear Design and Manufacturing: Providing complete gear solutions from concept to completion.
Material Expertise: Working with a wide range of steel alloys and other materials.
Advanced Equipment and Technology: Utilizing state-of-the-art CNC grinding machines and inspection equipment.
Comprehensive Quality Control: Ensuring that all gears meet the most stringent quality standards.
With Welleshaft, you can be confident that your gear grinding needs will be met with the highest level of precision, quality, and efficiency.
Conclusion
Gear grinding services are essential for achieving optimal performance, reliability, and longevity of hardened steel gears. By understanding the intricacies of gear grinding, the different techniques, and the factors to consider when choosing a service provider, you can ensure that your gears meet the most demanding requirements. With its expertise, technology, and commitment to quality, Welleshaft is a trusted partner for precision gear solutions, delivering exceptional results for a wide range of industries.